The unique capabilities of 3D printing have demonstrated value in a range of healthcare applications ranging from tablet manufacture to tissue engineering and implant construction.1
The flexibility to cost-efficiently produce bespoke, patient-specific designs and the ability to control critical properties such as porosity set 3D printing apart from conventional manufacturing techniques. However, the biomedical sector is necessarily limited with respect to materials that can be used, which must meet stringent toxicity and/or biocompatibility standards. The identification of new materials that are suitable for printing remains an ongoing challenge.
Silk is a natural biomaterial already used in biomedical applications, for example, in the form of a knitted surgical mesh, sutures, and therapeutic clothing for the treatment of skin conditions.2 Widely available and easy to sterilize and purify, silk has established biocompatibility and an advantageous property profile for bio-scaffold manufacture. It has already been successfully used to reinforce polymer-based structures produced using extrusion-based 3D printing techniques.3
This article describes experimental work carried out at Deakin University to investigate the feasibility of binder jet printing with silk powders.3 We discuss the test methods used to differentiate silk powders with a high chance of printing success, focusing on the application of powder testing, and explore the properties of printed components. The results demonstrate the viability and potential of binder jetting with a silk powder to make high-resolution bio-scaffolds, and more broadly, exemplify a strategy for characterising natural materials, including waste materials, for printing applications.
The Attractions of Binder Jetting
Binder jetting is a well-established commercial 3D printing technique used with powder feedstocks ranging from metals and ceramics to pharmaceutical formulations. In a binder jetting process, binder droplets flowing from a print head selectively bind areas of sequential powder layers to progressively construct a component of defined geometry (see figure 1). Depending on the application, the result may be a finished part or subject to further processing, such as sintering.
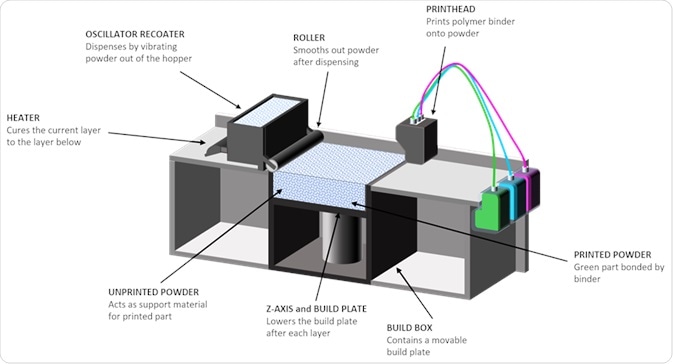
Figure 1: In a BJ printer, layers of powders are selectively bound together to form a printed component.
When it comes to 3D printing with silk, powders can be generated simply by pulverizing silk fibres, thereby preserving native crystallinity that confers critical properties in the printed component, such as slow degradation and good tensile strength. This contrasts with the creation of printing inks for material extrusion, which necessitates the dissolution and dialysis of silk fibre to form liquid silk fibroin, a process that destroys crystallinity and results in regenerated silk products that are weak and brittle.3 Using silk powders as fillers for polymer-based extrusion 3D printing is an option, but binder jetting offers important advantages, including:
- the opportunity to use silk as the matrix for the bio-scaffold, rather than as a filler, to fully capitalise on its property profile
- the ability to print more complex, precisely defined geometries, with potential for porosity control
- structural support for the component during the print process – by the surrounding loose powder bed – enabling the inclusion of features such as overhangs.
Identifying silk powders that will print well is the key to exploiting this potential. There is currently no standard method for evaluating the printability of a powder feedstock from measured parameters, but there is growing evidence of the relevance of certain properties. Successful binder jetting relies on consistent powder flow from the feed hopper and rapid dispersion across the build plate to form a thin layer of uniform density. Powder flowability and spreadability are therefore critical. Effective binding of the powder layers relies on the penetration of liquid ink into the powder bed, a process dependent on bed porosity and surface properties. Particle size and shape have an important role to play in influencing these bulk powder behaviours and the strength of binding between particles, but their aggregate effect, and that of other particle properties, can only be determined through bulk property measurement. Therefore, a robust assessment of powders for binder jetting demands the measurement of both particle and bulk powder properties.
