Release liners are a key component in medical products’ overall development and performance, for example, transdermal drug delivery systems, medical devices, advanced wound care dressings and pharmaceutical packaging products.
Release liners are required to offer consistent release performance and inertness in the end-use application while simultaneously adhering to increasingly strict regulatory criteria around performance, quality, purity and cleanliness.
It is imperative that careful evaluation and analysis be conducted to ensure the most appropriate release liner is chosen for a specific drug or medical product under development.

Image Credit: Shutterstock
Adhesive formulations may contain a range of wetting aids, viscosity modifiers, tackifiers, fillers and other additives, any of which could affect release performance.
The drug loaded into the adhesive adds further unknowns and complications, meaning that it is important to determine the compatibility of the release liner materials with the pharmaceutical ingredients as early as possible.
The sheer range of factors involved in this process means that it is advisable to evaluate several candidate release liners as part of the medical liner selection process.
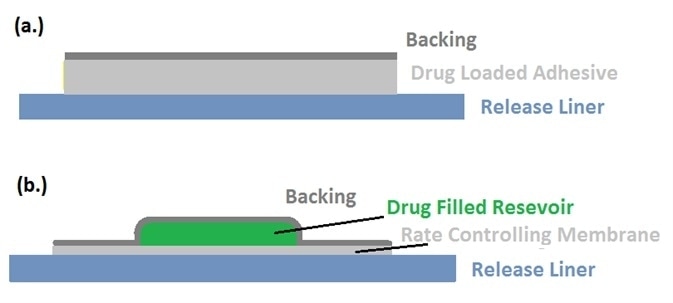
Figure 2. Schematic views of liners holding (a) a drug-loaded adhesive product, and (b) drug-filled reservoir. Image Credit: IEEE Globalspec.
Release liners fulfill several key roles in medical device manufacturing and pharmaceutical packaging – release liners package and protect a diverse array of products (Table 1).
Table 1. Release liner applications in drug delivery, medical device and pharmaceutical packaging products. Source: IEEE Global Spec
Medical / Pharmaceutical Applications |
Product Examples |
Diagnostic & Point of Care |
Diagnostic Test Strips (blood glucose, cholesterol, urinary tract infections)
Point of Care / Diagnostic Devices |
Drug Delivery & Pharmaceutical Packaging |
Transdermal Drug Delivery System (TDDS)
Drug Loaded Monolithic Matrix
Resevoir with Rate Controlling Membrane
Transdermal / Medicinal Patch
Transmucosal Drug Delivery System (TMDS)
Buccal Mucosal System
Oral Thin Films (OTF) / Oral Strips
Pharmaceutical Packaging Tapes |
Fixation, Surgical & Wound Care |
Advanced Wound Dressing (extended wear, burn treatment, MVTR, etc.)
Catheter Placement
Incise / Opthalmic Incise Films
IV Holders
Medical Fixation Tapes
Ostomy Pouches / Components
Surgical & Isolation Drapery |
Medical Sensors & Electrodes |
Disposable Electrodes
ECG, EKG and TENS Pads / Electrodes
Grounding Pads
Oxygen Sensors |
OTC / Consumer Healthcare |
Cosmetic Patches ( Face strips, acne pads, etc.)
Eye Patches
First Aid Bandages & Tape
Hygiene Products (diapers, sanitary napkins, incontinence pads)
OTC Therapeutic Patches |
Process Carrier Liner |
Enables Handling, Conversion & Assembly of Pharmaceutical & Medical Products |
They often act as process carriers, allowing easier handling, conversion and assembly by ensuring that adhesive medical products do not stick together.
Medical liner construction and manufacturing
Release liners are comprised of a release coating on a paper or cloth substrate or a plastic film (Figure 4) – the latter being the most commonly used in medical release liners.
