The Integral (area under the curve) of Viable Cell Concentration (IVCC), also referred to as the Integral of Viable Cell Density (IVCD), is a key calculated metric in cell culture operations.
The IVCC measures the effective working time for a dynamic viable cell concentration within a specific timeframe relative to the calculation of man-hours.
The calculation of IVCC for a specific culture timeframe can be utilized with product titers to evaluate culture productivity trends within specified timeframes of the process. They can also be utilized to estimate nutrient consumption profiles based on cell-specific nutrient requirements for a process.
In fed-batch processes, the calculated IVCC is critical for the characterization of the culture progression and for determining process action concerning bolus feed additions.1
Calculated changes in IVCC may be employed for the direct evaluation of changes in nutrient profiles in culture. Subsequently, the IVCC can be used to determine the volume and concentration of bolus addition required to return to a specific concentration set point.
Calculating IVCC
Traditionally, the trapezoid approximation between two off-line VCD data points is used to calculate an IVCC approximation, as shown in Figure 1.
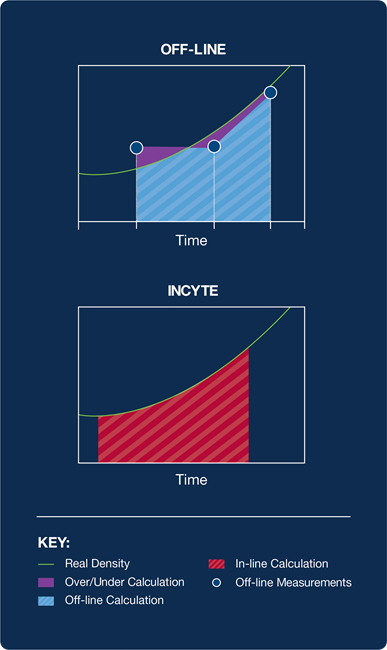
Figure 1. Off-line trapezoid calculation compared to permittivity calculation. Image Credit: Hamilton Company
The accuracy of the trapezoid calculation on the culture depends on the linearity of the culture growth between samples and the measurement frequency.
The intrinsic non-linearity of cell growth, large time gaps between off-line samples, and errors in measurement present in off-line sampling methods all contribute to the limited predictive capacity offered by IVCC calculations that are based on off-line VCD.2
The benefit and accuracy of the IVCC calculation can be improved significantly by replacing periodic off-line sampling with the continuous measurement of viable cell concentration via in-line permittivity measurement.
A continuous permittivity-derived VCD measurement can be utilized to enhance the quantity and resolution of input data for the trapezoid calculation, offering a robust IVCC calculation.
In addition, transitioning from off-line discrete sampling to continuous in-line measurement facilitates the development of automated calculation and process control strategies that are not feasible using only off-line sampling.
The advantages of better control capabilities are clear when evaluating modified strategies for process improvement or improving consistency between replicate batches.
Uses of on-line calculated IVCC metrics
At present, permittivity-derived IVCC calculations have been employed in both predictive and feedback control schemes in fed-batch processes.
For example, in one feedback control study, permittivity-calculated IVCC values were employed to establish the amount of nutrients that must be added to each bolus on a 24-hour fixed-feed schedule.
As shown in Figure 2, the process performance profiles were compared to the historical off-line-calculated IVCC process.
Similar total feed volumes and process titers were obtained between the runs, proving the equivalence of permittivity-calculated bolus addition to an established historical methodology, but without the demand for manual labor and sampling efforts.2
Additionally, permittivity-derived IVCC calculations were demonstrated to be less prone to errors and more consistent than offline VCD calculations.
This means that permittivity-derived IVCC calculations offer a more reliable signal, as well as increasing automation capabilities (including automated process control)3 and minimizing manual labor.
A follow-up study used the same automated permittivity-calculated IVCC value. It revealed that automation allowed the feeding frequency to be modified from every 24 hours to every four hours within the same process.
This more frequent feed schedule allowed smaller amounts of nutrients to be added for a given bolus addition.
IVCC calculations using offline VCD can offer limited predictive capability because of the intrinsic non-linearity of cell growth, large time gaps between offline samples, and error in the measurement itself.
A significant increase in titer production (as much as 20%) was realized with this modified strategy relative to historical process benchmarks.3
In another study, predictive feed control was employed using an in-line permittivity signal to determine the culture growth rate using IVCC and predict future nutrient feed demands for the subsequent feed addition.
