As the demand for more effective drugs increases, so does the potency of the drugs being developed. Safeguarding and protecting both products and the operators is vital, as is taking into consideration the need to ensure maximum flexibility in the design of systems for processing highly potent active pharmaceutical ingredients (HAPI).
Recently, a major pharmaceutical manufacturer has approached Hosokawa Micron Ltd wanting to develop an R&D batch milling and pack off system for processing of HAPI materials of a specific particle size. The system needed to meet the manufacturer’s stringent production demands and operator safety requirements.
Space constraint issues at the existing facility further complicated system design, as did the need to create the most ergonomic working environment for all operators across multi-shift operations.
Hosokawa Micron’s Solution
Engineers at Hosokawa Micron are experts in the supply and planning of contained processes for the manufacture of high-value, high-potency products. They developed a two-storey contained system that fulfilled all of the customer’s needs and enabled significant production flexibility, from the processing of small R&D batches, to operation as a continuous production unit.
Working closely with the end user’s engineering team and following substantial on site ergonomic evaluation in consultation with multiple shift operators, Hosokawa Micron engineers achieved the optimum design. The resulting system delivers maximal flexibility, offering a range of particle size and shape production along with a range of weighing and filling options. The system fulfills all of the customer’s requirements and generates genuine involvement from manufacturing personnel.
The integrated batch milling and packing system (Figure 1) is equipped with an upper tier, high containment isolator featuring an in-built pharmaceutical hammer mill. A lower tier laminar flow booth contains a flexible, continuous liner, filling and weighing system and HMI containment screens. The system is capable of handling batch volumes of up to 500L from the dryer positioned above and offers containment to Level 4 OEB, which will achieve containment repeatedly between 1 and 10µg/m3.
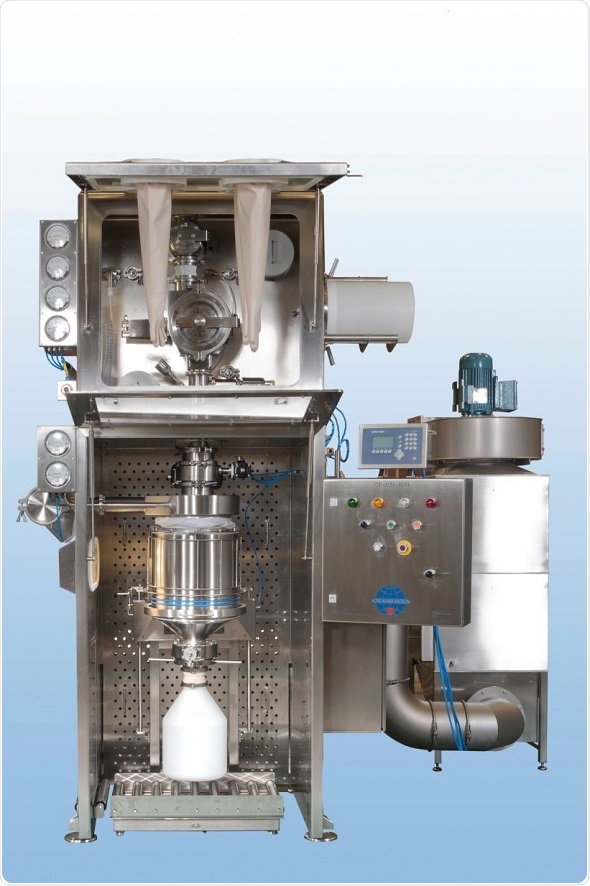
Figure 1. The R&D batch milling and pack off system
The system can be used in a hazardous area and has been designed to comply with hazardous area classification of Zone 1 and 21 IIB T4. Operation of the system under an inert atmosphere is possible by purging all areas inside the system with nitrogen, thus providing the option of handling hygroscopic or explosive products, for example.
