The 208C High Vacuum Turbo Carbon Coater from Cressington offers high-quality carbon coating methods for TEM, SEM, STEM, EDS/WDS, EBSD, and microprobe applications. The small, turbo-pumped system only requires a standard power outlet and only takes up a small amount of space on the bench.
The practical chamber size measures a diameter of around 150 mm and enables quick pump down and coating cycle times of approximately 10 minutes.
The usage of ultra-purity carbon rods present in a high vacuum chamber offers the high-quality coating needed for crucial EBSD, TEM, high-resolution SEM, and microprobe work. The modular design allows quick change between a range of applications with improved conditions.
Main features of the 208C High Vacuum Turbo Carbon Coater
- Voltage-controlled rod source provides several evaporation abilities
- The feedback loop allows accurate and persistent coating thickness
- A choice of operation techniques for improved operation
- Automatic evaporation control provides user-friendliness in busy surroundings
- Low cost, high-resolution thickness monitor ensures reproducible results
- 67 L/second turbo pump on a 150-mm diameter thickness chamber provides quick pumpdown
- Optional Dry Scroll Pump available
- Decreases operating cost in numerous ways: No requirement for water cooling; space-saving, no need for warm-up or cool down; compact bench top design, no need for LN2 (dry nitrogen gas optional); and short cycle time
Carbon evaporation supply
The 208C makes use of a completely combined unique electronic feedback-controlled power design for the rod-fed Bradley-type carbon evaporation source.
The tracking of current and voltage is done by sensor wires in the evaporation head where the evaporation source has been part of the feedback loop.
This feature gives the traditional rod-fed carbon source rare stability and reproducibility. The carbon source makes use of two-step ultra-pure carbon rods. The evaporation source can be operated in manual “pulse” or manual “continuous” modes.
The pulsed mode, when utilized in combination with the optional MTM-10 high-resolution thickness monitor, provides absolute control over the preferred thickness of the carbon coating. The automatic mode enables the user to set the voltage and time, which, jointly with the two-step rods, provides a consistent coating with ease of operation.
208C specimen chamber and optional stages
The flexible design of this practical-size chamber accepts two optional stages, which can be instantly implemented. With the addition of one of these stages, the telescopic pillar provides an easy, quick adjustment from long to short working distances to vary the deposition rate.
For SEM, EDS/WDS, and microprobe analysis applications, the Rotary-Planetary-Tilting stage with variable speed, adjustable tilt, and four specimen holders guarantees even coating on multiple samples.
The Rotary-Tilting stage has been specially developed for TEM and analytical applications and holds a 25 × 75 mm (1″ x 3″) glass slide. Both stages are mounted on a mounting collar and can be readily applied in the chamber.
Technical specifications for 208C
Source: Ted Pella, Inc
. |
. |
Chamber Size |
150 mm OD x 165 mm high (5.9” x 6.5”) standard
Variable height, 165 mm - 250 mm (6.5”- 9.8”) optional |
Evaporation Source |
Bradley type (6.15 mm OD rods [1/4”]); Heavy duty stainless construction |
Evaporation Supply |
Microprocessor based feedback loop controlled with remote current/voltage sensing; Safety interlocked; Variable, 180 A max. with over-current protection |
Sample Stage |
Static table holds 12 SEM 1/2” stubs; Height adjustment through 60 mm; Optional rotary-planetary-tilting stage |
Analog Metering |
Vacuum, dual range Atm - 0.001 mb; 1 x 10-3 mb to 5 x 10-6; Current, 0 - 200 A |
Control Method |
Automatic evaporation control using programmed voltage and timer; Full manual override with pulsed or continuous operation; Digital timer, 1 - 9.9 seconds; Digital voltage setting, 0.1 - 5.5 V; Automatic vent |
Electrical Requirements |
100-120 or 200-240 VAC, 50/60 Hz |
Power Requirements |
1200 VA max. |
Turbo or high-speed rotary pump combination
- Pumping Speed: 67 L/second
- Pumpdown Time: 1.5 minutes to 1 × 10-4 mb
- All metal vacuum integrated coupling system that includes an exhaust filter
- Desktop System: Rotary pump fixed on a desktop anti-vibration table
Optional dry scroll pumps available for clean room applications
- Reduced operation charges without the need to check or alter oil or filters
- Oil-free technology removes the likelihood of oil contamination
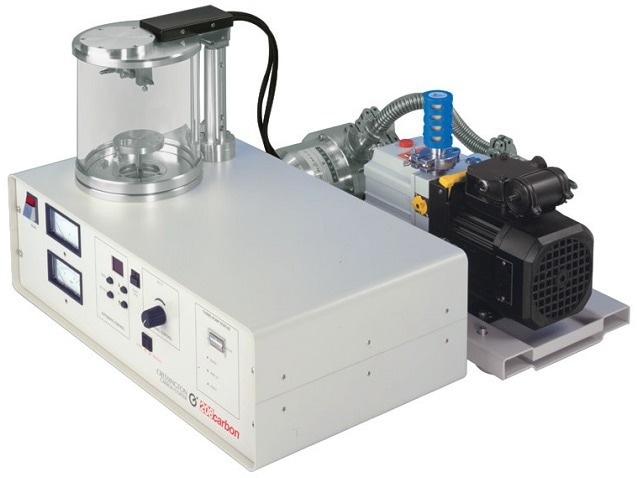
Image Credit: Ted Pella, Inc
Footprint
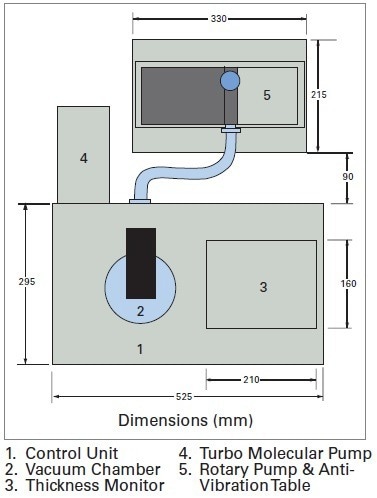
Image Credit: Ted Pella, Inc