PCR protocols should be controllable. Controlling the PCR process helps obtain reliable results that are repeatable and precise.
Establishing the PCR protocol—five crucial variables
When creating a PCR protocol, users normally concentrate on the template DNA, reaction mix (buffer, dNTPs, taq polymerase), primers, probes, and the thermocycler, which is the main instrument used to carry out the reaction.
The plastics used to process the samples, such as plates, strips, or tubes, are often overlooked.
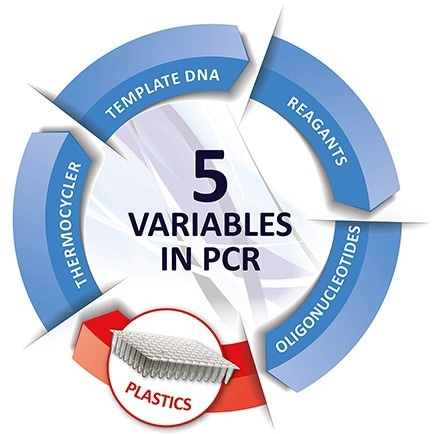
Image Credit: AHN Biotechnologie GmbH
The outcome of the PCR protocol
As an accredited laboratory, personnel accepts full responsibility for the accuracy of the results. An error could devastate a single patient, a larger population, or even a personal reputation.
This article will explain how PCR plastics affect the reproducibility and precision of the PCR protocol.
Controlling the PCR protocol #1: The variable of plastic
The impact of the plastic on the PCR protocol can be measured using two basic parameters:
- Accuracy: The average temperature reached on the entire thermocycler block
- Uniformity: The difference between the hottest and coolest well on the plate
The impact of plastics on the PCR protocol is detailed below.
Controlling the PCR protocol #2: Full DNA-sample recovery
The highly polished, non-binding inner surface is frequently emphasized on the market, although PCR is not about recovering the entire amount of liquid in the sample. The PCR protocol is based on the complete recovery of the DNA.
Expell PCR Plastics have anti-static properties. dNTPs and DNA are both negatively charged, but most plastics on the market are positively charged.
As a result, the probe’s elements will be retained by regularly used plastics.
Because the biomolecules do not “stick” to the plastic walls of the tube, Expell PCR Plastics ensures maximum sample recovery.
Controlling the PCR protocol #3: Closure of the tubes
Most PCR Plastics have a typical lid closure, with the cover’s straight edges pressed into the tube’s straight walls.
This closure necessitates higher pressure, resulting in “painful fingers,” particularly if the closure-opening action is performed frequently throughout the day.
Expell PCR Plastics’ lid-tube edges are bent. This one-of-a-kind and novel cap-tube design enables easy soft closure and opening while remaining 100% leak-proof throughout the PCR protocol, eliminating finger pain.
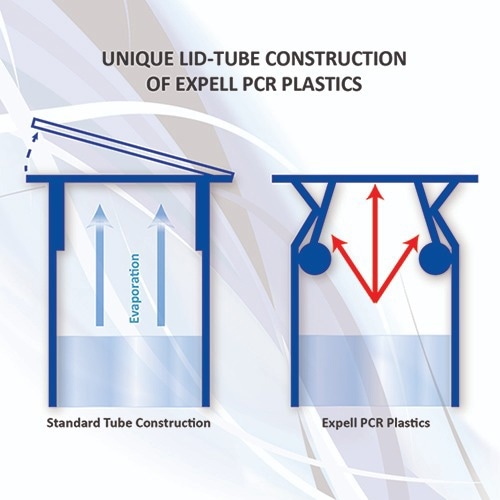
Image Credit: AHN Biotechnologie GmbH
Controlling the PCR protocol #4: Softness and flexibility of the Plastic
There are several types of polypropylene (PP) blends utilized in the fabrication of PCR Plastics. The type of plastic utilized will influence work comfort (open-close action), fitment of the plastic into the thermocycler block, and plastic durability.
Many routinely used PCR Plastics break during the PCR protocol.
Expell PCR Plastics’ unique PP composition makes them easy to use and keeps them from breaking when temperatures fluctuate.
Controlling the PCR protocol #5: Evaporation and thermal conductivity
Thin-walled plastics are associated with improved thermal conductivity, which is true to some extent. The key question here is which portion of the tube has thin walls. Are the tube’s sidewalls thin, or is it the bottom of the tube that touches the thermocycler block’s well?
The thicker the tube walls, the less gas escapes—as PP is not a gas-tight material.
Thermal conduction takes place at the tube’s bottom, where it makes direct contact with the block well, transferring heat.
Expell PCR Plastics have a thin bottom and thicker sides, allowing maximum heat conduction and, when combined with the revolutionary lid closure, lower the evaporation rate to only 5%.
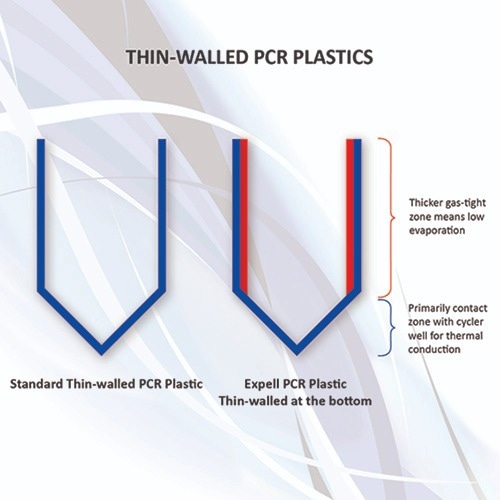
Image Credit: AHN Biotechnologie GmbH
Controlling the PCR protocol #6: Thermocycler fitment
When selecting the PCR plastic, consider the height of the tube. For example, fast PCR or qPCR thermocyclers operate best with low-profile tubes measuring 15.6–16.6 mm. Standard PCR/qPCR cyclers will work with 20.9–21.8 mm profile tubes. A regular profile tube will be crushed if used on a fast cycler.
