Continuous manufacturing is where a product is produced non-stop in one uninterrupted process and is used widely in sectors such as commodity chemicals, automotive, food, and electronics. In contrast, the pharmaceutical industry with its complex chemistry requirements has traditionally operated batch manufacturing which involves multiple steps and ‘hold’ times between steps.
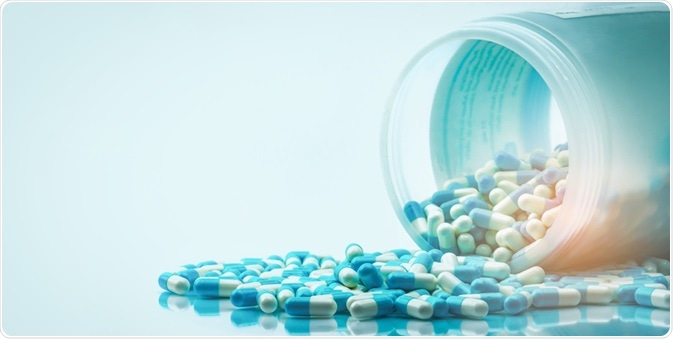
Image Credit:Shutterstock/Fahroni
However, in the last few years, the pharma industry has been moving towards continuous manufacturing, thanks to improvements in technology. The US Food and Drug Administration (FDA) is actively encouraging the implementation of emerging technologies, including continuous manufacturing, to improve product quality and address many of the underlying causes of drug shortages and recalls [1].
Continuous monitoring saves time, reduces the risk of human error, and allows the manufacturer to respond more quickly to market changes, for example, if demand increases, the process can run for a longer time [1]. Another advantage is that continuous manufacturing processes typically use automated monitoring techniques and predictive maintenance. What’s more, tracking and tracing material is more flexible with continuous manufacturing, allowing manufacturers to find contaminants or defective materials more efficiently.
The Advantages of Raman Spectroscopy
Raman spectroscopy has long been used in R&D and analytical labs, but it is also well suited for processing environments because it operates in real-time and in-process [2]. It can be used on many different types of samples including aqueous systems, slurries, feeds, turbulent mixtures, moving streams, gas-liquid mixes, gases, and biological tissues.
Raman spectroscopy involves illuminating a sample with a laser and collecting the scattered photons. It’s particularly useful for non-destructive chemical analysis as it detects fundamental vibrations that produce a unique Raman signature or spectrum; the intensity of the spectrum indicates the concentration of a molecule. Since the Raman spectrum of water is weak, the technique can be used in aqueous solutions unlike infrared imaging (where water spectrum is strong). A major advantage of Raman is that, unlike most other chemical analysis techniques, samples don’t need special preparation. What’s more, Raman is well-suited to monitor chemical reactions in real time because it acquires spectra quickly: anything from a fraction of a second to several minutes.
Raman Spectroscopy in Continuous Manufacturing
For over twenty years, Kaiser Optical Systems has produced Raman spectrometers for a range of industries employing continuous manufacturing so it is well-placed to aid pharmaceutical companies making the switch to continuous manufacturing. Kaiser’s systems can operate in processes involving liquids or solids providing real-time analytical data. New technologies in process Raman spectroscopy are generating a range of benefits for the manufacturer [2] including improved product quality and more efficient manufacturing. Monitoring materials in this way allows the manufacturer to optimize reaction times, maximize product yields and minimize waste.
Kaiser has pioneered revolutionizing holographic technology in Raman spectroscopy. Holographic transmission gratings mean that the whole Raman spectrum can be captured simultaneously rather than in separate steps. This gives better calibration stability and allows for real-time analysis. In the continuous processing of pharmaceuticals, for example, Raman can be used to monitor ingredient blends before they are turned into tablets to ensure blend uniformity as well as monitoring tablet coating operations [2].
Kaiser’s Raman Range
Kaiser has developed a wide range of Raman products for process applications.
For manufacturing environments, the Raman Rxn4™ analyzer is designed to work continuously in hazardous areas or classified environments. It boasts simultaneous full spectral coverage and high resolution and allows up to four measurement probes with a single analyzer. The analyzer can be used in pilot plants to learn about processes, or in production plants for process monitoring and control. A Nema4x enclosure option enable the Raman Rxn4™ to be placed into washdown environments.
Kaiser’s PhAT technology enables solids measurements from laboratory to manufacturing. This technology gives Raman-based quantitative monitoring and control of solid formulations. Its emergence has opened up new areas of solid-state chemistries for Raman analysis, particularly for batch operations such as granulation, milling, blending, coating, drying, compaction and tableting. Newer applications in continuous pharmaceutical solids operations include blend uniformity and coating endpoint monitoring. This sampling versatility comes from the fiber-optically coupled PhAT probe head. It can be used to analyze powders, slurries, flakes, plaques, gels or liquids.
Kaiser also offers the Raman Rxn2™ analyzer as a first-choice for laboratory or process development applications. The advantages of the Kaiser Raman approach include unified hardware with application-specific housing and ability to integrate into existing equipment without needing to modify the equipment. The analyzer can be coupled fiber-optically with Kaiser’s high-performance probes for immersion or non-contact measurements of solids, liquids, or turbid media. A Raman Rxn2™ analyzer also comes in the multi-channel configuration so that up to four probes can be used with a single analyzer. It has been proven in a range of applications in the Petrochemical, Specialty Chemical, Pharmaceutical, and Bioprocessing industries.
References
[1] Lee, S (2017), Modernizing the Way Drugs Are Made: A Transition to Continuous Manufacturing, FDA
https://www.fda.gov/drugs/news-events-human-drugs/modernizing-way-drugs-are-made-transition-continuous-manufacturing
[2] Esmonde-White, K. A.; Cuellar, M.; Uerpmann, C.; Lenain, B.; Lewis, I. R. Raman Spectroscopy as a Process Analytical Technology for Pharmaceutical Manufacturing and Bioprocessing. Anal Bioanal Chem 2017, 409 (3), 637–649. https://doi.org/10.1007/s00216-016-9824-1. Open Access Paper
About Kaiser Optical Systems, Inc.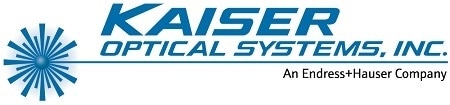
Kaiser Optical Systems, Inc. is a world leader in spectrographic instrumentation and applied holographic technology. Principal products include Raman sensors and instrumentation, advanced holographic components for spectroscopy, and astronomy and ultra-fast sciences. Principal offices and the manufacturing facility are located in Ann Arbor, Michigan.
Our products and services are deployed throughout the world in such diverse applications as pharmaceutical and chemical manufacturing, nanotechnology, telecommunications, education, forensic science, deep-sea exploration, and astronomy. From particles smaller than a human hair to objects as large as planets, our products are providing our customers unique insights into both today’s as well as “age-old” questions.
Kaiser was founded in 1979 to meet the need for diffractive or holographic optics for the avionics market. Kaiser entered the spectroscopy market in 1990 with the introduction of the holographic notch filter. In 1993 Kaiser released their first Raman analyzer, the HoloProbe. In 2013, the company became part of the Endress+Hauser Group.
To better serve the European community, Kaiser opened a new subsidiary in Europe in 1998. Kaiser Optical Systems SARL is located in Lyon, France. Kaiser SARL supervises our distributor network within Europe.
Sponsored Content Policy: News-Medical.net publishes articles and related content that may be derived from sources where we have existing commercial relationships, provided such content adds value to the core editorial ethos of News-Medical.Net which is to educate and inform site visitors interested in medical research, science, medical devices and treatments.