Several products from the food, chemical, or pharmaceutical industries are supplied in powder form.
These powders are prone to caking, which influences their quality and usage. In the majority of the examples, caking of powders is a result of the absorption of moisture from the environment.
The caking rate in powders and the factors that contribute to caking at different stages can be studied by utilizing powder rheometers.
Quantifying the Effect of Caking on Powder Flow - Freeman Technology
Causes of Powder Caking
Environmental elements that result in the caking of powders are humidity and temperature; changes in the latter cause the condensation of powder particles while changes in the former results in dissolution of the powder.
Mechanical caking of the powder can also be caused by the consolidation of powders throughout the process of testing. The powders must be placed under stringent testing in order to evaluate the onset and development of caking.
Contemporary powder testing techniques, for example the rheometer, are simple to function and offer efficient and helpful data regarding the characteristics of powder.
The information acquired indicates the effect of consolidation on the caking rate, which can be beneficial when choosing the most suitable storage and manufacturing conditions.
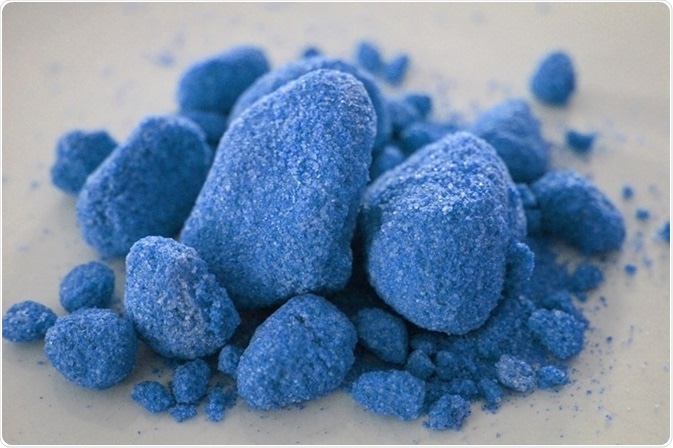
Image Credit: Freeman Technology
Testing Methods
Rheometers are very helpful in calculating the dynamic features of a sample and also allows the direct measurement of the flowability of a powder.
The Basic Flowability Energy (BFE) is the most critical baseline characteristic. This is the amount of energy required to rotate a blade that is submerged in the powder at a particular vertical and rotational speed.
Figure 1 demonstrates the rotational and axial forces performing on a blade.
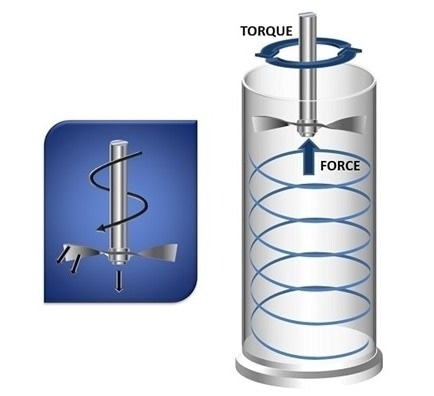
Figure 1. Measuring BFE with a powder rheometer. Image Credit: Freeman Technology
The BFE value can be quantified by automated test techniques and is the most vital parameter that provides a good understanding of the cohesive characteristics of the powder sample.
The caking of powders affects the value of BFE significantly for the reasons outlined below. Caking increases the inter-particle bonding which means that more energy is required to rotate the blade. If the caked sample is stiff, it will be more resistant to movement.
Caking produced by moisture absorption increases the sample’s bulk density which results in greater BFE values.
Effect of Consolidation on Caking
Several samples were subjected to the compacting stress of 9kPa, while the same amount of samples were left without consolidation in order to investigate the influence of consolidation on caking. In Figure 2, the test results of all samples with the related BFE values are demonstrated as a function of time.
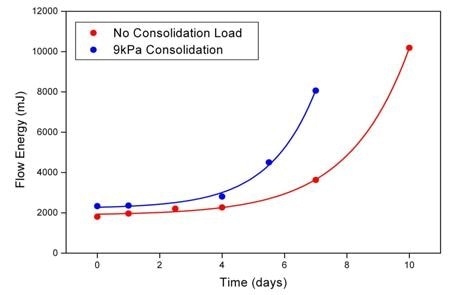
Figure 2. Investigating the impact of consolidation on caking by tracking changes in BFE as a function of time. Image Credit: Freeman Technology
It was noticed that in both of the samples, BFE increased at first over a period of four days. After four days, the consolidated sample demonstrated a significant increase in BFE.
