Fast, precise, adaptable, and sustainable - L.B. Bohle’s current edition of the BFC tablet coater is not only a technologically advanced tablet coater but also an exceptionally designed film coater.
Premium technology meets cutting-edge design
The new BFC Tablet Coater
L.B. Bohle’s tablet coaters have been a market leader in technology and a successful business for more than 20 years. The next wave of tablet coaters brings together design and technology in a way never seen before. The tablet coater, which has been completely revamped and has several technological advancements, raises the bar for tablet coating.
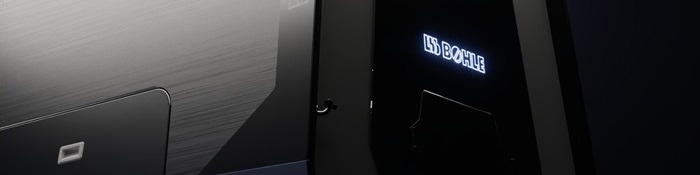
Image Credit: L.B. Bohle Maschinen und Verfahren GmbH
Highest flexibility and best tablet coating results
The BFC series of tablet coaters is redefining the global standard for quick, flexible, trouble-free, and effective tablet coating. L.B. Bohle tablet coaters achieve up to 40 % shorter process times than conventional short-drum tablet coaters (L/D ratio <1). This is because of the longer coating drum and greater spray rates.
Batches with a filling volume of 10–100 % of the drum size can be used with BFC tablet coaters, giving the operator the greatest amount of versatility. The best results are obtained by BFC tablet coaters with a tablet coating uniformity of RSD < 3 % and for colored coatings deltaE <0.5.
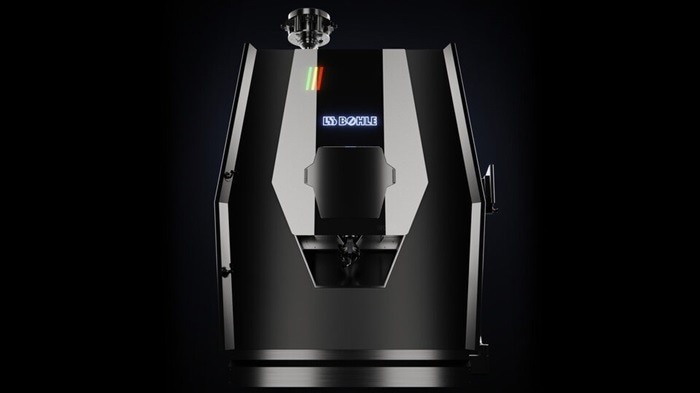
Image Credit: L.B. Bohle Maschinen und Verfahren GmbH
Why tablet coating?
Tablets are coated for several reasons. Tablets are frequently coated to alter the release of the active ingredient, protect it from light or moisture, or disguise a bitter taste in the tablet formulation. Tablets are often coated to enhance swallowability.
Coating with active substances is becoming increasingly significant. This applies to combination products as well as the use of two incompatible active ingredients in a single dosage form.
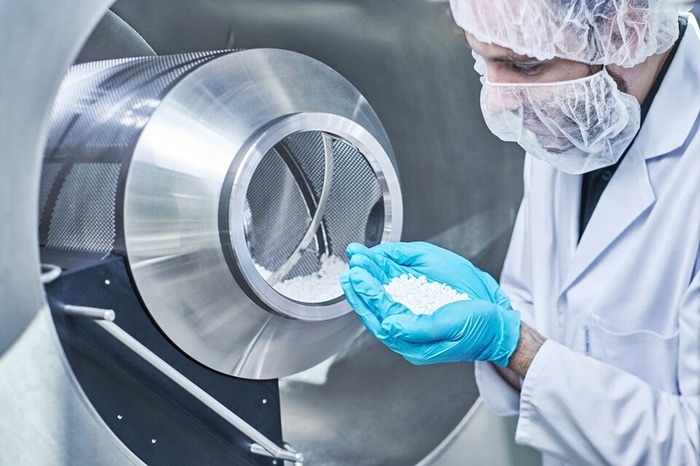
Image Credit: L.B. Bohle Maschinen und Verfahren GmbH
The process of tablet coating
Spraying
The L.B. Bohle BFC tablet coater's improved drum geometry produces a sizable spray area in the moving tablet bed. Compared to shorter drums, this enables the use of more spray nozzles, increasing the overall spray area and spray throughput. In addition to the coating suspension, the type of nozzle, number of nozzles, and nozzle spacing are also critical.
