Can you explain what a CRL transfer system is and how it is used?
Jeet Patil:
At CRL, we leverage our nearly eight decades of proven innovative industry experience to design and manufacture high-quality, customized transfer solutions, such as Rapid Transfer Ports (RTPs), for use in hazardous and sterile material-handling applications. As such, CRL offers a wide range of Alpha and Beta solutions that can be implemented depending on the nature of the product-transfer system that the end user is deploying.
Specifically, an RTP consists of an Alpha flange or female port, which is always mounted on the wall of a cleanroom or isolation chamber, and a Beta flange or male port, that is docked onto the Alpha flange via a bayonet (connection) action. Only when the Beta flange is docked correctly to the Alpha flange can the door be opened. In this application, the RTP uses a double-door design principle in order to prevent contamination from occurring, i.e., the port into the container may not be opened until the Alpha and Beta ports are connected properly while the port to the container cannot be opened until the Alpha and Beta ports are docked together, ergo the double-door principal.

CRL Rapid Transfer Ports (RTPs) are used to safely transfer potent or hazardous materials. Image Credit: Central Research Laboratories
There are two types of connection between the Alpha and Beta flanges: 1) a non-rotating Alpha is immovably attached to the wall of the isolator and the Beta flange is rotated onto the Alpha flange in order to create the connection; this style is used in 99% of cases and 2) a rotating Alpha is connected to a fixed Beta flange; this type of setup is usually used when the Beta is very heavy or it is filled with fluids and can’t rotate, though this style is very rare, mainly due to system cost and the technical complexity needed to help ensure a contamination-free connection.
There are also two types of door openings that can be used. In an internal door-opening system, which is currently the most prevalent, the door is manually opened by a technician who is physically located inside the isolator. However, Good Manufacturing Practices (GMP) in the handling of sterile or aseptic products or components are beginning to dictate how a person’s hands play a role in the transfer process, so there has been a move toward the creation and use of external door openings. In this design, the door is opened from outside the isolator so there is no human interaction with the sterile/aseptic product or component being handled.

The Alpha port is mounted onto an isolator or restricted access barrier system (RABS) wall and a Beta assembly must be securely mounted before the port door can be opened. Image Credit: Central Research Laboratories
What is a Beta assembly? What different types are offered by CRL and their advantages and disadvantages?
Jim Peterson:
As mentioned, RTPs are used to securely transfer materials from one isolation chamber to another without breach of containment, which helps protect both the product and the transfer environment by preventing contamination.
Because of their design capabilities, RTPs – which are available in five standard opening sizes: 105, 190, 270, 350 and 460 mm in diameter – are regularly used for material input or output, or for the removal of solid waste from isolation chambers during a manufacturing application. The RTP components are also manufactured from materials that are resistant to multiple types of sterilization procedures from food-grade autoclaving to ethylene oxide gamma sterilization and H2O2 sterilization.
Within RTP operation, the Beta assembly, which is generally a removable stainless-steel or plastic container or plastic bag that contains the material that needs to be transferred into isolation, plays a vital role in supporting the safe, sterile transfer of these products. But not all Beta assemblies are created equal, and CRL offers a complete portfolio that can be turned to depending on the nature of the material-transfer work that must be performed:
- Standard Beta Canisters: Mainly used to transfer non-sterile products or high-potency products that require a gas-tight design.
- Autoclavable Beta Containers: Typically used for the handling of sterile products that require moist steam to pass through the container in order to create a sterilized atmosphere
- Single-Use Beta Bags: Mainly used to transfer sterile products/parts/samples into or out of an aseptic operating environment, such as Petri dishes, waste material, stoppers/seals, etc. Single-Use Beta Bags are often used in place of multi-use steel or plastic Beta containers that must be cleaned and requalified before each subsequent use.
- Sterile Liquid Transfer Ports (SLTP): Used to transfer liquids.
- Alpha Sterilization Cover: Utilized during the decontamination of the isolator when it is necessary to have the Alpha doors open. The sterilization cover works as a “dummy” Beta container during the decontamination process.
- Beta Bag Flange Assembly: Used to attach tubing or Tyvek® liner bags for removal and intake operations; this operation is similar to a Single-Use Beta Bag.
- Beta Flange with Tri-Clamp Fitting: For the connection of large tanks and process equipment to isolation.
- Inside Funnel Assembly: Protects the “Ring of Concern” – the spot where the Beta assembly connects with the Alpha port, which is a prime spot for contamination or leaks to occur unless using the proper connection technology – during the transfer of materials or tools.
- Inside Bagging Ring Assembly: Works as a chute for dispensing when used in conjunction with a liner bag.
- Beta Couplers: Used to dock two isolators to one another, one stationary and one mobile.

