Pharmaceutical products are produced to meet strict standards for effectiveness and quality. Every aspect of quality is assessed, taking into account the risks associated with the method of delivery (such as injection or ingestion) and the way they are manufactured (whether aseptic, terminally sterilized, or under less controlled conditions).
The document focuses on two aspects of this process: the quality of the manufacturing environment and the standards governing particle concentration limits that define a controlled environment.
The paper examines standards for physical testing (specifically EN ISO 14644-1:2015)1 and the regulatory guidelines (EU GMP Annex 1).2
ISO 14644-1
ISO 14644-1, which became active in 1999, established the room classification standards within the ISO 14644 suite. It determines how a room should be classified and sets the maximum allowable particle count in a specific volume of air.
It is important to note that while ISO 14644 is widely adopted for cleanroom classification globally, there are variations in routine monitoring, especially when comparing ISO 14644 to EU and WHO GMP standards. The cleanroom's certification status should be determined before testing, and ISO 14644-1 defines three certification states.
- As-Built: This state represents a finished room with all services connected and operational, but it lacks production equipment or personnel.
- At Rest: In this state, all services are connected, and all equipment is installed and functioning as agreed, but no personnel are present in the facility.
- Operational: This state signifies that all equipment is installed and functioning according to the agreed format, and a specified number of personnel are present, following an agreed procedure.
The particle concentration limits for the cleanroom, exceeding a specified size, are outlined and provided in Table 1.
Table 1. Airborne particulate cleanliness classes for cleanroom and clean zones (as indicated in ISO 14644). Source: Particle Measuring Systems
ISO 14644-1:2015
Classification
Number (N) |
Maximum concentration limits (Particles/m3) |
0.1 μm |
0.2 μm |
0.3 μm |
0.5 μm |
1.0 μm |
5.0 μm |
ISO Class 1 |
10 |
|
|
|
|
|
ISO Class 2 |
100 |
24 |
10 |
|
|
|
ISO Class 3 |
1 000 |
237 |
102 |
35 |
|
|
ISO Class 4 |
10 000 |
2 370 |
1 020 |
352 |
83 |
|
ISO Class 5 |
100 000 |
23 700 |
10 200 |
3 520 |
832 |
|
ISO Class 6 |
1 000 000 |
237 000 |
102 000 |
35 200 |
8 320 |
298 |
ISO Class 7 |
|
|
|
352 000 |
83 200 |
2 930 |
ISO Class 8 |
|
|
|
3 520 000 |
832 000 |
29 300 |
ISO Class 9 |
|
|
|
35 200 000 |
8 320 000 |
293 000 |
These limits have been established in alignment with the standard using the following formula for the intermediate decimal classes:
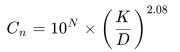
Where,
- Cn is the maximum permitted concentration (particles per cubic meter) of airborne particles that are equal to and greater than the considered particle size.
- N is the ISO classification number, which shall not exceed a value of 9 or be less than 1.
- D is the considered particle size, in micrometers, that is not listed in Table E-1.
- K is a constant, 0.1, expressed in micrometers.
The connection between the particle size and its prevalence in a population is determined by the function
. When plotting particle size against concentration on a logarithmic scale, each class exhibits a slope of 2.08, as indicated in the Table above.
