The need for a new custom sensor for your medical device is often immediate. However, the odds of a manufacturer producing custom sensors that match medical devices and their performance needs in stock and volume are almost non-existent.

Image Credit: Amphenol Advanced Sensors
Users should ideally have the sensors they need available as soon as needed. However, custom sensor technology in healthcare requires time to design, conceptualize, and manufacture at scale.
Below are the steps for making a custom sensor for your OEM medical device.
Seven steps to developing custom sensor technology in healthcare | start to finish
When creating a customized sensor solution for medical devices, there are two key things to be aware of: It is time-consuming and involved. A sensor created for your OEM medical device is unique, meaning that creating it is akin to cooking from scratch.
What does the process of developing a custom sensor solution look like?
Generally, there are seven steps in the development of a custom medical sensor with a sensor manufacturer:
- Initial consultation
- Drawing exchange
- Quoting
- Prototype development
- Sample performance review
- Product qualification/certification testing
- Full production
1. Initial consultation
This is the most important step. Setting the stage for what is to be created involves examining all of the details of the sensor and its application. This includes characteristics like:
- Sensor application – What is the sensor use and how will it be used?
- Sensitivity requirements – While accuracy is crucial, the required level of precision can vary depending on the intended application
- Temperature range – The thermal range the sensor requires to function effectively
- Environmental considerations – How much dust, moisture, and other environmental factors will the sensor be exposed to?
- Connectivity – Does the sensor need a wireless or wired connection for data transmission?
- Intended lifespan – Is the sensor reusable or disposable? If reusable, what is the ideal lifespan for the device?
- Any unique design considerations – e.g. size, material selection, housing
2. Drawing exchange
With an understanding of the final product specs, the sensor design team distills the vision into an engineering drawing. Once the drawing is completed, a copy is sent to the customer for review. In most cases, there will be further conversations to refine the plans.
This is similar to reviewing proposed schematics for a custom home—the plan will be very detailed.
Other elements, such as wiring diagrams, material selection, and other finer assembly points, will require reviewing, as well as the sensor's dimensions.
A few rounds of tweaking and adjustment will likely be needed to arrive at a design that meets and exceeds expectations.
3. Quoting
With an agreed-upon design with all of the specifics, your sensor manufacturer will provide a quote.
The quote will include a breakdown of the following:
- Unit cost at volume
- Prototyping costs
- Shipment logistics
- Turnaround time (relative to the order size)
- Tooling cost considerations
- Non-recurring engineering fees (where applicable)
4. Prototype development
This is where you will receive your first real-world look at the final product. It is also another stage of review.
The manufacturer will use the BOM, CAD, and other product literature from the design phase to develop physical prototypes. This is a crucial moment in development as you can interact with a physical version of your product before committing to production.
These early samples allow a look at the critical-to-quality elements, such as the biocompatible materials used, or to perform preliminary tests for performance and functionality.
The prototype phase is also an opportunity to make significant tweaks or adjustments as required.
5. Sample performance review
A sample is a step up from the prototype and the closest thing to the final product.
Similarly to the prototype, this is a chance to review the sample for performance, quality, and functionality – but at a more detailed level. Specifically, this is where you will evaluate:
- Sensor accuracy in detecting and measuring data
- Sensor performance over time, including consistency and reliability
- Sensor durability when exposed to the rigors of real-world use without breaking or malfunctioning
- The ease of use and user-friendliness to ensure it is intuitive and straightforward for medical professionals
- The overall size and fit of the device given its intended application.
Altering the sensor before the final step is possible; this is the last best chance to make any adjustments without drastically impacting the project timeline or budget.
6. Product qualification/certification testing
Qualification and certification testing is designed as another layer of review to prove the sensor's ability to operate safely and accurately in the intended environment.
This type of testing guarantees that the medical device meets the applicable national, international, and industry standards set by the FDA and CE or the EU's MDD. It is commonly executed by independent third parties, who review a wide range of elements, such as:
- Radiofrequency emissions
- Electromagnetic compatibility
- Environmental conditions, including temperature and humidity resistance
- Materials safety / biocompatibility
- Power usage / efficiency
Documentation and reporting processes are also crucial elements of the product certification process. Manufacturers must provide extensive data and documentation to show that their prototype medical sensors meet all required standards and regulations. This can include complex technical files, user manuals, labeling information, and other data that showcase compliance with regulatory requirements.
7. Full production
Once the above steps have been completed, the sensor is ready for total production. The sensor manufacturer will now deliver the sensors using the agreed-upon quality, quantity, and timeline.
It is important to note that manufacturers must continuously monitor the manufacturing processes throughout full production for product consistency and quality control purposes. This is key when producing a high-quality medical sensing solution that meets all regulatory requirements and customer expectations.
How long does it take to make a custom medical sensor?
In general, the process takes about 18 months to complete. Several factors can impact that timeline:
- Your Level of Readiness—In most cases, the client will arrive with many of the essential details ironed out, such as sensitivity, size, and intended lifespan. However, some are in the early stages of their product development and are not prepared to get into the specifics yet. In the latter case, it is going to take more time to resolve the initial stages of conceptualization and development as the specs are being debated in real time.
- Supply Chain Conditions—As seen during the pandemic, the global supply chain is very delicate. Although it has mostly recovered from the extremes of lockdowns, it is still fragile. No supply chain is impervious to outside factors that can cause disruptions—for example, extreme weather can create delays for several weeks.
- Meeting Compliance Requirements—Like the devices they are installed in, medical sensors must meet specific requirements to be approved for use. Depending on your location, this could result in additional rounds of evaluation and testing. Sometimes, it could also result in traveling to the testing facility or bringing an inspector on-site.
Custom sensor creation for medical devices | worth the wait
While developing a custom sensor for your OEM medical device does not happen quickly, nobody wants a component to fail to meet performance expectations.
It is a lengthy process, but working with a sensor manufacturer on a custom sensor solution during each step of production ensures that the sensor(s) more than meets the application's demands.
About Amphenol Advanced Sensors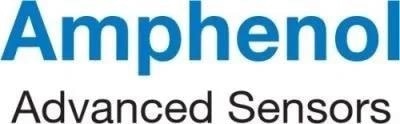
Amphenol Advanced Sensors, with its portfolio of industry-leading brands - Thermometrics, NovaSensor, Telaire, Protimeter and Kaye - is an innovator in advanced sensing technologies and innovative embedded measurement solutions customized for regulatory and applications, value by providing critical information for real-time decisions.
We offer domain expertise, rapid customization, world-class manufacturing capability and lasting customer relationships deliver the greatest value in cost of ownership to their customers.
Amphenol Advanced Sensors is a member of the USA-based Amphenol Corporation. With our own global presence we offer our customers exceptional technical support and service in the areas of development, production and distribution.
Sponsored Content Policy: News-Medical.net publishes articles and related content that may be derived from sources where we have existing commercial relationships, provided such content adds value to the core editorial ethos of News-Medical.Net which is to educate and inform site visitors interested in medical research, science, medical devices and treatments.