The pharmaceutical industry depends on quality and reliability, especially within the manufacturing and application of pharmaceutically active substances or excipients.
There are two core objectives here: first of all, substances need to be handled safely at all times so that operating personnel are protected; and secondly, these products must be without fault, having the right levels of quality built into the product itself and its process development. This principle is often referred to as Quality by Design.
Process Analytical Technology (PAT)
A central aspect of the Quality by Design concept is the Process Analytical Technology (PAT) initiative that has been developed by the US Food and Drug Administration (USFDA). The USFDA manages and monitors these production processes, examining every aspect from the intermediate products to the final, completed product. This is accomplished via a series of in-process control measures.
To ensure that these control measures are effective, critical process parameters (CPP) must be promptly measured using the most appropriate systems for the analysis and control of production processes. These critical parameters dictate the critical quality attributes (CQA) for source as well as in-process materials and as such, it is imperative that these are appropriately managed.
In order to demonstrate this concept, it is worth looking at a practical example. A frequently used process step within the manufacturing of a finely dispersed active ingredient powder used within solid dosage forms, is air jet grinding within the kilo laboratory.
This particular process relies on having suitable on-line analysis because without this in place, the grinding process would need to be manually analyzed on a regular basis through the removal of samples, then taking them to a laboratory for analysis. This causes interruption in the process, as well as having a negative impact on efficiency and throughput.
On-Line Particle Size Analysis
Using on-line particle size analysis however, real-time monitoring of the grinding level is possible with no interruption to the grinding process itself. Additionally, this means that the active substance can be completely contained, reducing any risks to operators working on the production line.
Using appropriate probes, sampling systems or TWISTER it is possible to retrieve minimal yet representative product quantities directly from the process itself. These are then discharged on a MYTOS laser diffraction sensor.
The MYTOS system can operate in a bypass line to the primary process stream where it is supplied with product samples via a sampling system. It is also possible to implement a multiplex installation involving several sampling points being connected to a single sensor.
The VIBRI precision vibratory feeder can be utilized as an interface for the transfer of process samples. When working with a uniform, regulated product supply this will ensure that an optimal concentration of sample enters the MYTOS system’s measuring zone.
.jpg)
Laser diffraction sensor MYTOS for process-related on-line installations in a mobile rack
Vital Grinding Parameters
As well as the benefits already discussed, on-line monitoring can offer real-time, reliable results for particle size distribution.
Essential grinding parameters such as form, quantity and classifier speed can be adjusted and optimized mid-operation and, since the active ingredient stays within a closed system throughout this process, any risks of contamination during analysis are significantly reduced.
.jpg)
Online measurement with MYTOS & TWISTER for targeted air jet grinding of lactose | Achieving the desired particle size distribution (x10 < 4 microns, x50 = 8 microns, x90 > 14 microns) within 20 minutes after two adjustments
About Sympatec GmbH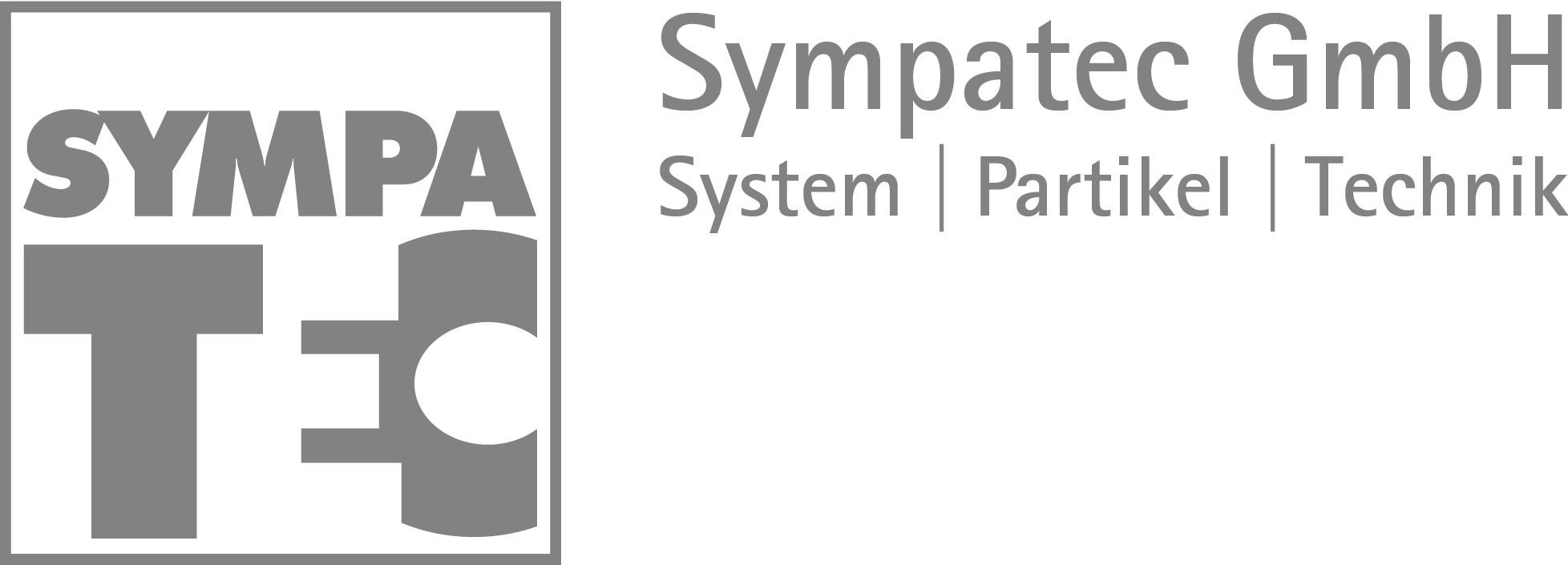
Sympatec develops, manufactures, sells, services and supports an innovative range of best instruments for particle size and particle shape analysis in laboratory and process: from small quantities as part of active ingredient development and preformulation through to manufacture of active pharmaceutical ingredients in batch operation or continuous volume processing on an industrial scale.
Sponsored Content Policy: News-Medical.net publishes articles and related content that may be derived from sources where we have existing commercial relationships, provided such content adds value to the core editorial ethos of News-Medical.Net which is to educate and inform site visitors interested in medical research, science, medical devices and treatments.