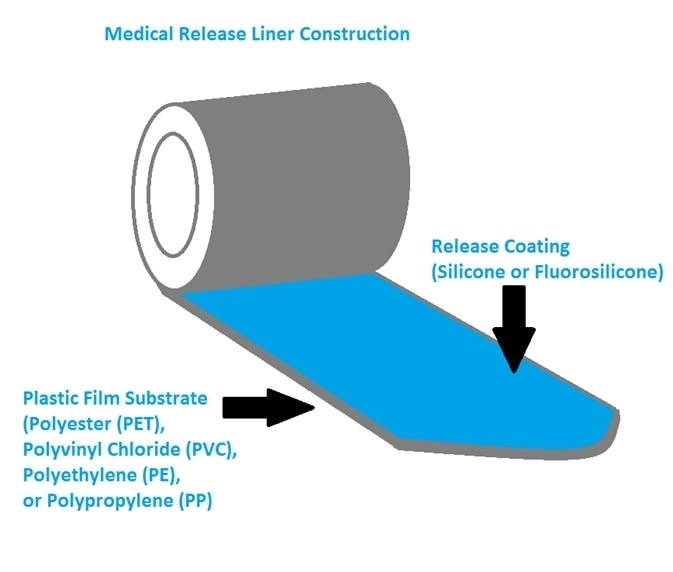
Figure 4. Sketch of medical release liner construction. Image Credit: IEEE GlobalSpec
These medical release liners are manufactured to precise coating weights on high-speed web coating or roll-to-roll machines in cleanroom environments. Once it has been deposited onto the substrate, UV light is used to set or dry the release liner coating.
The plastic films and substrates utilized in medical release liners are generally polyvinyl chloride (PVC), polyethylene (PE), polyester (PET), polypropylene (PP) or made from various fabrics.
It is important that the liner substrate offers appropriate mechanical properties such as elongation percentage, tensile strength and tear resistance in order to avoid breaks during handling and conversion processes. The film must be cut cleanly during any slitting, die-cutting and related converting steps.
Polyethylene and polyester substrates typically offer improved tear resistance. Polyethylene and polyester carrier films tend to be available in wider gauge ranges (100 to 2300 and 92 to 1400 gauge, respectively) than polystyrene and polyvinyl chloride films (~800 to 1000 gauge).
The release liner substrate must be rigid enough that healthcare professionals or patients can easily peel off the liner. Polyester typically offers improved die-cutting and kiss-cutting performance over PP, PVC and PE.
Some applications may require consideration to be given to other properties such as thermoformability, optical transmission or optical clarity.
For example, the optical clarity of the release may impact a medicine-filled dressing’s ability to be properly positioned over a wound while still allowing this to be monitored for any allergenic response.
Other designs may require the creation of a reservoir well by thermoforming the substrate material. Both polystyrene and polyvinyl chloride films can be thermoformed, while polyester substrates offer exceptional smoothness and optical clarity.
Table 2 details thicknesses, key properties and application suitability for a range of films employed in VERSIV ™ medical grade release liners.
Table 2. VERSIV ™ medical release liner film types, liner gauge availability and their key properties for drug delivery, medical device and pharmaceutical packaging applications. Source: Versiv Composites Limited
Film |
Gauge |
Application |
Key Properties |
Polyester (PET) |
92 - 1400 |
Pharmaceutical, Toiletries, Health & Beauty
Transdermal, Hydrogeis, Wound Care, EKG Hygiene |
- High Tensile & Tear Resistance
- Excellent Smoothness
- High Clarify
- Gauge Control
- Temperature Resistanace
- Recyclable
- Back side Printable
- Mechanically Stable
- Spliceable
|
Polystyrene (PS) |
750 - 1000 |
Hydrogeis, Wound Care, EKT Piggyback |
- Thermoformable
- Good Stiffness
- Back Side Printable
|
Polyvinyl Chloride (PVC) |
800 - 1000 |
Transdermal, Hydrogeis, EKT |
|
Polyethylene (PE) |
100 - 2300 |
One / Two Side, Transfer Wound Care, Hygiene |
- Tear Resistance
- Conformable
- High Yield
|
* Represents typical performance properties and should not be used for specification purposes.