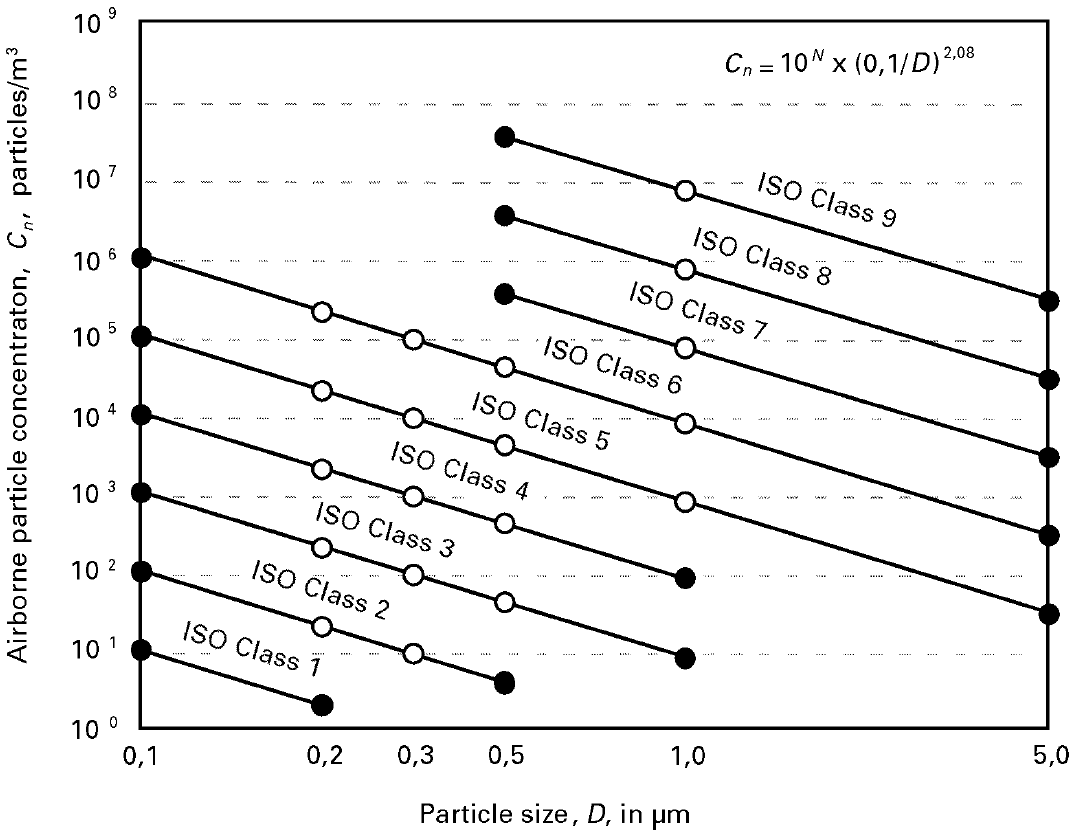
Figure 1. V Graphical representation of iso class concentrations limits for selected classes. Image Credit: Particle Measuring Systems
To certify a cleanroom or clean zone, the designation should include the following components:
- The room classification number is expressed as “ISO Class N.”
- The state of occupancy.
- The specific particle size is considered. It is also possible to certify a cleanroom for multiple sizes; in such cases, the sample volume requirement for the largest particle size is utilized.
Example
For instance, consider unidirectional airflow device X, which is classified as an ISO Class 5 clean zone at 0.5 µm with (3520 n/m3) in the operational state.
To confirm the classification, the ISO 14644-1 standard outlines the necessary steps for compliance verification. Assuming a clean air device intended for use in an aseptic preparation area.
This area must meet the ISO Class 5 standard at 0.5 µm, which is equivalent to 10,000 particles per cubic foot (≡ 10,000 /ft3) in the operational state.
The room is 12 m by 5 m (60 m2) and has a worktable in the center of the room.
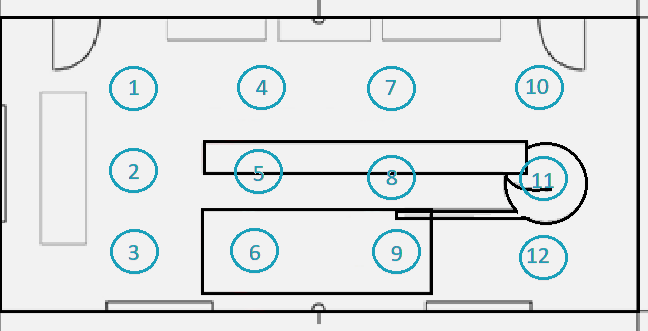
Figure 2. Diagram showing the locations for classification within the clean zone. Image Credit: Particle Measuring Systems
- Step 1: Calculate the maximum permitted particle concentration.

