Unexpected events are the last thing that businesses want to encounter when manufacturing and developing active pharmaceutical ingredients. Unfortunately, even with the most accurate techniques, strategies and processes, challenges can arise in manufacturing.
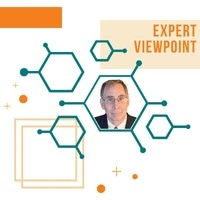
Image Credit: DSI, a PLG Company
From his time in the industry before the contemporary good manufacturing practice (cGMP), senior drug substance consultant at DSI, a ProductLife Group company, Dave Adams quickly grasped the necessity of understanding the facility and how the processes and equipment function when placing an API into production.
This means including the operators, listening to their concerns and collaborating with them to solve a challenge.
For many years at one of the companies I worked for, we operated a plant by having a team with one member from each department: QC, purchasing, warehousing, etc. There were maybe eight people on a process team, and this team would have full responsibility for running a batch, a campaign. We also included operators on the team, and they provided invaluable input on managing processes in cheaper, faster, and safer ways.”
Dave Adams, Senior Drug Substance Consultant, DSI, a ProductLife Group Company.
Developing your API
Companies must organize pilot batches and scale-up before they take a molecule into production. This is where personnel with development or plant expertise is required. The reason for this is that while a distillation or filtration might take minutes in a laboratory, it may take hours in a production facility.
“In production, time is money. The longer it takes to run the process, the more it’s going to cost your company, while the faster something is produced, the lower the cost,” Dave explains. “As soon as you see a distillation, an engineer can calculate how many hours of work that’s going to be, and what that is going to do to cycle time.”
The company’s development chemist should ideally have experience in working with plants so they can create the most efficient procedure for any facility.
“Make a process that separates well and doesn’t need conductivity sensors or that filters well and has good crystallization,” Dave notes.
“Another consideration is your choice of solvent. Pick a solvent that boils easily or works well for your process so the engineer won’t have too many difficulties putting it into the plant.”
An additional key consideration is to ensure that the development chemist considers any issues they note during development, captures any challenges and evaluates them further. This can stop expensive problems from becoming larger in the future.
Bringing in the regulatory experts
With the emergence of quality by design (GBD) and cGMP development approaches, there has been a trend toward bringing quality assurance and regulatory personnel in when the raw materials are designated, and a process is established.
This guidance is critical due to the requirement to identify possible impurities in the filings.
The company’s expectations from the supplier must also be specifically defined in the agreement stage, so there are no unexpected factors concerning the raw material.
“If you’re worried about heavy metals, if you’re worried about sand or two by fours, you need to spell that out,” Dave states. “You need to be very careful and do an audit to ensure that they’re not going to give you surprises.”
The expense of these surprises can be significant, from failed batches that can greatly impede the development program to damaged reactors if sand gets into the product.
Penny-wise, pound-foolish
Cost is a widespread consideration for businesses in the process of development. As the development time cannot be anticipated, it is important not to underestimate the testing and time it takes to produce the product.
“One very important thing I’ve asked every time I’m involved with a new project is, ‘Did you try it on the plant time cycle? Did you hold it?’,” Dave adds.
“One client intentionally held each step for 12 or 14 hours just to stress test it, they went purposely slow at each step, including a filtration step that could be done in half an hour. They wanted to prove that it was going to work.”
“Another client wanted us to heat a batch with sodium hydroxide and water so it boils at 100. When the sample was ready, it was already overcooked and degrading. On the second batch I asked the operator to take a sample before they heated it up, and it was already done.”
“The reaction was that fast in the plant that they didn’t need to heat and hold for an hour. By following their process, they were degrading the sample. So yes, you need to investigate every parameter during development, and some of them might lead to surprises.”
As the validation protocols are developed, these are critical factors to consider. The important process parameters should be defined, and safety elements should be incorporated for a dependable development process.