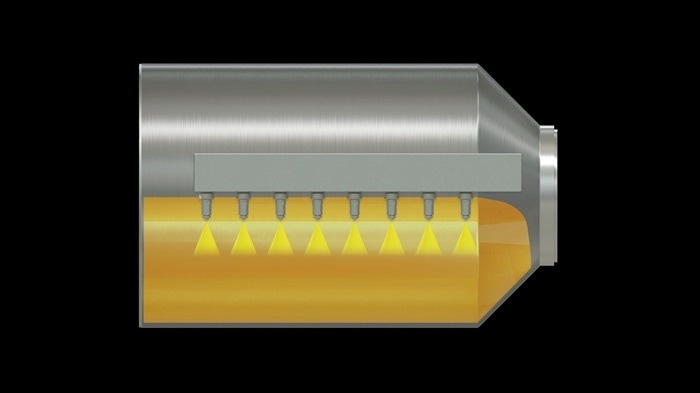
Image Credit: L.B. Bohle Maschinen und Verfahren GmbH
Mixing
The tablet cores must be moved uniformly and, most importantly, gently beneath the spray guns to prevent damage. The tablet cores cannot be put under an excessive amount of mechanical stress.
L.B. Bohle effectively utilizes an extended coating drum, with a length to diameter ratio (L/D) greater than 1, equipped with mixing spirals. These spirals ensure that the tablet bed is mixed continuously and gently. As a result, homogeneous mixing is achieved within just a few minutes and is consistently maintained throughout the process.
The design of a flat tablet bed reduces melt pressure within the tablet matrix. Owing to the consistent guidance provided by the mixing spirals, tablets experience minimal acceleration. This careful handling ensures that tablet breakage and twinning are prevented.
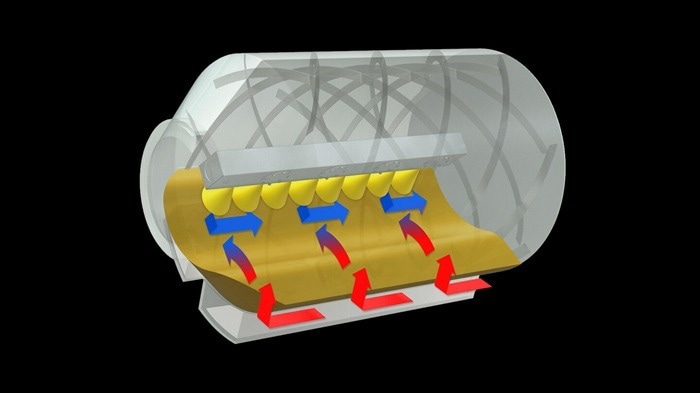
Image Credit: L.B. Bohle Maschinen und Verfahren GmbH
Drying
The key is ensuring optimal energy and mass transfer. This means that the energy must be introduced directly into the tablet bed. Air is directed smoothly and quietly into the tablet bed, facilitating the quick drying of the sprayed suspension. The outside of the coater or the housing is not heated.
Optimal air guidance ensures a smooth spray pattern, minimizing the effect of spray drying. Spray nozzles are not hit by the supply air stream and remain cool during the spraying process. This reduces spray drying effects significantly, leading to a coating uniformity of greater than 97 %.
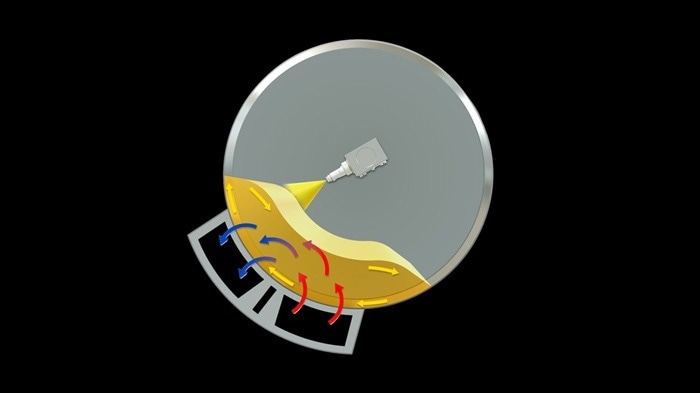
Image Credit: L.B. Bohle Maschinen und Verfahren GmbH
Coating of tablets in the pharmaceutical and nutraceutical industry
Tablets are the most important form of oral dosage in the entire pharmaceutical industry and often come coated. This coating process entails the application of a slender layer comprising one or several polymers, alongside functional excipients such as colorants or humectants, onto the tablet, which can perform a variety of functions.
The pharmaceutical and nutraceutical industries require efficient and flexible coating applications to meet stringent regulations concerning drug safety and compliance.
Reasons for tablet coating:
- Color masking
- Taste masking
- Improved swallowability
- As protection against light, oxygen or moisture
- Delayed release of the active ingredient; gastric juice resistance
- Odor masking
L.B. Bohle has the right equipment to ensure the best results, whether it is batches of tablets with low volumes or a best-selling pharmaceutical product with high volumes.