Introduction
Motion and positioning devices play an integral role in the life-science and medical engineering fields, fulfilling their many different requirements. The spectrum extends from simple low-energy drive components to ultrasonic transducers through to ultra-fast actuators and high-precision positioning systems for pumping and valve applications. These requirements are addressed by motor drives and piezoceramic transducers, which are known to have a long track record of ruggedness and reliability in optical technologies and semiconductor manufacturing industries.
PICMA® piezo actuators were even used for the Mars Mission after they passed 100 billion rounds of life testing with nil failures. Some applications for actuators, piezo transducers, and motors are given below:
- Zoom actuators for micropumps, endoscopes, pipettors, nanodispensers, flow meters and bubble detectors, nebulizers, and cutting tools in endoscopic piezosurgery
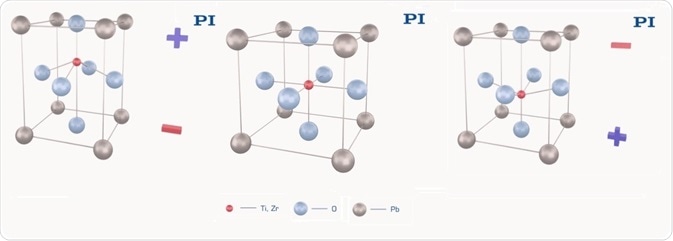
The solid-state effects inside piezoceramic materials when the electric field is changed (Image: PI)
High performance piezo-driven diaphragm micropumps
Miniaturized drive mechanisms are required in micro-diaphragm pumps to provide both variable and continuous flow rates. The small amounts for each pumping cycle ensures high drive frequencies in the 10’s of kilo Hertz range so as to obtain high flow rates.
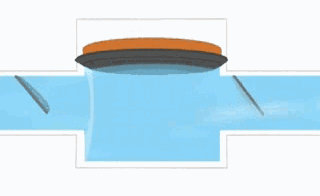
The diaphragm can be integrated with disk-shaped piezo transducers. A piezo linear actuator can be directly connected to a piston or a diaphragm for larger extensions or forces. Piezo drives can also be used to generate slow and continuous motion of infusion pumps as seen in the animation above.
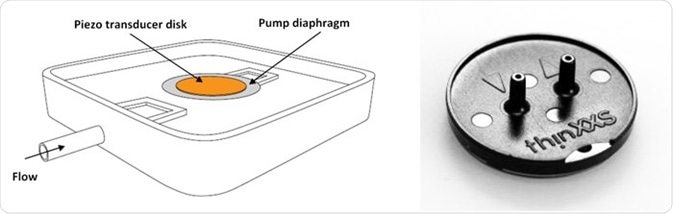
(left) Piezoceramic disks can be attached to the membrane of a micropump and thus move it with high frequency.(Image:PI) (right) Piezo-transducer driven micro-diaphragm pump for laboratory automation (Image: thinXXS Microtechnology AG)
Micro-dosing valves with piezo flexure drives
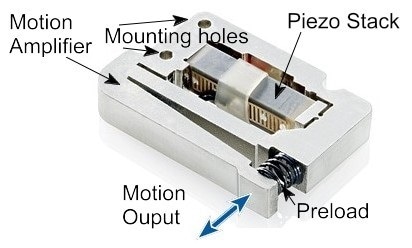
P-604 low-cost piezo flexure OEM actuator (Image: PI)
Micro-dosing valves meant for nanoliter or picoliter droplets are dependent on extremely fast actuation. Devices like piezo-actuators are employed in a number of drives – either they can directly operate the valves or operate against a flexible tubing or strong springs to displace liquid volumes. Usually, the rapid opening and closing of a valve is proportional to the amount of volume to be controlled.
It is preferred to have frequencies in the kilohertz range, and piezo actuators are capable of providing faster response when compared to electromagnetic drives, such as voice coils or solenoids. Piezo mechanisms generate high kinetic energy, which can produce extremely small droplets without the associated nebulization, dripping, or satellite formation.
Drop-on-demand method is similar to ink jet technology. In this method, piezo tube that contracts radially upon voltage application is available. Piezo flexure actuators with built-in motion amplifier can implement valves that need larger strokes.
