Continuous processing as described by the regulatory agencies is the pharmaceutical industry’s area of focus in order to enhance product quality and productivity.
It is essential to understand the correlation between the product features and the processing parameters to optimize continuous processing and gain the approval of regulatory agencies. This is a difficult task because the majority of traditional methods are ineffective for granule and powder analysis.
This article explains the application of Freeman Technology’s FT4 Powder Rheometer® and GEA’s ConsiGmaTM continuous high shear wet granulation and drying system to understand the relationship between granule features and differences in processing parameters and formulation in a continuous processing environment.
As part of the investigation, tablet manufacture was also investigated to specify the connection between granule characteristics and the key quality parameters of the tablets to acquire the data necessary for true Quality by Design (QbD).
Instrumentation
FT4 Powder Rheometer
Freeman Technology’s FT4 Powder Rheometer® (Figure 1) offers automated quantification of the properties of bulk materials. The extensive and reliable data is helpful to understand the influence of process and product development.
Many bulk material properties can be quantified by employing the universal powder tester. Along with analyzing flow properties, the rheometer is also supplied with a shear cell and can quantify bulk features like compressibility, density, and permeability.
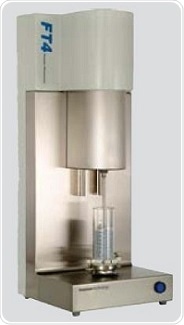
Figure 1. Freeman Technology’s FT4 Powder Rheometer®. Image Credit: Freeman Technology
ConsiGma-1
The ConsiGma-1 (Figure 2) is the laboratory-scale variation of the ConsiGma concept, including a patented continuous high shear granulator with a small dryer that can process samples of a few kilograms down to several hundred grams.
The instrument can continuously produce granules without significant shutdown and startup waste. Its integrated controls enable the production of granules with a range of features.
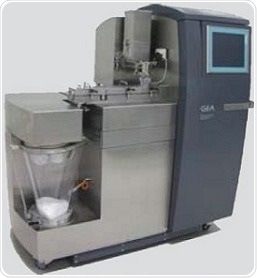
Figure 2. The ConsiGma-1. Photos courtesy of GEA Pharma Systems
The FT4 Powder Rheometer has become an essential tool to investigate the flow and caking behavior of our products.
Edgar Chavez, Group Leader, Nestle
Experimental Procedure and Results
To investigate the granule characteristics, a range of experiments were carried out on two basic powder formulations of dicalcium phosphate (DCP) and paracetamol (APAP) by changing the granulator screw speed, input powder feed rate, and the water content.
The reaction of the various materials to differences in processing parameters of the ConsiGma-1 is presented in Figures 3 and 4. Higher Basic Flowability Energy (BFE) is the consequence of a lower screw speed (Figure 3). BFE is the measure of the dynamic flow behavior of a powder or wet mass under investigation.
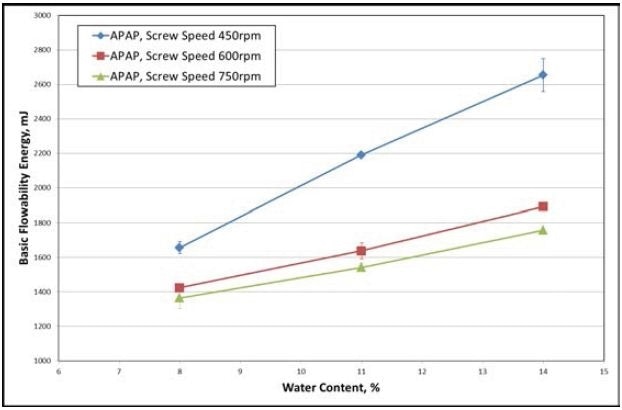
Figure 3. The data gathered from the APAP formulation shows increasing water content, which results in higher BFE for all screw speeds (for a fixed input feed rate of the powder). Image Credit: Freeman Technology
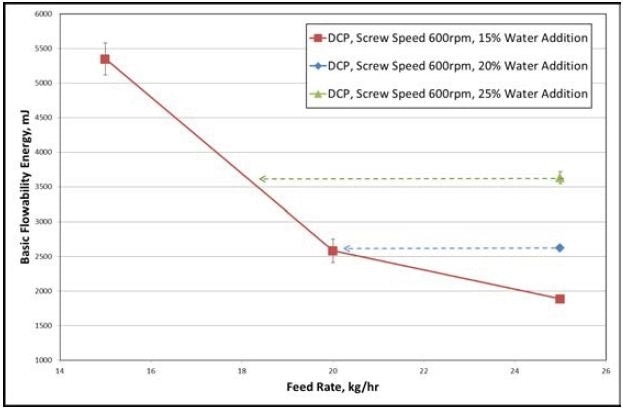
Figure 4. Results collected from the DCP formulation. Image Credit: Freeman Technology
Denser, larger, and more adhesive granules are a consequence of higher water content and lower screw speeds, offering a greater resistance to forced flow. BFE increases linearly in relation to water content, but not to screw speed.