Comparing Silk Powders for Binder Jetting
To identify a preferred candidate for 3D printing, researchers at Deakin compared the properties of two commercially available silk powders (Smiss Natural, China): superfine silk powder (SFSP) with an average particle size of 5µm and fine silk powder (FSP) with an average particle size of 20 µm. These powders were mixed in various ratios with PVA powder (Sigma Aldrich), a solid binder, to create a suitable feed for binder jetting with a water-based ink (Visijet PXL clear, 3D Systems, USA). A commercial binder jetting powder (Visijet PXL core, 3D systems, USA), with an average particle size of 15 µm, was also characterised for reference purposes.
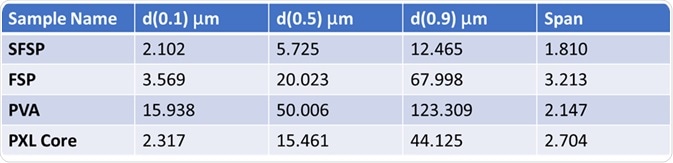
Table 1: Particle size distribution data show that both the d(0.5) and Span of FSP are similar to PXL core; SFSP is a finer powder with a tighter particle size distribution.
Table 1 shows particle size distribution data measured by laser diffraction (Mastersizer 2000, Malvern Instruments, UK) for each of the four powders: SFSP, FSP, PVA, and PXL core. The two silk powders have a d(0.5), or median, particle size consistent with the quoted values for the products, confirming the much coarser particle size of the FSP. However, the data additionally highlight differences in particle size distribution as captured by d(0.1), d(0.9) and Span, where d(0.1) and d(0.9) are the diameters below which 10% and 90% of the particle population lie on the basis of volume and Span is defined as d(0.9) – d(0.1)/d(0.5). These data indicate that FSP has a wider particle size distribution than SFSP and a Span far closer to PXL core. The results also show that PVA has a much coarser particle size, d(0.5) of 50µm, than the other powders.
A wide particle size distribution can be advantageous for 3D printing. While small particles offer high packing density, they are often associated with poor flowability. With a wide particle size distribution, the presence of larger particles helps to improve flowability while at the same time smaller particles fill the interstices between larger particles enhancing packing density. Therefore, these data suggest that as well as performing the role of binder, PVA might improve blend flowability and packing density, and by extension, the quality of printed parts.
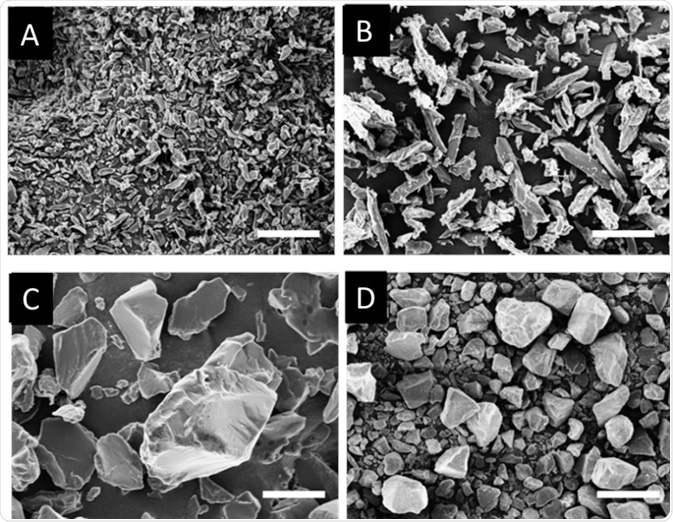
Figure 2: SEM images show the elongated morphology of silk powder particles which differs markedly from the more regular shape of PXL core [A – SFSP; B FSP; C – PVA; D- PXL core]
Figure 2 shows scanning electron microscopy (SEM) images (NeoScope, benchtop SEM JCM-5000, JEOL, Tokyo, Japan) images for each of the powders. Both silk powders have a distinctive, elongated, or needle-like appearance relative to the more regular shape of PVA and PXL core which, in addition, has smooth edges. These images suggest that silk particles may not move easily relative to one another, compromising flowability. Bulk powder testing was carried out to test this and the preceding hypotheses relating to particle size and quantify differences between the powders in terms of relevant bulk powder properties.
