The latest version of Instron’s Autoinjector Testing System was developed in close collaboration with CDMOs and pharmaceutical device manufacturers. It can perform thorough functioning testing on various drug delivery devices, such as safety syringes, button-activated devices, and needle shields.
This system’s important performance criteria are cap removal, dosage accuracy, activation force, injection length, needle depth, click detection, and needle guard lockout. By doing so, laboratories can meet both internal quality requirements and international standards such as ISO 11608.
Autoinjector Testing System | Semi-Automated System for Testing Pen and Autoinjectors to ISO 11608
Video Credit: Instron - USA
Get in touch now
All-In-One Solution
The Autoinjector Testing System replaces conventional test procedures, which sometimes require many pieces of equipment. This enables producers to reduce time to market by allowing customers to do a whole test sequence on a single machine.
- Reducing the time and devices required to complete testing
- Spending less on specimens, maintenance, and testing equipment
- Streamline the procedures of data aggregation, analysis, and validation
- Enhancing technology transfer to production facilities

Image Credit: Instron - USA
Full functionality testing
Run a complete sequence of tests on a single system

Image Credit: Instron - USA
Activation force
The system activates the device and calculates the force required to initiate injection.
Needle depth
The machine vision camera captures images at the beginning and end of the injection.
Click detection
A microphone detects an audible click during injection activation and needle removal.
Delivered volume
The fluid that has been ejected is weighed on a precise scale.
Injection time
A machine vision camera computes the entire time fluid in its field of view.
Needle guard lockout
The system loads the test device with a specified lockout force or until the defeat force is reached.
Dedicated test methods
Autoinjector Testing System | Simple Test Methods
Video Credit: Instron - USA
Bluehill® Universal uses more accessible test types, allowing users to quickly develop and alter method parameters while also providing the ability to add future devices without the need for Instron’s support. Users can choose the appropriate functional tests (cap removal, injection, and needle shield safety check) and insert their own parameters.
The system automatically runs the tests in the correct order, minimizing test time and ensuring consistency. The software has pre-loaded templates, allowing users to rapidly and easily create a new device method and begin testing.
- Quickly and easily establish a new device technique and begin testing
- Improved testing consistency among operators
- Flexibility to modify procedure parameters as needed
- Templates are preloaded for two-step, three-step, and safety syringe devices
System suitability testing

Image Credit: Instron - USA
The Autoinjector Testing System includes system suitability testing into the testing process by automatically prompting users to carry out admin-defined daily checks on the load cell, machine vision camera, and scale in compliance with internal rules and Good Manufacturing Practices.
The system’s audit trail preserves the results, facilitating compliance with FDA 21 CFR Part 11 and other accrediting body requirements.
- Control over what is checked and how often
- Ability to prevent system use until all system checks are finished
- Traceability is required to meet audit criteria
- Easy-to-use hardware kit accelerates the evaluation process
Get in touch now
Advanced camera capabilities
Optical measurements

Image Credit: Instron - USA
The autoinjector testing system comprises a machine vision camera that accurately monitors injection time and detects exposed needle depth at the beginning and end of the injection.
Root cause analysis

Image Credit: Instron - USA
A high-resolution video camera and a machine vision camera provide critical visuals for properly interpreting test results, making it easier to determine if a poor result was caused by a device failure or a mistake in the testing technique.
Device flexibility

Image Credit: Instron - USA
The autoinjector testing fixtures were designed to eliminate side loading during cap removal, support standard industry device forms, and accommodate bespoke devices.
- Increased flexibility and efficiency for testing several device types
- Easily create additional inserts to fit future devices
- Reduced variability in test results
- Simplified alignment
Safer
Light shield
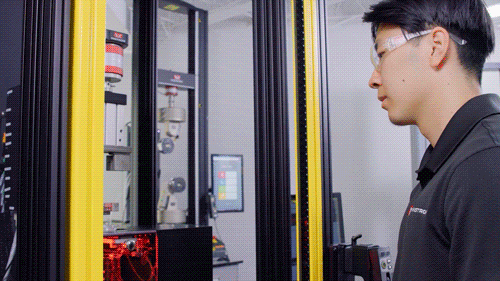
Image Credit: Instron - USA
Debris shields surround the testing system on three sides and a light barrier in the front, which prevents the machine from running when the operator is physically present in the test room. A physical door can be installed in the front to enclose the testing system.
Smart-close air kit and e-stop

Image Credit: Instron - USA
The pneumatic-powered upper and side grips employ the 6800 Series smart-close air kit technology, which allows customers to save preferred grip pressure settings in the test method and assures consistency between tests. The air kit is fully integrated with the system's emergency stop, which allows the grips to disengage when the E-Stop is activated.
Operator protect

Image Credit: Instron - USA
The autoinjector testing system uses Instron's patent-pending Operator Protect architecture. This intelligent procedure ensures equipment and operator safety by monitoring system status from setup to test completion. The built-in safety coaching consistently provides clear visual feedback on system status.
Get in touch now
System validation
Instron offers a complete turnkey solution, including goods and services, to help testing facilities accelerate their in-house validation procedures and employ their autoinjector testing equipment.
Traceability
Instron® | Traceability Module in Bluehill® Universal Software
Video Credit: Instron - USA
Bluehill Universal's Traceability module assists users in complying with audit regulations such as FDA 21 CFR Part 11, ISO 17025, Nadcap, and so on. This advanced add-on effortlessly integrates electronic approvals, an automatic audit trail, and Bluehill's built-in security to provide unsurpassed data traceability.
Centralized lab management
Bluehill® Central | Lab Management Software from Instron®
Video Credit: Instron - USA
Users can manage tech transfer and ensure that all sites use validated test methods by integrating Bluehill Central software. This laboratory management system offers centralized, remote management of Bluehill Universal software applications associated with different Instron test frames.
This software allows remote management of all Bluehill Universal users, test templates, results, file revision approvals, and audit trail data from several Instron systems.
On-site calibrations

Image Credit: Instron - USA
The Autoinjector Testing System, which measures needle depth, speed and displacement, and tension and compression force, can be calibrated on-site by Instron Professional Services. These services confirm that the results are computed accurately and that the testing parameters are met.
IQOQ Validation

Image Credit: Instron - USA
Software validation is necessary to guarantee adherence to ISO 13485 and FDA 21 CFR Part 820, also called the Quality System Regulation (QSR). Certified Instron Field Service Engineers complete vendor Installation Qualification and Operational Qualification (IQOQ) documentation on-site for Instron.
This validation ensures that the Instron testing device has been set up correctly, is suitable for its intended usage, and can yield reliable results. The knowledgeable service staff at Instron use their tested documentation bundle, which consists of instructions, reference files for calculation validation, and pertinent IQOQ documents.