Dry granulation, also called roller compaction, has been a popular method in recent years and has many applications. The powder is compressed between revolving rollers to generate flakes. The flakes are crushed with a sieve and sieve inserts to produce granules with the correct particle size distribution.
The pressed and dried granules are employed in various pharmaceutical applications, where they are used as starting materials, intermediates, dosage forms for rapid manufacture, or ingestible granules.
Compacted granules have a higher bulk density and particle size than the original material. As a result, the granules have improved flow characteristics, which leads to better processing. Granulation also lowers dust and particles, resulting in little to no material loss and minimal dust exposure.
Agglomerates pre-compacted through dry granulation are easier to tablet than powders. All of the features of compacted granules help to achieve the tableting goal of making the most uniform tablet feasible.
Unlike wet granulation, a batch process, dry granulation is a well-established method of producing solids. Dry granulation is very useful for moisture-sensitive medicinal compounds.
Dry granulation does not require any energy for drying or solvent recovery. This is a compelling argument favoring dry granulation, particularly in light of rising energy prices.
Horizontal roll arrangement with advantages
The arrangement of their rolls distinguishes dry granulators. Some systems use horizontal, vertical, and inclined rolls
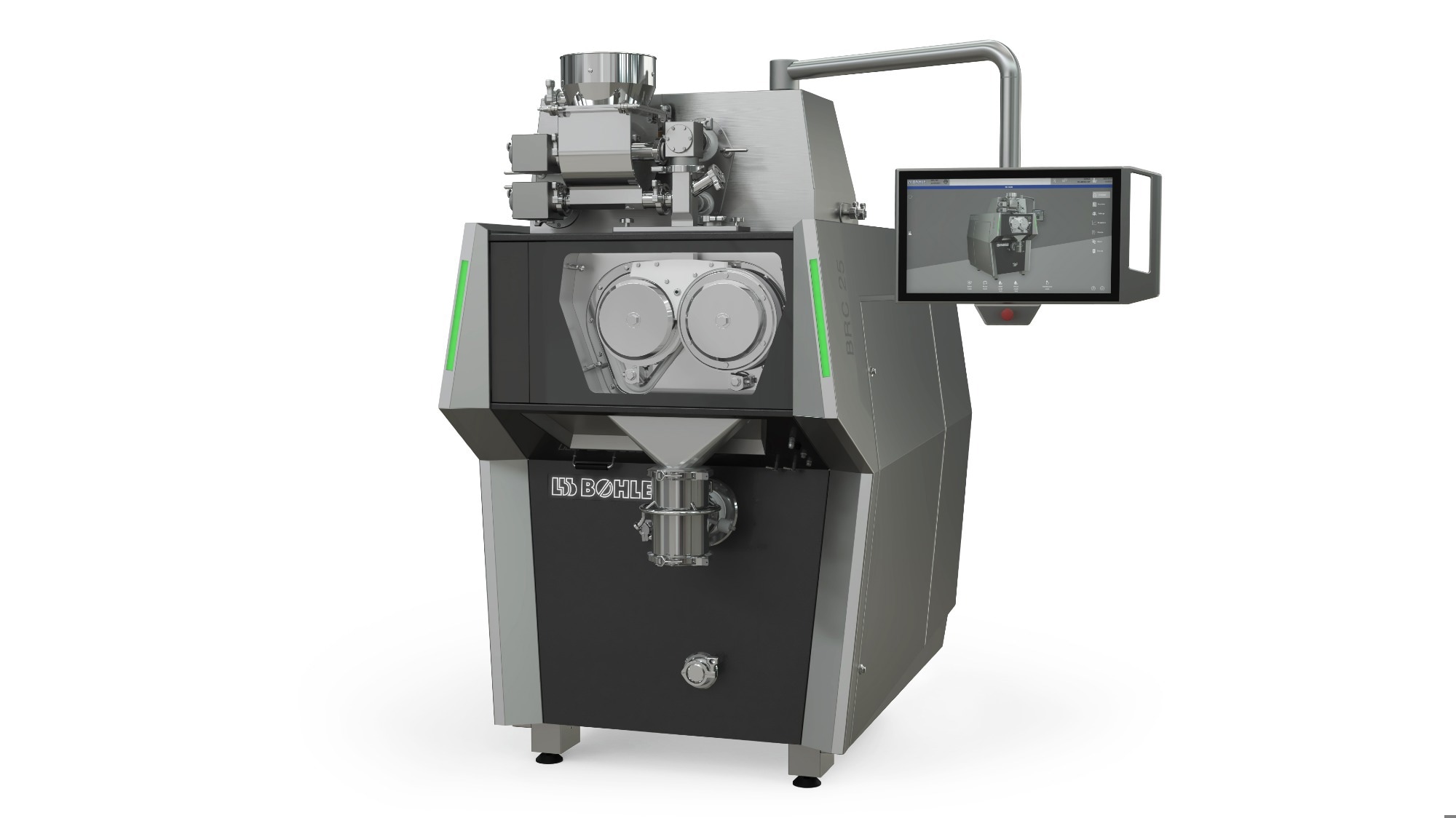
Image Credit: L.B. Bohle Maschinen und Verfahren GmbH
L.B. Bohle (Germany) uses horizontal rolls for compaction. This arrangement provides better ventilation for the screws and discharging the flakes over a shorter distance. Other dry granulators' characteristics include the compaction rolls' breadth, diameter, and surface finish.