Single-use systems, like the CRL Single-use Beta Bags, are a popular way to safely bring critical components into pharmaceutical fill lines. Image Credit: Central Research Laboratories
How do you help clients choose between single-use and multiple-use systems?
Jeet Patil:
Every material-handling system is unique and has its own specific product-transfer characterizations and requirements. In recent years, though, the advances that have been made in single-use systems have helped spark their growing popularity. The foundation of these next-generation single-use systems is Beta Bags, which, when they are done being utilized, can simply be disconnected from the isolation chamber, glovebox or cleanroom wall and disposed of. This eliminates the need for cleaning and requalification/revalidation operations at the conclusion of production runs while enabling the production process to meet all relevant regulatory-compliance parameters for purity and sterility in the production process.

At times, flexibility is needed for heavy cargo, or for Beta containers that cannot be safely rotated. Cases such as these require custom solutions to ensure safe and reliable material transfer. Image Credit: Central Research Laboratories
Also, when used in conjunction with an Alpha port, fully sterilized single-use beta bags will help facilitate the transfer of sterile components into isolation, as well as the removal of any toxic components or waste that may be produced.
While there is still a place for multi-use systems in life-science applications – and some operators may prefer them – the advances in single-use technologies are further highlighting the inherent shortcomings of multi-use systems: initial cost for equipment and installation and, as mentioned, the time cost involved in the cleaning/revalidation and overall upkeep of steel or plastic Beta containers.
How are changing regulations impacting the use/development of transfer systems?
Jeet Patil and Jim Peterson:
The goal of any regulatory agency in any industry is to provide guidance and direction that results in manufacturing practices that enhance product quality, improve safety and avoid human errors while realizing that manufacturing operations vary from industry to industry, company to company and person to person.
Navigating a complex regulatory landscape takes expertise, time and resources, and non-compliance can result in penalties, fines, negative publicity, and, in the worst-case scenario, the halting of manufacturing operations. This makes intimate knowledge of and adherence to all relevant regulatory regimes a front-of-mind concern for all operators in the life-science realm.
In the United States, the U.S. Food & Drug Administration (FDA) regulates the production of life-science products. In this role, the FDA develops and disseminates Current Good Manufacturing Practices (CGMP). The FDA can issue non-conformity notices to companies that fall out of compliance, potentially resulting in the disallowance of finished pharmaceuticals being sold to the public.
The FDA actively develops and enforces new regulations related to CGMPs, which is yet another reason that manufacturers of equipment and systems – such as RTPs or Beta Bags – used to manufacture life-science products must prioritize staying abreast of current regulations and regulatory developments.
Globally, the FDA is seen as a leader both in developing and enforcing regulations relevant to the life-science arena. As a result, many countries around the world have adopted FDA rules as their own. Uniform standards and requirements can help ease the burden on manufacturers of life-science transfer systems to produce products that are regulatorily compliant around the globe.
Equipment manufacturers and operators within the life sciences must also be aware that regulations are subject to a constant series of reviews and revisions. For example, in 2022, the European Union completed a revision of its CGMP Annex 1, which governs the “Manufacture of Sterile Medicinal Products.” This revision includes new requirements, as well as additional detail related to many of the requirements included in the prior version of Annex 1, which was released in 2008. This just underscores that it is imperative that the manufacturers and users of transfer systems be up to date on the latest regulatory rules and requirements relevant to the products they sell.
To this end, CRL has always designed its technologies with the latest regulatory developments top-of-mind. Our products promote and optimize operator safety and efficiency, along with product consistency. CRL also works directly with its customers to identify the best solutions, from standard product offerings to customized development, which can help ensure the creation of the best solution possible for safe and confident handling – of every application need.
What is CRL’s background, and how does this transfer to the creation of CRL transfer systems?
Jim Peterson:
It was in the fall of 1945, as World War II was concluding, that three recent graduates of the Massachusetts Institute of Technology – Frank G. Chesley, Demetrius Jelatis and Gordon M. Lee – put their resources together to create a company they named Central Research Laboratories®, Inc., (CRL). Backed by their undergraduate experience as researchers for the U.S. War Department, their company began life as one that designed radar-testing equipment for use by the various branches of the U.S. armed forces.