Expell PCR Plastics offers a comprehensive portfolio compliant with most cyclers on the market.
About AHN Biotechnologie GmbH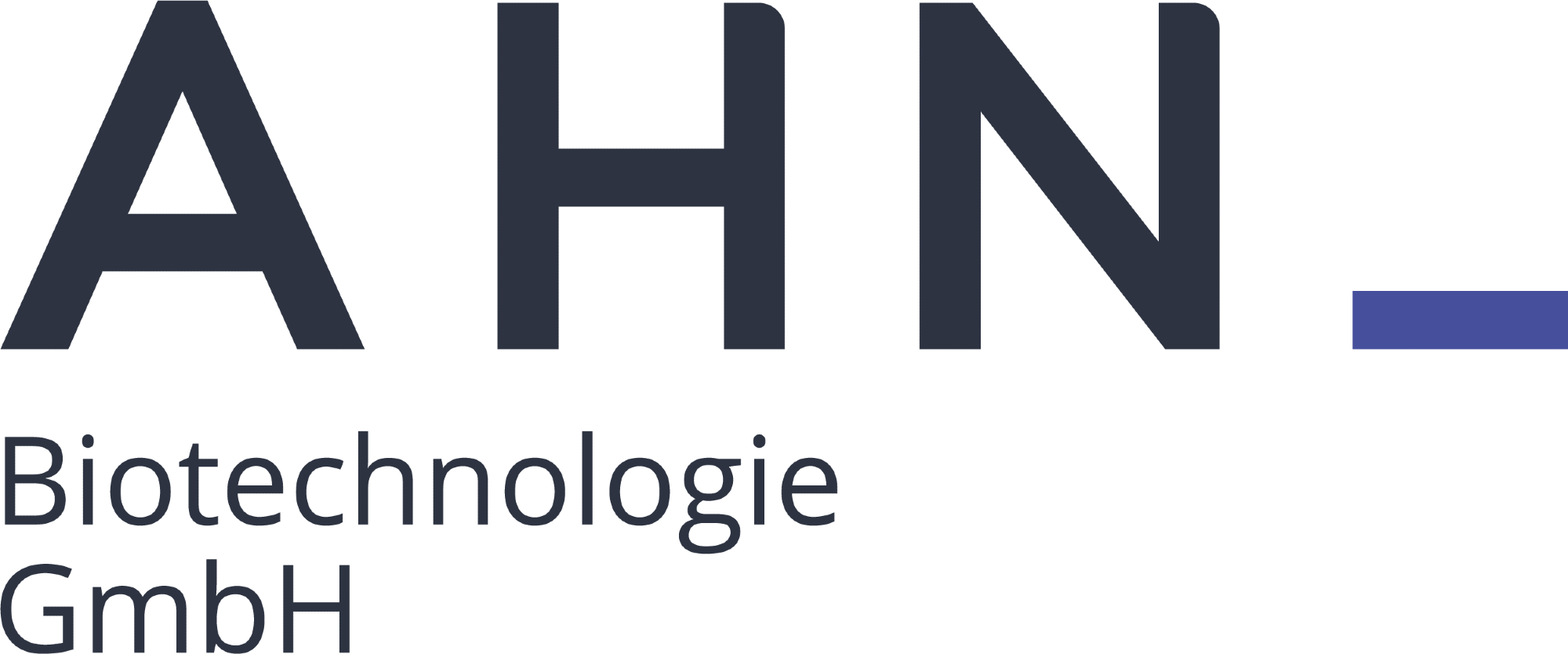
AHN Biotechnologie GmbH, based in Nordhausen, Germany, is a manufacturer of plastic injection molded products, life science products and laboratory consumables for worldwide laboratory use.
With over 20 years’ manufacturing experience in serving German and global leaders in the Laboratory Automation Industry, we have been acting as a global OEM manufacturer of consumables for many outstanding life science brands and distributors. Our state-of-the-art manufacturing facility meets and exceeds the rigorous standards and quality requirements of the best-known brands we supply.
At the same time, we are strengthening our three associated brands: CAPP, AHN and Maxxline by producing and supplying a comprehensive range of consumables, liquid handling devices and laboratory equipment. Our unique combination of flexibility, innovation and high-quality production automation ensures that our laboratory products meet the needs of customers worldwide and meet their high-quality requirements.
With our expertise in manufacturing laboratory consumables and the state-of-the-art electric injection molding technology that offers faster production turnaround time and sustainable quality products, we achieve the best value for money that meets the strict standards of the modern laboratory industry.
Sustainability is built into every part of our production flow and is reflected in all our products, such as the plastic-saving pipette tip refill systems, the cardboard racks for pipette tips or cryovials.
Sponsored Content Policy: News-Medical.net publishes articles and related content that may be derived from sources where we have existing commercial relationships, provided such content adds value to the core editorial ethos of News-Medical.Net which is to educate and inform site visitors interested in medical research, science, medical devices and treatments.