Sponsored Content by NuAireReviewed by Olivia FrostJun 15 2023
From the first generation of Class II Biosafety Cabinets (BSCs), using a single motor/blower have improved reliability for controlling airflow dynamics for both downflow and inflow versus a dual motor/blower systems that independently control downflow and inflow respectively.
A wide range of processes in biological research require a class II biosafety cabinet (BSC). Scientists and lab technicians use this technology as the primary engineering control (PEC) to protect themselves (personnel) and their work materials (products) when working with potentially hazardous biological particulate materials. BSCs are often utilized in various forms of life science and pharmaceutical research, as well as sterile hazardous drug compounding/preparation.
Given the crucial safeguards provided by a BSC, these engineering controls must reliably provide constant airflow dynamics. In addition, a BSC must supply the necessary level of safety at an affordable lifetime cost of ownership. Meeting those criteria as effectively as possible depends on the cabinet's design and components.
The first generation of the modern-day class II biosafety cabinet was originally specified by the National Institutes of Health (NIH) in the early 1970’s document NIH-03-112 for BSC suppliers to NIH as minimum requirements for construction and performance.
The specification stated: “The unit shall have only one motor driven fan system for both recirculated and exhaust air.” When a change in blower speed occurs, inflow, and downflow speed still remain equal; by design, a single-blower system is inherently balanced. The NIH specification strengthened this idea that simplicity enhances reliability by reducing points of potential failure.
While the technology for fans, motors, and controls has advanced since then, the fundamental class II BSC design that delivers protection for personnel, product, and the environment remains the same.
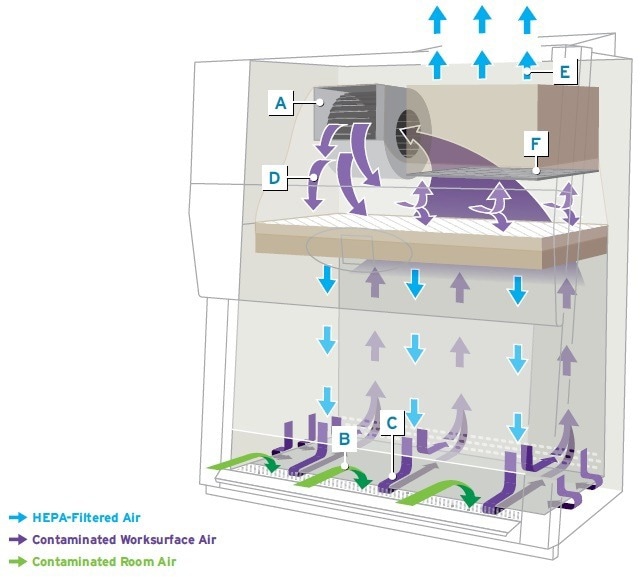
Class II Type A2 Biosafety Cabinet Airflow Dynamics. Image Credit: NuAire, Inc.
The class II BSC function provides airflow dynamics that start with the cabinet’s motor/blower system. [A] The motor/blower pulls air inflow through the cabinet’s access opening and into the front grill providing personnel protection. [B] The same motor/blower also pulls downflow air through the work zone’s and into the front and back airflow grills. [C] This combination of airflow action is often referred to as a Dynamic Air Barrier.
Simultaneously, the motor/blower pushes the air coming up from the intake grills through the supply HEPA filter, providing clean air for product protection. [D] The proportion of air that doesn't get recirculated is pushed out through the exhaust HEPA filter. [E] The exhaust volume is controlled by adjusting the baffle plate located beneath the exhaust HEPA filter. [F]
In a dual motor/blower system, the airflow pattern is identical to the above, but the exhaust airflow dynamics are controlled by an additional motor/bower.
Reliability and Balance
Reliability is the main feature of a biosafety cabinet since a BSC can only be safe if it is reliable. As the late Dutch computer scientist and winner of the 1972 Turing Award, Edsger Dijkstra, boasted, “Simplicity is prerequisite for reliability.” Expanding from this fundamental reasoning, a single-blower BSC is fundamentally more reliable than a dual-blower system by having one less point of potential failure.