Since its founding in 1945, CRL has been a trusted industry partner and an important part of the Red Wing, Minnesota, USA, community. Image Credit: Central Research Laboratories
From that beginning, CRL branched out into other areas of concentration and found success by developing safer methods of handling radioactive materials, which they supplied to the U.S. Atomic Energy Commission. Their success in this realm prompted CRL to begin concentrating on designing, engineering and manufacturing remote-handling technologies.
As CRL continued to evolve and expand its product expertise, it began developing systems for use in the life-science market, with the company’s first Rapid Transfer Port (RTP) technology developed in 1997. That was a watershed moment as the company has turned its attention to optimizing performance in life-science product-handling, with the latest innovation in its portfolio of Single-Use Beta Bags.
CRL has also been aided by its status as a product brand within DESTACO, a developer of automation, workholding and containment solutions for industrial markets, and Dover Corporation, a diversified global manufacturer and solutions provider for five industrial operating segments. This has given us the opportunity to leverage relationships with other life science-focused members of Dover’s Pumps & Process Solutions operating segment, including CPC®, which develops connectors, quick-disconnect coupling and fittings for life-science applications, and the newly formed PSG Biotech®, which offers pumps and flow-monitoring/measurement/control systems for life-science product production.
Still, at its core, CRL remains committed to offering solutions that protect the operator environment when handling sterile/aseptic or hazardous materials.
How have CRL transfer systems changed over the last decade?
Jim Peterson:
CRL’s transfer systems have expanded in a number of exciting new directions over the past decades. We have moved well beyond static multi-use systems to those that offer more variety and flexibility for the user.
The most obvious of these evolutionary innovations are the aforementioned Single-Use Beta Bags that eliminate the costly and time-consuming acquisition, cleaning/revalidating, outfitting and upkeep needs of multi-use stainless-steel systems.
We now also offer a more robust portfolio of RTP technologies, with the latest innovation being our ERTP model. The ERTP uses the same double-door transfer system as a typical RTP but includes a revolutionary new handle that utilizes minimal rotation to break the seal on a Beta container, which reduces operator effort for safer handling. The ERTP also features a streamlined interlock system with interchangeable mounts that can be replaced without breaking containment. The new-and-improved design also eliminates exposed fasteners and incorporates a smoother surface for easier cleaning.

The ERTP family of Alpha ports is the latest innovation in improving performance while lowering costs and lead times. Image Credit: Central Research Laboratories
How do you see CRL transfer systems evolving in the future?
Jim Peterson:
We plan to continue to expand our product line, invest in single-use systems, find ways to make operating RTPs easier and easier – without sacrificing product-containment and safety qualities – and evolve with changing regulatory requirements. This means that as our customers’ needs evolve, we will evolve with them.
To realize this, we will continue to optimize the flexibility that allows us to move with the market. We can accomplish this by trying every day to offer a better solution for what our customers want and need. We are and will remain, customer-intimate, constantly communicating with them to see what they need and then working on bringing what they need to market.
About Jim Peterson 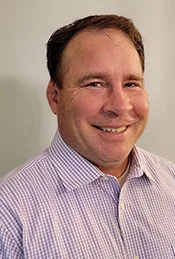
Jim Peterson is a Sales Manager at Central Research Laboratories (CRL), responsible for the company’s sales efforts in the Rapid Transfer Port (RTP) and Single-Use Beta Bag product categories for use in the life science market. He holds a Bachelor of Management Information Systems Degree from Augsburg University.
Jim has more than 20 years of managerial experience, primarily in sales manager roles with Donaldson. He joined CRL in 2019.
About Jeet Patil
Jeet Patil is a Sales Manager, Life Science at Central Research Laboratories (CRL).
He has more than 20 years of experience in business development for the capital goods industry, specializing in the pharmaceutical, food manufacturing and packaging industries.
He holds a bachelor of science in mechanical engineering from Maharashtra State Board of Technical Education with postgraduate certification in tool engineering.
Jeet’s sales manager experience began in 1994 as a product manager for ACG World. Since then, he has held sales roles with Fabtech Technologies International and Protech Group China before joining CRL in 2016.
About Central Research Laboratories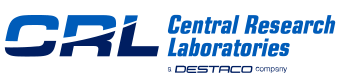
For 75 years, CRL has been a trusted supplier of remote handling solutions. Our innovative technologies provide safe and reliable protection for operators working with hazardous and sterile materials in Nuclear and Life Science applications around the world. We offer high quality products and exceptional technical expertise and support.