Everyone is keen to find out where to find the best Philly cheesesteak, both in terms of what goes into it and where it is made. There is no definitive answer to these questions, however, because there is no secret or perfect recipe – in the same way that no two drug development programs will progress in the same way. The debate around the what, how, where and when will never be truly settled because these things are very much down to individual preference.
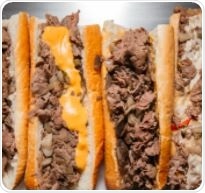
Image Credit: DS InPharmatics
Much like achieving the ideal Philly cheesesteak, when developing a pharmaceutical or biologic specific process and related finished product, product specifications and characteristics must be clearly defined in order to ensure product safety, effectiveness and consistency. These activities are commonly referred to as CMC, or Chemistry, Manufacturing and Control.
No two drug development programs develop in the same fashion, but every stage of the drug development life cycle will involve CMC. Throughout pre-clinical drug development, proper analytical methods must be qualified and validated to ensure that the product is consistent with expectations.
Stability testing will be conducted, with the product’s physicochemical properties being determined, and raw materials chosen then tested. As development progresses into the clinical stage, further characterization of the drug product is required.
As clinical trials continue, any scaled-up process must make sure that larger batches are identical, meeting exactly the same specifications as the drug tested in previous trials. Once the manufacturing process has been qualified, lot release and in process testing must continue.
A good drug development program (and indeed a good Philly cheesesteak) provides sufficient assurance that any compound involved will meet the required quality and technical elements at each stage of development, ultimately facilitating effective commercialization of the drug.
Like drug development programs, Philly cheesesteaks are best when made based on the customer’s requirements. Some people prefer the rolls toasted and crispy while others like them soft and chewy. Some prefer their cheesesteak dripping with grease, while others will say that too much grease results in a soggy roll. While some customers prefer the meat diced thinly, others enjoy larger slices or even small chunks.
Like the management of CMC Regulatory Affairs activities throughout development of the requirements to achieve a drug product’s preparation, there is no secret or perfect recipe.
It is important to learn the facts around a great cheesesteak’s key ingredients. Once these are understood, there is a wide range of great cheesesteak ‘manufacturers’ that can be explored in order to properly decide on a personal favorite. Likewise, with CMC Regulatory Affairs activities during development, there are a number of approaches which can be taken to help improve the chances of success.
The roll, much like the general properties of a drug substance, and the composition and excipients of its dosage form
Every great cheesesteak begins with the right roll. It should be chewy, but not too tough or too airy. Above all though, the roll should have some chew. Potato rolls may be right for lobster salad or hot dogs, but they are not a good choice for a cheesesteak.
Like a good cheesesteak roll, the physical and chemical properties of a drug substance, including the active ingredient within the drug product, must be fully explored and understood in order to develop an appropriate formulation.
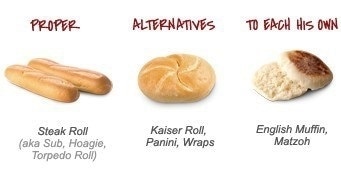
Image Credit: DS InPharmatics
For example, the rationalization of the choice between salt or free acid/base should be properly investigated in order to ensure the drug substance’s quality and that the drug product can be properly formulated.
The purity profile for various lots should be analyzed, with reversed phase High Performance Liquid Chromatography (HPLC) generally being employed for this analysis. The purity profile should be reproducible, with any impurities at International Conference of Harmonization (ICH) thresholds being appropriately identified, qualified and reported.
Examining the drug substance’s solution stability in different solvents at an early stage can offer an indication of the tendency for the drug substance to degrade during wet processing steps or when used in liquid formulations. Physical properties like hygroscopicity, solid-state stability, hydrate/solvate formation, polymorphism, and powder characteristics must also be analyzed.
A formulation’s drug product components will be categorized according to their function, as well as by the product’s route of administration. An outline of the drug product’s qualitative/quantitative composition will provide a full list of ingredients, including any solvents used in its manufacture.
The functional qualities of each individual component (excipients) of the drug product are vital to the development rationalization of the formulation. These components serve as important reference points in the analysis of supportive development data.