A release liner’s functionality greatly depends on the release coating, which provides its non-stick or release characteristics. Silicone and fluorosilicone are the most used release coatings for medical release liners.
Release liners must possess consistent coating thickness levels to avoid silicone skip (too thin) and over-coating of silicone (too thick). Inconsistencies in coating thickness may result in issues with dispensing, patch or device movement and conversion.
It is important that the medical release liner avoid pre-dispensing – the liner must retain the drug delivery product or medical device until the liner is manually peeled off.
Release coatings may be UV-cured or thermal-cured. An optimum release coating will exhibit slow degradation and long shelf life, coupled with a high degree of chemical stability. It must also maintain consistent release properties throughout the medical product’s lifetime.
UV-cured release coatings offer a warranty and shelf life of 12 months, while thermal-cured coatings offer a 6-month warranty and shelf life.
Both UV- and thermal-release coatings offer good optical clarity, while release coatings may be water-based and solvent-free, solvent-based or completely solid.
It is possible to adjust a release liner’s release properties from easy, to moderate, to tight – while an easy release liner may be removed using minimal low peel force. A tight release liner necessitates the use of a higher peel force in order to remove the adhesive medical product.
Numeric peel or release force values are provided in force per length (g/in, cN/m or N/m). These values can be determined through the measurement of peel force at a controlled peel rate (in/min, cm/min).
Medical release liners can be provided with peel release levels between 5 to 200 g/in. Differential release liners feature release coatings on either side, which possess varying levels of release – a potentially useful feature for more sophisticated multilayer medical product constructions.
Single-coated release liners are suitable for the majority of medical applications, such as wound care dressings, transdermal drug delivery patches, surgical tape and electrodes.
The easy release is ideal for applications that use a soft silicone gel adhesive or delicate drug-loaded adhesive, as this helps reduce any risk of damage to the gel or adhesive.
Adhesives are viscoelastic materials, meaning that the peel or stripping rate can influence the effective release force.
A release profile can be used to plot the release force for a range of peel rates, though it is recommended to ensure a flat release profile so that release force is consistent when working with changing manufacturing processes or differing end-use peel forces.
Release properties can also be impacted by peel speeds, the adhesive used, temperature, time at temperature (Keil aging) and surface roughness.
Each manufacturer employs its own distinct release-level designations and test methods, so working with the same supplier throughout the selection process is recommended.
The adhesive must not transfer to the release coating or otherwise be retained, and the release coating must not transfer to the adhesive. The release coating is required to keep the adhesive tacky because any transfer could inhibit the adhesive’s stickiness or impair drug delivery.
The release liner is discarded in the majority of applications, but specific medical applications may necessitate its reuse, repositioning or reapplication, for example, sensors or TENS electrodes. In these applications, it may be necessary to peel an adhesive-coated medical device on and off the release liner.
A range of release coatings can be provided to accommodate specific medical adhesives or drug-loaded adhesives.
For example, silicone release coatings are suitable for use with polyisobutane (PIB), acrylic (polyacrylate) and polyisoprene (synthetic rubber) adhesives.
Silicone and soft silicone gel adhesives are seeing increased use in wound dressing applications and medical devices due to their gentler action, which results in less trauma on injured tissue or other delicate skin. Silicone adhesives do require the use of a fluorosilicone release coating, however.
Table 3. Suitability of silicone and fluorosilicone release coatings for several adhesives commonly used in medical applications. Source: IEEE GlobalSpec.