An extensive reduction in the BFE can be seen in Figure 4 with an increase in powder feed rate. From the extra data, granules with similar features can be made at higher water contents by enhancing the feed rate.
Using the data acquired from two different substrates, granules with particular properties can be made by applying various combinations of water content, feed rate, and screw speed (Table 1).
Table 1. Generating granules of two different properties using a number of different process conditions. Source: Freeman Technology
Condition |
Process Parameters |
Granule Properties |
Screw Speed (rpm) |
Powder Feed Rate (kg/hr) |
Liquid Feed Rate (g/min) |
Moisture (%) |
BFE – Wet Mass (mJ) |
BFE – Dry Granules (mJ) |
BFE – Milled Granules (mJ) |
BFE – Lubricated Granules (mJ) |
1 |
450 |
11.25 |
15.0 |
8.0 |
2217 |
1623 |
1283 |
1526 |
2 |
750 |
20.0 |
36.7 |
11.0 |
2133 |
1973 |
1463 |
1417 |
3 |
450 |
6.0 |
20.0 |
20.0 |
3172 |
4610 |
2268 |
1761 |
4 |
750 |
9.0 |
30.0 |
20.0 |
3342 |
4140 |
1951 |
1795 |
Conditions 1 and 2 had BFE values of around 2200 mJ while evaluating the wet mass, whereas the BFE of Conditions 3 and 4 created values of around 3200 mJ.
During the development of the granules in the production system, the related BFE values continue to be consistently grouped. The BFE values for Conditions 3 and 4 are greater than those for Conditions 1 and 2 (Figure 5).
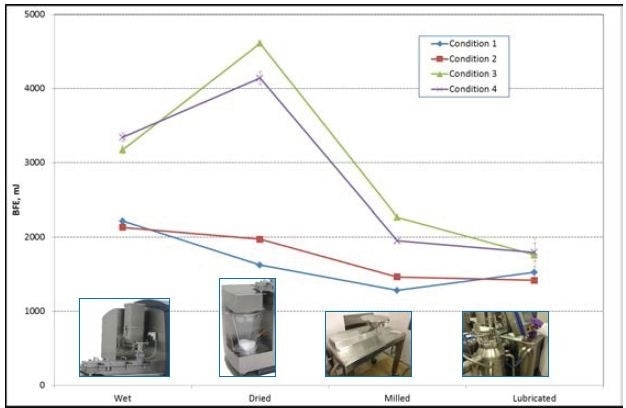
Figure 5. BFE values for Conditions 1, 2, 3, and 4. Photos courtesy of GEA Pharma Systems
The results show that manufacturing environments impact the properties of the granule and there are a range of manufacturing routes available to produce the granule quality desired.
These results are essential for the process engineer, formulation scientist, and equipment designer as it offers further choices to advance formulation or unit operation combinations in order to produce products with the intended quality.
It is even more meaningful to determine the correlation between the final product (tablet form) features and the granule characteristics.
For this reason, the four granule batches (lubricated, milled, dried, and wet) were pressed into tablet form utilizing a GEA ModulTM S rotary tablet press (Figure 6).
