Cleanroom classifications
Cleanrooms are designated as controlled environments where the levels of airborne particles are carefully regulated.
Their construction and utilization are meticulously planned to minimize the ingress, creation, and retention of particles and microorganisms within the space. Pertinent factors like temperature, humidity, and pressure are also carefully controlled as required.
How particle size impacts classification
The design and construction of a cleanroom in a contaminant-free environment by applying non-particulate materials significantly impact the space's cleanliness level. The amount of airborne particles with a diameter bigger than 0.5 µm per cubic meter of space is used to calculate the level of cleanliness, or ISO Class.
For instance, a customer may specify a requirement of fewer than 100 particles per square meter in their cleanroom, leading to selecting an ISO 5 cleanroom. However, a notable distinction arises when comparing particles of 0.5 microns and those measuring 5 microns.
If the customer assumes they are dealing with 0.5-micron particles, but the problematic particles are 5 microns in size, it significantly impacts the cleanroom classification. In such a case, the appropriate classification would be an ISO 8 cleanroom, not an ISO 5 cleanroom.
How contamination relates to cleanroom classification
Modular cleanrooms must adhere to the ISO 14644-1 cleanliness classification in design, construction, and operation.
The required level of cleanliness for a specific room is contingent upon the nature of the tasks conducted therein. Products that are more susceptible to contamination demand a higher standard of cleanliness. Once classified, the room must be consistently maintained to adhere to the specified criteria, including:
- Cleanliness
- Temperature
- Humidity
- Pressure
- Number of air changes/hr
- Flow rate
Cleanroom ISO classification
The ISO classification ranges from Class 1 (the cleanest) to Class 9, with lower ratings indicating cleaner environments.
For example, an ISO Class 6 cleanroom permits no more than 35,200 particles greater than 0.5 microns per cubic meter.
Source: Monmouth Scientific Limited
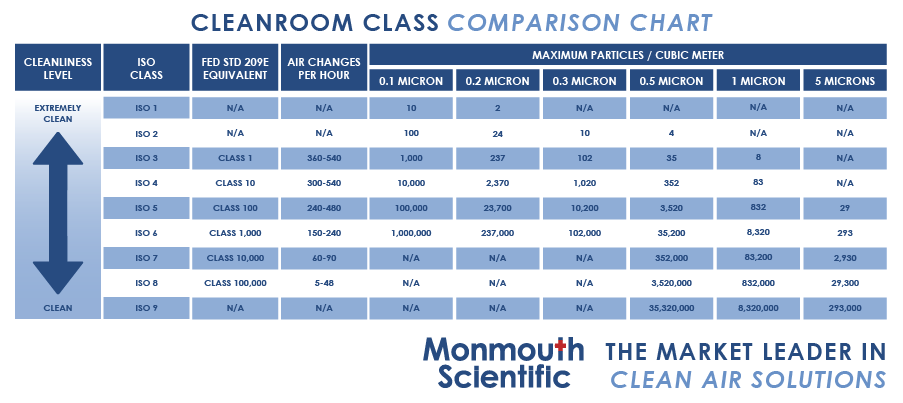
Cleanrooms rated ISO Class 7 or cleaner typically include a Changing Atrium for gowning, separated from the main working area. This measure reduces contaminants from entering the clean area due to personnel movement.
Various determining factors come into play, and each industry has a default starting point. In medical device packaging, for instance, the default is an ISO 7 cleanroom.
The key question to consider is: What level of contamination is required? Identifying the problematic particle size and determining the necessary air circulation to eliminate the contamination are essential considerations.
Positive & negative pressure cleanrooms
Most cleanrooms are designed as positive-pressure environments to prevent contaminants from entering the room. Air is introduced into the cleanroom, usually from the ceiling level, after passing through a fan-powered HEPA filter. These filters can remove particles as small as 0.3 microns.
This configuration creates a pressurized space, with higher inside air pressure than the exterior. This leads to the downward flow of air, along with any contaminants present, toward the floors, ultimately getting expelled through vents in the lower portions of the room.
Consequently, this continuous airflow ensures that air and contaminants generated within the room's processes are consistently expelled from the cleanroom. Furthermore, when air exits a room when doors are opened or through vents, it maintains sufficient pressure to prevent contaminants from entering through these openings.
In contrast, negative-pressure rooms are specifically designed to prevent contaminants from leaving the room. They are utilized in situations involving infectious diseases, pathogens, biocontaminants, and certain hazardous processes involving chemicals, flammables, and potentially explosive liquids and powders.
Inside a negative-pressure room, the air is actively extracted from the enclosure through reversed HEPA filters, generating negative pressure that keeps contaminants from escaping.
Simultaneously, the air is continuously drawn into the room through venting and other openings. The force of the incoming air effectively prevents contaminants from being released into the surrounding environment.
Save costs with a controlled environment
It is feasible to employ a lower ISO level cleanroom by outfitting individuals with garments suited for a higher level of cleanliness and gaining insights into the sources of contamination.
Strategic placement of return air grills and filtration systems can create cleaner zones within the cleanroom, effectively lowering the overall ISO level. This approach reduces construction expenses and leads to significant cost savings in operations.
About Monmouth Scientific Limited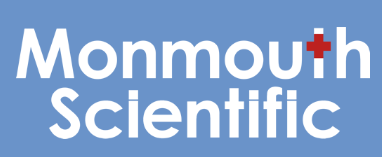
At Monmouth Scientific environmentally responsible recirculating technology is the core of our expertise.
Our specialised Fume Cupboard, Laminar Flow, Biological Safety, Powder Containment, and ISO Class Cleanroom solutions provide the best protection and performance for your personnel.
A UK Market Leader in Clean Air Solutions and at the forefront of the industry, we employ cutting-edge technologies and innovative engineering, to ensure that our solutions consume minimal energy while delivering optimal performance.
As experts in clean environments and laboratory personnel safety, our team continue to proudly pioneer innovative new technologies to guarantee the highest levels of safety for a diverse client base including;
- Laboratory
- Research
- Pharmaceutical
- Electronics
- Aerospace
Sponsored Content Policy: News-Medical.net publishes articles and related content that may be derived from sources where we have existing commercial relationships, provided such content adds value to the core editorial ethos of News-Medical.Net which is to educate and inform site visitors interested in medical research, science, medical devices and treatments.