Medical Release Liner Coating |
Compatible Adhesive |
Silicone
(Polysiloxane) |
Acrylic (Polyacrylate)
Polyisobutane (PIB)
Polyisoprene (Synthetic Rubber) |
Fluorosilicone |
Acrylic (Polyacrylate)
Polyisobutane (PIB)
Polyisoprene (Synthetic Rubber)
Silicone PSA |
Drug Master File (DMF) and compliance factors
A medical liner with appropriate film type, thickness, release level and other relevant properties can ensure a product’s operational and technical success, but regulatory success is a more complex issue.
A medical product is not permitted to go to market without appropriate regulatory compliance and approval.
Release liners employed in a medical product are required to meet relevant food and drug contact regulations and standards; for example, FDA CFR 177.160, USP, Ph.Eu. and EDQM.
There are also regulations like USP 467 in place that legislate a liner’s purity or levels of contaminants (including metal, monomer and solvent residuals) to ppm concentrations (Table 4).
Table 4. UPS 467 Class 2 residual solvents ppm levels. Source: Table 2 in USP 467
Solvent |
PDE (mg / day) |
Concentration Limit (ppm) |
Acetonitrile |
4.1 |
410 |
Chlorobenzene |
3.6 |
360 |
Chloroform |
0.6 |
60 |
Cumene |
0.7 |
70 |
Cyclohexane |
38.8 |
3880 |
1,2-Dichloroethene |
18.7 |
1870 |
1,2-Dimethoxyethane |
1.0 |
100 |
N,N-Dimethylacetamide |
10.9 |
1090 |
N,N-Dimethylformamide |
8.8 |
880 |
1,4-Dioxane |
3.8 |
380 |
2-Ethoxyethanol |
1.6 |
160 |
Ethylene glycol |
6.2 |
620 |
Formamide |
2.2 |
220 |
Hexane |
2.9 |
290 |
Methanol |
30.0 |
3000 |
2-Methoxyethanol |
0.5 |
50 |
Methylbutylketone |
0.5 |
50 |
Methylcyclohexane |
11.8 |
1180 |
Methylene chloride |
6.0 |
600 |
N-Methylpyrrolidone |
5.3 |
530 |
Nitromethane |
0.5 |
50 |
Pyridine |
2.0 |
200 |
Sulfolane |
1.6 |
160 |
Tetrahydrofuran |
7.2 |
720 |
Tetralin |
1.0 |
100 |
Toluene |
8.9 |
890 |
Trichloroethylene |
0.8 |
80 |
Xylene* |
21.7 |
2170 |
* Usually 60% m-xylene, 14% p-xylene, 9% o-xylene with 17% ethyl benzene.
BSE/TSE requirements state that the release liner must be free of animal-based raw materials. It should also be able to withstand EtO, UV or thermal sterilization regimes designed to meet microbial limits without suffering any property degradations.
It is also important that the release coating does not transfer, leach out additives or otherwise contaminate medicine in a reservoir, a drug-loaded adhesive or monolithic matrix.
The release liner should also be able to avert medicine leakage from a drug reservoir, and it should not extract or react with any of said medicine in a reservoir or a monolithic matrix.
Manufacturers and users of medical liners must be aware of additional compliance restrictions around REACH and the liner being free of allergens, latex, phthalates and melamine.
A specific medical packaging product may be awarded permitted status or a broader approval status. FDA approval affirms testing of the raw materials for compliance. Permitted materials have been reviewed and are considered to be free of harmful effects for certain FDA categories.
Medical release liners should be able to demonstrate an FDA DMF (Type III Packaging) status before being incorporated into pharmaceutical packaging or a medical device.
A Drug Master File (DMF) includes comprehensive documentation on the raw materials, formulation, processing, testing and analysis of a medical release liner, confirming that this meets all required FDA regulations and standards.
The Drug Master File often features proprietary information, so its contents remain confidential between the FDA and the liner OEM. Any medical manufacturer OEM incorporating a release liner into a medical product will refer to the DMF for the liner in its drug application to the FDA or other notified body.
Within this reference, the release liner OEM will provide a Letter of Authorization, allowing the medical manufacturer OEM to reference the DMF numbered product as part of the drug application.
