High concentration mAb formulations and their properties
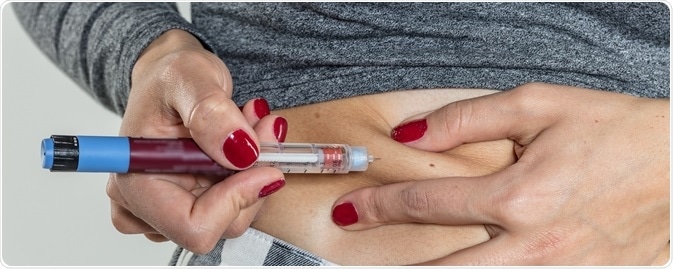
Image credit: Pall Corporation
Having first emerged as therapeutics in the 1980s, monoclonal antibodies (mAbs) are the predominant class of recombinant biologic drugs in development.
While intravenous (IV) infusion is a frequently utilized administration route for mAbs, for patients requiring a frequent dosing regimen, subcutaneous delivery (sub-C) in doses between 1-1.5 mL is now preferred as it supplies the possibility of self-treatment by utilizing pre-filled syringes2.
mAbs are usually required to be prepared at concentrations that are higher than 100 g/L and up to 250 g/L3,4 to be able to administer sub-C doses in these small volumes.
Molecular interaction potentials can create complications in fluids that contain high concentrations of mAb and other compounds, and understanding them and how they affect downstream processing, including filtration, remains difficult5.
Notably, interactions between mAb molecules can lead to a significant increase in viscosity at concentrations that are higher than 100 g/L, exponential with concentration and resulting in fluids between 20 and 60 centipoise (cP)6.
In order to assure a stable formulation of a finished drug product, a typical parenteral mAb for sub-C administration may contain:
- Stabilizers (e.g., trehalose, sucrose)
- Surfactants (e.g polysorbate 80, polysorbate 20, poloxamer 188)
- Buffers (e.g., acetate, phosphate, histidine)
- Viscosity reducers (e.g., arginine, sodium chloride)
Sterile filtration of high concentration mAbs
During a process that makes a Sub-C mAb, the highest mAb concentrations are typically seen after the concentration of drug substance before the final bulk filtration. They decrease slightly as a result of dilutions because of buffer flushes and formulation adjustments, although they continue to remain high until filling.
It is more complicated to sterile filter a highly concentrated mAb feed than it is to filter one at a low concentration. High aggregate contents have been reported with an increased mAb concentration7, affecting filter capacity and the high viscosities affect filter flux4.
Often, both of these factors are compensated for by utilizing oversized filters for what would traditionally be considered ‘small’ batch volumes; e.g., a 508 mm (20 in.) filter may be employed for a 10 or 20 L batch.
The presumption that a relatively large filter is needed for these batch volumes can bring about questions around filter compatibility; for example, how could an oversized filter influence critical to quality attributes (CQAs) through adsorption of critical formulation components or addition of leachables?
Membrane compatibility with the product and excipients is vital to this end and has to be assessed within a filter selection process3. Most significantly, oversizing of sterilizing filters causes excessive hold-up volumes of expensive fluid, which can be entrained in a device’s membrane, upstream volume and downstream volume.
This fluid (together with that in downstream tubing or pipework) is difficult to recover in a closed filter system, and its cost is much more than for traditional IV drugs. It can be thousands of dollars of cost for a few hundred mLs of held-up fluid in manufacturing, or even more if the hold-up is assessed in terms of market value.
When fluid is scarce in process development, it can affect the availability of material for clinical trials. Measures to recover products, like blowdown or buffer flush, are often considered, but they can be difficult to implement in closed systems because of their potential risk to system integrity and/or CQAs of the filtered fluid (e.g., sterility, purity).
Through good system design, the effect of non-recoverable fluid can be lessened and higher yields achieved at lower risk. The sterilizing filter specification is a key part of this. Using a compact filter with a low area will enhance yield and can also alleviate the compatibility concerns which might arise when utilizing an oversized filter.
Pall Corporation helps their customers to tackle these challenges, and those encountering challenges during the development or manufacture of high concentration mAb drugs are encouraged to go to Pall for support optimizing not only their sterile filtration step but other parts of their process workflow from concentration onwards.
About Pall Corporation
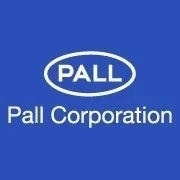
Pall Corporation is a global leader in high-tech filtration, separation, and purification, serving the diverse needs of customers across the broad spectrum of life sciences and industry.
Pall Life Sciences provides cutting-edge solutions for customers who discover, develop and produce biotech drugs, vaccines, cell therapies and classic pharmaceuticals.
Our advanced medical technologies are often a patient’s last line of defense from dangerous pathogens. And our food and beverage products provide critical protection from contaminants during various manufacturing steps.
Pall Industrial serves customers in the microelectronics, aerospace, fuels, petrochemical, chemical, automotive, and power generation industries.
Our products play key roles in:
- Manufacturing innovative semiconductors and consumer electronics
- Filtration for commercial and military aerospace vehicles
- Maintaining reliability of essential industrial equipment
- Addressing mounting water quality, scarcity and demand issues
- Helping energy companies maximize production and develop commercially successful next generation fuels
Headquartered in Port Washington, New York, Pall has offices and plants throughout the world.
For more on how we enable a greener, safer future, visit Pall - Enabling A Greener, Safer Future.
Sponsored Content Policy: News-Medical.net publishes articles and related content that may be derived from sources where we have existing commercial relationships, provided such content adds value to the core editorial ethos of News-Medical.Net which is to educate and inform site visitors interested in medical research, science, medical devices and treatments.