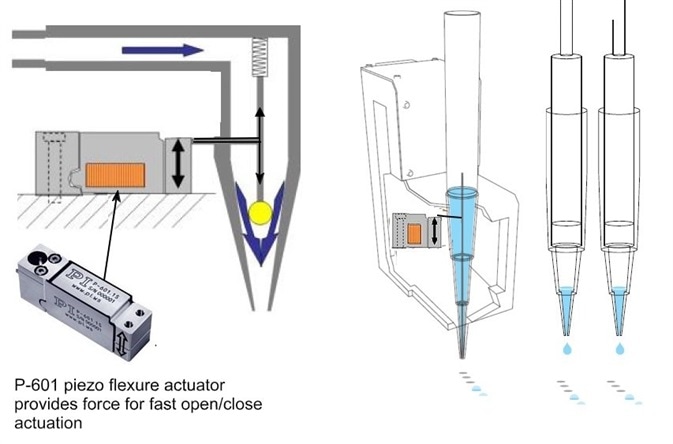
Principle design of a high-speed precision dosing valve for micro-liter to picoliter applications. Piezo mechanics are stiffer and can move faster than solenoids. Piezo flexure amplified actuators provide motion ranges of several 100µm and extremely fast mechanical response to drive signal changes in the order of milliseconds and below. The high speed combined with the virtually unlimited position resolution in the nanometer range provides advantages in open/close speed of valves and also in the dosing precision. (Image: PI)
The direct displacement method employed in PipeJet™ dispensers is another principle, built on an elastic polymer fluid line that features a thin internal diameter powered by high-force PICMA® piezo stack actuators. The piezo drive and the tube are separated, and therefore maintenance is made simple and easy and any component that is contaminated by fluid can be quickly and economically replaced.
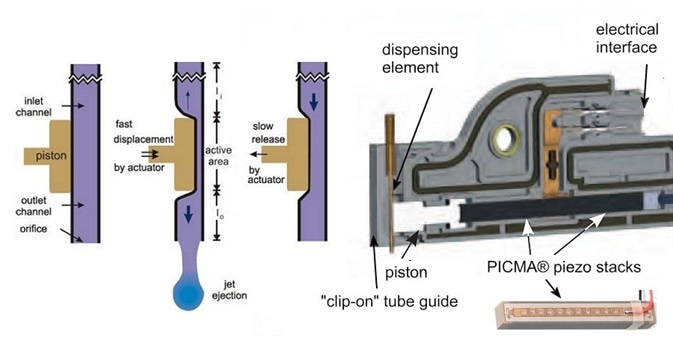
PipeJet micro-dosing pump. This system does not require a valve and is based on a PICMA® piezo-linear-direct drive actuator, displacing the liquid in a flexible tube. (Image: Biofluidix)
Pumps for outpatient therapy
Generally, outpatient therapy depends on mobile drug pumps for many different applications, such as pain therapy, parenteral nutrition, metabolic disorders, and oncology. Mobility enhances the quality of life and also reduces the costs related to therapies, since the patients no longer have to be treated at the hospital. When it comes to weight, size, flexibility, and reliability, traditional mobile drug pumps have certain limitations. These limitations can be overcome by using the latest developments in drive systems that are based on piezo ceramic motors, thus opening up new avenues for both patients and medical device manufacturers.
Balloon pumps are often associated with the concept of mobile and compact drug delivery, but these devices are not consistent in the medication delivery rate and are not capable of documenting the actual amount of injection administered. Since mobile patients do not stay in the hospital, no trained staff are available to accurately track their duration of therapy.
Where doctors are concerned, accurate information is required to ensure a successful treatment. Hence, a pump system can be used to accurately trace the amount of medication against the time spent outside the hospital. In such situations, peristaltic pumps provide the ultimate solution.
However, peristaltic pumps are known to have significant size and weight, which largely limit the mobility of patients, but then these devices enable an exact dosage and facilitate timely, programmable volume flows. Also, peristaltic pumps can be used for numerous medications, as they provide a constant flow (basal rate); even exclusive injections (bolus rates) can be easily dosed and scheduled in any way. Further, all procedures can be easily documented to assess the specified amounts of drugs and the duration of therapy, and to finally submit the related data to insurance providers.
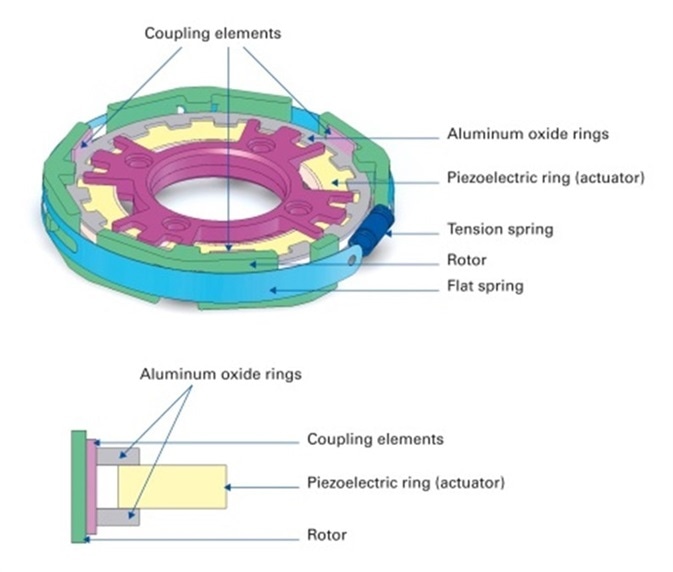
A compact piezoelectric ultrasonic rotary motor for variable drug delivery. The motor consists of a piezoelectric ring actuator excited with a travelling wave. Thin aluminum oxide rings (grey) on top and bottom of the piezo ring absorb the oscillations. With the help of the three coupling elements (pink) used in the rotor, the absorbed oscillations are transmitted to the pre-loaded rotor (green) and converted to a rotary motion. (Image: PI)
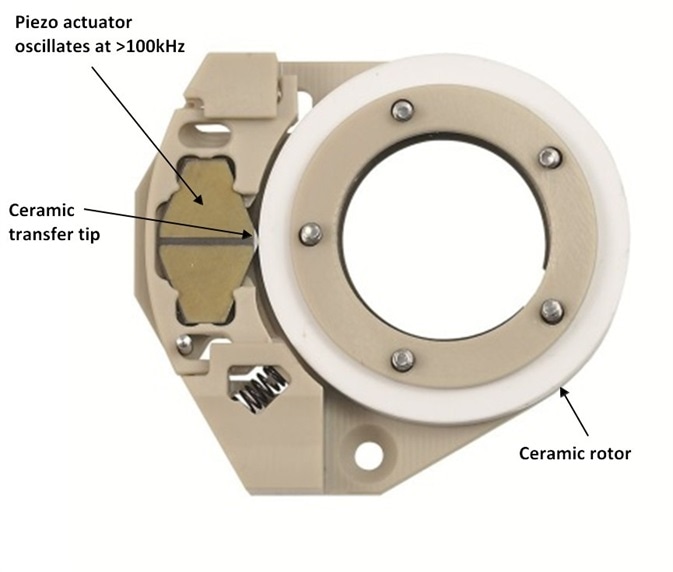
Designs with the piezo actuator mounted radially are also feasible. Inside the large aperture of this ring additional components can be arranged. Drug pumps built in such a manner are particularly small, light and silent. They offer a high degree of flexibility with regard to various therapies and dosages. (Image: PI)
Mobility and documentation
Peristaltic pumps integrate all the preferred requirements, except for mobility. Despite this fact, the motors used in the peristaltic pumps have to be further improved. The necessary torque needed for pumping can be generated by small electric motors with gear-box torque multipliers, but these motors are relatively slow plus their mechanical micro-gears have a tendency to wear and backlash, needing maintenance as well as lacking cost efficiency and reliability.
When using a gearless electric motor, torque can only be generated with a larger drive and the self-locking function of the gear box is also lost. Electric current also have to be used to maintain a steady position when at rest, which can affect the life of the batteries.
