In an ideal world, an OEM medical device would come together pretty easily. The design of the device would be remarkably straightforward, requiring no revisions, and the extensive research and development process would swiftly progress without the need for any external assistance.
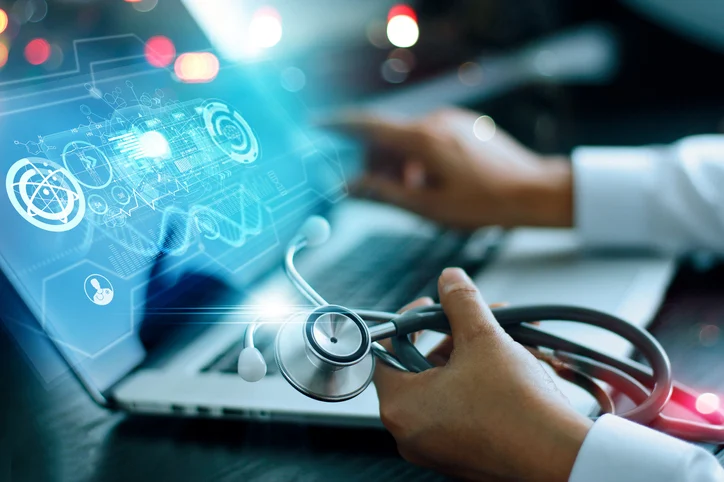
Image Credit: Amphenol Advanced Sensors
The device would successfully undergo regulatory testing, and there would be an extensive waitlist of dedicated customers eagerly anticipating the first production run from the company's assembly line. However, this idealistic vision is far from reality.
Developing an OEM medical device, whether it is a cranial catheter or a CPAP machine, demands years of meticulous research, hard work, and testing. It also involves collaborating with external suppliers and manufacturers to obtain custom components essential for the equipment's functionality.
Similarly, custom-integrated sensors, which are vital for OEM medical instrumentation application and design, do not effortlessly materialize. Achieving the desired outcome necessitates close collaboration with an experienced OEM sensor manufacturer, from the initial concept to the final stages of production and beyond.
Two Key starting points for medical instrumentation application and design
Two fundamental questions serve as crucial starting points when engaging with a sensor manufacturer during the design and development of electronic medical instrumentation:
- What is the application?
- Why is it important?
Although these questions may appear fundamental, their answers hold immense implications for the work carried out by the sensor manufacturer. They establish a solid foundation for the successful design of medical instrumentation with suitable sensor technology.
Understanding the application enables manufacturers to develop sensors that accurately measure and monitor data within the desired precision range, accuracy level, or operational environment while delivering robust results that meet performance requirements.
Comprehending the motivations behind an instrumentation project provides valuable insights into factors such as cost considerations and long-term usability needs. This knowledge can inform decision-making processes, such as specifying an optical filter for a detector system.
Ten other considerations for syncing sensors with medical instrumentation application and design
This is where the rubber starts hitting the road more. In essence, it becomes necessary to delve into finer intricacies concerning the medical device and its application. This enables the sensor manufacturer to craft a tailored device that not only fulfills but ideally surpasses all the specified requirements.
Although medical devices are often intricate, encompassing a range of considerations, the primary factors for selecting the appropriate sensor technology for the device are:
- Dynamic range
- Output
- Accuracy
- Environment
- Medium measured
- Device specs
- Customer-required performance specs
- Intended lifespan
- Budget
- Regulations/certifications
1. Dynamic range
Determining the necessary range for accurate sensor measurements is crucial. Insufficient range can result in missed changes, while excessive range may be unnecessary.
The linearity and hysteresis characteristics of the sensor should also be considered. It is essential to ascertain whether the sensor maintains accuracy across both low and high ranges.
2. Output
Consider the preferred method of data communication for the device's sensors. Depending on the application, analog or digital outputs, or even both, might be required. It may also be important to consider whether the device requires a specific interface like I2C or SPI, or whether it should be programmed to autonomously transmit data.
3. Accuracy
Precision is a non-negotiable aspect, but the required level of precision varies with each application. Advanced applications may demand high-accuracy sensors, whereas basic monitoring could suffice with lower-precision sensors.
4. Environment
It is vital to consider the environment in which the sensor will operate. For instance, it may have to encounter extreme temperatures, humidity, or other environmental factors.