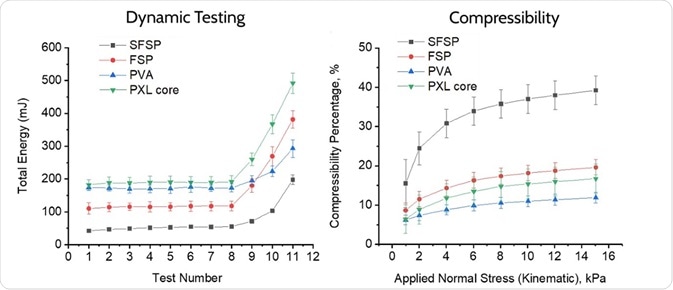
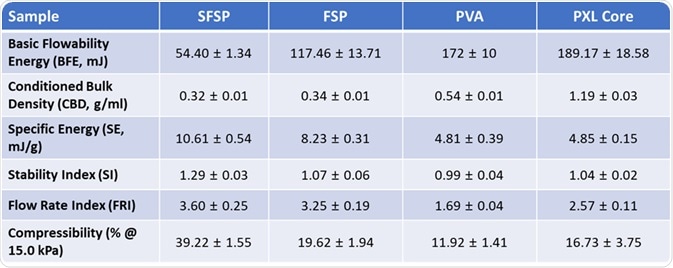
Figure 3/Table 2: Measurements of flowability and compressibility provide highly relevant insight for the assessment of powders for binder jetting.
Figure 3 and Table 2 show flowability and compressibility data generated for each of the powders using a powder rheometer (FT4 Powder Rheometer®, Freeman Technology, UK) by applying the standard test protocols.4 This instrument generates values of dynamic properties such as Basic Flowability Energy (BFE) from measurements of the axial and rotational forces acting on the blade of the rheometer as it passes through the powder sample along a defined path. While BFE is measured during a downward traverse of the blade, Specific Energy (SE) is measured as the blade moves upwards through the sample, imposing a gentle lifting action. Stability Index (SI) is the ratio of BFE measured during test seven (in a sequence of seven repeat tests) to BFE measured in the first test, while Flow Rate Index (FRI) quantifies how flow energy changes as a function of impeller speed, indicating whether a powder flows more easily at higher flow rates.
SFSP exhibits the lowest BFE and highest compressibility; values for FSP are much closer to those of PXL core. Compressibility quantifies how density changes as a function of applied normal pressure. More cohesive powders tend to exhibit higher compressibility because of their ability to form aggregated structures that entrain and retain air. Entrained air dampens the transmission of the force applied by the blade during BFE testing, and generated values are therefore often correspondingly low. In contrast, force transmission is more effective with less compressible powders, giving rise to higher BFE values. The high compressibility and low BFE values of SFSP are consistent with this rationale and suggestive of a relatively cohesive powder.
In contrast, SE values are much higher for the two silk powders than for PVA and PXL core. Since SE values are dominated by the strength of interparticular friction and mechanical interlocking, these results are directly attributable to the morphology of the silk powders.
Trends in SI, FRI, and conditioned bulk density (CBD) provide additional insight into the powders. SI values close to 1 indicate that all the samples are physically stable except SFSP, which has a noticeably higher SI of 1.27. FRI data provide further evidence of the relative cohesivity of the samples with values closer to 1 associated with more free-flowing powders. CBD values for both silk powders are substantially lower than for PVA and PXL core, a result which may be attributed to the morphology of the silk powders and its likely effect on packing density. The smooth regular PXL core particles, in combination with the wide Span of this powder, result in particularly efficient packing and correspondingly high CBD values.
These results identify FSP as superior to SFSP for binder jetting due to better flowability, greater physical stability, and more desirable settling/packing characteristics as evidenced by lower compressibility. Crucially, they show that FSP has a somewhat similar property profile to PXL core, unlike SFSP, which has different characteristics and is less likely to perform well in binder jetting.
Printing with Silk Powders
To assess the potential printing performance of the powders, spreadability tests were carried out using 1:1 FSP/PVA and SFSP/PVA blends, spreading several layers of powder across the printing station. Figure 4 shows images of the resulting powder bed and the spreading roller. The SFSP/PVA blend produced a bed with a rough surface, with significant quantities of powder adhering to the print roller (Figure 4 C/D); this blend could not be easily or uniformly spread. In contrast, the FSP/PVA blend exhibited superior spreadability, evenly filling the print bed and leaving a smooth surface, with no powder remaining on the print roller (Figure 4 E/F). These results confirm that the rheological properties allow the successful identification of the blend with superior spreadability, capturing its more free-flowing behaviour and clearly differentiating it from a blend less suitable for printing. Furthermore, PVA and FSP exhibit dynamic properties more similar to the commercial 3D printing powder - PXL core – highlighting the potential to use rheological testing to identify alternative feedstocks compatible with a specific process. In further experiments, detailed investigations of the print performance of FSP/PVA were carried out.
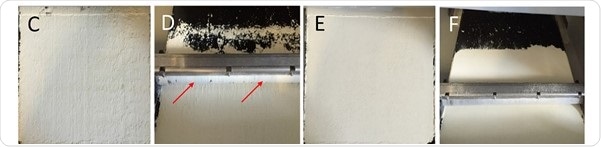
Figure 4: Testing confirms that the superior flow properties of FSP translate into better spreadability performance (C/D – SFSP; E/F FSP).
Figure 5 shows samples printed using FSP/PVA blends in a commercial binder jetting printer (ProJet CJP 460 Plus 3D Binder Jet printer, 3D Systems, USA).
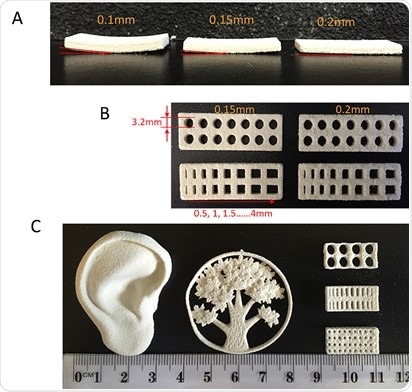
Figure 5: Samples printed in a commercial binder jetting printer using FSP/PVA powder blends including (A) Dense features; (B) Porous features; and (C) Alternative structures
Trials were carried out to investigate the impact of powder layer thickness and FSP/PVA ratio, and trends in porosity were also studied. Crucially, the porosity of FSP/PVA printed samples, typically between 30 and 50%, is well-suited to bone tissue engineering, suggesting that the inherent micro-porosity delivered by binder jetting with this blend is well-matched to the application. Furthermore, green printed parts showed acceptable mechanical strength relative to requirements for load-bearing applications, further confirming their utility for this application.
Unfortunately, the beneficial mechanical properties of the green printed parts were not combined with water stability due to the solubility of the PVA binder. This issue was addressed with some success by solution-based post-treatment with glutaraldehyde; a chemical used to crosslink PVA, with the water stability of printed parts increased by up to one month.
In summary, promising printing results were achieved, with FSP/PVA blends successfully processed in a commercial binder jetting printer to produce water-stable components with the porosity and strength required for bio-scaffolds. Further work would be required to optimise print conditions and blend composition fully.
Moving Forward
The study described here illustrates the exciting potential of silk powders for manufacturing bio-scaffolds via binder jetting, a cost-efficient process for making bespoke components with unique geometries and controlled porosity. 3D printing is already prized for biomedical applications, introducing new materials for printing further extends its value and is a critical ongoing task. Natural materials and/or those with established biocompatibility have a higher likelihood of meeting the demands of the application, but physical characterisation is essential to identify materials that will perform well in commercial 3D printers. Therefore, this study is more broadly useful from the perspective of exemplifying techniques and an experimental approach that can differentiate powders with a suitable property profile. By measuring relevant bulk powder properties such as flowability and compressibility, alongside particle size and shape data, researchers can learn how to select and engineer powders for 3D printing success and accelerate progress towards a wider palette of feedstocks.
With special thanks to the School of Engineering, Deakin University.
References:
1 P. Ahangar et al. ‘Current Biomedical Applications of 3D Printing and Additive Manufacturing.’ Applied Sciences, 2019, 9, 1713. Available to view at: https://www.mdpi.com/2076-3417/9/8/1713/pdf
2 C. Holland et al. ‘The Biomedical Use of Silk: Past, Present and Future.’ Sept 2018, Advanced Healthcare Materials. Progress report. Available to view at: https://onlinelibrary.wiley.com/doi/full/10.1002/adhm.201800465
3 J Zhang et al. ‘3D Printing of Silk Powder by Binder Jetting Technique’ Additive Manufacturing, 2020.
4 Freeman, R. ‘Measuring the flow properties of consolidated, conditioned and aerated powders — A comparative study using a powder rheometer and a rotational shear cell.’ Powder Technology, 2007, 174, 25-33.