If Lean Laboratory is properly implemented, the results can be impressive ─ delivering simpler workflows and processes, reduced lead times, and increased laboratory efficiency.
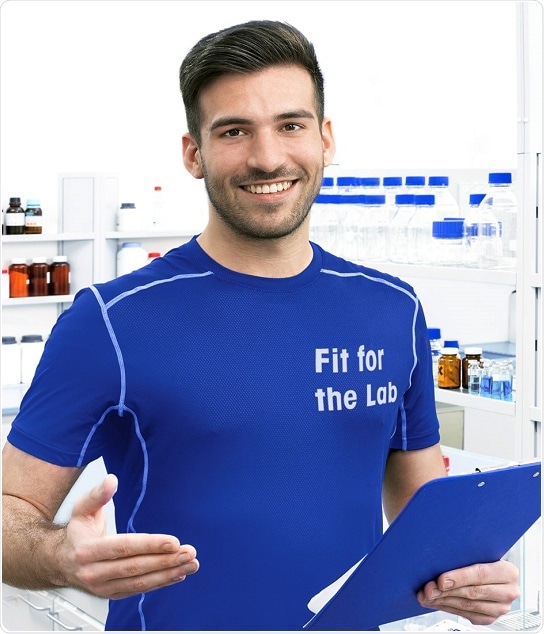
Successful lean manufacturing principles are increasingly being adopted in the laboratory environment. The challenge is to understand how best to put Lean Laboratory into practice in a particular workplace.
A two-part webinar series, "Employing a Lean Lab Approach to Optimize Lab Processes", co-presented by lean laboratory expert, Erwin Studer, explains the concept of Lean Lab and how it can be applied to established laboratories, or the design of a new laboratory.
Lean methods help to ensure that laboratory processes are clearly defined, structured, and controlled to deliver more consistent and predictable laboratory performance. This generates a detailed understanding of lab capacity and resourcing requirements and leads to a positive impact on lead time and costs, productivity, and right-first-time (RFT).
Part 1: Work Smarter, Not Harder introduces the basic concepts of Lean Laboratory and explains the 10 areas to consider in assessment of the current status of a lab. These are used to guide the improvement of existing processes. It is often the simplest or smallest changes that can bring about the most significant improvements.
Part 2: Improve Productivity goes deeper into value stream mapping and performance management. Advice is given on how to identify value-adding or unnecessary steps in a workflow, using the example of sample preparation for analysis. This allows participants to identify the issues which could have the biggest impact on improving lab productivity. Measuring the impact using a number of Key Performance Indicators (KPI's) is also discussed.
Watch these recorded webinars now at: