The aim of minimal invasive surgery (MIS), as the name suggests, is to cause minimal discomfort to patients. Here, endoscopes play a vital role. However, conventional Chip-on-the-Tip endoscopes that employ fixed focus optics are incapable of displaying objects at various distances with optimum resolution. Variable focusing is achieved by integrating a miniature drive, so that the object is optimally shown in sharp focus all the time.
Larynx diagnostics or laparoscopy — a surgical procedure where a thin tube is fed through a cut in the belly to view the abdominal organs — uses endoscopes that enable the MIS procedure. Then, using the so-called working trocars, optics and special instruments like hooks, scissors, ultrasound scissors, grasping forceps etc., are introduced into the abdominal cavity. After MIS surgery, patients will have only minimal post-operative pain and since the healing process is relatively quick they can be discharged from the hospital sooner than before. Also, the risk of wound healing disorders or wound infections is reduced to a large extent and enables treating patients who are at high risk.
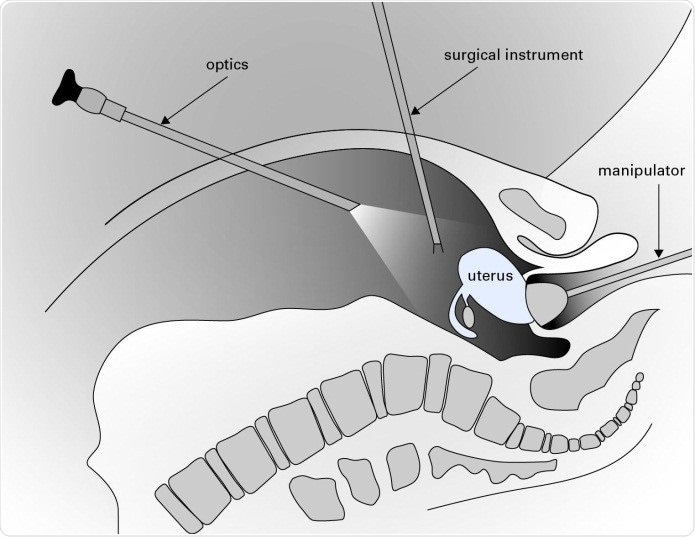
Modern medical technology is aiming at causing patients as little discomfort as possible with their therapies. Endoscopes that allow minimally invasive surgery provide an important contribution, e.g., in laparoscopy.
Placing the imaging sensor on the endoscope tip
Although conventional endoscope technology is a well-established tool and has reached a high level of sophistication, image transmission through traditional optics was a major limitation of this technology. Thanks to the rapid advancement of compact imaging sensors and microelectronics, more progress is now viable, for example, fitting a small camera into the tip of the endoscope (Chip-on-the-Tip).
However, with conventional endoscope optics, a manual focus lens or zoom lens can be attached between the camera and eye piece to set the focus to various object distances and then zoom into the details. On the contrary, the Chip-on-the-Tip technology has digital zoom function that only enlarges a detail and is always accompanied by reduced quality. The lack of a focus function calls for a trade-off between image brightness and depths of focus.
Optical zoom function for chip-on-the-tip cameras in endoscopes
This kind of trade-off can be easily eliminated if the actuators needed for zoom functions and optical focus are introduced between the imaging chip and optics. There is a very small installation space as the diameters are usually 10mm. While it does seem to be challenging, it is not impossible to come across the ideal drives for the focus and zoom lens.
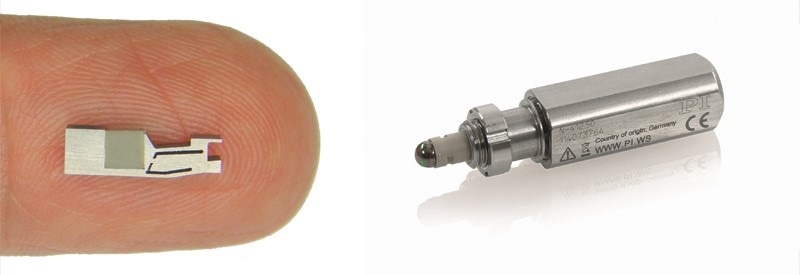
Piezo stick-slip mini motors are incredibly small as seen on the left. Designed into a drive, they can become an integral part with further size reduction possible. A standard miniature actuator with high-force piezo inertia motor is shown on the right. (Image: PI)
For instance, miniaturized voice coil drives and ceramic piezo motors could pave the way for a new application area in this field. This is the area where PI (Physik Instrumente) displays its know-how in compact precision drive mechanisms. These drives provide a solid platform for use in contemporary high-resolution microscopes.

If actuators could be installed between the optics and the imaging chip, optical focus and zoom functions can be added to a Chip-on-the-Tip Camera. With diameters of typically 10mm, the potential installation space is very small and it seems to be difficult, but not impossible, to find the right drives for the zoom and focus lens.
Small piezo motors or voice coil drives
Piezo motors are extremely precise and contact linear drives. They are lightweight, small, and consume minimal energy. As a matter of fact, they can maintain a position without power consumption. The direct-drive principle not only prevents the conversion of rotation into linear motion but also eliminates the requirement for mechanical components including gears that can easily wear out and reduce reliability.
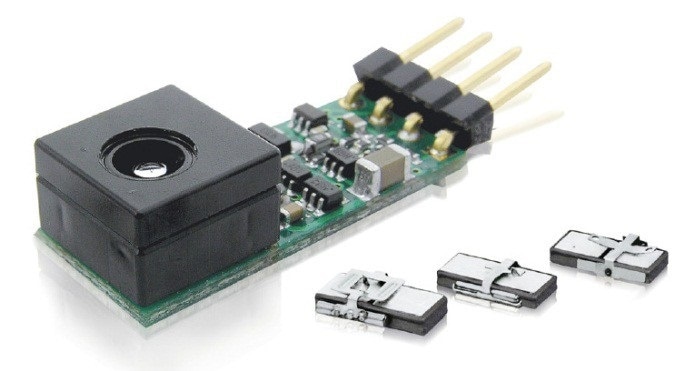
A miniature piezo motor positions an autofocus lens integrated along with the driver on a small PCB (Image: PI)
There are several feasible piezo motor principles (see videos below). All of them offer the required precision. Inertia motors and ultrasonic motors are both compact and cost effective.
Stick / Slip Piezo Linear Motor Animation - Mini Motor Actuator by www.pi.ws
Ultrasonic Motor Operating Principle PILine Linear / Rotary Piezo Motor by www.pi.ws
Miniature Linear Stage | Miniature Rotary Table, Rotation Stage w/Piezo Motor: How it works | PI
N470 Miniature Opto-Mechanical Actuator with Position Sensor based on Piezo Ratchet Drive www.pi.ws
Conventional electromagnetic linear motors (Voice Coils) can also be used in addition to piezoelectric motors.
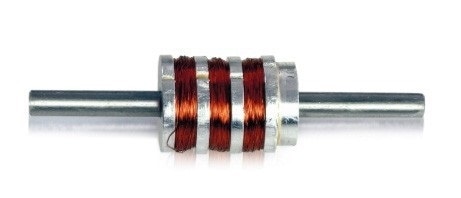
Miniaturized PIMagTM voice coil linear drive. This type of motor provides high speed and motion up to 25mm, enough for the requirements in endoscopes. (Image: PI)
How Does a Voice Coil Motor Work - Applications in Linear Actuators and Linear Stages. By www.pi.ws
Voice coil actuators and the transducers used in loudspeakers are somewhat related, the former can be developed with extremely small dimensions and deliver motion ranges from the millimeter to centimeter range, just sufficient for endoscopy. In view of these drive options, it would be interesting to find out as which of these devices will contribute to improved depth of focus and image quality in the sophisticated Chip-on-the-Tip endoscopes.

Miniaturized controller for a voice coil drive with integrated position sensor. (Image: PI)
Piezo scanner tubes for 2-photon endoscopy
High-resolution two photon endoscopy can make use of compact piezo XY scanners. In a recently published paper, it was described that for biological imaging of parts of the eye, a spiral fiber scanner based on a compact piezo scanner tube (1.5mm outer diameter) was employed. The small instrument has a 2mm diameter and provides axial and lateral resolution down to 1.5μm.
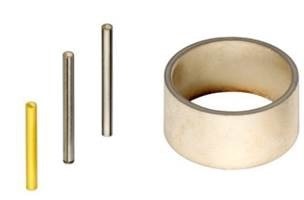
Miniature piezo scanner tubes compared to a standard piezo-ceramic ring. (Image: PI)
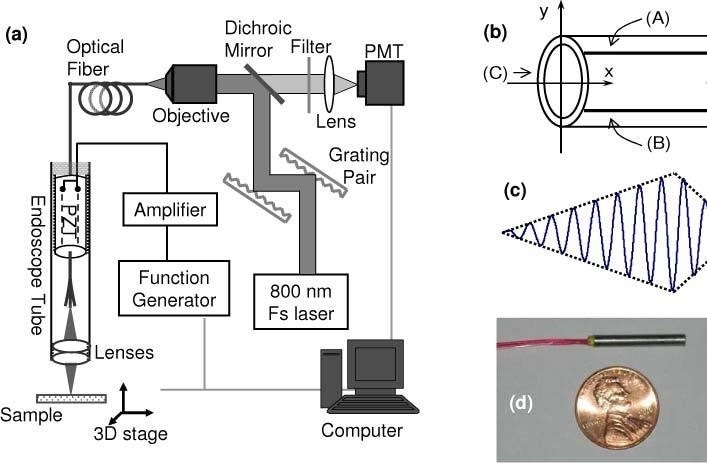
Design of the two-photon excitation fluorescence endoscope. (a) shows the piezo scanner tube; the complete 2 photon probe is shown in (d). (Source: http://www.ncbi.nlm.nih.gov/pmc/articles/PMC3018080)
Acknowledgments
Written from materials by Birgit Bauer, Business Development Manager Health Care at PI (Physik Instrumente)
About PI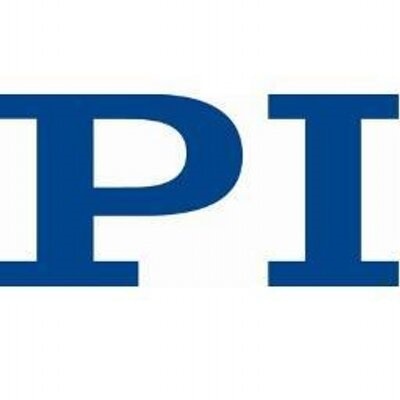
PI is a leading manufacturer of precision motion control systems such as Piezo Nanopositioning Systems, Air Bearings, Linear Motor Stages, Microscope Stages, Motion Controllers, Piezo Flexure Mechanisms, Piezo Ceramic Motors and Hexapod 6-Axis Stages -- for photonics, bio-nanotechnology, medical device & semiconductor applications.
PI recently acquired the majority of ACS, a global leader in high-end motion controllers for precision industrial automation. PI USA is also specialized in Air Bearing positioning systems boasting over 200 man-years of in-house air bearing design experience.
Linear, planar XY, and rotary air bearing stages and custom turnkey systems are available to serve industrial and research markets. Piezo actuators from our PI Ceramic division and precision stages from our PI miCos division were selected by NASA for the Mars Mission and are employed on in the Curiosity rover science lab. PI has been developing and manufacturing standard & custom precision products with piezoceramic and electromagnetic drives for 40 years.
Sponsored Content Policy: News-Medical.net publishes articles and related content that may be derived from sources where we have existing commercial relationships, provided such content adds value to the core editorial ethos of News-Medical.Net which is to educate and inform site visitors interested in medical research, science, medical devices and treatments.