When utilized in respect of upstream biopharmaceutical manufacturing, flexibility denotes the simplicity of setting up, scaling up, and switching between batches and various processes.
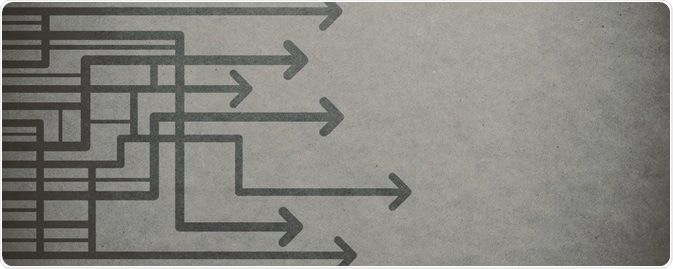
Image credit: Pall Corporation
Outstanding and enhanced flexibility is one of many key advantages of single-use systems (SUSs) and a primary reason why the adoption rate of SUS is so high. The more flexible single-use systems mean that processes can be developed and delivered a lot faster than stainless steel-based facilities.
This element is of vital importance in the global context of the race for a vaccine against COVID-19, which necessitates an industry-wide effort to hasten the development of vaccine candidates and to fundamentally support the accelerated manufacture of the billions of doses required for clinical trials and vaccination programs around the world.
The enhancement to upstream flexibility offered by SUSs has led to considerably simplifying the process development and scale-up.
This applies specifically to decentralized manufacturing – most elements of the cell culture unit process, including the single-use bioreactor in addition to auxiliary disposables including sampling manifolds, and connectors to mixing tanks and downstream equipment, can easily be replicated at a number of facilities.
Effective management and logging of the key variables in the process allow facilities on different continents to run almost identical processes.
With a certain degree of prior knowledge that comes with the process blueprint, time-consuming redesign and the building of infrastructure and hard piping, as in traditional steel systems, is no longer necessary.
This means current facilities can be re-tasked quickly and ready to manufacture with the appropriate regulatory approval in a matter of months as opposed to years.
For the coronavirus vaccine, speed to manufacture is crucial and upstream flexibility carried by single-use, the stirred tank has helped facilitate the global coordination of vaccine manufacture.
Another feature of flexibility is the capacity to effortlessly scale up a process. SUSs can enable this by maintaining vital cell culture parameters and fluid contact surfaces while also making the integration of supporting processes easier, including the preparation of cell culture media utilizing simple sterile connectors and disconnectors.
By both scaling-out and scaling-up, this straightforward technique can open up the possibility to produce clinical as well as commercial batches in the same facility.
SUSs also enable manufacturing facilities to rapidly switch between multiple drug manufacturing processes with ease. This is significantly more challenging with traditional steel systems.
Instead of spending additional time, before a new process, cleaning and validating a steel bioreactor, it is possible to just simply install a new SUS. This SUS is practically pre-validated as sterile and can prospectively run any process developed for that SUS and scale.
Such flexibility has led to biopharma facilities seeing a higher turnaround due to the possibility to manufacture a range of various products as necessary, allowing for the business to quickly respond to fluctuations in drug demand.
This requirement for flexibility is also reinforced by the fact that a number of newer drugs (especially those with orphan drug designation) are now being approved at an accelerated rate, meaning the demand for agile manufacturing facilities is now greater.
By adopting single-use technologies, especially upstream, generates a decrease in capital investment but also facilitates running multiple processes using the same hardware. Batch-to-batch and product-to-product contamination is eliminated due to the fact little, or no reusable fluid contact process elements are used.
This, in combination with the accelerated turnaround times in comparison to stainless steel-based processing, makes it an extremely attractive prospect to multiproduct facilities, and principally for contract development and manufacturing organizations (CDMOs).
In combination, flexibility and speed are powerful partners in supporting not only the fight against the current pandemic but the modifying the manufacturing landscape in general.
Here, some new drugs, namely those designated as orphan drugs, can follow a rapid approval process which results in an increased demand for agile manufacturing facilities.
In conclusion, single-use systems for the upstream phase of biopharma manufacturing have enabled the industry to enjoy simplified facility start-up, rapid scale-up and extraordinary agility to switch between processes.
For these reasons, it is anticipated that SUSs will create a legacy as the factories of the future are progressively centered around their use for their manufacturing needs.
About Pall Corporation
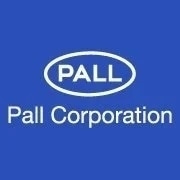
Pall Corporation is a global leader in high-tech filtration, separation and purification, serving the diverse needs of customers across the broad spectrum of life sciences and industry.
Pall Life Sciences provides cutting-edge solutions for customers who discover, develop and produce biotech drugs, vaccines, cell therapies and classic pharmaceuticals.
Our advanced medical technologies are often a patient’s last line of defense from dangerous pathogens. And our food and beverage products provide critical protection from contaminants during various manufacturing steps.
Pall Industrial serves customers in the microelectronics, aerospace, fuels, petrochemical, chemical, automotive, and power generation industries.
Our products play key roles in:
- Manufacturing innovative semiconductors and consumer electronics
- Filtration for commercial and military aerospace vehicles
- Maintaining reliability of essential industrial equipment
- Addressing mounting water quality, scarcity and demand issues
- Helping energy companies maximize production and develop commercially successful next generation fuels
Headquartered in Port Washington, New York, Pall has offices and plants throughout the world.
For more on how we enable a greener, safer future, visit Pall - Enabling A Greener, Safer Future.
Sponsored Content Policy: News-Medical.net publishes articles and related content that may be derived from sources where we have existing commercial relationships, provided such content adds value to the core editorial ethos of News-Medical.Net which is to educate and inform site visitors interested in medical research, science, medical devices and treatments.