SEM-Base® VI from TMC Ametek, is the next generation in STACIS active piezoelectric vibration cancellation. SEM-Base VI has been developed to aid all commercial Scanning Electron Microscopes (SEMs), as well as several Small Dual Beam and Focused Ion Beam (FIB) instruments.
SEM-Base VI offers enhanced vibration isolation performance, a quicker more robust controller, and a sophisticated graphical user interface (GUI). SEM-Base VI will allow more laboratories and facilities to obtain the level of floor vibration needed to fulfill the specifications of the tool manufacturer.
SEM-Base VI utilizes a special “serial architecture” in which the vibration sensors tend to quantify floor vibration, instead of payload vibration. This guarantees that, contrary to other designs, payload resonances do not innately restrict vibration isolation or result in instability.
The vibration sensors are known to be low-frequency inertial velocity sensors that are utilized for utmost sensitivity in the difficult-to-measure sub-Hz range. Once integrated with the special piezo-actuator technology, SEM-Base VI obtains extremely high levels of vibration cancellation, even on floors that are already quiet.
On average, SEM-Base VI offers 6 dB more vibration isolation compared to earlier models. TMC’s next-generation controller, the DC-2020, also features a new dual-core processor and offers tool owners and scientists a highly simple and user-friendly graphical interface for quick system evaluation and operational peace of mind.
While connecting over Ethernet, the DC-2020 makes the SEM-Base GUI in the user’s browser with no extra software or application program to install. Instead, the user could interface with the controller through an onboard menu-driven Liquid Crystal Display (LCD).
The SEM-Base VI advantage
- Hard-mount technology – SEM-Base VI is consistent with all internal SEM vibration control systems and aggressively reduces low-frequency floor vibration starting at 0.6 Hz.
- Active inertial vibration cancellation – SEM-Base VI utilizes low-frequency, high sensitivity inertial velocity sensors to obtain high levels of vibration attenuation, even on quiet floors.
- Serial design with piezoelectric technology – The special serial design and proprietary highforce piezoelectric technology leads to an extensive active bandwidth from 0.6 Hz to 150 Hz and matchless, inertial active vibration cancellation with a 90% decrease starting at 2 Hz.
Specifications
Performance specifications
Table 1. Source: TMC Vibration Control
. |
. |
Active degrees of freedom |
6 |
Active bandwidth |
0.6 Hz - 100 Hz |
Passive natural frequency |
12 Hz nominal |
Effective active resonant frequency |
0.5 Hz |
Isolation at 1 Hz |
40% - 70% |
Isolation at 2 Hz |
90% |
Isolation at ≥3 Hz |
90-98% |
Internal noise |
<0.1 nm RMS |
Operating load range |
Standard capacity: 900 - 2,500 lbs (408 - 1134 kg)
High capacity: 2,500 - 3,200 lbs (1134 - 1452 kg) |
Magnetic field emitted at maximum 4 in.(102 mm) from the platform |
<0.02 µG broadband RMS |
Design, dimensions and environmental and utility requirements
Table 2. Source: TMC Vibration Control
. |
. |
Environmental and safety |
CE and RoHS compliant |
Active isolation elements |
Piezoelectric actuators with minimum 3300 lb. (1500 kg) capacity receive signal from a high-voltage amplifier with an output of up to 800 VDC. Vertical actuators support the isolated payload. |
Passive isolation element |
single stiff elastomer (no compressed air supply required) |
Vibration sensor elements |
downward facing geophone type inertial sensors that measure floor vibration below the isolator and deliver voltage proportional to the velocity of vibration motion |
Active feedback control loop |
Floor vibration is measured, processed and attenuated below the spring supporting the isolated surface |
Dimensions (WxD) |
35.25 x 44.25 in.
