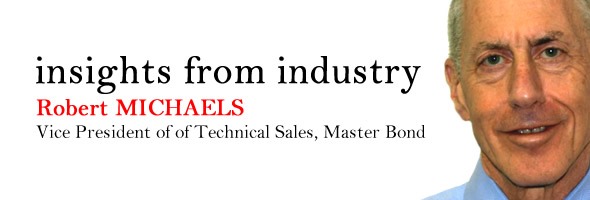
An interview with Robert Michaels, discussing the major challenges faced by engineers when designing medical devices and how Master Bond are working to make safe medical adhesives that aid the development of new technologies.
Could you please provide a brief introduction to the industry that Master Bond Inc. works within and outline the key drivers?
Master Bond manufactures a full line of formulations that have been fully tested to meet USP Class VI requirements for both disposable and reusable medical devices.
The growth of high performance polymers has given engineers more options when designing medical devices. Assembly with adhesives can offer big cost savings and performance advantages over traditional mechanical fasteners, as well as other bonding methods like welding, brazing and soldering.
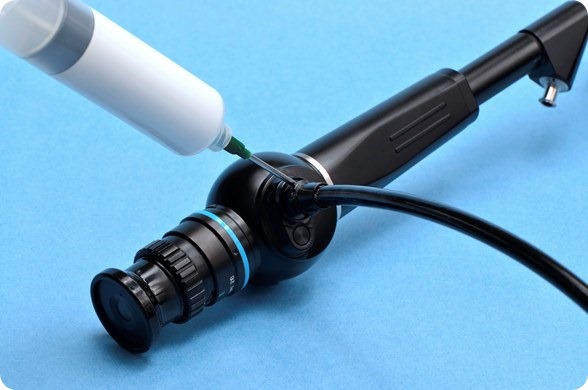
What are some of the issues medical device engineers face with respect to manufacturability requirements?
Successfully bonding medical components involves a thorough understanding of design options for joining similar and dissimilar materials, performance characteristics of the adhesive and substrate properties, assembly methods, curing procedures, and performance testing of the bonded joints for assembled devices.
Medical device engineers not only have to contend with difficult application requirements—such as high bond strength, thermal performance and chemical resistance—but they have the added challenge of working within a strict regulatory environment.
They must choose materials that are biocompatible and can withstand aggressive sterilization methods, which sometimes have conflicting end-use and manufacturability requirements.
What should the engineer know about biocompatible adhesives?
A common misconception is that United States Food & Drug Administration (FDA) regulations require that adhesives be tested for biocompatibility before they can be incorporated in a medical device.
Yet the FDA actually considers only the biocompatibility of the finished medical device, not its individual materials. Engineers have the freedom to select and combine materials as they please, as long as the finished device passes muster with the FDA.
In practice, sticking with materials known to be biocompatible makes it more likely that the finished device will be biocompatible. So device engineers rightly favor adhesives and other materials that have been “pre- screened” by passing industry standard biocompatibility tests. In North America, the most widely accepted test standard is United States Pharmacopeia (USP) Class VI.
Intended to evaluate the suitability of polymeric materials for direct and indirect patient contact, the USP Class VI regimen consists of a series of in vivo reactivity and toxicity tests. These tests involve injecting and implanting samples of the material under consideration into mice and rabbits, which are then evaluated at fixed time intervals for any ill effects.
Keep in mind that passing USP Class VI testing doesn’t guarantee that a device will gain FDA approval. What it does tell an engineer is that a material has low levels of in vivo toxicity under the test conditions. Yet given that a large number of standard adhesives cannot be considered biocompatible, USP Class VI testing represents a valuable tool for identifying products suitable for medical applications.
Master Bond formulates many specialized systems, such as UV15X-6Med-2, a UV curable system for bonding, sealing, coating and casting. It meets USP Class VI specifications and features high flexibility and outstanding abrasion resistance.
How do the sterilization methods affect the medical device and what is the impact of the sterilization on the adhesive used?
To answer this question, I’d like to focus on two broad categories of medical devices, disposable and reusable.
Let’s start with disposable devices. These are typically bulk sterilized a single time as part of their manufacturing process. ETO and gamma radiation have traditionally been the methods of choice, and neither pose a degradation problem for medical adhesives at that level of exposure.
