To meet the requirements of regulatory agencies, pharmaceutical products are produced in a controlled setting. One example of such a controlled environment is a cleanroom, which is used to minimize the risk of contamination and the variability of the production environment.
As controlled environments, cleanrooms can be adjusted to adhere to specific standards. GMP regulations mandate strict monitoring to ensure continuous awareness of the current environmental conditions, encompassing both viable and nonviable contamination.
A cleanroom serves as the fundamental basis for controlling contamination. It is defined as a room in which the control of air filtration, air distribution, utilities, construction materials, and equipment is paramount.
Operational procedures are established and controlled to maintain airborne particle concentrations following appropriate particulate cleanliness classifications.
There are primarily two basic types of cleanrooms:
- Turbulent dilution of contamination
Cleanrooms with turbulent airflow use filtered air exchange to reduce contamination to an acceptable level. HEPA-filtered air is distributed through a central system via ceiling diffusion panels at a rate ranging from 10 to over 40 room volumes per hour (Air Exchange Rate).
This rate is influenced by the activities and the number of personnel in each area. A portion of the return air is recirculated, with some fresh air added for comfort.
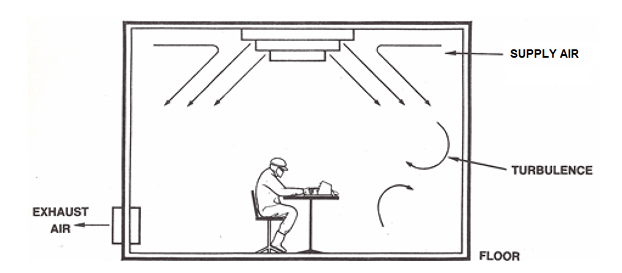
Figure 1. Turbulent dilution of contamination. Image Credit: Particle Measuring Systems
Unidirectional air cleanrooms utilize airflow velocity to create a barrier preventing external particles from potentially contaminating adjacent areas.
When processes or operators generate particles, the airflow is designed to direct these particles away from the critical zone, which can be confirmed through the smoke airflow visualization test. Flow rates typically range from 0.36 to 0.54 meters per second, but other airflow velocities can be employed.
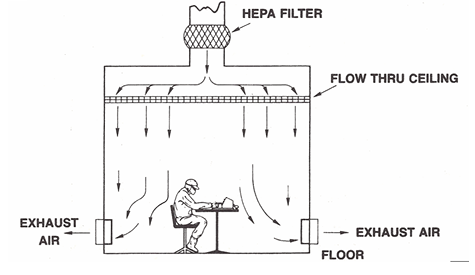
Figure 2. Unidirectional air wash. Image Credit: Particle Measuring Systems
Within the cleanroom, operations are typically conducted on HEPA-filtered workbenches, allowing for the manual handling of products, containers, and processing equipment.
The benches can have either horizontal or vertical flow directions. When the flow is horizontal, it moves directly toward the operator, effectively sweeping away any contaminants carried by the operator out of the critical zone. In vertical flow, the air descends over the process, maintaining a protective shroud around the critical areas.
Vertical flow also enables automation and enclosure of fill and finish equipment within a designated space. The filling machine can be accessed from above and utilizes the one-way airflow in the room to isolate the process from general room activities outside.
Access to the critical processing zone can be restricted using either fixed or flexible curtains. This provides a level of separation between the critical area and the general room environment, allowing operators to intervene when necessary.
Alternatively, a dedicated filter can be used to supply filtered air solely to the processing equipment. This approach allows for lower-grade air in background areas and increased separation between the critical and background areas.
This design can be extended and scaled up to establish restricted access barrier protection (RABS), where entry to the critical zone requires gloved access ports. Full isolation can be achieved through fully enclosed isolator systems, which also facilitate sanitation and sterilization processes.
The nature of activities and the choice of cleanroom will determine the necessary environmental monitoring. The more operators have access to a process, the higher the risk of contamination, as personnel are the primary source of airborne contaminants within a cleanroom.
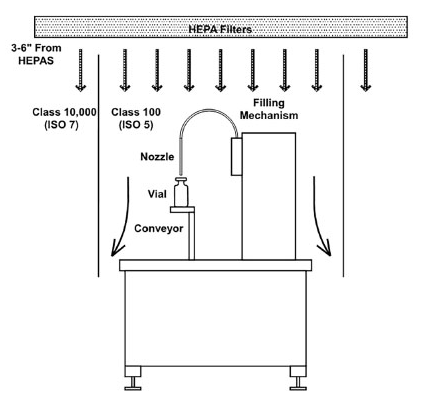

Figure 3. Filling mechanism diagrams. Image Credit: Particle Measuring Systems
Acknowledgments
Produced from materials originally authored by Mark Hallworth from Particle Measuring Systems.
About Particle Measuring Systems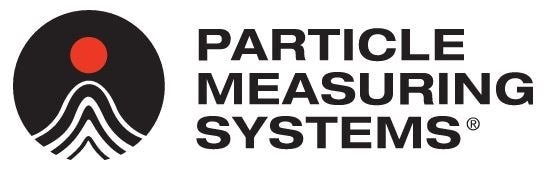
Particle Measuring Systems has 35 years experience designing, manufacturing, and servicing microcontamination monitoring instrumentation and software used for detecting particles in air, liquid, and gas stream as well as molecular contamination monitoring.
Specific applications include cleanroom monitoring, parenteral sampling, filter and in-line testing in deionized water and process chemicals, and point-of-use monitoring of inert gases and in-situ particle monitoring. Specialty monitoring includes parts cleanliness testing with a highly automated solution.
Particle measuring systems
Whether you want to protect product or meet industry requirements, such as ISO 14644, USP 797, or GMP, Particle Measuring Systems has a large variety of particle counters and molecular monitors to meet your needs. With 35 years experience, we have the proven reliability to support your application.
Particle counters
Protect your product with our reliable particle counters. We have airborne, portable, and liquid particle counters for a wide variety of applications including DI water, chemicals, and cleanroom monitoring. Compare particle counters or learn how to monitor your cleanroom or product by reading our papers.
Molecular contamination monitors
Molecular contamination creates costly problems to high value products, production processes, and equipment surfaces. We have solutions for both Airborne Molecular contamination (AMC) and Surface Molecular contamination (SMC). With parts-per-trillion limits of detection, real-time sampling, NIST traceable calibrations, and various data analysis packages, you can monitor in confidence.
Gas detectors
If you need gas detectors for process control or continuous emissions monitoring, we can help. Get real-time, reliable results with our ammonia, hydrogen fluoride, and chlorine detectors for worker protections, CEMs, and pollution monitoring.
Sponsored Content Policy: News-Medical.net publishes articles and related content that may be derived from sources where we have existing commercial relationships, provided such content adds value to the core editorial ethos of News-Medical.Net which is to educate and inform site visitors interested in medical research, science, medical devices and treatments.