Pharmaceutical research and development (R&D) and industry require a continuous fluid-bed dryer that provides a lengthy process time and delivers a high standard for a long time.
This article discusses the investigational testing on a new R&D system (QbCon® 1) that provides continuous granulation and drying. Attention has been focused on the dryer and the granules produced.
The dryer achieved extremely narrow and duplicatable residence time distributions, resulting in dissimilar size classifications of granules that dried uniformly. The process provides a reliable standard of particle size and moisture content of the granules over a few hours.
Altering the transportation speed of the granules in the dryer and leaving all other factors unchanged established the scope for combining a set procedure and mixture dependent on the fluid bed depth.
The capability of observing the process in-line and an innovative drying system establishes the QbCon® 1 as the perfect equipment for continuous wet granulation.
Introduction
The FDA Guidance on Process Analytical Technologies (PAT) and the ICH Guidelines Q8, Q9, and Q10 on pharmaceutical development, quality-related risk management, and quality systems have supported the idea of continuous pharmaceutical production. The application of continuous production processes offers many benefits to the pharmaceutical industry.1-3
Monitoring a manufacturing process meticulously using PAT produces products with consistently high standards. Major benefits are decreased costs, increased patient safety, improved understanding of the process, and enhanced process control.
Continuous processes require extended manufacturing timelines rather than scaling up. Everything begins in the laboratory, where compact equipment suitable for the smallest throughputs is required.
Granulation and granule drying improve flowability, prevent segregation, and reduce dust. Continuous production does not always eliminate these issues. However, no continuous drying systems currently available meet pharmaceutical manufacturing standards.
A shortened residence time of the granules in the dryer with a narrow residence time distribution is vital in targeting defective products without discarding a substantial percentage of the batch. This occurs when there is excessive back-mixing.
Narrow residence time distributions allow material in the continuous process to be easily traced. Tracing completed tablets back to the raw materials or tracing raw materials to the finished tablet is less complicated.
There are several quality requirements for a dryer. It must produce consistent, duplicatable drying for all the assorted sizes of granules during the whole process. A small processing chamber keeps the volume as low as possible in the drying process, and an extended use of the exhaust air filters eliminates interruptions to the drying process or the need to change the filters.
Semi-continuous or quasi-continuous dryers for granules (with multiple drying chambers working in parallel) are available from several different suppliers. However, they do not meet the quality requirements of the pharmaceutical industry. In addition, some semi-continuous dryers do not meet the specifications for a fully continuous dryer by not reducing waste products.
In semi-continuous drying processes, a large amount of material remains in multiple chambers, resulting in whole partial batches being disposed of to eliminate the doubt created by excessive (back-)mixing. It is not possible to discard only specific partial quantities.
The article details an innovative continuous dryer that combines all the standards required for a pharmaceutical system. The dryer is a component of the QbCon® 1, a system for R&D. The QbCon® 1 provides fully continuous manufacturing of granules through wet granulation and drying integrated with a fully automated and mechanical unit.
In testing the systems’ tolerance, the function of granulation and drying was explored and its suitability as a continuous operation has been demonstrated. For this reason, vital quality properties of the granules were analyzed during the process, as were the limits of process.
Materials and methods
Materials
A powder mixture (proportions: 80/17/3) combining α-lactose monohydrate (Granulac 200, Meggle, Wasserburg, Germany), microcrystalline cellulose (Avicel PH 101, FMC BioPolymer, Philadelphia, PA, USA) and povidone (Kollidon 30, BASF, Ludwigshafen, Germany) was chosen for granulation. Purified water was utilized as granulation liquid. The blue, water-soluble dye FD&C Blue No.1 (BASF) was chosen to analyze the residence time distribution of the granules in the dryer.
Manufacture of the granules / System description QbCon® 1
The three powders were combined in a laboratory mixer (LM 40, L. B. Bohle Maschinen + Verfahren GmbH, Ennigerloh, Germany) at a speed of 15 rpm. Granules were manufactured in a fully continuous process.
The QbCon® 1 (Fig. 1) (L. B. Bohle) system has fully integrated software and unit functions comprising various components by L. B. Bohle (automatization, liquid feeding, wet granulation, drying) and Gericke (powder feeding). Feeding of powder and liquid, wet granulation and drying are attainable in one fully continuous process step with no interruptions. A touch panel controls and monitors the entire process.
The minimum throughput of the system is 0.5-2.5 kg/h but can deviate upwards significantly. When high-density material is utilized, the necessary moisture for granulation is low or the required residual moisture is higher. In testing, the above noted powder mixture was poured into the gravimetric powder feeder (GZD150.12 special, Gericke, Regensdorf, Switzerland) and dosed at a rate of 1 kg/h into the first zone of the QbCon® 1 twin-screw granulator.