The systems also differ in whether the gap is fixed or variable. Dry granulators with varying gaps are preferable. This is the only technique to assure consistent pellet porosity at constant pressing force, resulting in reproducible flake output.
During continuous gap distance measuring, real and target values are compared. The idea is to keep a parallel gap between the rolls throughout the operation so that the departing flake has the same qualities across its entire width.
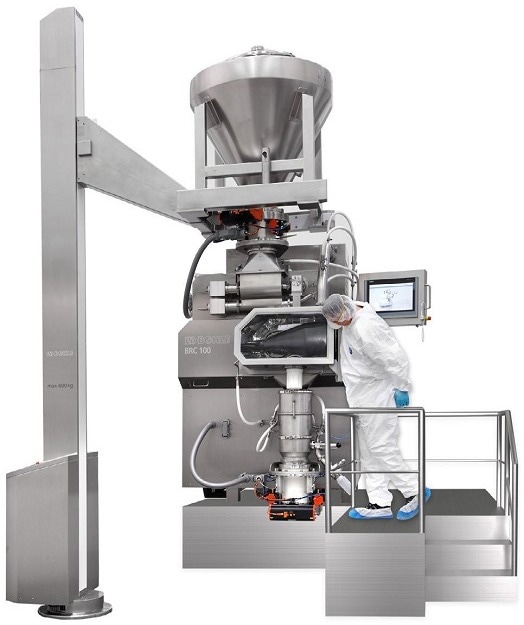
Image Credit: L.B. Bohle Maschinen und Verfahren GmbH
The screw speed is linked to the gap adjustment via a control loop. As a result, when the nip opens, the screw moves less material into the nip, allowing it to close again. The automatic control creates flakes with preset thickness and porosity.
Electromechanical drive
L.B. Bohle's BRC series provides high product capacity while minimizing material loss. In contrast to competitive hydraulic systems, force generation is entirely electromechanical. This maintains consistent scab properties.
The electromechanical drive overcomes hydraulic control's shortcomings, such as oil and control valve aging, temperature variations, and oil pollution.
This high-precision technique is further enhanced by employing force-measuring sensors inside the force adjustment, which directly measure the pressing force. The results are more exact than in hydraulic systems, where values are often determined.
The BRC's unique compaction force and flake thickness management ensures uniform material compaction across a production range of < 1 - 400 kg/h. At the same time, the smart, unique machine design makes handling easier and shortens the assembly process.
The hygienic design and standard integrated washing nozzles ensure an effective WIP procedure that removes the product without leaving residue. Furthermore, the compactor fits the "Quality by Design" concept's requirements due to its functional GMP-compliant design and the ability to incorporate PAT tools.
In addition to compaction force, the size reduction step has a considerable impact on the ultimate particle size of the granules.
The Bohle Conical Turbo Screen Mill BTS and its screen inserts gently reduce the flakes to granules with the correct particle size distribution, even at high material throughputs.
At the same time, each BRC may be quickly converted to an alternate rotary screen BRS, allowing it to be easily tailored to process and flake needs.
Dry granulation in practice
L.B. Bohle has been producing its BRC range since 2012, and the number of items created with the BRC has grown dramatically internationally as this granulation technology is particularly cost-effective.
Dry pelletizing is a continuous process that achieves great throughput while needing less space and energy. It also eliminates the need for granulating fluids and drying equipment.
Roller compaction can be used on various items. Many generic pharmaceuticals, including ibuprofen, metformin, blood pressure medications, and antibiotics, are dry-granulated. Dry granulation is increasingly being used from the start when developing novel products.
While roller compaction is a continuous production method that can accommodate both big and small batch sizes, nearly all products are produced in batches.
The changeover is quick because of its revolutionary design (ergonomic height, no ladder or framework required).
Changeover after cleaning and reassembling takes 30 minutes. Competitors' systems require up to eight hours for cleaning and assembly. The BRC requires only the bare minimum of tools (at the roller and scrapper), while all other components are designed for tool-free replacement.
Flexibility: Versatile integration in the production process
Roller compactors have a small footprint and may be easily integrated into production.
L.B. Bohle has set up many BRC series machines in batch and continuous production settings. Solutions include stand-alone systems, wall-mounted installations, platform and multi-floor applications, interlinked systems, and confinement applications.
Containment - No problem
Active pharmaceutical ingredients (APIs) are becoming more potent, particularly in new medications. In some areas, the category for high-potency APIs (HPAIs) is rising at a double-digit rate, fueled primarily by oncology medications.
In addition to the standards outlined in manufacturing rules, the product must be safe for the machine operator and, of course, the patient. As a result, L.B. Bohle faces new hurdles across all hazard classes where clients seek to employ plants and processes.
For example, a specific version for containment applications at the OEB 5 level is shown.