Figure 3. Maximum permitted particle concentration calculation. Image Credit: Particle Measuring Systems
Cn |
3520 n/m3 |
is the maximum permitted concentration |
N |
5 |
is the ISO classification number |
D |
0.5 μm |
is the considered particle size, in micrometers |
K |
0.1 μm |
is a constant, 0.1, expressed in micrometers |
- Step 2: Determine the number of sample locations from the Table below.
Table 2. Number of sample locations required. Source: Particle Measuring Systems
Area of Zone (m2) |
ISO 14644-1:1999 |
ISO 14644-1:2015 |
2 |
2 |
1 |
4 |
2 |
2 |
6 |
3 |
3 |
8 |
3 |
4 |
10 |
4 |
5 |
24 |
5 |
6 |
28 |
6 |
7 |
32 |
6 |
8 |
36 |
6 |
9 |
52 |
8 |
10 |
56 |
8 |
11 |
64 |
8 |
12 |
68 |
9 |
13 |
72 |
9 |
14 |
76 |
9 |
15 |
104 |
11 |
16 |
108 |
11 |
17 |
- Step 3: Calculate the sample volume.
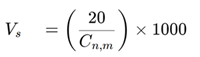

According to ISO 14644-1:2015, the formula calculates a sample volume of 5.68 liters. Using a standard particle counter with a flow rate of 28.3 liters per minute, a 1-minute sample would exceed the minimum sample volume requirement. Therefore, to adhere to the specifications, a 1-minute sample at each of the 12 locations is required.
- Step 4: Take measurements at each location (1 minute per sample) and record the results.
Table 3. Illustration of locations within the example clean zone and measurement results. Source: Particle Measuring Systems
LOCATION |
NUMBER /m3 |
1 |
708 |
2 |
885 |
3 |
1522 |
4 |
2336 |
5 |
3363 |
6 |
2584 |
7 |
2301 |
8 |
2089 |
9 |
1344 |
10 |
2013 |
11 |
1756 |
12 |
1897 |

This area satisfies the requirements for an ISO Class 5 clean zone at 0.5 µm and is now ready for its intended use. The room classification should be periodically reevaluated as determined by ISO 14644-2.3
EU GMP Annex 1
The European Union GMP guidance for sterile manufacturing underwent a revision in 2003 to align with the shift from various cleanroom standards to a unified cleanroom standard, ISO 14644-1. This alignment is highlighted on the front page.
“Annex 1 of the EC Guide to Good Manufacturing Practice (GMP) provides supplementary guidance on the application of the principles and guidelines of GMP to sterile medicinal products. The guidance includes recommendations on standards of environmental cleanliness for clean rooms. The guidance has been reviewed in the light of the international standard EN/ISO 14644-1 and amended in the interests of harmonization but taking into account specific concerns unique to the production of sterile medicinal products.”
More specifically, the certification process for cleanrooms needed to adhere to the rules and format of ISO 14644-1 guidance. However, there were modifications in the ISO standard related to sterile medicinal products.
In response, a table of cleanroom certification values was established to align somewhat with ISO 14644-1. To ensure clarity, a series of notes accompanied this Table, though the initial Note 'a' caused some confusion.
The confusion was addressed in the 2008 release of EU GMP Annex 1, which clearly outlines three essential phases to be conducted.5
Each cleanroom and clean air device should first undergo classification. Subsequently, it should be regularly monitored to confirm the maintenance of conditions concerning product quality. The data collected from this monitoring should be reviewed in light of the risk to the quality of the finished product.
Table 4. EU GMP Annex 1:2008 room classification table. Source: Particle Measuring Systems
EU GMP Grade |
At Rest |
In Operation |
Maximum number of particles permitted/m3 equal to or greater than the tabulated size |
0.5 μm |
5.0 μm |
0.5 μm |
5.0 μm |
A |
3520 |
20 |
3520 |
20 |
B |
3520 |
29 |
352,000 |
2900 |
C |
352,000 |
2,900 |
3,520,000 |
29,000 |
D |
3,520,000 |
29,000 |
Not Defined |
Not Defined |
It is important to note that the limits in the EU GMP table slightly differ from those in the ISO 14644 standard.