The granulation liquid was dispensed into the second zone of the granulator using a high-pressure pump and a nozzle with an internal diameter of 0.25 mm. The liquid feed rate was regulated by a Coriolis flow meter at 4 g/min obtaining a granule moisture level of 24 %. In a twin-screw granulation process, powder and liquid are dispensed onto two co-rotating screws continuously. The components are constantly moved, mixed, and sheared, producing granules that exit the granulator at the outlet.
See Figure 2 for an example and summary of the granulator process zone. The twin screw granulator of the QbCon® 1 has screws with a diameter of 25 mm and a length of 20 x diameter, operating at a screw speed of 50 1/min. The screw configuration comprised mostly double-flighted conveying components.
After the liquid feeding, a kneading component incorporating five individual discs with an offset angle of 45° and a length of 25 mm was utilized supporting the even dispersal of liquid in the granules. Just before the outlet, a second kneading zone with identical length and offset angle was installed.
The movement of the granules and the airflow can be adjusted separately. This keeps the drying effect of the granules under control by adjusting the airflow, supply air temperature, and the moving speed. The filter surface for the exhaust air is kept free with a cleaning process based on a new concept. Making continuous granulation with no interruptions to the process is possible.
The dry granules exit the QbCon® 1 via a pneumatically operated valve where they can be assessed and processed. A prepared mechanical interface for a NIR probe or similar probe permits in-line quality validation controlling the process based on active ingredient content, moisture, and product temperature of the granules.
Residual moisture content
The residual moisture of the granules was calculated based on the loss from drying of all the samples (approx. 3 g). This test used an analytical moisture analyzer (HR73 Halogen Moisture Analyzer, Mettler Toledo, Columbus, Ohio, USA) at a drying temperature of 105 °C. The abort criterion was a mass loss of < 1 mg within 60 seconds. The test was completed three times for each sample.
For one test, the dry granules were separated into four size classes with test sieves of 1.4 mm, 1.0 mm, and 0.5 mm to calculate the consistency of drying in a variety of sieve fractions.
Granule size distribution
A photo-optical analyzer (CPA 2-1, Haver und Boecker, Oelde, Germany) was utilized to determine the granule size dispersal. A sample of dried granules gathered over ten seconds was dispensed into the measuring zone with an automatic vibrating feeder. A line scan camera calculates the granule size and immediately transmits the information to the connected software for assessment. For the evaluation, the 10 %, 50 % and 90 % size quantiles of the Q3 distribution were used.
Residence time distributions
The residence time distribution of the granules in the continuous dryer was calculated using ExtruVis 3 (ExtruVis, Riedstadt, Germany). The equipment combines an industrial camera, a ring light to constantly illuminate the recorded room, and specialized software for evaluating the data. During processing, a pulse of moist granules dyed blue was manually dispensed into the inlet of the continuous dryer. The colored granules moved simultaneously with the white granules toward the outlet.
The ExtruVis camera was located at the front of the outlet to record the dispersal of the colored granules within the white granules. The software calculated a density distribution of the residence time as a function of time (E (t)) based on the color intensity at the outlet.
The full specifications of the equipment can be read in Meier et al.4 Calculating the frequency of approximately 20 images per second provided a dependable in-line assessment of the residence time distribution in the dryer. The mean residence time of the granules in the dryer is calculated by halving the area under the residence time curve.
Trial design
This study focused on the drying process of QbCon® 1. A long-term test was completed utilizing the process data previously noted, where samples were obtained at regular intervals over 2.5 hours, and then inspected for a variety of quality features.
The drying conditions were changed by varying the moving speed of the granules in the dryer while all other process and mixture factors were maintained. The goal was to determine the process limits of the dryer for underlying conditions dependent on the residence time.
Results and discussion
It was noted that the continuous granulation and drying tests could be completed without interrupting or disturbing the process. The vital process factors of feeding, granulation, and drying remained constant throughout the test period.
The exhaust filters had a small amount of the fines content of the granules on their surfaces. This resulted because of the exceptionally low fluidization of the granules in the dryer. This reduced the cleaning time of the product filters to 20 minutes. The filters were completely cleaned without leaving any product residues behind.
Residual moisture is an essential quality feature for dried granules. Fluctuating values and high residual moisture content can cause unreliability in downstream processes, like soiling of sieve surfaces, differences in tablet content, or problems with continuously feeding the granules.