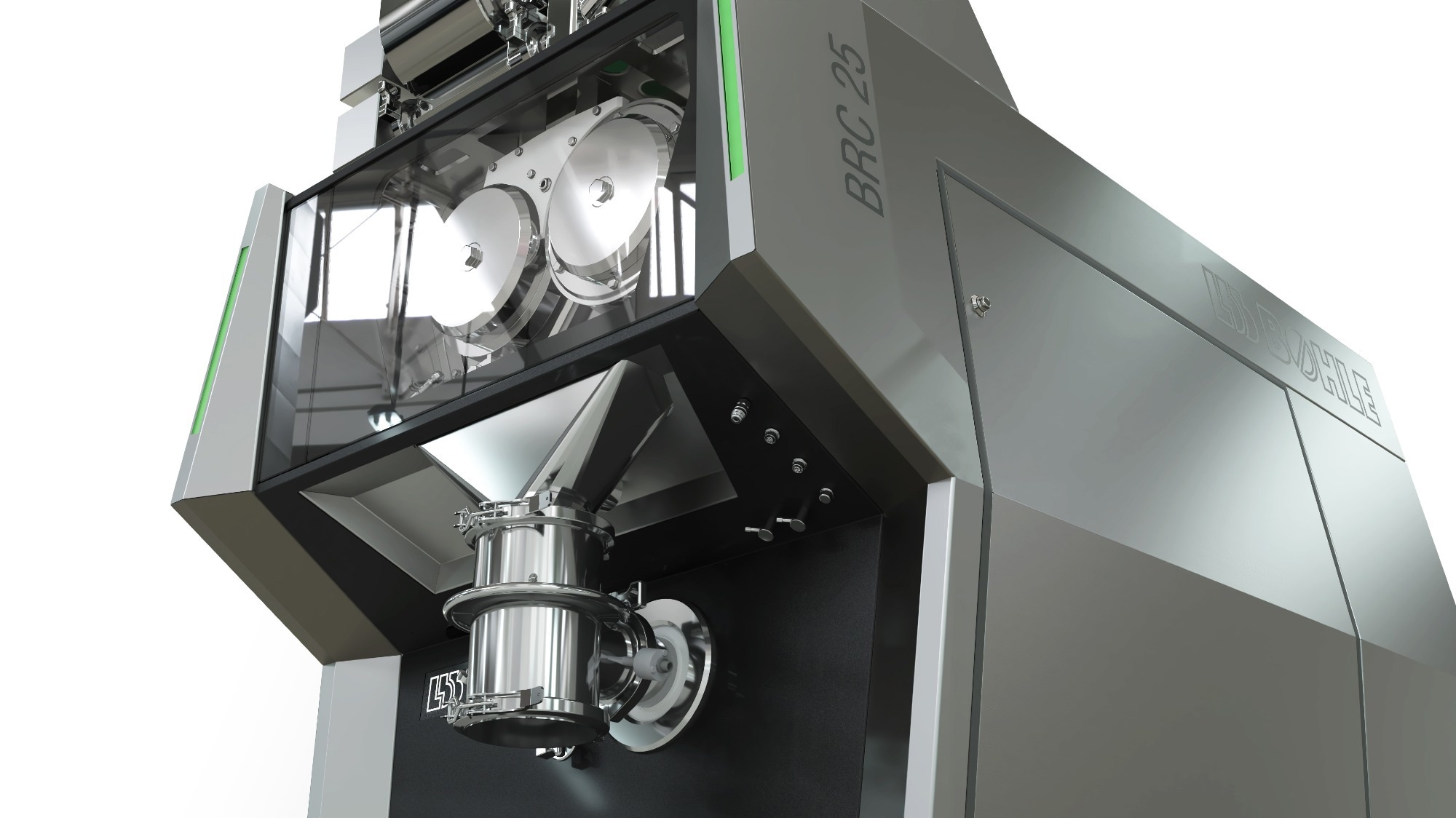
Image Credit: L.B. Bohle Maschinen und Verfahren GmbH
The confinement version contains:
- Integrated isolator unit in the compacting unit with vacuum monitoring
- Glove box and safety request for flake removal
- Containment port for flake sample collection
- Containment port beneath the sieve unit for the removal of grains
- Convenient access because no full isolator unit is fitted around the entire compactor
- Integrated WIP equipment allows for residue-free product removal (WIP is also integrated into the standard version)
About L.B. Bohle Maschinen und Verfahren GmbH
L.B. Bohle with the headquarter in Germany, is one of the largest system suppliers for the pharmaceutical processing industry and related sectors. Internationally active, they focus on machinery and equipment as well as process technology and components.
In addition, L.B. Bohle offer sustainable solutions for demanding production processes in batch and continuous manufacturing for the oral solid dosage production. For instance, L.B. Bohle provides single or interlinked machines for the processes Weighing, Dry and Wet Granulation, Grinding and Sieving, Container Blending, Tablet Coating and Tablet Handling.
Sponsored Content Policy: News-Medical.net publishes articles and related content that may be derived from sources where we have existing commercial relationships, provided such content adds value to the core editorial ethos of News-Medical.Net which is to educate and inform site visitors interested in medical research, science, medical devices and treatments.