With a single-blower BSC, a small adjustment to the blower speed and/or the damper is all that’s needed to calibrate your airflow setpoints. In most cases, an annual adjustment of the choke (baffle) plate provides precise airflow balance. Once the choke (baffle) is set, it doesn’t change, unlike a secondary motor/blower that can slow down as it ages. A change in the single motor/blower speed will ensure the inflow and downflow always remains balanced.
However, a dual motor/blower system results in more complex problems. Both motor/blowers must be controlled accurately, as even minute changes in either motor/blower will greatly impact the other.
The safety level of a dual motor/blower system depends entirely on how precisely the two motor/blowers can be calibrated. It is a delicate balancing act to keep two
blowers properly performing when they are in a constant state of pulling air from the same plenum and discharging in opposite directions. Essentially, the two motor/blowers are inclined to counteract each other if not properly maintained.
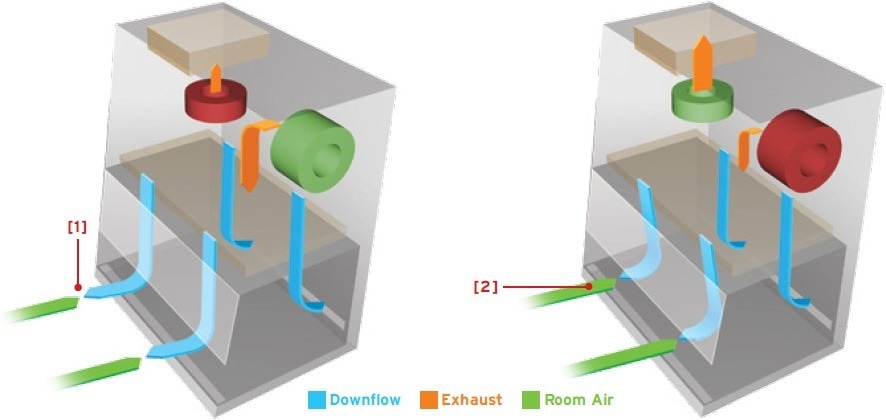
With a dual motor/blower system, a failure, or reduction in speed of the exhaust motor/blower can result in a high downflow condition, forcing potentially contaminated air into the room. [1] Conversely, a reduction in speed of the supply motor/blower can cause low downflow and allow room air to enter, and contaminate the work space. [2]
Image Credit: NuAire, Inc.
Filter Loading
Keeping the proper level and balance of airflow also depends on the condition and type of filters inside of the biosafety cabinet. The static pressure or resistance on the filter changes over time as it gathers particulates, which results in "filter loading." With a single motor/blower system, the ratio of downflow to inflow velovities remains about the same as the filters continue to load. In addition, some motor/blower systems automatically accommodate filter loading over time by adjusting the speed of the motor/blower as needed.
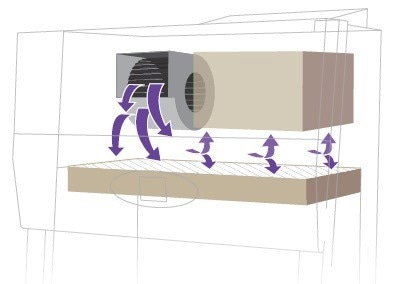
As particulate loads HEPA filters between certifications, a single motor/blower system maintains a consistent ratio of downflow to inflow, preventing uneven filter loading.
Image Credit: NuAire, Inc.
For most dual motor/blower systems, the two manually controlled motor/blowers are adjusted annually during field certification. Manually controlled motor/blowers typically do not accommodate for filter loading, leading to an unbalanced airflow dynamics, which could impact containment performance.
Other dual motor/blower systems use multiple feedback systems or sensors to automatically adjust blower speed. The increased intricacy of parts and sensors further exacerbates the number of points for potential failure, which makes the whole system more complex and less reliable.
Certification and Safety
To ensure the safe operation of any BSC, it should be certified upon installation, after any repair or being moved and, otherwise, annually. The field certification process should follow the NSF/ANSI 49 (Annex F).
The certification process of a BSC is performed by five tests:
- Downflow velocity test
- Inflow velocity test
- HEPA filter leak test
- Smoke pattern test
- Site installation test
The downflow and inflow velocity tests are performed at the same time, because adjusting either the motor/blower or baffle system affects both results. However, since the baffle system is fixed and not dynamic, adjustment can be made rapidly without system changes. It is usually more desirable for the certifier to set the nominal airflow velocities in the center of the NSF acceptable range that produces the highest level of containment performance.