Figure 3 shows the residual moisture of the manufactured granules after continuous drying for a test period of 2.5 hours. The initial moisture percentage of the raw material was 1.28 %. The residual moisture of the granules fluctuated between 1.02 % and 1.38 % during the test and averaged 1.21 ± 0.11 %.
This irregularity around the mean value is allowable for residual moisture calculation using LOD and is considered as extremely low. Regarding the moisture content of the dried granules, obtaining a dependable and duplicatable outcome is essential in a continuous process. The drying produced impressive results, with some granules having lower moisture content than the raw material.
This is extremely important for moisture-sensitive products. If the residual moisture is too low, the process can be adapted to shorter drying times (= residence times), lower temperatures and air flow rates to obtain higher residual moisture contents.
In addition to residual moisture, a constant granule size dispersal is essential for processing the granules further. Figure 4 shows the granule size dispersals' 10, 50, and 90 % quantiles. The continuous granulation and drying process results in uniform granule sizes due to the low fluctuations in the 10 % quantile (mean value: 298 μm) and median granule size (mean value: 726 μm).
Normal fluctuations for twin-screw granulation are in the 90 % quantile, which is the highest percentage in absolute terms for these tests, and the smallest has a relative standard deviation of 6 %. Fluctuations in the 90 % quantile (mean value: 1805 μm) are allowable. In addition, larger granules are normally classified following the drying step resulting in a narrower size dispersal.
The residence time of the granules in the dryer decides when the moist granules are subjected to the drying airflow. A continual residence time distribution is important for dependable drying outcomes.
Residual moisture and granule sizes determines a constant residence time. Investigating the residence time behavior in the continuous dryer is important for upscaling larger systems and for discharge theories for faulty materials in a fully continuous process.
Figure 5 demonstrates the distribution of the residence time of the granules in the dryer at the beginning, middle and end of the tolerance test. The curves are almost identical, as previous results described. The mean residence time for continuous drying of the three tests was quick at 57, 61 and 63 seconds. Maintaining low residual moisture exemplifies how effectively the drying air flows through the granules.
The mean residence time and the width of the residence time distribution are critical variables that describe the movement and mixing actions of the system. The small width of the calculated dispersals is perfect for a continuous dryer. The goal is to move all the granules through the dryer at the same speed to obtain a consistent drying result. Wide residence time distributions can produce variable moisture content in a sample. The curves are almost axis-symmetrical indicating reduced back-mixing in the dryer.
These factors make it necessary to test the consistency of the drying process in a sample. Optical observations did not indicate variations in the movement speed of fine or coarse particles.
Figure 6 demonstrates the residual moisture of granules of varying sizes in the same sample having only small variations. The granules with the largest fraction had a slightly elevated moisture level. This is common in fluid-bed drying and is not significant within the scope of this article.
To further describe the QbCon® 1 and to test the limitations of the mixture and throughput, the moving speed of the granules was increased or decreased with an adjustment to the vibration feeder. This resulted in varying granule bed heights in the dryer and residence time distributions, producing different lengths and widths. This is demonstrated in Figure 7.
The mean residence times varied between 49 and 229 seconds (about four minutes), and the curves had a high degree of symmetry. The residence time distribution with the longest mean residence time is particularly interesting. The extended time between the first and last appearance of colored granules in the residence time test indicates that sample granules would not dry uniformly. This is demonstrated in Figure 8, where the residual moisture of the granules is described as a function of the mean residence time.
When the mean residence time increased from 49 to 148 seconds (about 2 and a half minutes), the residual moisture of the granules dropped from 1.37 to 0.65%. When the mean residence time is increased to 229 seconds (about 4 minutes), the residence time curve is widened simultaneously, and the residual moisture increases again. In addition, the values disperse widely with a relative standard deviation of > 41 %. A reduced inconsistent flow through the granules results when the residence time is too long, and the bed thickness of the granules in the dryer increases. These two factors are important considerations when designing a specific process.
Conclusion
An innovative system for continuously manufacturing and drying granules on a laboratory scale was explored. The testing indicates the exciting potential of this new drying process utilizing a fluid bed. A short and narrow residence time distribution produced consistent and continuous drying of the granules. This was obtained with various size classes and particle size dispersals over time. These results are unique in continuous wet granulation and illustrate the system’s superior performance with common processes.
Using variable conveying speeds of the granules in the dryer allowed the limits for a given mixture and throughput to be determined by the residence times and residual moisture content.
The height of the granule bed was a factor that required careful control. The ability to observe the process in-line makes the QbCon® 1 and its pioneering drying process the perfect equipment to introduce continuous wet granulation to pharmaceutical companies.
