An important element of many manufacturing processes in the pharmaceutical industry is the blending of a small amount of Active Pharmaceutical Ingredient (API) with a bulk excipient, and then subsequently processing this through a range of unit operations.
The way that the blend performs in downstream processes will be a function of the characteristics of the components of that blend.
When formulations are manufactured to be delivered in the form of a capsule, the blend needs appropriate features to ensure an accurate and precise fill of the dosing capsule.
A fundamental part of Quality by Design (QbD) is the ability to characterize formulations regarding their process behavior.
The technique used to quantify the characteristics of powdered formulations in order to promote effective performance in a dosator must enable a design space to be defined and determine the material properties that will produce final products of a high quality.
This will offer extensive commercial advantages such as decreased wastage and higher productivity.
Performance Variation Between Similar Formulations
Three powdered formulations were utilized in the creation of a DPI product. Variations in the final product’s quality were measured according to which formulation was utilized.
Of the three formulations, Formulation 1 demonstrated average behavior regarding filling performance from the dosator. Formulation 2 exhibited the worst behavior and Formulation 3 offered the best.
Samples from the three formulations were analyzed employing an FT4 Powder Rheometer®. The tests evaluated the bulk, shear, and dynamic features of the samples as a means to understand trends that were related to the performance of the dosator.
Test Results
Dynamic Testing: Specific Energy
Formulation 3 had the lowest specific energy of the three materials, whereas Formulation 2 had the highest.
High specific energy indicates a higher degree of mechanical interlocking and friction inside of the bulk, normally resulting in problems in operations like filling, where gravitational flow is essential.
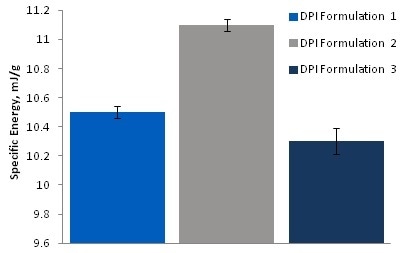
Image Credit: Freeman Technology
Bulk Testing: Compressibility
Formulation 3 was the least compressible of the samples, whereas Formulation 2 was the most compressible. High compressibility shows that a powder entrains a larger proportion of air within its bulk, which is a feature normally observed in more cohesive powders.
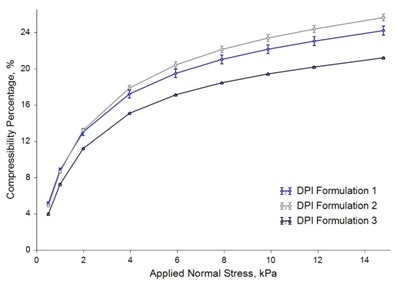
Image Credit: Freeman Technology
Shear Cell Testing
Minimal differentiation was seen across the three samples, with six data sets, for example two repeats on every sample, producing almost identical shear stress values to within a sufficient standard deviation.
This absence of correlation with the process behavior shows how shear cell testing, created to evaluate how a powder develops from a static to dynamic state after consolidation, may not be appropriate to the more dynamic, low-stress conditions that a powder is subjected to in the dosing process.
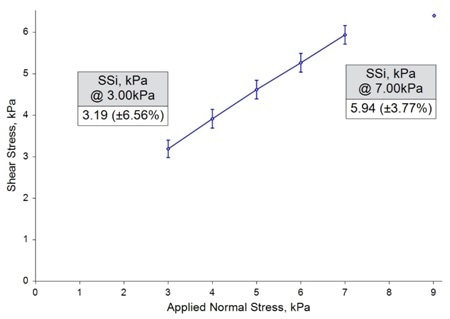
Image Credit: Freeman Technology
Conclusions
The FT4 has established repeatable and clear differences between three similar formulations which matched well to the relative performance seen in the dosator.
Specific energy and compressibility were demonstrated to be highly differentiating which indicates that mechanical interlocking or friction and the packing structure of the powder bed have the most impact on process performance.
The shear cell test offered minimal information which suggests that shear properties had little to no impact on the total performance.
The bulk and dynamic parameters can be employed to make a design space of process-relevant measurements, which can be utilized as a template for formulations in the future and allows process behavior to be confidently predicted.
Powder flowability is more about the ability of powder to flow in a desired manner in a particular piece of equipment rather than being an inherent material property.
Effective processing requires that the process and the powder are well-suited and it is common for the same powder to function well in one process but perform inadequately in another.
This means that multiple characterization techniques are necessary, the results from which can be matched with process ranking to construct a design space of parameters that relate to sufficient process behavior.
Instead of depending on single number characterization to outline behavior throughout all processes, the FT4’s multivariate method simulates various unit operations, enabling the direct investigation of a powder’s response to a range of environmental and process conditions.
About Freeman Technology
Freeman Technology specialises in systems for measuring the flow properties of powders and has over 15 years’ experience in powder flow and powder characterisation. The company invests significantly in R&D and applications development, and provides detailed know-how to support its range of products. Expert teams guide and support users around the world in addressing their individual powder challenges, focusing on delivering the most relevant information for the process. The result is world-leading solutions for understanding powder behaviour - in development, formulation, scale-up, processing, quality control, or anywhere that powders have a role.
Freeman Technology’s solutions include the FT4 Powder Rheometer®, a uniquely universal powder tester, and the Uniaxial Powder Tester, a complementary tool for quick and robust powder assessment. Systems are installed around the world in the chemical, pharmaceutical, toners, foods, powder coatings, metals, ceramics, cosmetics, and many other industries. They deliver data that maximise process and product understanding, accelerating R&D and formulation towards successful commercialisation, and supporting the long term optimisation of powder processes.
Freeman Technology is also the global distributor for Lenterra sensor instrumentation which provides in-line, real-time flow measurement solutions to enhance process understanding, and improve manufacturing efficiency and quality.
Founded in 1989 as a developer of automated testing systems for materials characterisation, the company has focused exclusively on powders since the late 1990s and in 2018 became part of Micromeritics Instrument Corporation The company’s R&D, manufacturing and commercial headquarters are in Gloucestershire, UK, with operations and distribution partners in key global territories.
In 2007 the company received the Queen’s Award for Enterprise in Innovation and in 2012 the Queen’s Award for Enterprise in International Trade.
Sponsored Content Policy: News-Medical.net publishes articles and related content that may be derived from sources where we have existing commercial relationships, provided such content adds value to the core editorial ethos of News-Medical.Net which is to educate and inform site visitors interested in medical research, science, medical devices and treatments.