The GFD®Pilot is an Agitated Nutsche Filter Dryer (ANFD) that performs solid-liquid separation processes at kilolab and pilot scales, building on feasibility and proof of concept activities from earlier research and development stages. Despite its compact size, the GFD®Pilot maintains the quality, reliability, and efficiency characteristic of full-size PSL ANFD filter dryers.
PSL's unique GFD® technology addresses common production challenges manufacturers face with traditional methods like Büchner filtration and oven tray-drying.
The GFD®Pilot features an agitated vessel that operates under both vacuum and pressure. This vessel is available in Borosilicate 3.3 glass, 316L Stainless Steel, or Alloy 22 and includes a heated jacket for efficient drying. Solid-liquid separation occurs within a distinctive filtration basket that can be removed to facilitate and maximize product recovery.
Designed as the next step in scaling up from the GFD®Lab used in laboratory settings, the GFD®Pilot is instrumental in evaluating and developing the desired end product before transitioning to commercial production.
Download the Brochure for More Information
Features and benefits
Combined filtration and drying
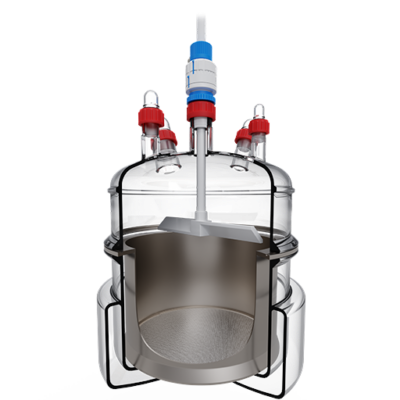
Image Credit: Powder Systems
The GFD®Pilot is an all-in-one filter dryer optimized for pilot plant production scale. It adheres to Good Laboratory Practices (GLP), making it a popular choice for pharmaceutical and fine chemical processing applications. This versatile system allows developers and manufacturers to conduct a broad array of processes within a single, standardized setup:
- Product Sampling
- Slurry Filtration (solid-liquid separation)
- Re-slurry
- Product Washing
- Vacuum Drying
- Product Discharge
Maximum product recovery
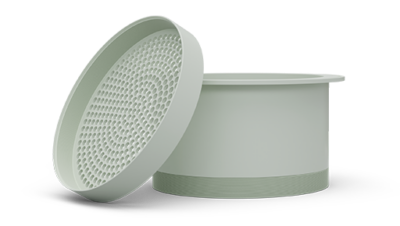
Image Credit: Powder Systems
Maximizing yield is crucial at pilot-scale feasibility stages and during small-scale production. The GFD®Pilot is designed with this priority in mind, recognizing the significance of the final product.
After completing the process, the product batch can be easily collected thanks to the removable design of the filtration basket.
The GFD® basket is ideal for multi-product applications, enabling quick and easy changeover of filtration meshes with various pore sizes and materials, including Polypropylene, PTFE, 316L stainless steel, and Alloy 22.
Flexible modular design
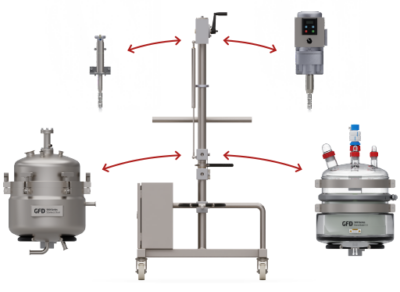
Image Credit: Powder Systems
The compact, mobile GFD®Pilot filter dryer offers exceptional production flexibility due to its modular design.
Like the GFD®Lab range, the GFD®Pilot’s base frame and motor are compatible with all relevant vessel materials (Borosilicate 3.3 Glass, 316L Stainless Steel, and Alloy 22), providing a simple, fit-for-purpose solution.
Complete mobility
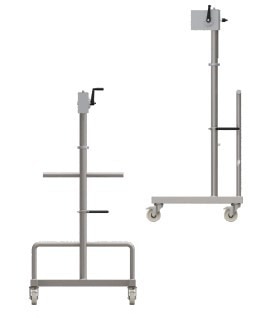
Image Credit: Powder Systems
The GFD®Pilot is mounted on a mobile frame to facilitate integration with various upstream processes.
The frame is designed to be as compact as possible, allowing it to fit within fume cupboards and walk-in laminar flow booths.
Hazardous area compliant
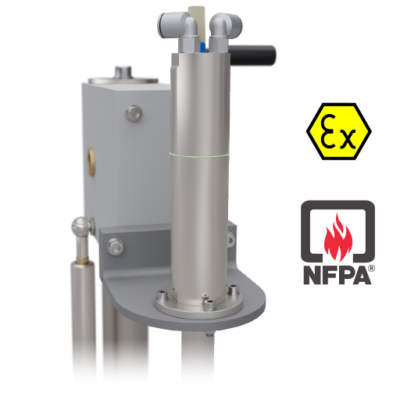
Image Credit: Powder Systems
When scaling up to the operational volumes available with the GFD®Pilot, the use of organic solvents in chemical and pharmaceutical processes often necessitates consideration of hazardous area requirements.
To address this, PSL provides alternative agitator drives that are suitable for such environments and come with the necessary certifications, such as ATEX and NFPA.
Furthermore, the use of pneumatic motor drives helps maintain a compact design.
Pressure directives
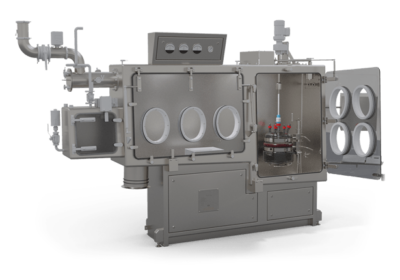
Image Credit: Powder Systems
When higher operating pressures are required, metallic versions of the GFD®Pilot are available.
These versions are designed and manufactured in compliance with the pressure directives of the installation location. PSL can provide U-Stamp, PED, and SELO certification as needed.
Be containment-ready with the GFD® Filterbox
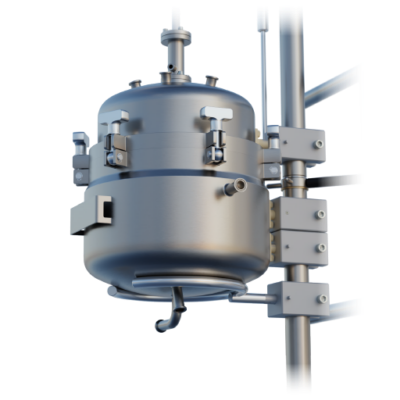
Image Credit: Powder Systems
As one of the early pioneers of containment technology, PSL developed the unique FilterBox isolator range to accommodate all types of vessels used with the GFD®Pilot.
By opting for a GFD®FilterBox, operators are safeguarded from the most toxic and potent compounds, while the product is protected from production environments.
Additionally, PSL can provide integration packages for third-party containment providers, ensuring comprehensive safety and compatibility solutions.
Download the Brochure for More Information
Technical overview
Applications and options
Vessel specification. Source: Powder Systems
. |
. |
Typical Product Cake Volume |
0.93 – 5.00 L |
Vessel Volume |
10.0 L |
Filtration Area |
0.05 m2 |
Frame Dimensions (H x W x D) |
1680 x 784 x 650 mm |
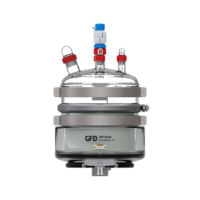
500 Series Glass Vessel. Image Credit: Powder Systems

500 Series Metallic Vessel. Image Credit: Powder Systems