The worst-case scenario for many laboratories is sample freezer failure. It is crucial to have a process in place in the event that a ULT freezer malfunctions.
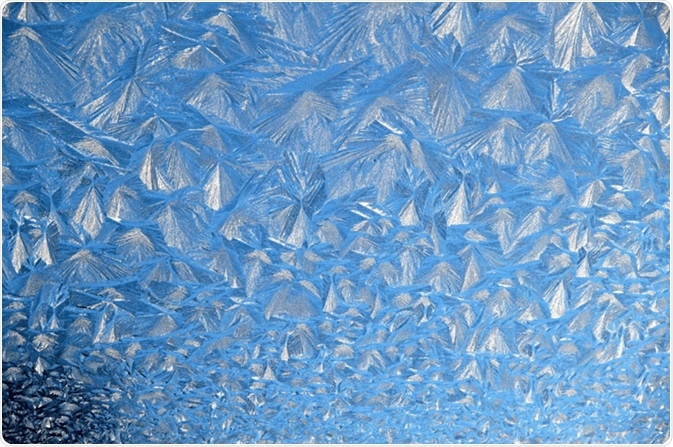
It is a disaster for sample storage centers and laboratories if their freezer fails and irreparable damage is caused to samples.
Whether it is caused by a temperature control issue, the failure of a compressor, or the power supply, an ultra-low storage freezer malfunctioning can mean that important samples are unviable in a matter of hours.
With the significant number of user variables and parts in upright freezers, it means that failure is inevitable when they are utilised for long periods of time.
The Effects of Sample Freezer Failure
A freezer malfunction at a hospital in Los Angeles in September 2019 resulted in the destruction of 56 stem cell samples taken from child cancer patients. The temperature sensor of the freezer did not identify the failure, so it was not found until the samples had already been destroyed.
Typically, stem cells and embryos are frozen specifically due to the concern they will not be available - or will be of inferior quality - if an attempt is made to produce them later. This is a tragedy for the victims.
Adam Wolf, Lawyer for the Families Involved
A similar but significantly greater failure happened in 2012 at the Harvard Brain Tissue Resource Center when the world’s biggest storage of autistic brain samples experienced a freezer malfunction.
The temperature alarm of the unit was not raised even though the inside of the freezer was similar to that of a household refrigerator. It was said that this malfunction may have set research in autism back by a decade.
A range of crucially important samples is kept in research centers across the globe. They are commonly an integral element of scientific investigations into diseases that can potentially impact billions of people around the world.
These events demonstrate the issues created as a result of the unpredictable malfunctions of upright mechanical freezers. One might ask what the solution is when upright freezers are so prevalent in laboratories found across the globe.
Minimizing Upright Freezer Failure
There are several ways to work around the issue to make sure that samples are viable if the worst-case scenario occurs. Having one or several empty back-up freezers operating consistently can ensure that samples can be transferred with efficiency if a freezer malfunctions. However, this incurs both financial and environmental costs.
Manufacturers of ULT freezers understand the issues involved with freezer failure. Power back-ups are often built-in to the systems and manufacturers publish official instructions on the best way of avoiding complete sample loss when a freezer fails.
A number of freezers include temperature alarms to show when temperatures are not safe. As the two examples outlined earlier demonstrate, these are not always trustworthy.
There are a few widespread sources of failure for ULT freezers, for example:
- A compressor malfunction. These normally utilise a refrigerant like propane (R290) or ethane (R170).
- A power cut. A back-up power system may be included with the freezer, but these can be unreliable and restrictive.
- Electronics malfunction. The temperature of a freezer is often controlled digitally.
- HVAC system malfunction. The upright mechanical freezers’ design means there is a substantial quantity of heat being dispersed. This heat can cause the freezer to warm which can damage samples if the HVAC system malfunctions.
- Just forgetting to close the door. While a number of freezers include indicator alarms to show when the door has not been closed, this continues to be a concern.
Samples must be transferred to a back-up freezer straight away if the freezer fails and samples are no longer safe, so long as the fault is discovered before samples were harmed.
The person responsible should then be told about this issue. Each facility should have a system in place that is clearly shown on or near to the freezer itself.
Even if all of these systems and back-ups are being used, failure is still the price to be paid for utilising ULT upright freezers.
The Best Solution
If leaving the door open, HVAC malfunctions, power cuts, and compressor faults are the key factors leading to freezer failure, then eliminating these issues is the best solution.
A solution to all of the problems above and an alternative to mechanical minus 80 °C upright freezers is the MVE Variō™ series variable rate nitrogen vapor freezers.
Operating with ease at a completely user-specified temperature between -20 °C and -150 °C, liquid nitrogen is pushed through a heat exchange system by the Variō™ which uses the vaporisation energy of liquid nitrogen for stable and accurate temperature control.
Due to its exclusive design, the Variō™ does not include a compressor and uses less than 1% of the power consumed by upright freezers. So long as LN2 is consistently supplied, the system will continue to keep samples frozen. The requirement for an unreliable and expensive HVAC system in the cryo-room is also removed.
The contamination risk is substantially reduced as samples are not stored in or near to liquid nitrogen, dissimilar to standard cryogenic LN2 freezers. This also means that if the lid is not closed, the temperature can easily remain stable for some time.
The degree of insulation also means that if the liquid nitrogen supply ceases, it would take four days for the temperature to increase from -80 °C to -60 °C.
In summary, a much more reliable and secure solution to mechanical ULTs is found in the Variō™ variable rate sample freezer. While regular upright freezers are used industry-wide, it is up to individuals to evaluate whether the advantages outweigh the weaknesses.
About Air Products PLC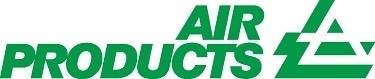
Air Products touch the lives of consumers around the globe in positive ways every day. With approximately 16,000 employees and operations in 50 countries, we serve customers across a wide range of industries from food and beverage to medical, energy, and transportation. We supply a unique portfolio of atmospheric and process gases, equipment, and services. Founded in 1940, Air Products has built a reputation for its innovative culture, operational excellence, and commitment to safety and the environment. Our passionate, talented, and committed employees from a diversity of backgrounds are driven by Air Products’ higher purpose to create innovative solutions that benefit the environment, enhance sustainability and address the challenges facing customers, communities, and the world.
Sponsored Content Policy: News-Medical.net publishes articles and related content that may be derived from sources where we have existing commercial relationships, provided such content adds value to the core editorial ethos of News-Medical.Net which is to educate and inform site visitors interested in medical research, science, medical devices and treatments.