The “8 Waste” methodology of lean management principles focuses on lab processes in a new METTLER TOLEDO guide and offers a useful way to identify non-value adding or unnecessary steps in routine workflows. Commonly performed tasks benefit from streamlining in terms of productivity and cost savings.
Labs often perform the same operations repeatedly, causing process steps to become familiar. This makes it difficult for lab operators and management to assess these processes with a critical eye—particularly in the absence of a systematic methodology to help them identify wasteful or unnecessary actions.
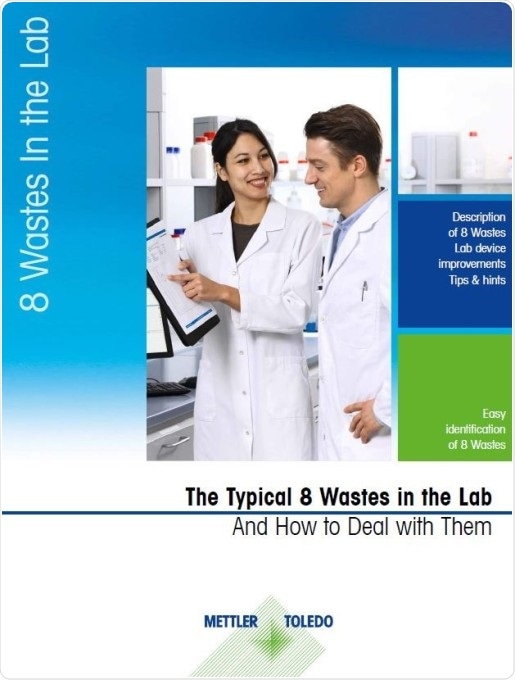
Created with the help of both internal and external process experts, METTLER TOLEDO’s “8 Wastes Guide” will provide lab operators and managers with a concrete methodology for identifying time- and resource-wasting lab efforts. This will help optimize routine workflows such as buffer preparation, batch release, and other common activities.
“8 Wastes” were originally identified by Toyota’s chief engineer Taiichi Ohno within the context of their manufacturing program. Applying this effective framework to labs of all types can improve lead times and process accuracy. This can benefit both internal and external clients and result in processes that are more easily scalable to production volumes.
METTLER TOLEDO’s “8 Wastes Guide” describes what the 8 wastes are, according to the acronym "DOWNTIME", which refers to:
- Defects
- Over-production
- Waiting time
- Not engaging all employees
- Transportation
- Inventory
- Motion/distances
- Extra-processing
It goes on to provide examples of where these wastes typically occur in a laboratory environment - with examples from a range of workflows - and translates its wisdom into applicable guidelines for assessing workflows using common lab equipment. Laboratory managers and operators can gain a clear idea of where lean potential can be found in day-to-day processing efforts.
Overall, the “8 Wastes” guide will help eliminate errors and improve overall quality and efficiency by ensuring that processes are optimized and sustainable. The guide will also show how to determine the cost- and resource-savings impact of changes that are being contemplated.