Operating principles of different types of piezo motor drives
Stick / Slip Piezo Linear Motor Animation - Mini Motor Actuator by www.pi.ws
Ultrasonic Motor Operating Principle PILine Linear / Rotary Piezo Motor by www.pi.ws
Here, ultrasonic direct drives based on piezo actuators can pave the way for new opportunities. These devices are compact, quiet, self-locking and low-wear, and continue to maintain their position even when they are powered off, hit, shaken, or dropped.
The working mechanism of these compact piezo drives can be easily understood: oscillations in the ultrasonic frequency range of a piezoceramic plate are shifted to a moving runner in a rotary or linear motion. A monolithic piezo ceramic (stator) equipped with two electrodes forms the core piece of the drive. The right or left electrode is electrically excited, in the 100kHz range or above, to establish the direction of motion. Then, each oscillation shifts a coupling element that is connected to the piezo ceramic by several nanometers. In contact with the moving runner, the overall outcomes of the micro impulses are high speed motion combined with extremely high precision.
Various designs are feasible
The drive electronics needs very little installation space as it can be easily incorporated as a chip. The solution is also highly reliable and low-wear, because only few mechanical components are present, such as gears. A large spread of dosages is enabled by a broad speed spectrum. Based on the design, it is possible to make dosages from a few degrees up to a number of revolutions per second, or from <1mm/second up to several 100mm/seconds in the case of linear drives.
Miniature drives / pipetting with uniform force
As the amount of liquid reduces and the number of micro wells increase, there is a need for miniaturization of the drives, together with better precision for dosing smaller quantities.
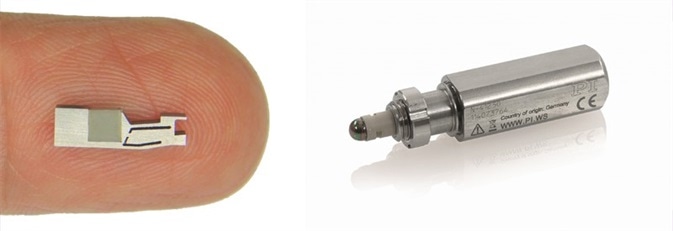
Piezo linear motors can be designed incredibly small. The inertia motor shown on the left provides provide nanometer precision and is ideal for integration into miniaturized drives and instrumentation. A miniature actuator with piezo motor is shown on the right. (Image: PI)
In order to meet these needs, compact piezo linear motors can be developed which can provide even force and speed together with positioning accuracy from micrometer to nanometer range. The major reduction of moving components as opposed to traditional motor/screw drives not only increases the reliability but also reduces the size.
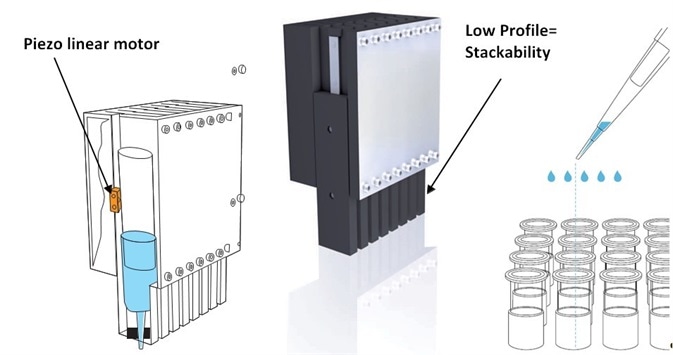
A compact piezo motor drives the pipetting mechanism. The low profile allows for stacking of multiple units. Miniaturization higher dosing precision is advantageous as liquid volumes fall and micro well counts go up. (Image: PI)
Atomizers / aerosols generation
Atomizers are medical devices that can efficiently deliver medication to the respiratory tract. Here, the aerosol’s homogeneity is crucial and piezo-transducer driven membranes oscillating at high ultrasonic frequencies can create droplets whose sizes are predefined.
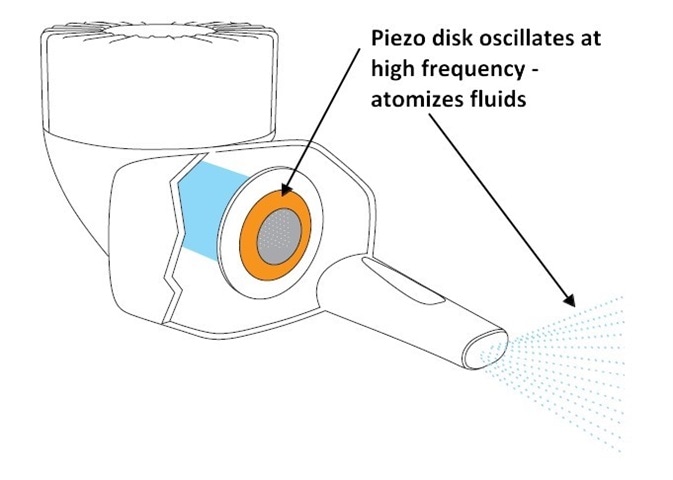
An annular piezo disk excites a perforated membrane with oscillations up to 100 kilohertz. Medication is thus quickly and efficiently atomized. (Image: PI)
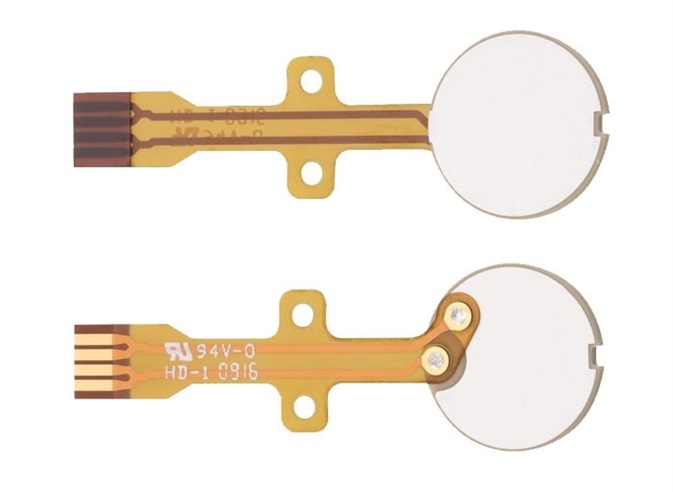
Piezo transducer discs are available with flexible PCB to facilitate integration in volume production. (Image: PI)
Bubble detection and flow measurement
Impurities or bubbles in blood transfusion or dialysis applications can be detected using ultrasonic piezo transducers. Transducers operate as both actuators (transmitters and ultrasound detectors) and sensors, due to the inverse and direct piezo effect. No direct contact is made with the fluids and as a result, maintenance is not required. The piezo transducers can detect bubbles and also determine the flow velocity.
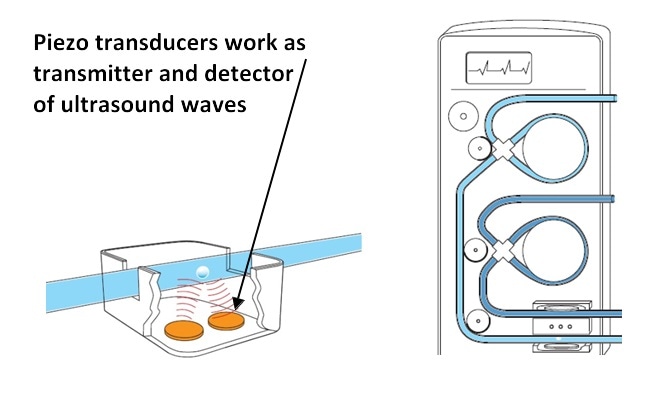
Air In-Line Sensor: The piezo transducer element works both as an ultra-sound generator and detector. The measurement is based on the Doppler Effect: oscillations in the 100kHz range are reflected by the medium. Signal processing electronics can tell frequency offsets and changes in the reflection pattern and reliably measure flow rate and detect air bubbles. (Image: PI)
Piezo drives for endoscopy and ophthalmology
Piezo drives are used in many more different fields, for instance, as precision shutters for radiation therapy, focusing drives in endoscopy, and laser beam control in ophthalmology and cosmetic applications.
