Sponsored Content by MecmesinOct 18 2017
The importance of reliability and quality of medical devices cannot be over-estimated, as the lives, safety, and well-being of patients are at great risk and the industry is closely regulated. Therefore, medical devices are an area of well-established scrutiny and standards.
Suppliers and manufacturers alike have to be very careful, because harm born from unexpected circumstances can result in legal action against manufacturers, suppliers, clinicians, and users.
It is estimated that the world’s vast medical devices industry will reach $398 billion annually by the year 20171. This extensive industry includes basic mass-produced components, new materials development, and highly advanced one-off products. However, for everyone concerned, a major part of the quality assurance (QA) testing process depends on pulling, pushing, and twisting.
Production Quality
While that may sound simple, many unforeseen events can occur during the course of torque or force application. On the production floor, continuous and repeatable testing of samples can help detect manufacturing quality drift, and this information can be fed back to take corrective action before a line goes out of the preset tolerances.
On the production line, the right tests are chosen and programmed into torque and force testers, and they reliably execute the same test every time. However, the question at this juncture is what exactly is the right test?
There are well-established international standards for all medical devices to make sure that these products are sufficiently sharp and strong; peel and adhere consistently; as well as stretch, bend or click in accordance with specification.
It may sound very simple to determine and evaluate for quality and at one level it actually is. If users have a universal force tester, which is fixtured to hold the item under consideration, all they have to do is to drop in the sample, begin the test, and then take the sample out.
An instant response can be indicated to pass/fail the sample, while the raw test data for each batch is stored for analysis and comparison at a later time and to provide a detailed audit trail.
International standard test methods apply to standard components, as these components are not subject to many design changes over time - some examples are provided in brackets in the following list, below:
- Will an infusion tube get disconnected from a coupling within the expected limits of pressure or force (ISO 80369-1)?
- Will a single-use needle batch enter the skin easily every time (BS EN 11608, BS EN ISO 7864), and is the sharps bin that is placed in resistant to puncture (BS7320, ASTM F2132)?
- Is a syringe’s plunger-activation force consistent with the need for a syringe pump (BS EN ISO 7886-1)?
- Will bone screws drive in cleanly and accomplish the right torque (BS 3531-5.6, ASTM F543, ISO 6475)?
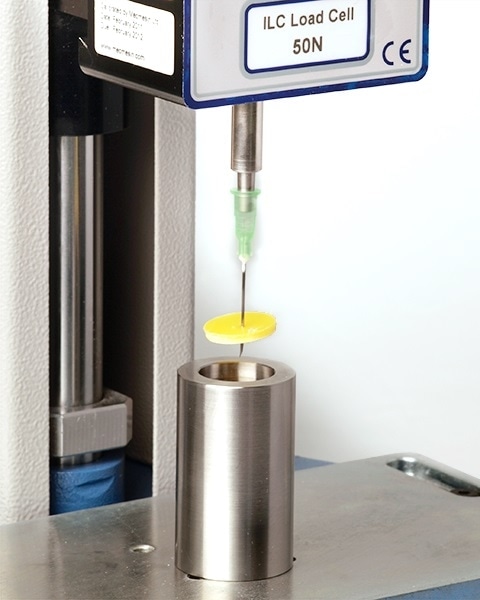
Precision measurement
Thus, there are thousands of QA checks which are easily carried out like these in repeatable ways — using international standard methods and universal testers to apply tensile and compressive forces or torque. Fully programmable testers can be used to acquire significant amounts of information and therefore, they are used from the design phase through to the production phase.
At times, there is a need for a single measure, for instance, a break point or a peak force, but most often the comprehensive characteristics of a test to release, or a test to failure, provides more valuable data. This may be needed for analysis or as proof, if concerns are raised about a product’s performance.
Precision Measurement
The Luer lock (ISO 594, BS EN 20594-1, BS EN 1707) is a ubiquitous and simple-looking product. It is specifically developed to provide leak-proof and secure connections, but also designed for rapid application and release of syringes to needles (BS EN ISO 11608-2).
Every year, billions of these devices are used, but the patient may experience more than a little pain if their vein is traumatized by sub-optimal performance of one. The problem is caused by production quality drift, that results in a costly and damaging batch recall, rather than by the one-off substandard product.