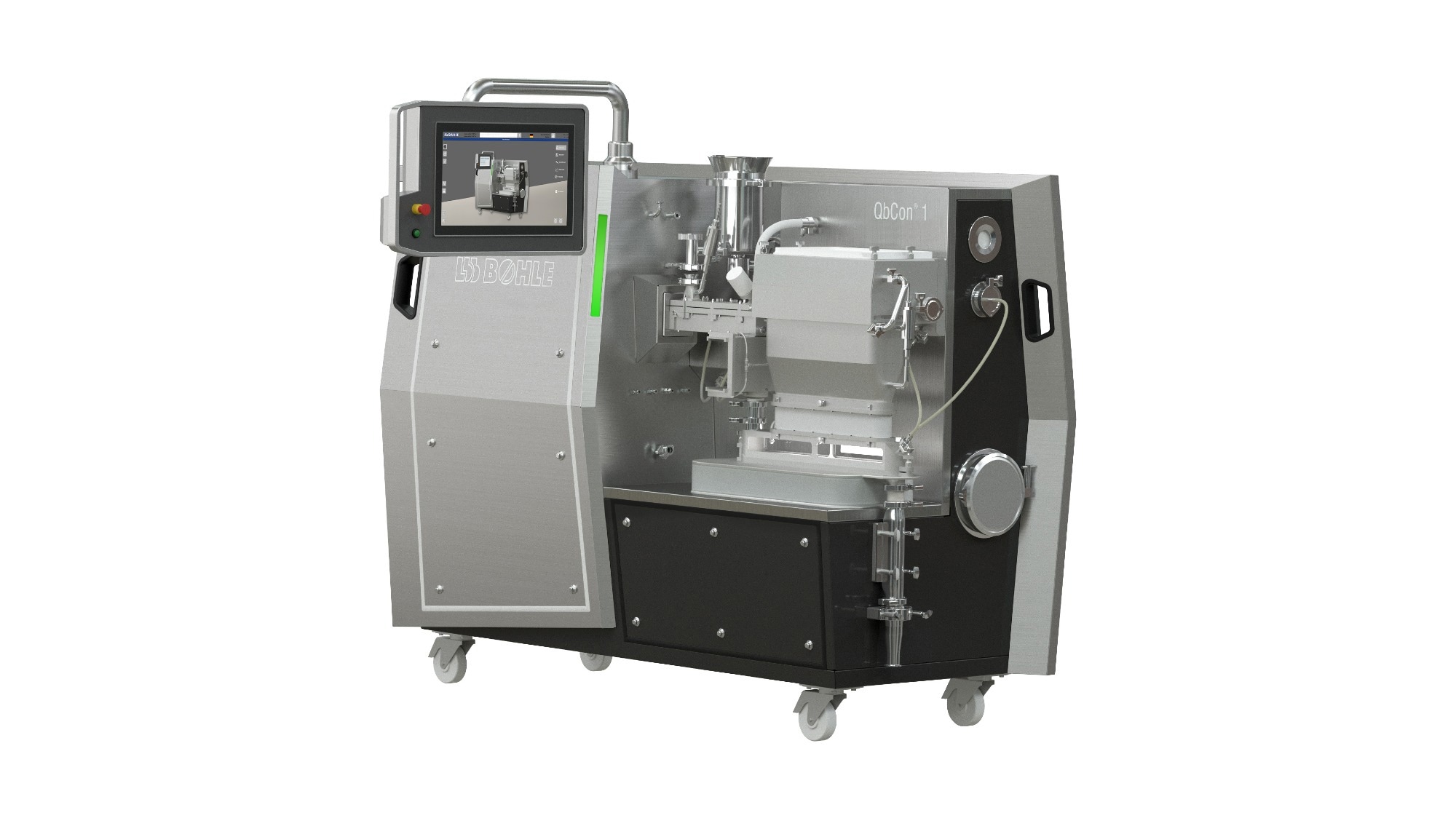
Figure 1. QbCon® 1 - Fully continuous and fully integrated system for the production of granules. Image Credit: L.B. Bohle Maschinen und Verfahren GmbH
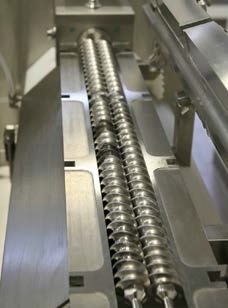
Figure 2. Insight into the process zone of the granulator, which is part of the QbCon® 1. Image Credit: L.B. Bohle Maschinen und Verfahren GmbH
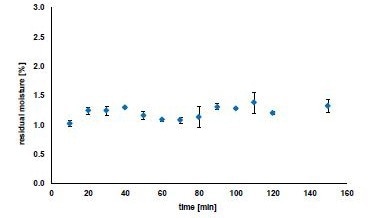
Figure 3. Moisture content of the produced granules after continuous drying over a process time of 2.5 hours; n=3, mean ± standard deviation. Image Credit: L.B. Bohle Maschinen und Verfahren GmbH
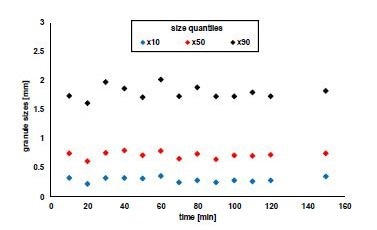
Figure 4. Size quantiles of the granule size distribution after continuous drying over a process time of 2.5 hours. Image Credit: L.B. Bohle Maschinen und Verfahren GmbH
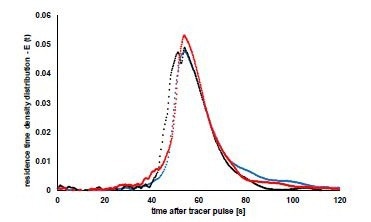
Figure 5. Measured residence time distributions of the granules in the continuous dryer at times t=0 min (red), t=75 min (black) and t=150 min (blue). Image Credit: L.B. Bohle Maschinen und Verfahren GmbH
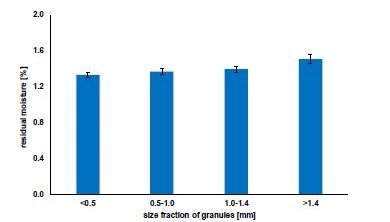
Figure 6. Residual moisture content of the different size fractions of the dried granules; n=3, mean ± standard deviation. Image Credit: L.B. Bohle Maschinen und Verfahren GmbH
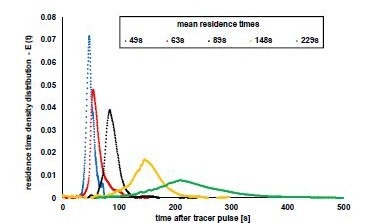
Figure 7. Measured residence time distributions of the granules in the continuous dryer at different conveying speeds. The legend of the graphic shows the calculated mean residence times associated with the curve progressions. Image Credit: L.B. Bohle Maschinen und Verfahren GmbH
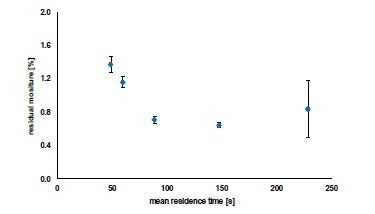
Figure 8. Residual moisture content of the produced granules as a function of the mean residence times; n=3, mean ± standard deviation. Image Credit: L.B. Bohle Maschinen und Verfahren GmbH