The same goes for newer bulk sterilization methods, such as hydrogen peroxide and electron beam. In these disposable applications, a wide variety of Class VI epoxies, UV-curables, cyanoacrylates, and silicones adhesives can fit the bill. The choice will depend on the application requirements not related to sterilization.
Reusable devices paint a different picture. The vast majority of these will have to endure multiple trips through an autoclave, possibly even dozens of trips. Or they may be repeatedly treated with polymer-unfriendly chemical sterilizing agents.
For these devices, aggressive sterilization does indeed limit the number of suitable adhesives and polymer substrate materials. Epoxies typically hold up best to chemical, moisture and thermal resistance. So the majority of autoclave-tolerant adhesives tend to be an epoxy of one kind or another, although other adhesive chemistries can hold up in the autoclave as well if the cycles are more limited.
What is the relationship between designing a device for use and designing it for assembly?
Here again, the answer may depend on whether the device is reusable or disposable. If you assume that disposables have the highest manufacturing volumes, that would translate to the need for the most productive medical adhesives available.
For these applications, there are many Class VI adhesives that require little or no complex mixing, are easy to apply, cure quickly, bond without fixtures and resist common bulk sterilization methods. Among the popular choices for these high-volume applications are cyanoacrylates, UV-curables, LED light curable adhesives and some one-part epoxies.
With reusable devices, two component epoxies are best at withstanding multiple autoclave cycles, but are not always the fastest or easiest to use on the shop floor. They don’t cure as fast as cyanoacrylates or uv-curables. They may have mix ratios less straightforward than a simple 1:1. They may require fixturing and a heat cure. These issues are by no means insurmountable, and medical device makers successfully work with these adhesives every day.
At what point in the design process should the engineer consider which materials and bonding methods to use?
The best advice I can offer is to evaluate both materials and adhesives together, as a system, early in the design process. There is potentially a solution for just about every substrate combination, especially since the adhesive industry is continuously making strides in formulating products that work with tough-to-bond and dissimilar materials.
But some materials families, such as polyolefins, are notoriously difficult to bond and would require priming or pre-treating. This adds time and cost to the assembly process. If materials and adhesives were considered together, up front, one might be able to avoid some expensive trade-offs.
Are there any other productivity issues to consider?
Engineers will typically favor adhesives that cure at room temperature to avoid the time and expense of a heat cure. In medical applications, where quality and performance are paramount, adhesives formulated to cure at room temperature should still get the benefit from a heat cycle. In other words, mechanical and physical properties that are good after a room temperature cure are even better after a heat cycle, and medical devices need to be the best they can be.
How do you see the changes in medical device manufacturing affecting the field of adhesive technology over the next decade?
With the rise of medical electronic systems, from massive MRI and CT imaging systems, to tiny, implantable circuits, the design of medical electronics is becoming more sophisticated. Advanced assembly and packaging technologies are critical for achieving size, form factor, and power requirements while ensuring reliable performance, and keeping patients safe.
The combination of increasingly complex assemblies and exacting quality requirements is compelling design engineers to be exceptionally careful when selecting components, materials, and packaging technologies for medical electronic devices.
About Robert Michaels, Vice President Technical Sales
Robert Michaels received a BA in biology from Lehigh University, where he also minored in chemistry. He earned a Masters of Science degree from New York University in biology.
He has been lead coordinator all technical activities at Master Bond for the past 25 years. Supervisor of all technical support activities to both end users and as it pertains to quality control, Robert is also involved in product development and regulatory issues.
He has played an integral role in implementing growth and expanding the customer base both domestically in internationally to various high-tech industries including electronics, aerospace, medical device manufacturing, opto-electronics, OEM and related industries. He has published many articles and white papers on adhesives, sealants and coatings.
About Master Bond Inc.
Master Bond Inc. was founded in 1976. Their focus has been on developing the best in epoxies, silicones, UV cures and other specialty adhesive systems. They formulate the highest quality products and offer unmatched technical advice and customer support.
Their product line consists of advanced adhesives, sealants, coatings, potting/encapsulation compounds and impregnation resins. Each compound is designed to meet specific application needs and requirements.
For more information please visit: http://www.masterbond.com/