895 x 1124 mm |
Height |
6.3 in. (160 mm) nominal,
doesn't change when SEM-Base is switched off |
Operating temperature |
50° - 90° F
10° - 32° C |
Storage temperature |
-40° - 130° F
-40° - 55° C |
Humidity |
< 80% @ 68° F | 20° C, Maximum dewpoint 18 degrees C |
System power requirements |
100, 120, 230, 240 VAC
50/60 Hz AC; <600 W
CE compliant |
Floor displacement |
<800 µin. (20 µm) below 10 Hz |
Built-in controller specifications
Table 3. Source: TMC Vibration Control
. |
. |
Processor |
150/75 MHz dual core |
Sampling rate |
10 kHz |
Analog outputs |
16 channels |
Analog inputs |
16 channels |
Status light |
single LED |
Front panel ports |
1x serial USB 2.0
1x serial Micro-USB
1x Ethernet RJ-45
2x BNC |
User interface |
Front panel LCD display
haracter menu on HyperTerminal
Extended GUI for Microsoft Windows
mbedded Ethernet GUI |
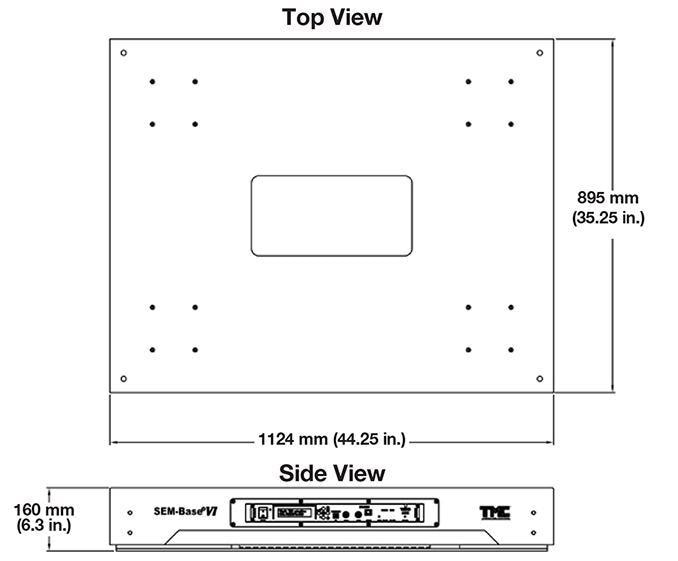
Image Credit: TMC Vibration Control
Performance
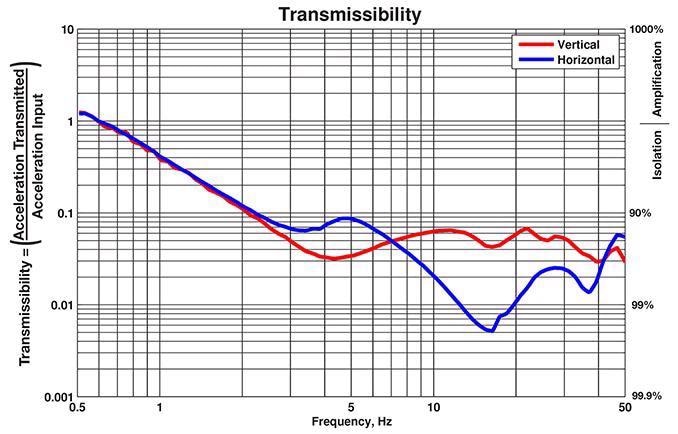
1800 lbs (818 kg) payload tested with simulated vibration at VC-C (500 μin./s, 12.5 μm/s RMS). Image Credit: TMC Vibration Control
Application photos
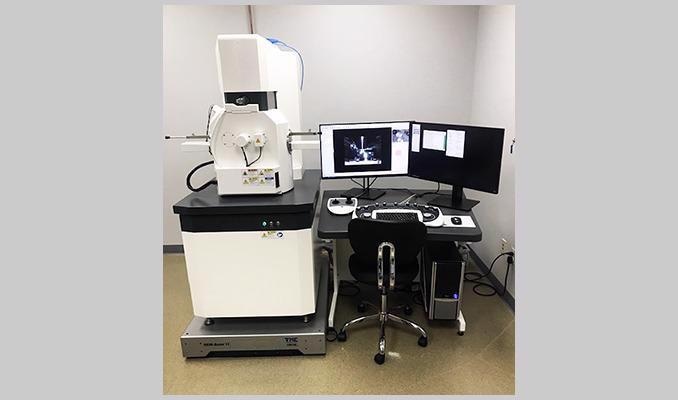
Image Credit: TMC Vibration Control
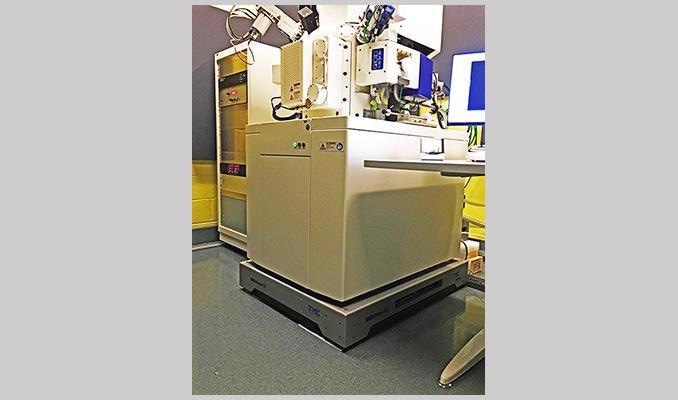
Image Credit: TMC Vibration Control
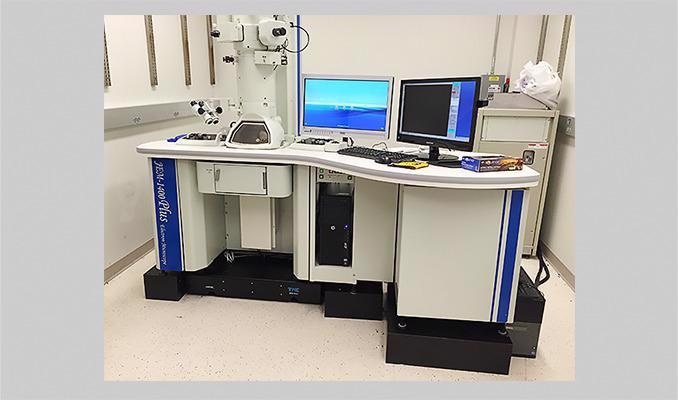
Image Credit: TMC Vibration Control
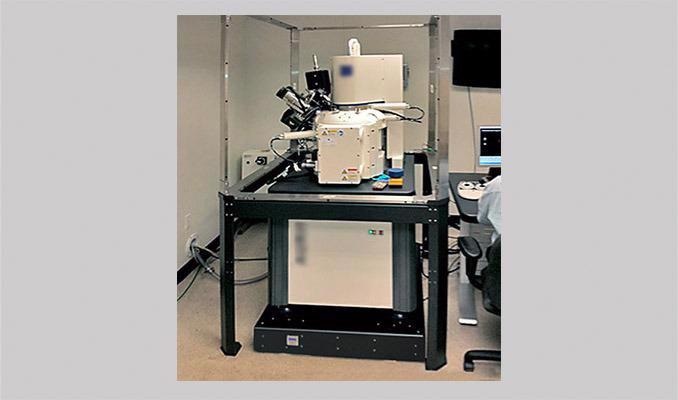
Image Credit: TMC Vibration Control
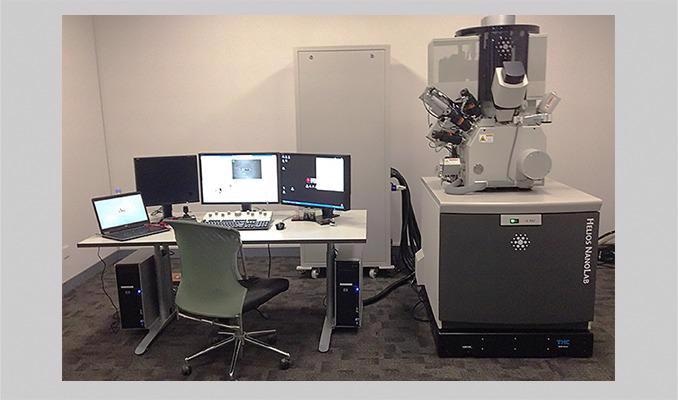
Image Credit: TMC Vibration Control
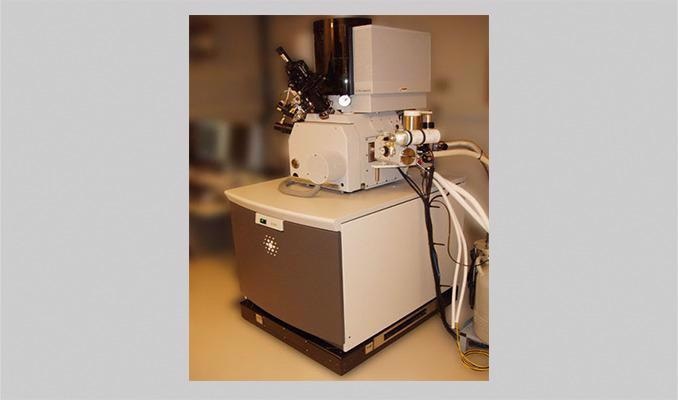
Image Credit: TMC Vibration Control
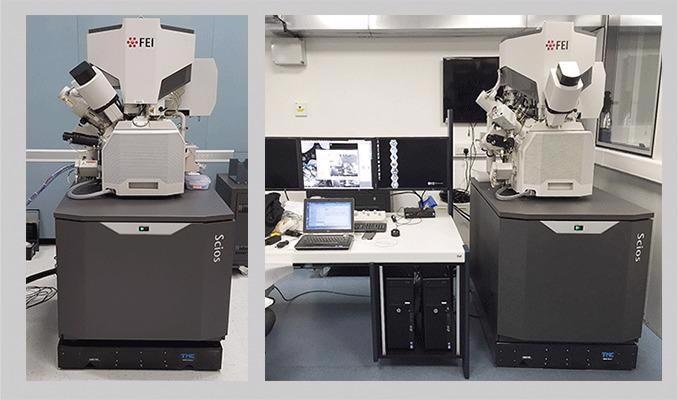
Image Credit: TMC Vibration Control