References and further reading
- H. Leuenberger, New trends in the production of pharmaceutical granules: Batchversus continuous processing, Eur. J. Pharm. Biopharm., 52 (2001) 289-296.
- C. Vervaet, J.P. Remon, Continuous granulation in the pharmaceutical industry, Chem.Eng. Sci., 60 (2005) 3949-3957.
- J. Rantanen, J. Khinast, The future of pharmaceutical manufacturing sciences, J.Pharm. Sci., 104 (2015) 3612-3638.
- .R. Meier, M. Thommes, N. Rasenack, K.-P. Moll, M. Krumme, P. Kleinebudde, Granule size distributions after twin-screw granulation - do not forget the feeding systems, Eur. Journ.Pharm. Biopharm., 106 (2016), 59-69.
About L.B. Bohle Maschinen und Verfahren GmbH
L.B. Bohle with the headquarter in Germany, is one of the largest system suppliers for the pharmaceutical processing industry and related sectors. Internationally active, they focus on machinery and equipment as well as process technology and components.
In addition, L.B. Bohle offer sustainable solutions for demanding production processes in batch and continuous manufacturing for the oral solid dosage production. For instance, L.B. Bohle provides single or interlinked machines for the processes Weighing, Dry and Wet Granulation, Grinding and Sieving, Container Blending, Tablet Coating and Tablet Handling.
Sponsored Content Policy: News-Medical.net publishes articles and related content that may be derived from sources where we have existing commercial relationships, provided such content adds value to the core editorial ethos of News-Medical.Net which is to educate and inform site visitors interested in medical research, science, medical devices and treatments.