Fast Piezo Mirror Mounts for Laser Beam Steering: Laser Eye Surgery with FSM - Piezo Tip/Tilt | PI
Piezo ceramic motors do not create strong magnetic fields and are also not affected by them. During tumor treatment, radiation beam can affect healthy tissues. Here, multi-leaf collimators are used to minimize these side effects. Piezo drives are not only extremely compact but also enable tighter packaging, resulting in increased leave count and improved adjustment of the contour and thus ensuing better protection for the patient.
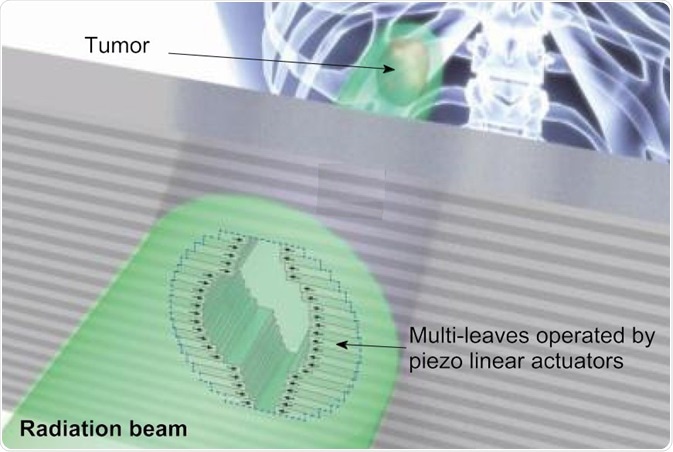
Piezo linear motors can be tightly packaged to control the leaves in a multi-leaf collimator for radiation treatment.
Conclusion
Piezo technology such as actuators, transducers, and motors deliver sophisticated solutions to various dosing, motion, positioning, and measuring problems. Piezo elements can directly change mechanical energy into electrical energy and vice versa. Additionally, the piezo effect is built on crystalline displacements, without physical wear and friction. Piezo ceramics can be baked at high temperatures; they are also sterile and do not need lubrication. Piezo products are intrinsically non-magnetic and vacuum compatible, which are essential for bio-medical applications.

Variety of piezo ceramic transducer disks, rings benders, and tubes. (Image: PI)
The Piezoelectric Effect, Manufacturing Processes: How do Piezoelectric Transducers work?
About PI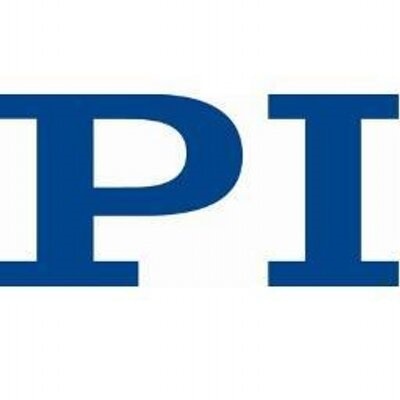
PI is a leading manufacturer of precision motion control systems such as Piezo Nanopositioning Systems, Air Bearings, Linear Motor Stages, Microscope Stages, Motion Controllers, Piezo Flexure Mechanisms, Piezo Ceramic Motors and Hexapod 6-Axis Stages -- for photonics, bio-nanotechnology, medical device & semiconductor applications.
PI recently acquired the majority of ACS, a global leader in high-end motion controllers for precision industrial automation. PI USA is also specialized in Air Bearing positioning systems boasting over 200 man-years of in-house air bearing design experience.
Linear, planar XY, and rotary air bearing stages and custom turnkey systems are available to serve industrial and research markets. Piezo actuators from our PI Ceramic division and precision stages from our PI miCos division were selected by NASA for the Mars Mission and are employed on in the Curiosity rover science lab. PI has been developing and manufacturing standard & custom precision products with piezoceramic and electromagnetic drives for 40 years.
Sponsored Content Policy: News-Medical.net publishes articles and related content that may be derived from sources where we have existing commercial relationships, provided such content adds value to the core editorial ethos of News-Medical.Net which is to educate and inform site visitors interested in medical research, science, medical devices and treatments.