Milling Process
A fully contained environment is provided by the milling isolator during active product handling, thereby offering complete barrier isolation. The isolator is integrated into an existing product flow from a dryer located above the unit. The dryer feeds HAPI material into the pharmaceutical hammer mill at a controlled rate using hygienic rotary valves (Figure 2). The hammer mill can run at speeds of up to 6000rpm, depending on the particle size required.
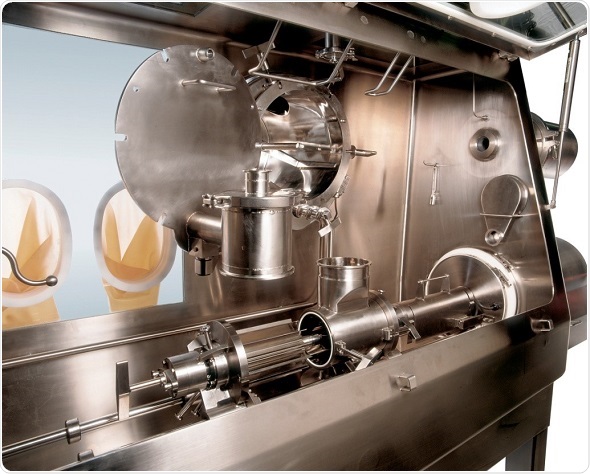
Figure 2. The HAPI material is fed from the dryer through hygienic rotary valves at a controlled rate into the pharmaceutical hammer mill.
Different particle sizes and shapes can be achieved with a series of interchangeable meshes in the system, providing additional operational flexibility. Dismantling the mill for mesh changing and cleaning is simple. Hosokawa Micron has specifically designed the mill for isolator integration. All components can easily be removed and in most cases, the operator does not need to handle and lift large, heavy components. All motors are kept within the technical area to the rear and not in the processing area.
A wide range of particle sizes is delivered by the pharmaceutical hammer mill, normally below 50µm, with small amounts of ultrafines. At the hammer mill, temperature monitoring maintains the material within temperature tolerances and prevents product degradation. Using a 270 RTP, it is possible to perform contained sampling from the milling isolator, thus enabling QC end-product tests such as particle size measurements, to ensure the product is maintained within specification.
Filling and Weighing Process
The filling and weighing system is housed within a laminar flow booth located directly beneath the milling isolator, enabling direct material discharge to the filling packing head and maintaining the benefits of the small, compact footprint within space limitations.
Once milled, material is gravity fed into continuous liner, single liners or 23L charge bottles situated on the fill/weigh platform via a 100mm charge point valve, to provide low containment product transfer.
A containment screen positioned at the compact inward sealer provides further barrier protection from the potential risk of airborne particles inside the laminar flow booth, by increasing the laminar flow booth face velocity throughout the actual pack off process.
Material handling and operator intervention are minimized, owing to the design of the system’s internal composition. The fully WIP system features integrated spray guns, which are placed in such a way that efficient clean down is ensured.
A freestanding extraction fan complete with safe change filter housing with double H14 HEPA filtration is incorporated into the system, providing further operational safety and reducing the risk of contamination in the surrounding working environment.
Conclusion
Working together with the customer, Hosokawa Micron developed standard operating principles to help meet the customer’s requirement for repeatable containment and OELs designed to ensure both product and operator safety.
About Hosokawa Micron Corporation

Hosokawa Micron Corporation was established in 1916 as Hosokawa Iron Works in Osaka, Japan. Today, Hosokawa Micron Group is a world leader in providing process solutions in the fields of powder and particle processing technology, blown film technology, and confectionery technology.
Hosokawa Micron Group maintains facilities for research, engineering, manufacturing and service throughout Asia/Oceania, the Americas and Europe. Hosokawa Micron is advancing 100 years of powder and particle technology experience and market leadership in the future with the application, development and commercialization of ultra fine composite particles in the rapidly expanding field of Nano Particle Technology.
Sponsored Content Policy: News-Medical.net publishes articles and related content that may be derived from sources where we have existing commercial relationships, provided such content adds value to the core editorial ethos of News-Medical.Net which is to educate and inform site visitors interested in medical research, science, medical devices and treatments.