The certification process can be somewhat more complicated in a dual motor/blower system that is not fixed, but dynamic with feedback and sensor systems. As you adjust one motor/blower, the system pressure will change causing an increase or decrease load on the second motor/blower.
This can make the certification of a dual motor/blower BSC more difficult when balancing the airflow. The certifier might measure the inflow, adjust one motor/blower, measure the downflow, adjust the second motor/blower, and this might be repeated several times, especially if one motor/blower keeps speeding up and slowing down due to system pressures.
If a single motor/blower experiences failure, it would be handled with the exact same procedure as a power interruption; the cabinet user would immediately stop their workflow, cover any open containers, and immediately exit the cabinet.
In a dual motor/blower system, if the supply blower fails, the exhaust motor/blower will continue to run, which would maintain some degree of air inflow. However, the inflow movement would be fundamentally different and very unsafe. The inflow movement would be more lateral and actually may cause more material to escape during the cabinet user’s stop work procedure.
When the exhaust motor/blower fails, a required safety interlock system must turn off the supply blower; otherwise personnel safety will be greatly compromised.
Furthermore, the additional requirement of the safety interlock creates another potential point of failure in a dual motor/blower system. The interlock must depend on a dedicated sensor system a to ensure the supply motor/blower turns off whenever the exhaust fails.
The timing of this interlock is very critical. In most cases, there is a slight delay from the moment the exhaust blower fails and when the interlock will disable the supply blower. During this brief time, there is a potential loss of containment resulting in potential contamination to the BSC user.
Overall, simplicity increases ease of certification, safety and reliability.
Total Cost of Ownership
To evaluate the total cost of ownership, the motor/blower system capacity must be taken into consideration. As a basic engineering principle, it takes more horsepower for a dual motor/blower system to achieve the same system capacity of a single motor/blower system. The additional motor capacity is needed to overcome the loss from the dual motor/blower system fighting itself.
If a manufacturer provides the required additional horsepower, the BSC creates more noise and vibration, as well as consuming more energy. The typical end result of today’s cabinets that use dual motor/blower systems is that they don’t provide an equal amount of system capacity. With lower system capacity, HEPA filter replacement occurs more often.
As a case in point, some dual motor/blower BSCs require filter replacements—a several thousand dollar repair—every 4 to 5 years, because the motor/blowers lack the necessary horsepower to properly compensate for filter loading. For example, today the NSF/ANSI 49 standard tests for the motor/blower system to handle at least a 50 percent increase of the starting filter load without readjusting the motor speed
control. However, in the past, the NSF/ANSI 49 standard required a benchmark of total system capacity to handle at least 180% with adjusting the motor speed control. This benchmark was removed as a requirement from the standard since the use of more energy efficient AC motor systems.
The result is that some dual motor/blower systems struggle to compensate for just 150 percent of the starting filter load. On the other hand, NuAire BSC’s with a properly designed, energy-efficient DC ECM single motor/blower can handle up to and even exceed 250 percent of the starting filter load. Consequently, the single motor/blower system works safely for 10 or more years before requiring any filter replacements.
Last, even if the two different motor/blower designed BSCs used all of the same components, the dual motor/blower system would cost more over time because doubling the parts will cost more for replacement when they fail in terms of both labor and material. When this occurs, the BSC must be decontaminated, and—in most cases—both blowers will be replaced, rather than risking a repeat of the procedure a year or two later for the other blower.
