Parenteral drugs are sterile drug products that come in the form of emulsion, solution, reconstituted lyophilized powder, or suspension ideal for administration through injection. These drugs form a highly crucial segment of the pharmaceutical industry.
In general, parenteral dosage forms are favored for their direct absorption at the delivery site rather than an oral route through the stomach, which can result in irregular absorption and usually a very gradual onset of action.
Parenteral drug delivery is essentially related to biological drugs (though this route can be used for small molecule drug products, specifically where solubility poses a difficulty).1 In 2018, parenterals constituted 32% (by volume) of the worldwide drug market.2
The growth of the parenteral market has been due to the higher development of biologics and complex active pharmaceutical ingredients (APIs), which is in turn induced by the increasing incidence of chronic illnesses across the world, for example, diabetes, cardiovascular diseases and cancer.
Pharma and biotech companies are often encouraged to create biologics because these usually target unsatisfied medical requirements or orphan diseases. But when it comes to volumes and components, these novel, niche product areas necessitate higher flexibility.
Thanks to the focus on parenteral drug development, it is expected that by the end of 2024, the parenteral packaging sector will experience major growth at a compound annual growth rate (CAGR) of 11.14%.3 Meanwhile, higher pressures are being placed on regulatory elements to better manage the contamination risk of aseptic fill-finish operations.
Need for ready-to-use packaging systems
There is an ever-increasing need for ready-to-use (RTU) packaging systems induced by the growing need for personalized medicines and biological drugs, and the resultant demand for manufacturing capacity flexibility.
Since RTU packaging systems save considerable amounts of investment or operational requirements, pharma companies gain more time and resources to concentrate on drug development and core added value operations.
Besides the substantial expansion of biotech therapies, listed below are the other drivers of the industry’s movement toward RTU packaging components:
- The demand to minimize the total cost of ownership (TCO): There will be a constant increase in pharma running costs, with a standard investment of more than US$2 billion needed to advance from a laboratory concept to successful commercialization.4 Conventional filling lines need high running costs and space, and thus many companies have been looking for new solutions.
- The thrust to reduce drug costs, improve efficiency and bring down patient risk: Demands from governments and society for higher access and reduced cost will place pressure on pharma companies across the globe. Adding to this pressure are a patient-first and right-first-time mindset, as well as the demand to deliver on-time release and higher yield.
- The demand for quick and flexible reactions to industry requirements: There is a need to change primary packaging frequently (based on emerging markets and personalized medicine) and a need for a smaller batch filling.
- Higher quality and regulatory compliance: Pharma companies have been looking for ways to maintain pace with the fast-evolving global regulatory environment and materialize responsibility.
Suppliers of RTU packaging systems wash, depyrogenate, and sterilize the packaging so that the only step that remains in the in-house process is to fill and complete the container, which avoids the need for a considerable part of the operational constraints.
Currently, RTU solutions for small-volume containers are widely recognized and used by smaller labs and industries, but the option for containers of a larger volume (those above 20 mL) is still a critical demand in the market.5
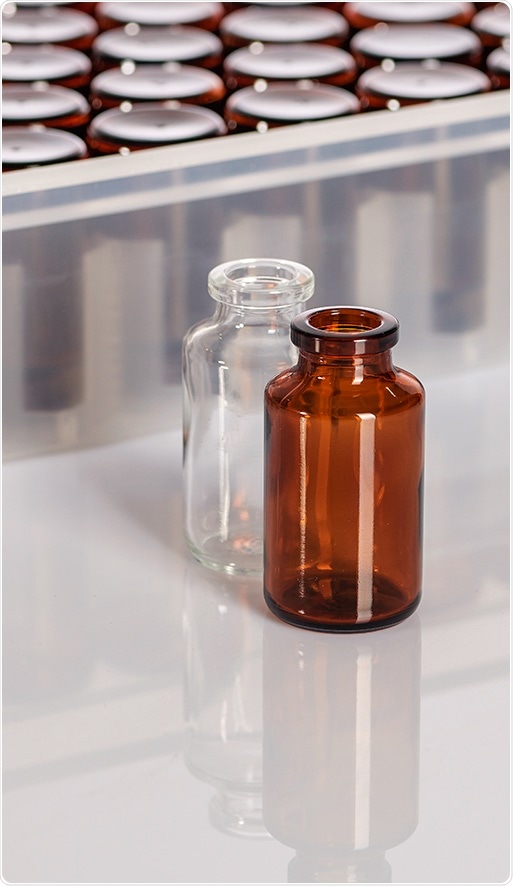
SGD Pharma amber and clear molded glass vials. Image Credit: SGD Pharma
In the past 10 years or so, the geometry and composition of glass vials have been adjusted according to the demands of pharma companies that produce complex drug products and biologics.
Molded glass constitutes a major part of the worldwide injectable glass vials market (roughly 40%) and offers high mechanical and chemical resistance. Molded glass vials prove to be a supplemental solution for pharma companies that use tubular vials, where solutions ranging from 20 to 500 mL are now available.
References
About SGD Pharma
SGD Pharma is a global leader in glass pharmaceutical packaging. SGD Pharma produces over 8 million vials and bottles per day at its five manufacturing plants in Europe and Asia. All plants are ISO 15378 certified, and two are entirely new facilities.
With 10 sales offices and a wide distribution network, SGD Pharma offers a broad range of sizes and finishes in Type I, II, or III, amber and clear glass, as well as innovative added-value services like internal siliconization or protective plastic coatings.
Sponsored Content Policy: News-Medical.net publishes articles and related content that may be derived from sources where we have existing commercial relationships, provided such content adds value to the core editorial ethos of News-Medical.Net which is to educate and inform site visitors interested in medical research, science, medical devices and treatments.