Implementing an automated dynamic feed system that employs permittivity-derived calculations and a feed frequency of four hours initially exhibited an insignificant improvement in yield in comparison to a fixed 72-hour bolus strategy.
However, when the modified feed frequency was applied with IVCC-expedited media optimization, the titer increased by approximately 50% compared to the baseline platform process and approximately 20% compared to the optimal feed without modified feed frequency.4
Creating a dynamic feeding strategy was fundamental to effective media optimization, with the growth rate feeding strategy eliminating the need for developing specific dose and frequency strategies for each iteration of media reformulation.
As PAT and automation have a greater role in biopharmaceutical operations, continuous in-line methodologies for process control will become increasingly important.
In-line permittivity offers a robust, low-complexity tool for measuring biomass growth throughout a run. It also enables the replacement of offline sampling and measurements when calculating the parameters involved in determining critical culture variables.
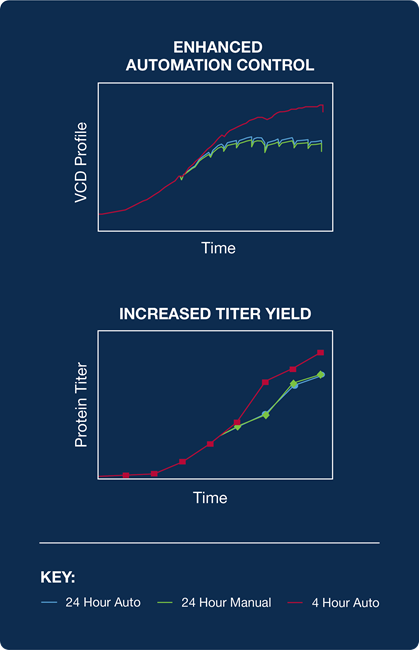
Figure 2. Benefits of permittivity control. Figure includes increased consistency (more accurate calculations), improved automation control (24 to 4 hr), and improved titer yield (dynamic control). Image Credit: Hamilton Company
References and further reading
- Pan, X.; Streefland, M.; Dalm, C.; Wijffels, R. H.; Martens, D. E. Selection of Chemically Defined Media for CHO Cell Fed-Batch Culture Processes. Cytotechnology 2017, 69 (1), 39–56. https://link.springer.com/article/10.1007/s10616-016-0036-5
- Zhang, A.; Tsang, V. L.; Moore, B.; Shen, V.; Huang, Y.-M.; Kshirsagar, R.; Ryll, T. Advanced Process Monitoring and Feedback Control to Enhance Cell Culture Process Production and Robustness: Advanced Process Monitoring and Feedback Control. Biotechnol. Bioeng. 2015, 112 (12), 2495–2504. https://onlinelibrary.wiley.com/doi/abs/10.1002/bit.25684
- Moore, B.; Sanford, R.; Zhang, A. Case Study: The Characterization and Implementation of Dielectric Spectroscopy (Biocapacitance) for Process Control in a Commercial GMP CHO Manufacturing Process. Biotechnol Progress 2019, 35 (3), e2782. https://aiche.onlinelibrary.wiley.com/doi/abs/10.1002/btpr.2782
- Lu, F.; Toh, P. C.; Burnett, I.; Li, F.; Hudson, T.; Amanullah, A.; Li, J. Automated Dynamic Fed-Batch Process and Media Optimization for High Productivity Cell Culture Process Development. Biotechnol. Bioeng. 2013, 110 (1), 191–205. https://onlinelibrary.wiley.com/doi/abs/10.1002/bit.24602
About Hamilton Company
Hamilton Company specializes in the development, manufacturing and customization of precision measurement devices, automated liquid handling workstations, and sample management systems. Hamilton's processes are optimized for quality and flexibility. Whether it's a custom needle with a quick delivery time frame, a special length pH sensor, or a comprehensive solution to fully automate your assay workflow, trust that Hamilton products will always meet your needs.
Hamilton Company has been a leading global manufacturer for more than 60 years, with headquarters in Reno, Nevada; Franklin, Massachusetts; Timișoara, Romania; Bonaduz, Switzerland; and subsidiary offices throughout the world.
Sponsored Content Policy: News-Medical.net publishes articles and related content that may be derived from sources where we have existing commercial relationships, provided such content adds value to the core editorial ethos of News-Medical.Net which is to educate and inform site visitors interested in medical research, science, medical devices and treatments.