French manufacturer, Bone 3D, has installed a Stratasys J750 3D Printer after identifying its full color, multi-material attributes as the solution to strengthen its capabilities and quickly produce highly precise medical and orthodontic models for its customers.
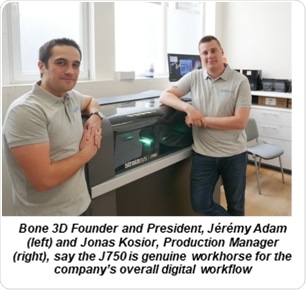
We needed a reliable multi-material 3D printing technology to produce ultra-accurate surgical guides and simulators, and we’ve found exactly that accuracy in the Stratasys J750. Since its installation, it has quite literally transformed what we’re able to achieve and the speed with which we can do it; the J750 is now the tip-end of the spear for our business – both insofar as production of highly-realistic models, and R&D development.”
Jérémy Adam, Founder and President of the Paris-based start-up
Highly accurate models produced within just four hours
According to Adam, the J750 has proven itself to be a genuine workhorse for Bone 3D’s overall digital workflow – both from a production standpoint, as well as in R&D development. “Having access to this technology on site has enabled us to significantly speed up processes when it comes to the design and development of medical models,” he continues. “As an example, something designed at 2pm can be produced and tested within just four hours, which is amazing.”
Bone 3D purchased the J750 through Stratasys’ French partner, CADvision, and currently uses it in two key application areas. Firstly, the creation of patient-specific surgical guides that help surgeons better plan operations and to perform more precise surgery, and secondly as surgical simulators on which medical practitioners train in order to authentically replicate the actual surgery.
In each instance, the company currently leverages the versatility of six different material solutions from two Stratasys PolyJet material families to meet its needs. The vivid appearance and dimensional stability of the Vero range enables the team to reproduce lifelike anatomical structures; while the high-tensile strength of the rubber-like Agilus materials ensures that the mechanical properties are faithfully matched.
For the Bone 3D team, the level of dimensional stability offered by each material was something with which they were particularly impressed and was one of the factors that influenced the decision to invest in the J750.
We were pleasantly surprised by the way in which printed models were able to faithfully maintain dimensional stability. They print with only negligible levels of deformation to enable fast production of reliable and leak-free injection molds.”
Jérémy Adam
Supporting the future of medicine
As well as allowing today’s surgeons to work more effectively, Adam believes that, from a training perspective, the J750 could hold the key to enabling more advanced and realistic methods to teach surgeons of tomorrow. This, he thinks, could eventually see less use of cadavers within student training, with 3D printing instead presenting opportunities to simulate challenging scenarios to test trainees more effectively.
In the meantime, Adam has ambitious business objectives with the J750 and envisages a scaling of production in due course. “Our aim is to fine-tune the design of our simulators before making them commercially available throughout France. The Stratasys technology that we now have at our disposal gives me the confidence that we will achieve this goal,” he concludes.