Hosokawa Micron Ltd was approached by a major pharmaceutical products manufacturer wanting a customized, multi-purpose dispensary weigh booth to be developed. The aim was to increase capacity at their Centre of Excellence for tablet manufacturing and packaging, situated in the north of England.
The manufacturer needed a GMP design dispensary downflow booth that would support the dispensing, weighing, de-lumping and material handling of Level III active pharmaceutical compounds (APIs) using containment systems that would ensure operators are protected from dangerous airborne particles.
The Solution
Working closely with the customer, engineers at Hosokawa Micron decided what the best system design would be to provide an ergonomic solution that was able to offer operator safety at operator exposure levels (OELs) of less than 10µm/m3 time weighted average for a period of 8h, across a range of manual and semi-automated powder handling processes.
Before customer sign off, a wooden model of the booth and integrated equipment was created to ensure the most effective and ergonomic design of the downflow booth. The final design is highly flexible, offering the ability to handle a range of drum sizes, semi-automated and manual handling processes, as well as a screen for operator protection.
Situated on a mezzanine floor, the downflow booth is equipped with drum lifting equipment, two drum tipping stations, equipment for de-lumping products and drum charging and gravity feed chutes to lower level IBC stations (Figure 1).
Considering the space constraints, Hosokawa Micron have designed the downflow booth to fit into an existing building footprint, while overcoming design and integration challenges and meeting throughput demand.
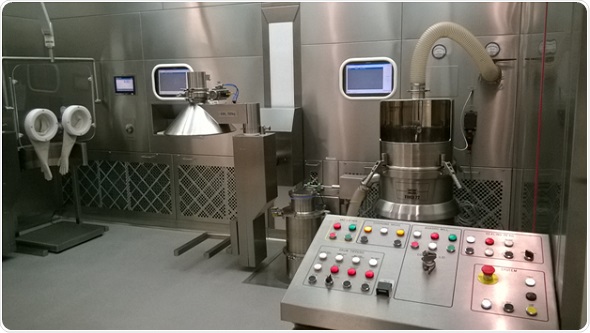
Figure 1. Multi-functional dispensary booth
Hosokawa Micron’s Carl Emsley commented that the company’s engineers developed an integrated, ergonomic design solution by working closely with the customer to ensure their requirements are met. The system provides an improved working environment for personnel, as well as meeting the demand for increased capacity and streamlined product throughput.
Emsley added that equipment from a number of major OEMs has been brought together to meet the demand for a user-friendly, integrated facility for the handling of active pharmaceutical ingredients.
Key Components of the Multi-functional Dispensary Booth
Material filled drums enter the open front design Downflow Booth, where vertical downflow of air reduces the rise of dust in the breathing zone of the operator, which may occur as a result of opening drums or drum tip and sampling processes.
Two separate drum tipping stations are present in the downflow booth. A pneumatic hoist is used to load the drums into the drum tippers. Following de-lidding, the drums are elevated to 180° by the drum tippers. Then, the product can either be dispensed into a receiving drum or operators can dispense manually from the drum at the 90° rotated position.
During dispensing from the downflow booth to an IBC located on the facility’s ground floor, the drum is inverted and docked before gravity discharge down a vertical transfer chute. The chute passes through the floor and is equipped with a Stott hygienic, inflatable, downward sealing head that seals against the IBC’s top opening.
This reduces the operator’s exposure to dust during the filling process. The downward sealing head features an LEV extraction collar for dust removal once the seal is deflated. (Figure 2).
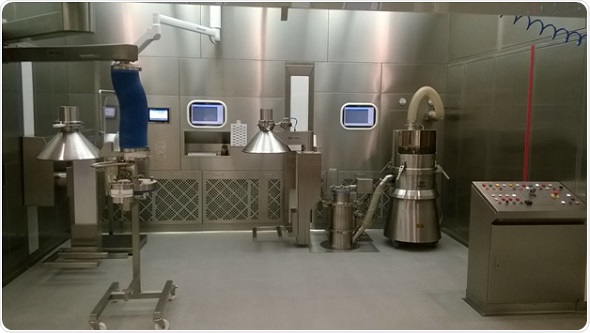
Figure 2. Another view of the downflow booth and integrated equipment
Emsley explained that the system also features a secondary level of barrier containment and is equipped with a 5D containment screen, located on an articulated arm. This provides a physical barrier between the operator’s breathing zone and airborne dusts, thereby reducing operator exposure levels and the potential risks associated with API contact.
The positioning of the containment screen in the booth and its range of movement provides additional operator safety at either tipping station and provides access to all areas of the downflow booth, Emsley added.
The downflow booth is also equipped with a milling station so that product de-lumping can be achieved before further sampling, subdivision or IBC loading. The drums are completely inverted by the drum tippers to dock onto the mill to create a dust seal that reduces airborne dust.
From a single console, all operations and automated equipment can be fully operated. A cooling package integrated into the downflow booth provides an operator-friendly environment by maintaining the booth temperature at 21±2°C.
Conclusion
During commissioning, full onsite OEL testing was completed by Hosokawa Micron to ensure that all customer requirements were met by the final installation and to enable all standard operating procedures and operational protocols to be confirmed002E
About Hosokawa Micron Corporation

Hosokawa Micron Corporation was established in 1916 as Hosokawa Iron Works in Osaka, Japan. Today, Hosokawa Micron Group is a world leader in providing process solutions in the fields of powder and particle processing technology, blown film technology, and confectionery technology.
Hosokawa Micron Group maintains facilities for research, engineering, manufacturing and service throughout Asia/Oceania, the Americas and Europe. Hosokawa Micron is advancing 100 years of powder and particle technology experience and market leadership in the future with the application, development and commercialization of ultra fine composite particles in the rapidly expanding field of Nano Particle Technology.
Sponsored Content Policy: News-Medical.net publishes articles and related content that may be derived from sources where we have existing commercial relationships, provided such content adds value to the core editorial ethos of News-Medical.Net which is to educate and inform site visitors interested in medical research, science, medical devices and treatments.