The sensor's accuracy and reliability can be influenced by the conditions it faces during operation. If the environment is particularly harsh, the OEM must ensure that the selected sensor meets or surpasses the necessary industrial rating standards.
5. Medium measured
Similar to environmental considerations, it is important to determine the specific parameter that the sensor will measure. For example, a temperature sensor immersed in fluid requires a different design compared to one that remains dry, ensuring accuracy and longevity. This also applies to other sensor types, such as pressure and flow sensors.
6. Device specs
As each medical device is unique, it is essential to identify what sets the device apart. Specifically, what are the defining characteristics that the selected sensor must meet? Considerations may include:
- What is the device the sensor is going in?
- How big is the device?
- How much room is there for the sensor?
- What does the installation area look like?
- How should the sensor connect to the system, and what is the circuitry like?
- Are there sensor housing considerations?
As the device is one-of-a-kind, its sensors should also be unique. Every aspect of design and performance should be exclusively tailored to align with the specifications of the individual device.
7. Customer-requested performance specs
Each customer has unique requirements for the performance of the medical device and its sensors, often demanding specific benchmarks to be met. These include:
- Minimum and maximum response times
- Operating temperature range(s)
- Calibration requirements (or lack thereof)
- Supply voltage
- Drift and stability compensation
While these specifications may vary for each client, similar to the device specifications, it is crucial to engage in an in-depth conversation to ensure their specific needs are met.
8. Intended lifespan
Another crucial consideration to bear in mind is the expected lifespan of the sensor. Sensors designed for long-term use differ in their design and manufacturing compared to those intended for single-use applications.
Several factors influence this decision, such as environmental conditions (e.g., temperature or humidity), the need for frequent recalibration, and cost considerations.
9. Budget
Determining the budget is a fundamental question that lays the foundation for custom sensor development.
Depending on how much funding is available for the project, the OEM sensor supplier will need to carefully evaluate the choice of materials, production techniques, and technologies necessary to create the final product.
More importantly, if the budget does not match the actual production costs, it can stop moving forward on creating an inferior sensor. Think of it as a safety net in the process.
10. Regulations and certifications
It is well-known that all medical devices must undergo regulatory review and obtain approval before they can be made available to the public.
This meticulous process requires absolute attention to detail, as any errors can lead to delays or complete halts in the approval process. All it takes is one component of an OEM medical device not to meet a standard to put the entire piece of equipment out of compliance.
Some common regulations and certifications the device is likely to encounter include the following:
- CE Certification (European Union)
- ISO 13485 Certification (International Standardization)
- FDA 510(K)
These examples are only a fraction of the considerations involved when collaborating with an OEM sensor manufacturer to design medical devices that incorporate appropriate sensing technology.
Depending on the product and its application, there may be additional regulations and certifications that the devices and their components must meet. The manufacturer must stay updated on the specific regulations that apply to their products.
Syncing medical instrumentation application and design
Creating the accompanying sensor technology in collaboration with an OEM sensor manufacturer is a complex process that demands careful deliberation, much like designing medical devices.
By fostering a close partnership and paying meticulous attention to detail, both the design team and the sensor manufacturer can develop a product that not only meets but surpasses the required standards.
About Amphenol Advanced Sensors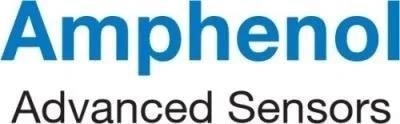
Amphenol Advanced Sensors, with its portfolio of industry-leading brands - Thermometrics, NovaSensor, Telaire, Protimeter and Kaye - is an innovator in advanced sensing technologies and innovative embedded measurement solutions customized for regulatory and applications, value by providing critical information for real-time decisions.
We offer domain expertise, rapid customization, world-class manufacturing capability and lasting customer relationships deliver the greatest value in cost of ownership to their customers.
Amphenol Advanced Sensors is a member of the USA-based Amphenol Corporation. With our own global presence we offer our customers exceptional technical support and service in the areas of development, production and distribution.
Sponsored Content Policy: News-Medical.net publishes articles and related content that may be derived from sources where we have existing commercial relationships, provided such content adds value to the core editorial ethos of News-Medical.Net which is to educate and inform site visitors interested in medical research, science, medical devices and treatments.