The effectiveness of the state-of-the-art Fume Cupboards, Laminar Flow, and Biological Safety Cabinets lies not only in their sophisticated airflow systems but also in the crucial role played by the selection and efficiency of the filters.
Activated Carbon Filters
The slow and controlled degradation of the solid charcoal mass through high-temperature steam activation generates millions of pores. This process induces the formation of a highly porous material, ensuring an extensive internal adsorption surface.
An example of this adsorption capacity is evident in the carbon filter of a standard fume cupboard, which boasts a surface area equivalent to 5000 football pitches.
Physical adsorption involves the carbon atoms' attraction of outward forces from the surface. These forces, commonly known as Van der Waal's forces, draw in the molecules of surrounding gases, leading to their adsorption at the surface of the activated carbon.
In cases where certain substances are not effectively adsorbed, specialized impregnated carbon filters come into play, entrapping fumes and gases through chemisorption.
The process of chemisorption attracts the surrounding gas molecules to the adsorbent filter surface through several means, including:
- Converting the gas into another species that is either more readily adsorbed or non-hazardous.
- Chemically combining with the gas.
- Promoting catalytic activity whereby the gas/vapor reacts with air or itself to produce another species that is either more readily adsorbed or non-hazardous.
As a result, compounds with low adsorption ratings, including ammonia, hydrogen sulfide, inorganic acids, mercury, and formaldehyde, can be efficiently captured and neutralized using specially impregnated carbon filters.
Source: Monmouth Scientific Limited
Carbon Code |
Suitable for Removal of |
AC |
General Organic Compounds (iodine, Solvents, Odors etc) |
ACID |
Acidic Compounds (and general organics) |
ACR |
Alkali Compounds (and general organics) |
AMM |
Ammonia & amine compounds (and general organics) |
CYN |
Cyanide Compounds |
ETHER |
Ether Compounds (and general organics) |
FORM |
Aldehydes (and general organics) |
SUL |
Sulfur Compounds (and general organics) |
MCH |
Special blend of up to 4 of the above carbon types |
ED |
Tri-Layered Filter for schools (organic, acid & alkali removed) |
The selection of the appropriate carbon grade, as is the fan and filter bed sizing, is crucial to ensure both containment and filter efficiency.
Unlike particulate filters, carbon systems operate as dynamic rather than absolute filters. When a gas molecule is adsorbed onto the carbon bed, various forces, such as heat, air velocity, molecular energy, and displacement by a more readily adsorbed chemical, may cause it to move from one site to another within the filter bed.
Consequently, there is always an active zone within the filter where the primary adsorption occurs. As the carbon becomes laden with adsorbed substances, this active zone shifts through the bed. If it approaches the outlet, desorption from the filter can lead to the release of the chemical back into the atmosphere, necessitating the replacement of the filter.
To achieve containment at the working aperture of the fume cupboard, a face velocity ranging from 0.3 to 0.5 m/sec is necessary.
This volume of air must pass through the carbon filter, and to ensure effective filtration, the minimum dwell time within the filter bed must be sufficient to allow proper adsorption and prevent excessive desorption. Consequently, the filter bed depth becomes a critical design criterion.
High-efficiency particulate air (HEPA) filters
HEPA filters and ULPA filters share the same construction method and are designed to capture 99.97% of air contaminants and particulates measuring 0.3 microns or larger through a complex web of fibers. The filtration process involves four different mechanisms depending on the size of the particle: Inertial Impaction, Diffusion, Interception, or Sieving.
For larger contaminants, inertial impaction and sieving are utilized. These particles either collide with the fibers and become trapped or are obstructed while attempting to pass through the fibers.
Medium-sized particles are captured through interception as they move through the filter where they are intercepted by the fibers. Smaller particles are dissipated while they traverse through the filter until they eventually collide with a fiber and become trapped.
A notable advantage of HEPA filters is their increasing efficiency as they become saturated with contaminants. As the filters load up, their airflow capacity decreases, and static pressure rises, leading to greater efficiency.
Once the recommended speed of 0.45 m/s at the filter surface can no longer be maintained, it indicates that the filter has reached its capacity, and a replacement becomes necessary. The monitoring of this process is facilitated by a differential pressure gauge.
Ultra-low penetration air (ULPA) filters
ULPA filters boast exceptional efficiency, ensuring a remarkable 99.99996% arrestance of 0.12 µm particles.
This advanced filter technology plays a vital role in providing surgically clean air within operating theatres, safeguarding foodstuffs and pharmaceuticals during manufacturing processes, creating safe working conditions for personnel at nuclear power plants, and producing clean air within safety cabinets.
The filtration media employed in ULPA filters is predominantly composed of fine-diameter sub-micron glass fibers, typically ranging from 0.3 to 4 µm in size. These fibers are folded into pleats and secured within a frame. Importantly, the gap between the fibers is significantly larger than the size of the particles to be removed.
The filtration process relies on particles coming into contact with the fibers and being retained through either surface or electrostatic forces. Although the airstream brings particles close to the fibers, the final collision is primarily a result of factors such as inertia, Brownian motion, or electrostatic attraction.
About Monmouth Scientific Limited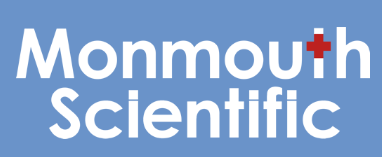
At Monmouth Scientific environmentally responsible recirculating technology is the core of our expertise.
Our specialised Fume Cupboard, Laminar Flow, Biological Safety, Powder Containment, and ISO Class Cleanroom solutions provide the best protection and performance for your personnel.
A UK Market Leader in Clean Air Solutions and at the forefront of the industry, we employ cutting-edge technologies and innovative engineering, to ensure that our solutions consume minimal energy while delivering optimal performance.
As experts in clean environments and laboratory personnel safety, our team continue to proudly pioneer innovative new technologies to guarantee the highest levels of safety for a diverse client base including;
- Laboratory
- Research
- Pharmaceutical
- Electronics
- Aerospace
Sponsored Content Policy: News-Medical.net publishes articles and related content that may be derived from sources where we have existing commercial relationships, provided such content adds value to the core editorial ethos of News-Medical.Net which is to educate and inform site visitors interested in medical research, science, medical devices and treatments.