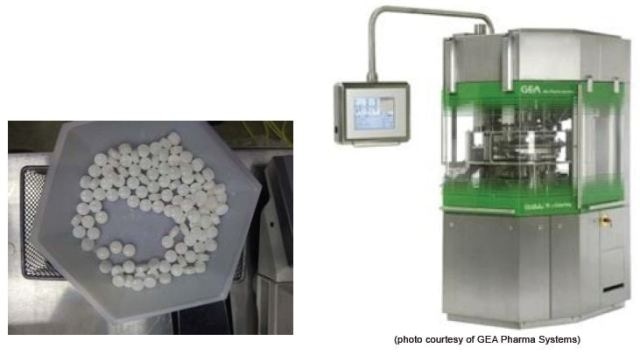
Figure 6. GEA ModulTM S rotary tablet press. Photos courtesy of GEA Pharma Systems
A Dr. Schleuniger Pharmatron 8M tablet hardness tester was employed to quantify the strength of the resulting tablets.
For the milled and dried granules, the relationship between the hardness of the tablet and the BFE is very strong with an R2 value > 0.99 (Figure 7).
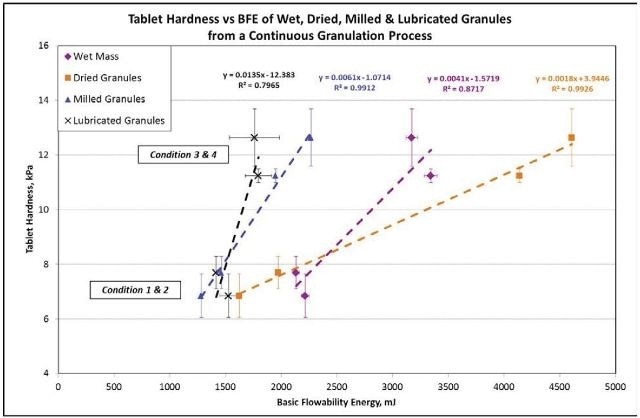
Figure 7. The correlation is extremely strong between tablet hardness and the BFE for the dried and milled granules with an R2 value of greater than 0.99. Image Credit: Freeman Technology
For the lubricated granules and wet mass, the correlation is not as significant because of the presence of water and lubricant, which greatly impact the bulk flow characteristics, regardless of their low concentrations.
Conclusion
The quantification results of BFE verify that there is a direct correlation between the bulk flow characteristics of the granules. This information is also beneficial in the production of scaling measures for processes involving batch granulation.
Once a particular BFE has been established as providing the optimal critical attribute for the final tablet, it is no longer a requirement to focus on particular operational conditions or instrument types.
The quality of the tablet can be ensured as long as the wet granule attains the intended BFE value.
The results of the investigation demonstrate the potential to create tablets with desired properties by using different combinations of process parameters.
This is an important step in the process for a full Design Space specification. Investigations in the future will verify the relationship between the granule features and further CQAs of the final tablet, such as content uniformity, dissolution, and weight variation.
About Freeman Technology
Freeman Technology specialises in systems for measuring the flow properties of powders and has over 15 years’ experience in powder flow and powder characterisation. The company invests significantly in R&D and applications development, and provides detailed know-how to support its range of products. Expert teams guide and support users around the world in addressing their individual powder challenges, focusing on delivering the most relevant information for the process. The result is world-leading solutions for understanding powder behaviour - in development, formulation, scale-up, processing, quality control, or anywhere that powders have a role.
Freeman Technology’s solutions include the FT4 Powder Rheometer®, a uniquely universal powder tester, and the Uniaxial Powder Tester, a complementary tool for quick and robust powder assessment. Systems are installed around the world in the chemical, pharmaceutical, toners, foods, powder coatings, metals, ceramics, cosmetics, and many other industries. They deliver data that maximise process and product understanding, accelerating R&D and formulation towards successful commercialisation, and supporting the long term optimisation of powder processes.
Freeman Technology is also the global distributor for Lenterra sensor instrumentation which provides in-line, real-time flow measurement solutions to enhance process understanding, and improve manufacturing efficiency and quality.
Founded in 1989 as a developer of automated testing systems for materials characterisation, the company has focused exclusively on powders since the late 1990s and in 2018 became part of Micromeritics Instrument Corporation The company’s R&D, manufacturing and commercial headquarters are in Gloucestershire, UK, with operations and distribution partners in key global territories.
In 2007 the company received the Queen’s Award for Enterprise in Innovation and in 2012 the Queen’s Award for Enterprise in International Trade.
Sponsored Content Policy: News-Medical.net publishes articles and related content that may be derived from sources where we have existing commercial relationships, provided such content adds value to the core editorial ethos of News-Medical.Net which is to educate and inform site visitors interested in medical research, science, medical devices and treatments.