Accelerated clinical development programs for breakthrough therapy products will lessen the time available to optimize phase III and commercial manufacturing processes. This will require priority given to development efforts on process reliability over yield and cost of goods. Consequently, process and formulation optimization might require deferral to post-approval; if it can be determined, there is no effect on the safety of patients or product availability.
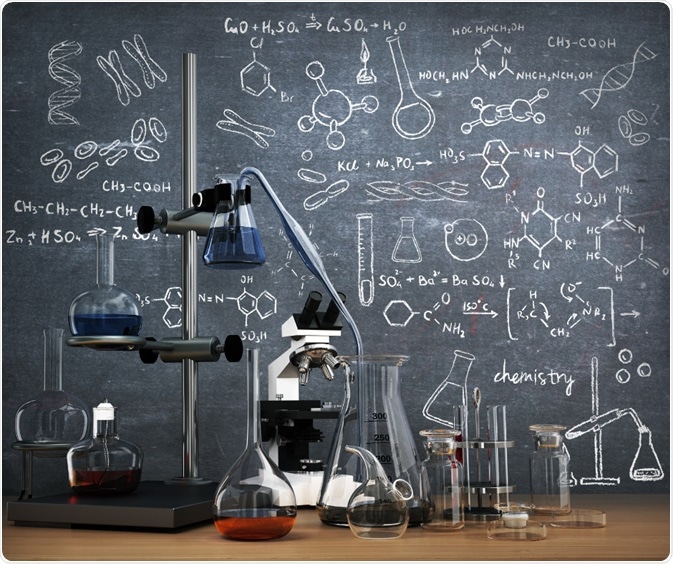
Image Credit: DS InPharmatics
Accelerating products to market
A number of activities that might be seen to accelerate development activities are:
- Introducing commercial processes with limited experience, but adequate data to guarantee that the process can dependably yield a drug to meet the expected quality of safety and efficacy profile and enhance post-approval
- Utilizing data from development material or the clinical supplies, with acceptable comparability data to support material from preliminary commercial process lots, might be required
- The consideration of deferring intermediate hold time research and as an alternative completing straight through processing and scheduling of intermediates to accelerate process development
- Lock the phase l/ll drug product formulation and optimize post-approval to prevent the requirement for bioequivalence research
- If efficacy is indicated in phase I clinical studies, in oncology patients, sponsors might decide to strive for a commercial dosage form to be utilized in the pivotal phase II clinical program
- For biologic products, complete early optimization of cell line development and carry through phase III and commercial production
- For small molecule products, concentrate on the active pharmaceutical ingredient (API) and excipient qualities influencing formulation and DP manufacturability and performance
- Consider close alignment on linkages in control strategies, for example, particle size distribution impact on dissolution for small molecule drugs, and predominant themes that might apply to both biologics and small molecule drugs, such as moisture sensitive API.
Formulation and manufacturing process of small molecules
In the last 10 years, there has been significant development in computer simulation of pharmaceutical materials, processes and product performance. Gradually, more mechanistically based models are being developed, providing a stable basis for describing 'prior knowledge' of the behavior of the systems being described.
The increase in available models offers a unique opportunity to implement a systems-based approach to formulation and process design associated with pharmaceutical product quality and performance.
In particular, in an accelerated development paradigm, in-silico tools can be used for formulation and process selection with the associated mechanistic understanding of in-vitro and in-vivo performance, including the effect of product stability.
In several cases, these models can be created or calibrated utilizing specific experimental measurements of physical properties or one to a few carefully designed experiments, instead of relying on a completely empirical understanding determined by detailed experimental design methodologies.
It is essential to identify that the knowledge gained previously that comes with utilization of models enables increased product and process understanding to be gained from experimental calibration and validation, instead of experimental mapping or interpolation.
This will also result in improved process establishment with decreased experimental packages, accelerating clinical supply and ultimately commercial supply. Additionally, the effect of unseen future variations, for instance, raw materials, can be predicted and assessed using models, thus enhancing future process capability and security of supply for patients.
Continuous manufacturing: Small molecules and large molecules
Traditional batch processes for the production of both drug substance and drug product are being supplemented with continuous processing approaches. Employing continuous processes enables innovative approaches of drug substance production to be utilized. For instance, the use of largely selective reactions or otherwise hazardous materials. The nature of the equipment makes it possible to quickly develop the production process, for instance, to optimize reaction conditions and to evaluate critical manufacturing parameters.
After development, the scale up of continuous processes is somewhat easier to predict compared to batch processes. Consequently, the quality of material produced at laboratory scale has a higher likelihood to be suggestive of the quality produced at commercial scale manufacture.
It also provides advantages for supply chain for products where the predicted volumes of drug substance and drug product are uncertain, for example, it is easier to stop and start continuous processes in comparison to batch processes. This methodology is also amenable to innovative analytical approaches like in-line process monitoring which can be utilized for continuous process verification.
About DS InPharmatics 
DS InPharmatics (DSI) provides regulatory, technical, and project management consulting services to healthcare product companies that manufacture and/or market pharmaceuticals, biopharmaceuticals, and cellular and gene therapy products.
Since 2007 we have provided our clients with innovative strategies and exceptional quality work products intended to enhance product development, approval, and marketing presence. Whether advocating CMC strategy, directing CMC operations or developing CMC submission content that represent the best interests of emerging biotech, we focus on the critical CMC issues and build programs that enhance development.
In April 2021 we were thrilled to announce that DSI has just become part of ProductLife Group.
French-headquartered ProductLife Group (PLG) is well-known in the Life Sciences market. It has a track record of successfully managing global outsourcing programs and insourcing services for its international client base. The company is on a mission to help transform human health outcomes by optimizing regulatory affairs, safety & vigilance, and quality compliance for life sciences organizations worldwide.
The fit between our two organizations could not be more perfect. We will complement PLG's growing biotech services portfolio. US biotech sponsors recognize DSI as a leader in consulting for go-to-market strategies and RA pre-market consulting. At the same time, PLG has a strong reputation for managing end-to-end outsourcing of regulatory affairs and pharmacovigilance activities worldwide.
Our merger with PLG will harness our combined strengths, offering our clients on both sides of the Atlantic support with their developed drugs approvals and post-approvals compliance, plus advisory services on the best market strategies to deliver a rapid ROI on their development. Together we will offer our clients increased pharmacovigilance capabilities - including a QPPV; pharmacovigilance consulting; and a fully validated safety database - as well as complementary toxicology-related services; RIM/electronic document management services; and support for medical device regulatory requirements.
We see enormous potential in this new chapter for DSI and you, our clients. As a PLG company, we have the opportunity to become part of a global force in life sciences regulatory and compliance solutions and services, and we're incredibly excited to add our momentum to that effort.
Sponsored Content Policy: News-Medical.net publishes articles and related content that may be derived from sources where we have existing commercial relationships, provided such content adds value to the core editorial ethos of News-Medical.Net which is to educate and inform site visitors interested in medical research, science, medical devices and treatments.