When test data is plotted a thousand times a second, it becomes easy to observe how things fail or deform, and as a result better designs can be developed. This is particularly critical in the case of novel materials and devices. During the design and manufacture of medical devices, weight reduction and materials saving are some of the common pressures that are faced, but in addition to these, safety factors are considered to be even more challenging.
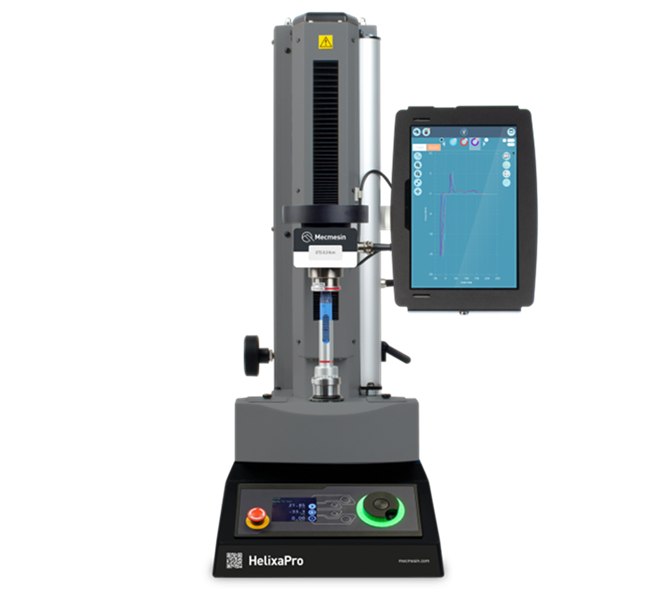
Defects in a Luer screw thread can be detected with an appropriate high-precision torque tester, which can measure down to a few mN∙m. Such defects can be traced back to the production process and corrected before it turns into a major issue, while being able to test to failure.
While a Luer fitting can be developed for light application, a strong hand is still likely to overdo it. As such, a sophisticated torque tester is needed to capture the finest torque properties at the point of releasing or securing the fitting, while it is simultaneously under the representative axial pull or push forces.
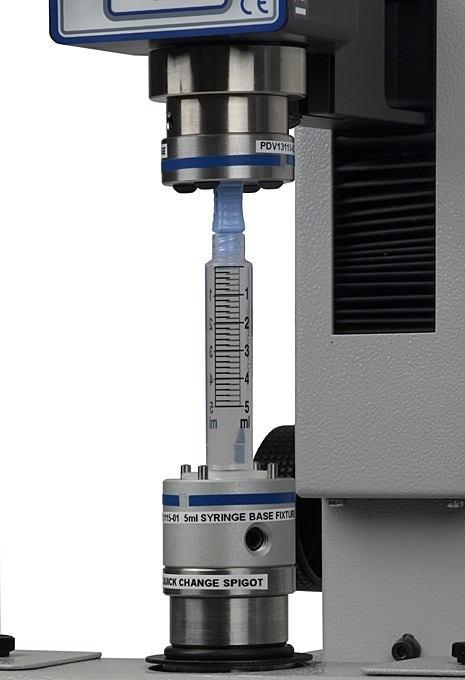
Measuring the loaded torque of a Luer lock.
Patient Drug Delivery
Pharmaceutical delivery has always trended towards patient application, partly to save the time of medical specialists and partly for the convenience of the patient. As a result, single-use devices such as prefilled syringes, inhalation devices, dose-controlled injectors, and transdermal patches are employed by patients, but often this application is less consistent than that by trained professionals.
A critical element is dose-delivery, which depends on an assembly of mass-produced components, such as plastic components, triggers, buttons, springs, and dials. Batch sample testing has to be performed on each of these components, because failures (for instance, a spring with not quite enough strength) may not necessarily result in fast detection of over or under-dosing.
Simple mechanical force testers can accurately determine measure spring rates, but programmable motorized testers can considerably boost throughput and provide the flexibility of storing a library of tensile and compression test routines for a wide range of springs.
New Developments
At the other end of the spectrum, there are custom-made devices or those uniquely designed to suit individual needs; where it is vital to test prototypes to failure, or where the strength of the end product has to be tested without damaging it.