The resistance displayed by the consolidated sample was double that of the first value after five and a half days. In comparison, the unconsolidated powder showed this amount of resistance just after eight days. The BFE value steadily increased in both of the samples.
The results suggest that it is more effective to store the powder after subjecting it to low stress, and the storage period should be limited to four days.
Practical Aspects to Controlling Caking
Discussed below are some practical solutions to manage caking. Running the bin with a small level of powder and topping it up frequently with small volumes is one suggestion.
This method decreases the amount of pressure applied to the material in the hopper and also reduces the amount of time that the powder is stored in the bin.
The time that the powder is kept in the bin is related to the flow within the bin; it decreases uniformly for powders running in a mass flow, but that is not the same for funnel flow.
Mass flow describes when all of the powder particles moving in the bin and the powder is taken out of the bin in a first in, first out sequence.
If a hopper has walls that are steeper than the limiting value, mass flow will occur. When such a hopper is not utilized, funneling will happen and the storage time of the powder becomes non-uniform. Figure 3 shows both of these flows.
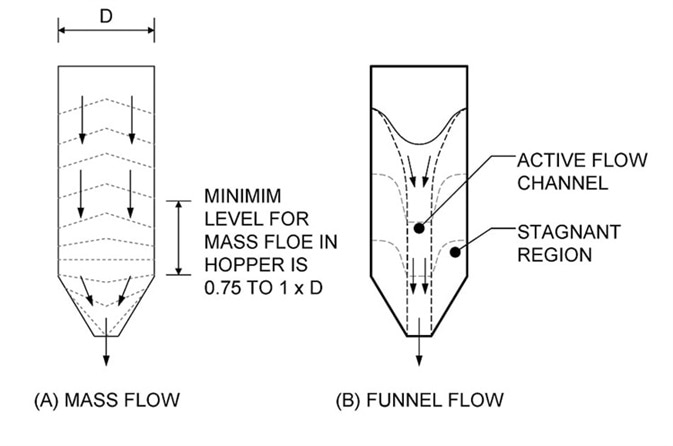
Figure 3. Comparing powder transit through a hopper under A) mass flow and B) funnel flow conditions. Image Credit: Freeman Technology
Caking is affected by the flow in the bin and additionally by the static storage of the powder.
Conclusion
It is evident from the above description how caking influences the performance of the powder and can limit its quality by a significant extent.
By utilizing effective testing techniques to establish the BFE, which offers information about the influence of consolidation and the extent of caking, chemical and process engineers can make more informed decisions on the correct manufacturing and storage techniques.
About Freeman Technology
Freeman Technology specialises in systems for measuring the flow properties of powders and has over 15 years’ experience in powder flow and powder characterisation. The company invests significantly in R&D and applications development, and provides detailed know-how to support its range of products. Expert teams guide and support users around the world in addressing their individual powder challenges, focusing on delivering the most relevant information for the process. The result is world-leading solutions for understanding powder behaviour - in development, formulation, scale-up, processing, quality control, or anywhere that powders have a role.
Freeman Technology’s solutions include the FT4 Powder Rheometer®, a uniquely universal powder tester, and the Uniaxial Powder Tester, a complementary tool for quick and robust powder assessment. Systems are installed around the world in the chemical, pharmaceutical, toners, foods, powder coatings, metals, ceramics, cosmetics, and many other industries. They deliver data that maximise process and product understanding, accelerating R&D and formulation towards successful commercialisation, and supporting the long term optimisation of powder processes.
Freeman Technology is also the global distributor for Lenterra sensor instrumentation which provides in-line, real-time flow measurement solutions to enhance process understanding, and improve manufacturing efficiency and quality.
Founded in 1989 as a developer of automated testing systems for materials characterisation, the company has focused exclusively on powders since the late 1990s and in 2018 became part of Micromeritics Instrument Corporation The company’s R&D, manufacturing and commercial headquarters are in Gloucestershire, UK, with operations and distribution partners in key global territories.
In 2007 the company received the Queen’s Award for Enterprise in Innovation and in 2012 the Queen’s Award for Enterprise in International Trade.
Sponsored Content Policy: News-Medical.net publishes articles and related content that may be derived from sources where we have existing commercial relationships, provided such content adds value to the core editorial ethos of News-Medical.Net which is to educate and inform site visitors interested in medical research, science, medical devices and treatments.