The functional aspects of excipients can be effectively split into four core categories, based on the way in which they may impact the drug substance’s stability, in vivo absorption, physical characteristics, and manufacturability.
While it is possible to apply these general classifications in most cases, excipients can also perform multifunctional roles. This means that the degree of the excipient’s physical characterization reliant on the manufacturer completely understanding its function.
A dosage form needs justification, and likewise, the ideal roll on a Philly cheesesteak should be uniform, long and slender, while not being skinny. The ends must be rounded - not pointy – shaped like the wider side of an egg, allowing the steak to fill the roll evenly and ensuring that every bite yields an equal meat to bread ratio.
The meat, much like the manufacturing process and process controls during clinical development
The meat found within a Philly cheesesteak should comfortably fill the roll, similar to the allowable excess volume and labeled vial fill size in an injectable drug, or like content uniformity for an oral form.
Having an inch of roll with no meat present is considered to be a definite no. Beef is the standard meat component, but chicken cheesesteak (which is only slightly healthier than its beef counterpart) is also popular. While both are delicious, first-timers are recommended to try the beef initially.
Meanwhile, a detailed narrative description of each step in the manufacturing process of both the drug substance and drug product can usually be found within early phase regulatory documents. This narrative will be compared against batch records from the manufacturing facility itself.
A comprehensive analysis of the process will incorporate a review of the required quantities of solvents, catalysts, raw materials and reagents. It will also include an identification of essential steps and process controls, the size and type of processing equipment, as well as key operating conditions such as pressure, temperature, pH, and the final drug product’s mixing time.
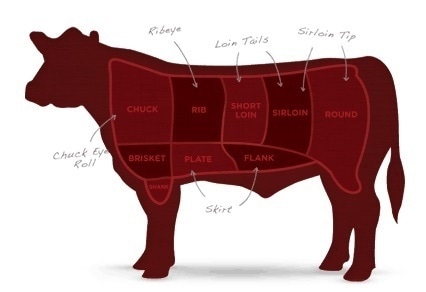
Image Credit: DS InPharmatics
In cases where the process has been scaled-up from previous batches which had been used in toxicological studies, the impurity profile will be investigated and compared with the previous toxicology batches.
Investigation of raw materials will include the availability of reagents and important safety concerns, such as any specialized processing equipment required, handling concerns or protective equipment needed by the operator.
Following characterization of the drug substance, excipients, their interaction potential and the manufacturing process development for the drug product may begin. Process development commences at a small scale, transitioning to a minimum of 10 % before full scale production is made and the process is validated.
Process development should emphasize reproducibility of critical quality attributes (CQAs). Alterations to the manufacturing method must be detailed as the process progresses from initial Phase 1 studies to the final commercial process.
Here, the focus will be on process changes which were made after the initial clinical study. A review will be compiled of all clinical studies, with the manufacturing process utilized for clinical supplies thoroughly documented.
Development studies must thoroughly document the impact of process changes on CQAs associated with both intermediates and the final drug product.
When working with sterile products, a review of the pre-sterilization bioburden data must be conducted, as this is vital in demonstrating that the process is sufficiently robust.
When working with nonsterile liquid products, however, a review of the microbial limits testing data must be conducted. For any components in contact with liquid products during the manufacturing process, compatibility data must confirm that there are no deleterious effects to the product quality (for example drug adsorption onto processing tubing or filters) or unacceptable extractable components.
Whether the drug product is a lyo product manufactured through a complicated, multistep process or a tablet manufactured via a basic direct compression process, knowledge and effective control of critical process parameters are cornerstones of a well-controlled and robust process.
With direct compression tablets, flow behavior of the formulation before tableting is a crucial characteristic that will affect the selection and control of ranges of process parameters.
A number of parameters are important in the direct compression process. These could include order of addition of excipients, mixing or blending time, and flow rates of the blend into the tableting press. Water absorption by powder during manufacturing may require the use of specialist humidity controls within the manufacturing facility.
With a lyo product, parameters that control the lyophilization must be well-defined. These include the impact of any deviation from set points for critical operations. Overall, the design process should only be considered to be successful with predefined quality requirements and a thoroughly developed testing plan.
