The price and availability of drugs are frequent topics for debate. There is considerable tension between the sustainable cost of a therapy and expected returns on the high-risk investment associated with drug development.
Cost pressures intensify the need for better manufacturing efficiency and have increased the attractions of outsourcing and low-cost base geographies. Today’s pharmaceutical supply chains are complex and global. Safeguarding product quality and availability relies heavily on effective supply chain management and building resilience into manufacturing processes.
The advent of Quality by Design (QbD) in the early 2000s marked the beginning of an increased focus on manufacturing. QbD calls for a detailed understanding of the process and product, and the resulting knowledge provides a secure foundation for effective supply chain management and process troubleshooting. Manufacturers that invest in learning how to rigorously and reliably define materials that will process well have a valuable advantage that extends throughout the lifetime of the drug.
For powders - and many actives and excipients are handled in this form - it is flowability and other bulk properties, such as compressibility and permeability, that are often the critical differentiators of process performance, the properties that make one supply superior to another, or that elucidate a processing problem. This article explores the value of powder testing within this context referencing experience at GlaxoSmithKline (GSK), a leading global healthcare company.
A Strategy for Testing Alternative Supplies
Market specifications for a raw material, excipient or active define its quality and are necessarily met by any potential supplier. Supplies meeting the specification will perform their defined role in terms of delivering therapeutic efficacy. However, for powders, market specifications often fail to reflect manufacturing performance. Supplies that are equivalent in terms of producing an acceptable product may be substantially different in terms of process behaviour.
This situation is attributable to the failure of many powder specifications to capture an aspect of behaviour that affects process performance. Flowability is a prime example. The ease with which a powder flows can impact, for example, the time taken to blend to homogeneity, the efficiency of die-filling, and the throughput of a tablet press, but is rarely quoted in a specification. And where it is quoted the technique used may suffer from poor repeatability, be relatively insensitive and/or lack relevance, showing little correlation with process performance.
One way of addressing this issue is to negotiate a tightened specification with a supplier, if feasible, one augmented with additional requirements to ensure an optimal material. But this is potentially costly. The smarter, more flexible alternative is to use a more detailed understanding of material characteristics to learn how to handle different supplies more effectively and to identify and avoid those that are non-compliant, that cannot be processed to make a product of acceptable quality. This approach enables supply chain optimisation without incurring premiums that will ultimately elevate drug costs for the patient.
Differentiating Supplies
One of the powder processes operated routinely by GSK Consumer Healthcare is roller compaction; example applications include the production of Over-The-Counter (OTC) medicines. Through extensive powder testing, the company has established a database of properties for all materials regularly used in the manufacture of a range of OTC products. Central to the implementation of this testing strategy has been the FT4 Powder Rheometer®, an instrument that measures shear, bulk and dynamic powder properties to produce a comprehensive, multifaceted powder profile. Test data are used to evaluate new supplies, the consistency of an established supply and for process optimisation and troubleshooting. Correlations between process performance and powder properties streamline the identification of optimal processing conditions for powders with defined properties.
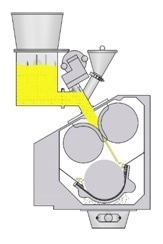
Figure 1: For roller compaction, a dry granulation process, compressibility is a critical powder property. Image Credit: Freeman Technology
This work has identified compressibility - change in bulk density as a function of consolidation pressure - as critical to roller compaction performance, and established correlations between compressibility and optimal compaction parameters. Highly compressible powders require a greater compaction force to produce a stable ribbon, and by extension, granules of acceptable quality. Having determined that one of the actives routinely processed by roller compaction had a compressibility of 5%, the company evaluated alternative commercial supplies of the same material to determine their suitability for the process. Compressibility testing revealed considerable variability between these supplies with respect to this critical characteristic.
One supply, with a compressibility of 10%, was readily processed by adjusting compaction parameters in line with the established correlations for the process, by processing at a higher compaction pressure than for the supply with 5% compressibility. However, a further supply exhibited the unexpectedly high compressibility of 25% and proved more problematic. Efforts were made to compact this powder by applying an exceptionally high compaction force, with the expectation of producing very hard granules, but in fact it was not possible to apply sufficient force to manufacture a stable ribbon. This value of compressibility defines a supply that cannot be processed, and the associated testing helps to further refine understanding of how to process viable materials. These results demonstrate the potential to use such measurements to differentiate commercial supplies.
Optimising Manufacturing Efficiency and Resilience
The preceding example highlights the role of powder testing in identifying a raw material that will fail to process. However, a more common problem, particularly with legacy products, is a gradual decline in manufacturing performance due to the selection of raw materials that do process, but sub-optimally. In the absence of a secure understanding of which properties influence process behaviour successive supplies may erode efficiency by being not quite the same as the original, with no way of identifying what the critical difference is. In the long term, the economic impact of this type of drift can be significant.