This is common with products like carbon composite prosthetic limbs, bionic devices, and replacement implants or joints, which may seem like other advanced engineering solutions, but malfunction and failure can lead to a serious injury. Therefore, accurate, detailed, and repeatable testing is important.
New instances in the field of additive manufacturing (3D printing) comprise of maxillofacial prostheses which require lightness and strength, channels for nerves, and cavities for muscle attachment. These devices are radical, complex, irretrievable, and permanent and have to be validated in both design principle and material suitability.
The mechanical needs are known; the joint stress forces can be determined, and titanium material can be evaluated against bone for strength and density. However, additive manufactured metals are different from wrought or cast equivalents.
The benefits of these metals are they are a single integrated component, generally stronger but less ductile, and can have residual stresses. By contrast, prostheses produced in a conventional way may either need reworking or multi-part assembly, with different weakness points.
If the same components, produced by different methods, are subjected to comparative testing, they can provide important information on the right manufacturing method for a specific application, based on where exactly it is required in the body.
A computerized universal compression and tensile tester that can test for break point, flexure, pull-out of fixings, and tensile strength will put a part design through its paces, and also in the details of the data, will detect points of possible weakness.

Computerized Force Testing Profiles Human Joints for Prosthesis Development
New coatings, cements, and adhesives (ASTM F1160, F2256, F2258, ASTM F2255) in medical devices is another area where testing has to be performed. In the case of external devices, traditional forms should be resilient to their predicted environment such as fluids, solvents, temperature and so on, but other factors are involved when employed internally.
For instance, the adhesive for a transdermal patch can be easily user-tested, as effectively as in standardized conditions, as reapplication is easy and samples with inactive ingredients can be used. In a similar way, a new wound-closing adhesive (ASTM F2458), used as an alternative to staples or sutures, can be applied externally in vivo where alternative tested solutions can be rapidly used in the event of failure.
However, detailed testing for internal components such as those for heart valve repairs, which are used during complicated surgery cannot allow for failures as they can prove to be catastrophic. Therefore, to test for potential flaws, stringent tensile testing on synthetic or wet cultured skin can be carried out in conditions that are highly monitored and controlled.
A universal tester can cyclically and programmatically test peel, shear and tensile strength properties with various formulations under the same conditions. Further, the repeatability of the test method as well as conditions provides reliable data that is not afforded by in vivo testing.
Conclusion
The variability faced during quality testing of medical devices and components can be eliminated through fully programmable force and torque testers. These testers use a library of custom test methods and international standards to execute an array of procedures, right from the production floor to the specialist design laboratory.
Materials and medical device innovation require comprehensive analysis of the mechanical performance of parts and components, as their application is crucial and highly regulated for safety compliance.
References
1 Visiongain (2013), Medical Devices Industry and Market Prospects 2013-2023
About Mecmesin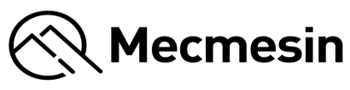
Established in 1977, Mecmesin is a global brand renowned worldwide for delivering reliable, affordable and innovative force, materials, and torque testing equipment for quality control.
Mecmesin is part of the Physical Properties Testers Group (PPT Group), a multi-national group of brands expert in the design and production of solutions for testing a range of physical properties including compression, light fastness, moisture, dry rate, water repellency, abrasion, flammability, texture, tensile and torque properties.
The PPT Group has regional offices in the UK, France, Germany, the USA, Thailand and China. The Mecmesin brand is also supported by a global network of distributors in more than 50 countries able to provide technical expertise and after-sales support to customers locally.
The focus of the brand has always been to provide high-quality test solutions, which are an affordable alternative to the many higher-priced systems available, enabling small and large businesses alike to undertake quality control checks on their products without compromising on precision and accuracy.
The rugged design of these systems means they can withstand tough factory conditions and perform tests at the point of production rather than having to use expensive laboratories to ensure consistent manufacture.
Sponsored Content Policy: News-Medical.net publishes articles and related content that may be derived from sources where we have existing commercial relationships, provided such content adds value to the core editorial ethos of News-Medical.Net which is to educate and inform site visitors interested in medical research, science, medical devices and treatments.