3D bioprinting involves printing biocompatible materials, cells, growth factors, and other required support materials to create functional complex living tissues, including skin, bone, vascular grafts, and cartilage structures.
Various materials and formulations can be chosen to create both hard and soft tissues based on the desired properties. Among the various 3D printing techniques available, extrusion-based methods using bioinks are predominantly used due to the sensitivity of the materials involved.
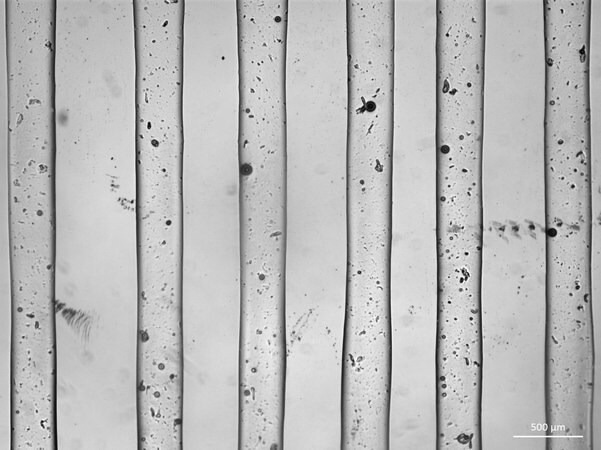
Figure 1. Printed Fibers using a G30 needle; scale bar represents 500 μm. Image Credit: Merck
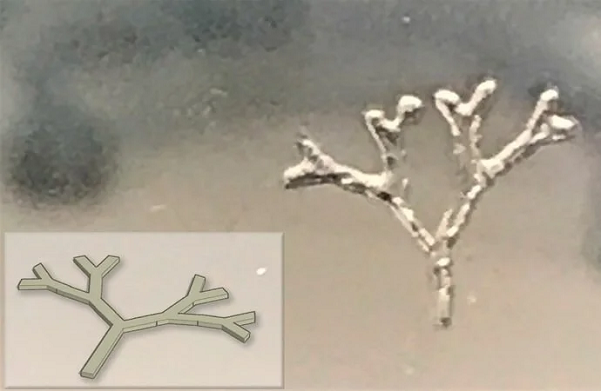
Figure 2. 3D printed branch-like structure using TissueFab® GelAlg UV; CAD design (inset). Image Credit: Merck
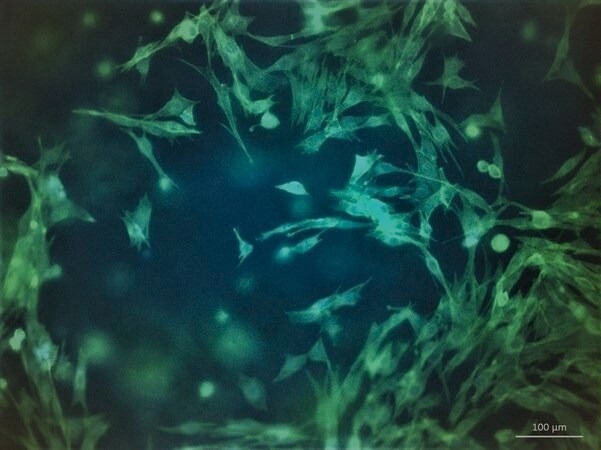
Figure 3. Morphology of C2C12 after 7 days post-printing with TissueFab® GelAlg UV. Cell cytoskeleton stained with F actin (green) and nuclei DAPI (blue). Image Credit: Merck
Properties
Source: Merck
. |
. |
Description |
0.2 μm sterile filtered, Suitable for 3D bioprinting applications |
Form |
Viscous liquid |
Packaging |
1 ea of 10 mL |
Impurities |
≤5 CFU/g Bioburden (Fungal)
≤5 CFU/g Bioburden (Total Aerobic) |
Color |
Colorless to pale yellow |
pH |
6.5-7.5 |
Application(s) |
3D bioprinting |
Storage temp. |
2-8 °C |
Application
Gelatin methacryloyl (GelMA) is a hydrogel material derived from natural extracellular matrix components. Its affordability, abundance, and ability to retain cell binding motifs make it popular in tissue engineering.