For example, a detailed study by GSK of a legacy tableting process revealed that over many years of operation tableting rate had declined by almost 50%. By applying the modern testing strategies outlined above, the company identified both compressibility and flowability as key powder properties for the tableting blends, and, on the basis of test data, defined specifications for materials that would return throughput to historical levels. As a result, a relatively modest investment in powder testing technology and analysis leveraged a major efficiency gain with the tester returning around 50 to 100 times its initial cost.
An alternative route to more efficient and resilient manufacturing may be the re-design of a problematic item of equipment. Here too, powder testing can be elucidating with in-house capability, judiciously applied, often helpful in solving long-standing problems. A final example from GSK illustrates alternative strategy.
Studies of hopper discharge efficiency in one the company’s processes revealed that at low levels the product became either super- or sub-potent due to segregation of the active from the bulk. Operational practice was therefore to discard a certain mass, towards the end of each batch, to safeguard product consistency.
The technique of shear cell testing was developed specifically to support a scientific approach to hopper design and can be applied using the FT4 Powder Rheometer®; integrated hopper design software can be used to design a new unit or check the design of an existing one1. GSK applied these capabilities to investigate the performance of the hopper and as a result replaced it with a new 55% larger unit with a different half angle and outlet size. Hopper design is often outsourced as an expert task, but these results were readily and efficiently generated in-house.
Video footage from inside the old and new hoppers shows a transformation in flow regime from a funnel flow pattern that induced rolling segregation at the hopper walls to the desirable mass flow, “first-in, first-out” regime associated with superior hopper performance. The new design exhibits no edge effect at the wall of the hopper, right up to the point of complete discharge, and despite being larger, empties faster. The waste saving associated with the change is in the region of 8% of each batch.
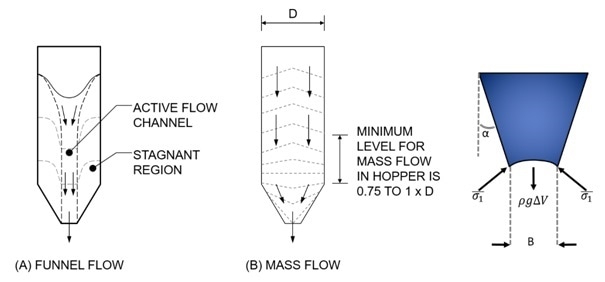
Figure 2: Changing the critical dimensions of a hopper - half angle (α) and outlet size (B) – can change the flow regime from funnel (A) to mass flow (B), a preferable state that results in first in first out powder discharge. Image Credit: Freeman Technology
In conclusion
Powder testing can be a powerful tool for a pharmaceutical and healthcare industry intent on building optimised, resilient manufacturing trains and secure supply chains. Modern powder testing instrumentation offers the sensitive, differentiating, multi-faceted characterisation required to build robust correlations between powder properties and process performance, and equally importantly allows testing to be brought in-house. Putting powder testing into the hands of those best-equipped to use the resulting data, to select better raw materials or to enhance equipment design, is a powerful strategy to support efficient pharmaceutical production.
References and Further Reading
- T. Freeman ‘Modern Tools for Hopper Design’ Available for download at: https://freemantech.co.uk/news/modern-tools-for-hopper-design
About Freeman Technology
Freeman Technology specialises in systems for measuring the flow properties of powders and has over 15 years’ experience in powder flow and powder characterisation. The company invests significantly in R&D and applications development, and provides detailed know-how to support its range of products. Expert teams guide and support users around the world in addressing their individual powder challenges, focusing on delivering the most relevant information for the process. The result is world-leading solutions for understanding powder behaviour - in development, formulation, scale-up, processing, quality control, or anywhere that powders have a role.
Freeman Technology’s solutions include the FT4 Powder Rheometer®, a uniquely universal powder tester, and the Uniaxial Powder Tester, a complementary tool for quick and robust powder assessment. Systems are installed around the world in the chemical, pharmaceutical, toners, foods, powder coatings, metals, ceramics, cosmetics, and many other industries. They deliver data that maximise process and product understanding, accelerating R&D and formulation towards successful commercialisation, and supporting the long term optimisation of powder processes.
Freeman Technology is also the global distributor for Lenterra sensor instrumentation which provides in-line, real-time flow measurement solutions to enhance process understanding, and improve manufacturing efficiency and quality.
Founded in 1989 as a developer of automated testing systems for materials characterisation, the company has focused exclusively on powders since the late 1990s and in 2018 became part of Micromeritics Instrument Corporation The company’s R&D, manufacturing and commercial headquarters are in Gloucestershire, UK, with operations and distribution partners in key global territories.
In 2007 the company received the Queen’s Award for Enterprise in Innovation and in 2012 the Queen’s Award for Enterprise in International Trade.
Sponsored Content Policy: News-Medical.net publishes articles and related content that may be derived from sources where we have existing commercial relationships, provided such content adds value to the core editorial ethos of News-Medical.Net which is to educate and inform site visitors interested in medical research, science, medical devices and treatments.