To complete the necessary certification, it is crucial to understand the principles of ISO 14644-1, the certification of cleanrooms according to that standard, the rules regarding the number of sample points, sample point locations, sample volume at each location, and the statistical analysis of cleanroom data that must be followed.
However, instead of using the classification limits provided in ISO 14644-1, it is recommended to use the Table displayed above, as specified in the revised guidance document.
The GMP also defines other expectations, such as a sample volume of 1 m3 per sample location for Grade A or the use of minimum sample tubing length due to the high precipitation of 5.0 µm particles in transport tubing (ideally, no sample tubing should be used).
Additionally, the recertification of cleanrooms should adhere to the guidelines in ISO 14644-2, with annual recertification for ISO Grade 6 and higher and semi-annual recertification for ISO Grade 5.
Exceptions are made for extending the recertification period for ISO Grade 5 areas if a continuous monitoring system has been implemented. Suitable times for certification include media fills or simulated filling runs.
Acknowledgments
Produced from materials originally authored by Mark Hallworth from Particle Measuring Systems.
References
- International Standards Organization. Cleanrooms and associated controlled environments — Part 1: Classification of air cleanliness by particle concentration, ISO Standard No. 14644-1:2015 (2015).
- European Commission. The Rules Governing Medicinal Products in the European Union Volume 4 EU Guidelines for Good Manufacturing Practice for Medicinal Products for Human and Veterinary Use: Annex 1, Manufacture of Sterile Medicinal Products, Annex 1 (2022).
- International Standards Organization. Cleanrooms and associated controlled environments — Part 2: Monitoring to provide evidence of cleanroom performance related to air cleanliness by particle concentration, ISO Standard No. 14644-2:2015 (2015).
- European Commission. EC Guide to Good Manufacturing Practice Revision to Annex 1: Manufacture of Sterile Medicinal Products, Annex 1 (2003).
- European Commission, EudraLex. The Rules Governing Medicinal Products in the European Union Volume 4 EU Guidelines for Good Manufacturing Practice for Medicinal Products for Hum
About Particle Measuring Systems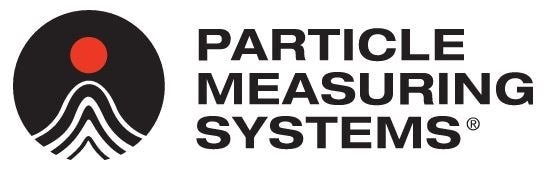
Particle Measuring Systems has 35 years experience designing, manufacturing, and servicing microcontamination monitoring instrumentation and software used for detecting particles in air, liquid, and gas stream as well as molecular contamination monitoring.
Specific applications include cleanroom monitoring, parenteral sampling, filter and in-line testing in deionized water and process chemicals, and point-of-use monitoring of inert gases and in-situ particle monitoring. Specialty monitoring includes parts cleanliness testing with a highly automated solution.
Particle measuring systems
Whether you want to protect product or meet industry requirements, such as ISO 14644, USP 797, or GMP, Particle Measuring Systems has a large variety of particle counters and molecular monitors to meet your needs. With 35 years experience, we have the proven reliability to support your application.
Particle counters
Protect your product with our reliable particle counters. We have airborne, portable, and liquid particle counters for a wide variety of applications including DI water, chemicals, and cleanroom monitoring. Compare particle counters or learn how to monitor your cleanroom or product by reading our papers.
Molecular contamination monitors
Molecular contamination creates costly problems to high value products, production processes, and equipment surfaces. We have solutions for both Airborne Molecular contamination (AMC) and Surface Molecular contamination (SMC). With parts-per-trillion limits of detection, real-time sampling, NIST traceable calibrations, and various data analysis packages, you can monitor in confidence.
Gas detectors
If you need gas detectors for process control or continuous emissions monitoring, we can help. Get real-time, reliable results with our ammonia, hydrogen fluoride, and chlorine detectors for worker protections, CEMs, and pollution monitoring.
Sponsored Content Policy: News-Medical.net publishes articles and related content that may be derived from sources where we have existing commercial relationships, provided such content adds value to the core editorial ethos of News-Medical.Net which is to educate and inform site visitors interested in medical research, science, medical devices and treatments.