Like the Philly cheesesteak, there are numerous options for each dosage form. Cheesesteak options include various cuts, naturally flavored, unseasoned products, single cut, hand-packed. seasoned, fully cooked, blended seasoned and, of course, chicken. Like with dosage forms, specifications are important.
The cheese, much like the specs, analytical procedures and validation
Some people enjoy the bright yellow (artificial) Cheez Whiz, but the majority of locals will opt for provolone or American cheese. While Cheez Whiz may provide taste satisfaction after a late night, American cheese is always a better option, because, when properly thought about, most people realize that Cheez Whiz is unpleasant and not a good food choice.
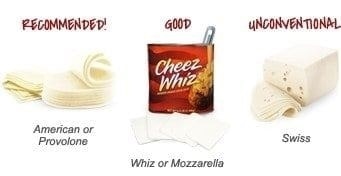
Image Credit: DS InPharmatics
Other types of cheese - like Swiss, for example - are not only inappropriate for a Philly cheesesteak, but will likely cause anyone ordering them to be mocked if overheard doing so in public. Provolone and American are the two traditional cheeses, and these are the only options that should be considered. However, the type of cheese used should complement the steak’s flavor.
Similarly, specifications for drug substance or drug product will be comprised of test methods and their acceptance criteria. These should be chosen based on the nature of the product itself, for example, solid oral, biologic, small molecule or liquid parenteral. Each product specification should be provided along with a rationale for its specified limits.
A range of tests and acceptance criteria exist which are applicable to all drug substances.
A description or qualitative statement is normally made regarding the drug substance’s appearance. Identification testing will normally distinguish between the drug substance and any closely related compounds.
Normally, two identification tests will be performed, with one of these tests being the HPLC retention time match with a reference standard material. The second test will generally be a spectroscopic technique such as IR, however, UV-Vis absorbance spectra are not usually specific enough to differentiate between related compounds.
HPLC methods are generally employed in the control of impurities, and all methods should be specific while indicating stability.
Further specifications may be applicable, based on the drug substance and drug product’s natures. These additional specifications may include polymorphic form, particle size, melting point, loss on drying and Karl Fischer.
When working with drug substances which are used in solutions and suspensions, additional physico-chemical characteristics could affect the formulation of the drug product. These characteristics may include microbial limits or the pH of the solution, and these specifications must be consistent with drug safety study results and existing process capability.
Specifications of impurities during early development will be primarily controlled via the qualification limits established by toxicology studies. In the early stages of development, full justification of specifications will not be available, but this is unnecessary at this stage as final specifications are defined through the complete development experience.
By the time Phase III is reached, the drug substance process should be well-defined with no significant changes anticipated. This is because Phase III pivotal clinical studies and stability batches will utilize material from the current process.
Once again, two identification tests will be performed, with one of the tests being the HPLC retention time match, using a reference standard material. Again, the second test will usually be a spectroscopic technique such as IR.
The most commonly used assay procedures are HPLC and titration methods. If a titration method is employed for assay, a further, specific, stability indicating method must be applied in order to manage impurities in the drug product.
Much like the drug substance, additional specifications may be applicable, dependent upon the nature of the specific drug product. These specifications may include dissolution, disintegration, residual solvents, moisture (water) and microbial limits.
When working with drug product solutions and suspensions, further physico-chemical characteristics of the drug product may affect its performance. These characteristics can include the particle size of the suspended drug, the pH of the solution, the clarity of the solution (turbidity), the color of the solution, or its viscosity, preservative testing or volume of fill.
There is a common misconception from people who do not live in the Philly area is that a genuine Philly cheesesteak should be heavily covered with Cheez Whiz, but this is simply not true. Sliced white American followed by sliced provolone are the most requested types of cheese on cheesesteaks, and this is the case throughout Philly and even the rest of the country.
It is important that the cheese is not overwhelming in terms of salt or sharpness. When selecting a white American, would-be cheesesteak consumers should look for specifications which impart a creamy taste. For provolone, however, they should opt for a mild or medium profile, along with a light smoky flavor.
