DSI has reviewed many pharmaceutical development reports varying from hundreds of pages to an outline of conclusions fixed to stacks of data. When it comes to putting a regulatory filing together, the latter can make the process challenging.
It has become evident that recording development data and decisions from the beginning in a living document is good practice and evaluating whether the information gathered so far is assisting development aims. It serves as a point of reference for what has been finished and what has yet to be done.
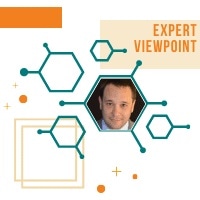
Image Credit: DSI, a PLG Company
Although a development report should ideally be near to a complete state at the time of filing, this is not a complete necessity, explains Kyriakos Michailaros, the Head of Drug Product Services at DSI, a ProductLife Group company.
Better known as Q, Kyriakos states that the development report is designed to tell the background of the drug’s development. It must identify the background science, initial goals, data, experiments and anything that directs the development of the process and establishes the final manufacturing and formulation process.
Start with a plan
All development schedules must begin with a plan. Near the beginning of a project, companies should write a Quality Target Pharmaceutical Profile (QTPP) that outlines what the product is designed to treat, dosing, administration and other appropriate characteristics.
A Gantt chart presents the timeline and milestones to achieve this from early stage and possibly through to filing, Q explains.
Some of the milestones along that journey involve finalizing the formulation, excipient compatibility, phase two, optimization, process development and possibly the end of phase three.
At those points, it’s important to have a report or a risk assessment documenting the data collected and the conclusions and decisions made based on that data for the development program. Better yet, a characterization report outlines your critical process parameters and demonstrates that you can consistently make the product.”
Kyriakos Michailaros, Head of Drug Product Services, DSI, a ProductLife Group Company.
A widespread challenge is that data tends to be in different reports until the filing stage. This is because turnover can be common in the development team and development programs progress over the years.
Creating an up-to-date living document can solve the issue of managing the various stages of the process and recording the complete history of the program.
“Having your development data and conclusions automatically downloaded to a common document means you have all the critical information that you’re basing your development program on in one place,” Q explains.
“So, if you’re having a meeting with the FDA or planning a filing, you know where to find all the relevant information.”
It is also important to record data that was not utilized in the development because every effective program performs risk assessments throughout the journey to show that the main challenges have been solved.
Piecing it all together
Q and his team as CMC consultants usually note that the development story requires a jumble of organized and often disorganized assessments, data summaries, reports which may or may not be finished, and batch records to be pieced together.
The main advantage of a working development document is to keep the information in one location, where there is a shared understanding of where data is stored.
This eliminates confusion and saves time for the members of a development program. It makes it simple to see the information that has formed the basis of decisions and if there are any gaps.
Creating a complete report of development work so far helps possible buyers with the process of due diligence, even if a business chooses to only take a product to the IND stage before looking for a buyer.
An alternative and effective method would be to create a working document repository with a file structure that can be followed in order to build a report.
Q states, “I think it’s actually more important in a situation like that, where you don’t want to take a project all the way to completion, to have a working document because you’re not then scrambling to get something together that’s coherent if and when you enter talks with a potential buyer.”
Addressing the gaps
It is crucial to establish what the gaps are in a business development program as it becomes closer to milestones. This is where CMC experts like Q are called in to offer a gap analysis.
Q states that when performing a gap analysis, “The first thing I would check is that a company has the appropriate stability information. Is the stability on the finalized packaging configuration or formulation or process in line with expiry data? It takes time to acquire stability data, so fixing this issue will take some time.”
Further areas to evaluate are whether the process control parameters have been correctly measured and if they are suitable for the drug product and the procedures that are utilized to manufacture it.
There are several types of drug products, and it is essential to take an approach that is tailored to the product when investigating. It is important to understand which regulations are relevant and to know the explanation behind the choices that are made.
“At the minimum, you need to check the boxes,” Q explains. “You need to have the particular issues that are known for the type of formulation, for the type of drug product, for the type of packaging configuration, pretty well covered because they’ll be scrutinized.”
Start early, stay up to date
Q and his team, as drug product subject matter experts, have worked on several reports where the source documents were incomplete and disorganized. Not only is it time-consuming to solve this, but it also leads them to question whether certain development tasks have been recorded in full.
“It’s never too early to start your development report to have the story of the development complete and summarized by the time you’re making an NDA submission,” Q explains.
“With information easily available, it becomes simpler to put forward arguments to the reviewers, present explanations and justifications for certain data, and tackle difficult issues head-on, rather than wait for reviewers to notice the problematic data during the review,” states the principal and chief regulatory scientist Ed Narke from DSI.
Acknowledgments
Produced from materials originally authored by Meranda Parascandola from Design Space InPharmatics .
About DS InPharmatics 
DS InPharmatics (DSI) provides regulatory, technical, and project management consulting services to healthcare product companies that manufacture and/or market pharmaceuticals, biopharmaceuticals, and cellular and gene therapy products.
Since 2007 we have provided our clients with innovative strategies and exceptional quality work products intended to enhance product development, approval, and marketing presence. Whether advocating CMC strategy, directing CMC operations or developing CMC submission content that represent the best interests of emerging biotech, we focus on the critical CMC issues and build programs that enhance development.
In April 2021 we were thrilled to announce that DSI has just become part of ProductLife Group.
French-headquartered ProductLife Group (PLG) is well-known in the Life Sciences market. It has a track record of successfully managing global outsourcing programs and insourcing services for its international client base. The company is on a mission to help transform human health outcomes by optimizing regulatory affairs, safety & vigilance, and quality compliance for life sciences organizations worldwide.
The fit between our two organizations could not be more perfect. We will complement PLG's growing biotech services portfolio. US biotech sponsors recognize DSI as a leader in consulting for go-to-market strategies and RA pre-market consulting. At the same time, PLG has a strong reputation for managing end-to-end outsourcing of regulatory affairs and pharmacovigilance activities worldwide.
Our merger with PLG will harness our combined strengths, offering our clients on both sides of the Atlantic support with their developed drugs approvals and post-approvals compliance, plus advisory services on the best market strategies to deliver a rapid ROI on their development. Together we will offer our clients increased pharmacovigilance capabilities - including a QPPV; pharmacovigilance consulting; and a fully validated safety database - as well as complementary toxicology-related services; RIM/electronic document management services; and support for medical device regulatory requirements.
We see enormous potential in this new chapter for DSI and you, our clients. As a PLG company, we have the opportunity to become part of a global force in life sciences regulatory and compliance solutions and services, and we're incredibly excited to add our momentum to that effort.
Sponsored Content Policy: News-Medical.net publishes articles and related content that may be derived from sources where we have existing commercial relationships, provided such content adds value to the core editorial ethos of News-Medical.Net which is to educate and inform site visitors interested in medical research, science, medical devices and treatments.