Sponsored Content by MecmesinOct 18 2017
Introduction
Bespak is an leader in specialty medical devices for anesthesia and inhaled drug delivery. Each year, the company produces over 450 million complex devices, most of which include inhalers that are used to administer exact metered doses of aerosolized medicine or dry powder to patients suffering from conditions like: chronic obstructive pulmonary disease, asthma, and other related illnesses.
The operating mechanism of these complex devices is based on a key element — tensile and compressive helical springs. As a supplier quality control measure, Bespak conducts free tensile/compressive force tests as well as height tests on the springs in order to comply with specifications.
These tests are critical to ensure that the resultant device will work correctly. Each week, the springs, which vary in length between 20 and 120 mm, are delivered in 6 deliveries to Bespak's King's Lynn site based in the UK. From each batch 30 to 50 samples have to be tested.
Earlier, this process was carried out with a gauge placed on a test stand, which was operated manually. However, the Bespak quality control team observed that this set-up does not meet their requirements and that a more advanced testing system can fix this problem.
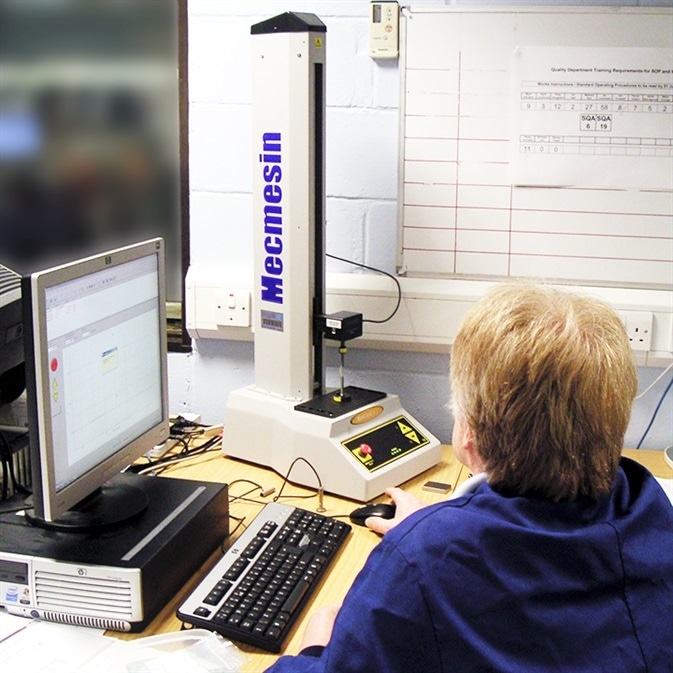
Testing-medical-springs
Solution
Bespak was supplied with a MultiTest 1-i computer-controlled force testing system from Mecmesin, equipped with a 50N Loadcell. Integrated with the powerful Emperor™ software from Mecmesin, the system allowed for complete automated control of all the test parameters eliminating inaccuracies resulting from manual force application.

Spring-compression-fixtures
A compression test is carried out by loading the spring on custom-made alignment pins. The loadcell, which is mounted on the automated crosshead of the testing system, subsequently moves down at a steady rate. It first stops to record the free height of the spring and then proceeds to the specified test height, simultaneously taking 2000 readings per second to correctly map the compression profile of the spring.
For further analysis, the results are sent to Microsoft® Excel and later uploaded onto Bespak's quality module in SAP for storage. Next, force profile charts are saved in the Emperor™ software for viewing at a later time.
System
MultiTest 1-i, equipped with a 50N Loadcell, was used in this procedure. (Superceded by OmniTest 1 universal testing machine).
Testimonial
We have used Mecmesin equipment for a number of years to perform compression and tension tests on helical springs intended for use in our respiratory drug delivery devices. We now estimate that every second, more than a thousand people reply on a Bespak device to help them breathe and as our testing requirements have grown, so too has our relationship with Mecmesin. Today we use their computer-controlled test systems to guarantee the quality of our supplied materials.”
Peter Haken, Quality Engineer, Bespak plc.
About Mecmesin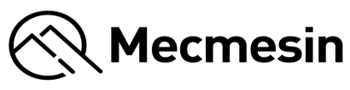
Established in 1977, Mecmesin is a global brand renowned worldwide for delivering reliable, affordable and innovative force, materials, and torque testing equipment for quality control.
Mecmesin is part of the Physical Properties Testers Group (PPT Group), a multi-national group of brands expert in the design and production of solutions for testing a range of physical properties including compression, light fastness, moisture, dry rate, water repellency, abrasion, flammability, texture, tensile and torque properties.
The PPT Group has regional offices in the UK, France, Germany, the USA, Thailand and China. The Mecmesin brand is also supported by a global network of distributors in more than 50 countries able to provide technical expertise and after-sales support to customers locally.
The focus of the brand has always been to provide high-quality test solutions, which are an affordable alternative to the many higher-priced systems available, enabling small and large businesses alike to undertake quality control checks on their products without compromising on precision and accuracy.
The rugged design of these systems means they can withstand tough factory conditions and perform tests at the point of production rather than having to use expensive laboratories to ensure consistent manufacture.
Sponsored Content Policy: News-Medical.net publishes articles and related content that may be derived from sources where we have existing commercial relationships, provided such content adds value to the core editorial ethos of News-Medical.Net which is to educate and inform site visitors interested in medical research, science, medical devices and treatments.