Manufacturers of medical release liners frequently partake in thorough audits of quality management systems and facilities to ensure compliant processes.
Full GMP manufacturing is not required because release liners are deemed an inactive packaging product by the FDA. Despite this, medical release liners must be manufactured in cleanrooms that are free of pests and microbial contamination.
Recommendations and next steps
There are several factors that must be considered when selecting a medical release liner. The release liner must be strong enough to withstand conversion, handling and assembly throughout the various stages of medical device manufacturing.
The correct degree of rigidity allows the release liner to be peeled off the pressure-sensitive adhesive with ease, while the optimum release coating type will be influenced by the desired release level, the adhesives in use and the medicine being released.
All medical release liners are required to have FDA DMF status. The use of a release liner without DMF status is not recommended, as this can impede or disrupt the regulatory approval process for a medical product.
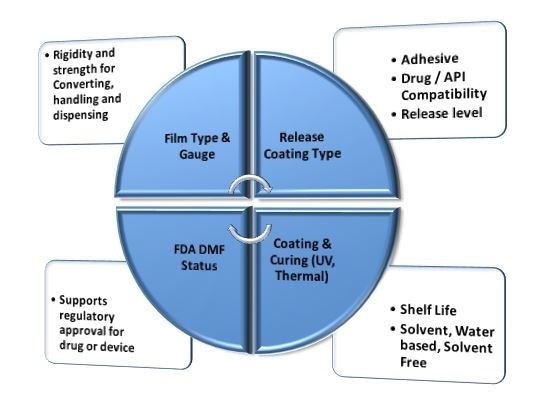
Figure 6. Factors for medical release liner selection. Image Credit: IEEE GlobalSpec.
Medical liner selection should begin with the sampling and testing of several release liner samples in product assemblies. This should be completed using the actual adhesive or drug-loaded adhesive formulations.
Once the range of challenges around design, approval and implementation of products using a medical liner has been fully considered, a liner can be selected.
It is advisable to work with a competent, experienced release liner OEM such as Versiv Composites Limited from the beginning of the development process in order to maximize performance, reduce costs and better troubleshoot problems.
There are several recommended steps for selecting a medical release liner. These include:
- Evaluate adhesive or drug-loaded adhesive formulations with an appropriate release liner supplier
- Choose appropriate FDA-approved medical liners with DMF status
- Screen a diverse array of release liners prior to shortlisting candidate liners
- Evaluate and thoroughly test UV-silicone release systems first because these liners exhibit a longer shelf-life
- Be patient – approval for new drugs and medical devices can take between 3 and 5 years
The selection of a widely-recognized, reliable and robust release liner supplier is essential. The supplier should ideally offer a broad product portfolio and custom engineering capability and should be able to rapidly respond and provide a solution to any medical liner implementation issues throughout the product development process.
When a suitable, reliable, high performance medical release liner system has been selected for an application, it is also important to maintain product quality and minimize product variability by working with a single release liner OEM, such as Versiv Composites Limited.
About Versiv Composites Limited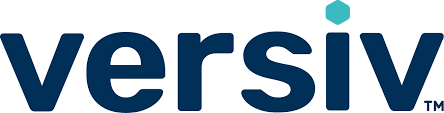
Versiv™ is a recognized expert in high-performance, technology-driven, composite films and fabric solutions. Through our ability to provide proven products and customized solutions we serve customers across a diverse array of sectors.
Our composite materials encompass a broad range of high-performance material solutions on the market, designed and manufactured with the most demanding applications in mind. At the core of our offering is our expertise in films and fabrics composites and true versatility of the products that we offer.
Sponsored Content Policy: News-Medical.net publishes articles and related content that may be derived from sources where we have existing commercial relationships, provided such content adds value to the core editorial ethos of News-Medical.Net which is to educate and inform site visitors interested in medical research, science, medical devices and treatments.