Working with partners
The main factor to consider when collaborating with contract manufacturers is their level of expertise. The only way to establish this is often to have some experience or insight into the production process before a CMO is contracted.
It is also important to note that if the signed contract with a CMO does not cover batch quality and cycle time, money could be lost as a result of this.
“It helps to have somebody on your side who understands production and knows when you’re being taken advantage of, even up front when you’re signing your contracts,” Dave states.
Developing a relationship with the CMO and the sponsor to strengthen the link between engineering, quality control and production ensures the process is much more seamless than simply having a colleague in the CMO look at a document.
When transparent channels for communication are put in place, the sponsor receives frequent updates on the manufacturing process instead of waiting weeks or months to identify progress.
It is vital to have standard operating procedures established when managing the transfer of technology between the CMO and the sponsor. Record what will be moved, who will supply the samples, who is responsible for what tasks, test procedures, references, and what will be manufactured at which facility.
“It’s important to connect people on both sides – the analysts, the engineers, the chemists, and so on,” he explains.
“They need to follow SOPs and document everything they’re doing. They sign it every time a method is transferred, or batch record goes back and forth for approvals and revisions until both sides agree that it’s transferred correctly.”
Selecting a champion
At the top of the pyramid, it helps to establish a process champion who is responsible for the process and is a complete expert in the field. They will be the person who will make the most important choices, for example, placing orders, moving to a different location, or increasing production.
“It’s very important to have one process owner or process champion, one person who represents the process,” Dave states. “It’s this person who deals with scheduling issues at different plants, ensuring production at one site is ready in time for delivery to another site and that the overall plan is working.”
Acknowledgments
Produced from materials originally authored by Meranda Parascandola from Design Space InPharmatics.
About DS InPharmatics 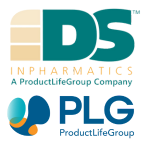
DS InPharmatics (DSI) provides regulatory, technical, and project management consulting services to healthcare product companies that manufacture and/or market pharmaceuticals, biopharmaceuticals, and cellular and gene therapy products.
Since 2007 we have provided our clients with innovative strategies and exceptional quality work products intended to enhance product development, approval, and marketing presence. Whether advocating CMC strategy, directing CMC operations or developing CMC submission content that represent the best interests of emerging biotech, we focus on the critical CMC issues and build programs that enhance development.
In April 2021 we were thrilled to announce that DSI has just become part of ProductLife Group.
French-headquartered ProductLife Group (PLG) is well-known in the Life Sciences market. It has a track record of successfully managing global outsourcing programs and insourcing services for its international client base. The company is on a mission to help transform human health outcomes by optimizing regulatory affairs, safety & vigilance, and quality compliance for life sciences organizations worldwide.
The fit between our two organizations could not be more perfect. We will complement PLG's growing biotech services portfolio. US biotech sponsors recognize DSI as a leader in consulting for go-to-market strategies and RA pre-market consulting. At the same time, PLG has a strong reputation for managing end-to-end outsourcing of regulatory affairs and pharmacovigilance activities worldwide.
Our merger with PLG will harness our combined strengths, offering our clients on both sides of the Atlantic support with their developed drugs approvals and post-approvals compliance, plus advisory services on the best market strategies to deliver a rapid ROI on their development. Together we will offer our clients increased pharmacovigilance capabilities - including a QPPV; pharmacovigilance consulting; and a fully validated safety database - as well as complementary toxicology-related services; RIM/electronic document management services; and support for medical device regulatory requirements.
We see enormous potential in this new chapter for DSI and you, our clients. As a PLG company, we have the opportunity to become part of a global force in life sciences regulatory and compliance solutions and services, and we're incredibly excited to add our momentum to that effort.
Sponsored Content Policy: News-Medical.net publishes articles and related content that may be derived from sources where we have existing commercial relationships, provided such content adds value to the core editorial ethos of News-Medical.Net which is to educate and inform site visitors interested in medical research, science, medical devices and treatments.