Alginate, a naturally occurring polymer, finds extensive use in bioprinting due to its adjustable printability through polymer density changes and crosslinking using calcium chloride (CaCl2). Alginate is frequently combined with gelatin to enhance cell adhesion and promote differentiation.
Incorporating photocrosslinkable methacrylamide functional groups into GelMA enables the creation of biocompatible, biodegradable, and non-immunogenic hydrogels that remain stable under biologically relevant conditions and encourage cell adhesion, spreading, and proliferation.
The methacrylamide functional group not only contributes to rapid gelation but also offers the ability to regulate key physical characteristics of the hydrogel, including pore size, degradation rate, and swell ratio.
By adjusting the degree of functionalization and polymerization conditions, precise temporal and spatial control over the crosslinking reaction can be achieved. This flexibility enables the creation of hydrogels with distinct patterns, 3D structures, and morphologies.
Bioinks based on gelatin methacrylate have proven effective in 3D bioprinting, offering high printing resolution, shape fidelity, and excellent cell viability. These bioinks have been employed for bioprinting a diverse range of tissues and constructs, including osteogenic, chondrogenic, hepatic, adipogenic, vasculogenic, epithelial, endothelial, cardiac valve, skin, tumor, and various other tissue types.
Bioinks containing both gelatin and alginate have been effectively employed for 3D bioprinting, facilitating the creation of three-dimensional constructs using a variety of cell types, such as human mesenchymal stem cells (hMSC), embryonic stem cells (ESC), human umbilical vein endothelial cells (HUVEC), fibroblasts, and cancer cells.
Packaging
The product contains 10 ml of bioink packaged in a glass bottle.
Other notes
Some essential tips to achieve optimal bioprinting results are:
- Optimize printing condition: This includes adjusting parameters such as nozzle diameter, printing speed, printing pressure, temperature, and cell density.
- Reduce bubble formation. Air bubbles can disrupt the bioprinting process. Thus, handle the bioink with care when mixing and transferring it to avoid bubble formation. Avoid vigorous vortexing or shaking.
- UV light Crosslinking. Position the light source directly above the printed structure. The intensity of the light source affects the distance and exposure time required for crosslinking. For recommended conditions, place an 800 mW/cm2 light source approximately 8 cm above the printed structure and expose it for 30 to 60 seconds.
Procedure
- Prepare the bioink solution: Warm the TissueFab® - GelAlg-UV bioink in a water bath or incubator set to 37 °C for approximately 30 minutes or until the bioink becomes fluid. Gently invert the bioink to ensure it forms a homogeneous solution. Be careful not to vortex or shake the bioink vigorously.
- Prepare the bioink-cell solution: Resuspend the cell pellet at the desired cell density using the bioink solution. Gently pipette the mixture up and down to ensure even distribution. For extrusion-based bioprinting, a typical cell density ranges from 1 to 5 x 106 cells/mL. Load the bioink-cell solution into the printer cartridge of choice.
- Bioprint: For gelation, cool the loaded printer cartridge to below 23 °C, either by employing a temperature-controlled printhead or by placing the cartridge at 4 °C for a few minutes. If the 3D printer has bed temperature control, set it to 20 °C. Follow the manufacturer's instructions for the 3D printer. Attach the print cartridge to the 3D printer and begin printing directly onto a Petri dish or multi-well plates. Make flow adjustments based on nozzle diameter, printing speed, printing pressure, and temperature. For optimal results, print under a gentle flow of 200 mM CaCl2 solution. To maintain the CaCl2 solution flow, consider using a portable humidifier.
- Crosslink: For photocrosslinking, position the UV light source directly above the 3D-bioprinted structure and expose it to UV light at a wavelength of 365 nm. Adjust the distance and exposure time according to the bioprinter's specifications. For chemical crosslinking, introduce a solution of 100 mM CaCl2 in PBS and immerse the printed structure for 1 minute. Rinse it with PBS twice.
- Culture cells: To culture the bioprinted tissue, employ an appropriate cell culture medium, following standard tissue culture procedures.