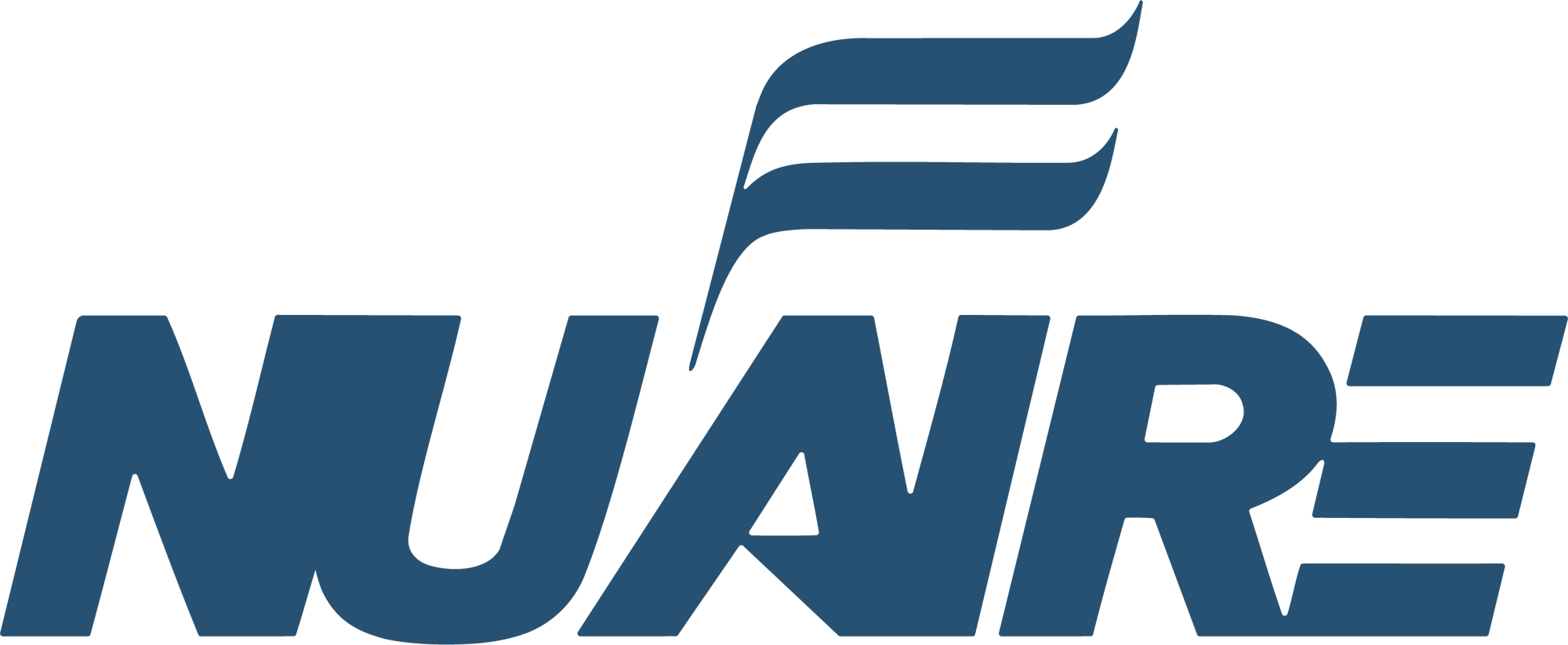
Laboratory Equipment - Premium Quality and Service
For over half a century, NuAire has consistently led the industry in safety standards and customer satisfaction. We obsess over our customers’ needs and tailor unique solutions to meet those needs. With invaluable input from customers like you, we now offer a wide range of biosafety cabinets, CO2 incubators, restricted access barrier systems, animal handling workstations, ultralow temperature freezers, and custom solutions. With our cutting-edge robotic sheet metal facility, we are able to deliver you custom, innovative solutions in addition to the standard laboratory equipment that we sell.
NuAire, Inc. has now sold more than 100,000 biosafety cabinets in more than 150 countries, spanning across all seven of the world’s continents. We pride ourselves on our products’ industry leading quality, reliability, low cost of ownership, and environmental sustainability. Our quality management system is certified to adhere to ISO 9001:2015 and 13485:2016 requirements. Our products are also celebrated for their ergonomic design, ease of use, and quiet operation. All standard BSC units sold in the US and Canada come with a 5-year parts & labor warranty. Every one of our machines are built specifically to your order, so we can guarantee satisfaction.
Add and extend your laboratory’s capabilities with any of the following products:
As NuAire continues to grow, we are committed to continuously improving our products and expanding our offerings. We always strive to provide you with the optimum level of personnel, environmental, and product protection throughout any industry.
Choose NuAire as the Safer Choice for Your Lab.
Sponsored Content Policy: News-Medical.net publishes articles and related content that may be derived from sources where we have existing commercial relationships, provided such content adds value to the core editorial ethos of News-Medical.Net which is to educate and inform site visitors interested in medical research, science, medical devices and treatments.