The onions, much like the reference standards, container closure and product stability
Unless someone is seriously averse to fried onions, then these should be added to a cheesesteak to improve it. Sweet or hot peppers are also popular additions, but other than these, anything else is considered somewhat ‘fancy’.
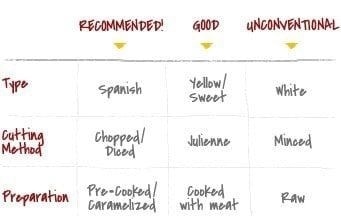
Image Credit: DS InPharmatics
Some people like to add pizza sauce, creating a pizza steak, while some add lettuce, tomato, onion, and mayo, resulting in a cheesesteak hoagie. While every one of these variations is delicious, anyone new to the world of cheesesteaks is advised to keep it simple and opt for the classic - a beef cheesesteak complete with American cheese and fried onions - at least for their first time.
Throughout drug development, the validity of analytical results is partially reliant on the use of appropriate reference standards. Reference standards utilized in the drug substance analysis, or the analysis of starting materials, intermediates and drug product must employ further testing in order to confirm both the identity and purity of the reference standard itself.
Normally, the reference standard is fully characterized, and this will include full structural data alongside comprehensive testing for impurities. Once the reference standard has been fully characterized, a secondary reference standard can be tested against the primary standard to facilitate routine testing.
A primary package from storage should be available, and the potential for incompatibilities between the package and compound should be explored and understood. Physical and chemical reactivity will generally dictate the type of packaging required.
For example, hygroscopic drug substances may necessitate the inclusion of desiccants in the primary package. If drug substances are sensitive to environmental conditions such as light, oxygen, heat and moisture, data on the packaging component’s qualification should be provided.
Following identification of critical packaging parameters, these parameters will be routinely tested upon receipt of the container, before it is used to hold the drug substance.
Additionally, an appropriate package should be selected based on knowledge of the chemical and physical behavior of the drug product in pre-formulation, along with subsequent stability studies of model formulations.
For stable products which are not sensitive to environmental conditions, the justification of the package will still require enough data to illustrate the acceptability of the drug product’s physico-chemical attributes when stored.
For products that are sensitive to moisture or oxygen, a package must be shown to provide an effective barrier. It may also be necessary to use headspace analysis to show that packaging conditions offer an appropriate internal atmosphere, or that this can be achieved via the addition of a suitable inert gas.
The choice of packaging components for liquid formulations is ascertained during pre-formulation development.
A secondary package for the drug product may also be required, such as a cardboard box. If this secondary packaging material is designed to provide protection to the product, then stability studies both with and without this secondary package should demonstrate the secondary package’s suitability for this role.
Development of a robust stability protocol early on in development is advisable. A review of every stability batch should be conducted once the product is considered stable, with special attention paid to any increases in impurities or the appearance of a new degradation product. Variability observed between batches in the level of degradation products is often indicative of the overall process robustness.
New impurities or alterations in impurity levels are often observed in poorly controlled processes. As such, the degradation pathway and any critical intermediates should be thoroughly explored.
Like stability, many would say that onions are essential in a good cheesesteak. Overall though, onions are an ‘add-on’ - but not just any – ‘add-on’ – it is the most significant addition for those who prefer the extra flavor of “with” or “wit”. Nothing is ever straightforward, though, and even when considering onions for a cheesesteak there are three key decisions to be made: Type, cutting method and preparation.
The location, much like the supply chain
With a firm grasp of the complexities of the development and ordering process for a Philadelphia cheesesteak, now is a good time to go and order one. Luckily, it is easy to source quality Philly cheesesteaks around the city – there are shops all over. Regardless of whether it is an individual’s first cheesesteak or their 100th, each bite should be savored.
Much like a cheesesteak shop, a contract manufacturing organization (CMO), sometimes referred to as a contract development and manufacturing organization (CDMO), is a company which can be contracted by other companies in the industry to deliver comprehensive services ranging from drug development through to drug manufacturing.
Hiring an external organization allows large pharmaceutical companies to outsource these roles, assisting with scalability or allowing the large company to fully focus on drug discovery and drug marketing.
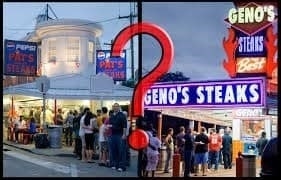
Image Credit: DS InPharmatics
CMOs can offer a wide range of services. These can include pre-formulation, formulation development, method development, stability studies, pre-clinical and Phase I clinical trial materials, formal stability, late-stage clinical trial materials, registration batches, scale-up and commercial production.
CMOs are commonly contract manufacturers, but they can provide many other services because of their development aspect.
Customers not only expect competitive pricing, but also flexible production capability, regulatory compliance and on time delivery. The CMO must comply with its client’s existing manufacturing practices, as well as best practice from an official organization such as Food and Drug Administration (FDA).
The location, name, and current Good Manufacturing Practice (cGMP) status of the CMO of core starting materials and drug substances should, ideally, be available. Furthermore, an overview of the manufacturer’s quality assurance aspects can provide insight additional insight into the viability of the process.
A manufacturer can request a report of the most recent cGMP manufacturing inspection from the United States Food and Drug Administration (FDA) or related European Union (EU) authority, facilitating a general overview of the facilities’ cGMP compliance aspects.
Specific indications of issues around testing practices or cGMP compliance can assist in ascertaining the reliability of data supplied by the manufacturer. Should testing be performed at a different facility, an investigation into that testing facility’s cGMP status should be undertaken.
While somewhat more complicated, once someone learns about the key ingredients required for a quality Philly cheesesteak, there is a wide selection of great cheesesteak locations to explore while deciding on a personal favorite. First though, reading up on Finding a Great Philly Cheesesteak! is worthwhile, in order to make the ordering process as smooth as possible.
Design Space Inpharmatics want to help their customers find some of the best cheesesteaks in Philadelphia. In the City of Brotherly Love, cheesesteaks remain a civic icon, a cultural obsession and a strong draw for visitors. They are often imitated across the globe, but the Philly cheesesteak is rarely successfully replicated outside of Philadelphia.
Acknowledgments
Produced from content originally authored by Edward A. Narke from Design Space Inpharmatics.
About DS InPharmatics 
DS InPharmatics (DSI) provides regulatory, technical, and project management consulting services to healthcare product companies that manufacture and/or market pharmaceuticals, biopharmaceuticals, and cellular and gene therapy products.
Since 2007 we have provided our clients with innovative strategies and exceptional quality work products intended to enhance product development, approval, and marketing presence. Whether advocating CMC strategy, directing CMC operations or developing CMC submission content that represent the best interests of emerging biotech, we focus on the critical CMC issues and build programs that enhance development.
In April 2021 we were thrilled to announce that DSI has just become part of ProductLife Group.
French-headquartered ProductLife Group (PLG) is well-known in the Life Sciences market. It has a track record of successfully managing global outsourcing programs and insourcing services for its international client base. The company is on a mission to help transform human health outcomes by optimizing regulatory affairs, safety & vigilance, and quality compliance for life sciences organizations worldwide.
The fit between our two organizations could not be more perfect. We will complement PLG's growing biotech services portfolio. US biotech sponsors recognize DSI as a leader in consulting for go-to-market strategies and RA pre-market consulting. At the same time, PLG has a strong reputation for managing end-to-end outsourcing of regulatory affairs and pharmacovigilance activities worldwide.
Our merger with PLG will harness our combined strengths, offering our clients on both sides of the Atlantic support with their developed drugs approvals and post-approvals compliance, plus advisory services on the best market strategies to deliver a rapid ROI on their development. Together we will offer our clients increased pharmacovigilance capabilities - including a QPPV; pharmacovigilance consulting; and a fully validated safety database - as well as complementary toxicology-related services; RIM/electronic document management services; and support for medical device regulatory requirements.
We see enormous potential in this new chapter for DSI and you, our clients. As a PLG company, we have the opportunity to become part of a global force in life sciences regulatory and compliance solutions and services, and we're incredibly excited to add our momentum to that effort.
Sponsored Content Policy: News-Medical.net publishes articles and related content that may be derived from sources where we have existing commercial relationships, provided such content adds value to the core editorial ethos of News-Medical.Net which is to educate and inform site visitors interested in medical research, science, medical devices and treatments.