Key Issues
- Real-time glucose control in cell culture bioprocesses achieved using Raman technology
- Product quality is optimized to the target product profile through Raman-based feedback control of glucose
- Decreased target monoclonal antibody glycation by more than 50% and higher peak viable cell density achieved
- Kaiser Raman is a verified Process Analytical Technology (PAT) for Quality by Design (QbD)
- Real-time process and product quality assurance
Introduction
Inline analytics is strongly supported by the U.S. Food and Drug Administration’s Process Analytical Technologies (PAT) and Quality by Design (QbD) initiatives to verify process quality before the final product is tested.
The creation of protein therapeutics by mammalian cells is the most commonly utilized bioprocess as it is able to correctly generate and fold a recombinant protein. This bioprocess creates 60 to 70% of biopharmaceuticals.
Cell metabolic processes are affected by bioreactor parameters and intricate bioreactor knowledge is required to attain a consistent and balanced metabolic state of the cells.
The main process parameters in bioprocessing are dissolved oxygen (DO), pH, agitation rate, temperature, and glucose. Glucose is an essential process parameter as it influences the post-translational non-enzymatic glycation of proteins, the creation of waste products, and the metabolic profile of the cells.
Advanced glycation end products can also be produced through glycation, which leads to the loss of therapeutic function, binding inhibition, and may produce an undesirable immunogenic response. Carefully controlling the concentration of glucose in the process can minimize glycation.
New research has demonstrated that the online quantification of glucose can enhance fed-batch strategies to increase process robustness, cell density, and titer.
Frequent glucose measurements deliver crucial bioprocess data for process understanding and facilitates feedback control feed conditions from process development (PD) to manufacturing.
The investigation by Berry et al. outlines the fast production of Raman spectroscopy for feedback control of a CHO cell bioprocess were an important quality attribute was determined to be glycation of the monoclonal antibody (mAb).1
This study shows how a Raman technique was used to facilitate automatic glucose setpoint control strategies that decreased undesirable glycation of the mAb. It specifically outlines an online feedback control system, similar to the schematic detailed in Figure 1, where consistent in situ Raman spectral analysis measures the glucose concentration.
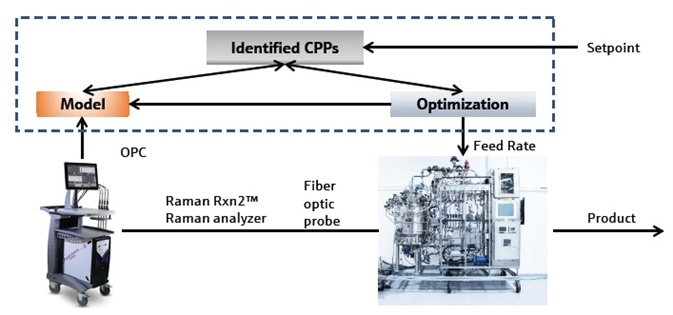
Figure 1. Schematic of Kaiser Raman-based feedback control. Image Credit: Kaiser Optical Systems, Inc.
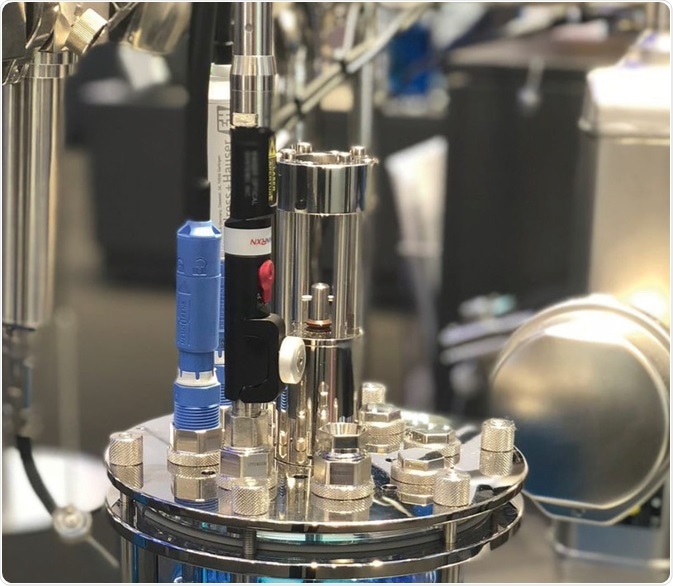
Figure 2. Inline control of product quality achieved from lab to process. Image Credit: Kaiser Optical Systems, Inc.
Experimental
Kaiser Raman analyzers featuring a stainless-steel bIO-LAB in situ probe head and a 785 nm Invictus™ laser were used to acquire the spectra of the process contents, displayed in Figure 2. The information was automatically exported to a PLS model in the SIMCA software package.
The data acquired online from the feedback control loop was contrasted with the Raman data acquired offline with offline traditional measurements and a 10X noncontact optic (NCO).
Two varying strategies of the glucose feedback control system were investigated. The aim of the first strategy was to achieve a consistent glucose concentration of 2.25 g/L for the duration of the production cycle. The second strategy produced a stepwise decreasing glucose concentration from 9.75 to 2.25 g/L over the same duration.
For each strategy, glucose stock solution was introduced (when required) in response to online Raman data and each day, glucose-free nutrient was given to the bioreactor.
The concentration of glucose in the bioreactor was limited to within 0.25 g/L of the setpoint utilizing deadband control. When the glucose concentration decreased below this value, the control logic was initiated.
Results
A Raman-based glucose control model was utilized to supply either a stepwise decrease of glucose concentrations over time or a consistently low glucose concentration to the bioprocess.
The investigation demonstrates that Kaiser Raman can optimize product quality, control bioprocess conditions, and can be integrated within an industrially-relevant bioprocess. Substantial glucose control was attained and efficiently integrated into PD work.
As the Raman driven control scheme was introduced early in PD, undesirable process changes were determined and quickly corrected, prior to scaling the process to manufacturing.
The replacement rate for the complex nutrient feed is one example of a process change. This was changed to four days to mitigate precipitation.
Conclusions
Raman spectroscopy is a critical PAT solution in fermentation and cell culture bioprocesses. Raman offers simultaneous, in situ quantifications of many important process parameters with one probe.
Raman’s specificity is advantageous for efficient model development and transfer, enabling the model to be transferred from laboratory to manufacturing with no substantial rework.
One example was that Raman quantification demonstrated differences in the complex nutrient feed over time. The team could then use this information to modify the media replacement schedule to mitigate precipitation of media components.
References and Further reading
- Berry, B. N.; et al. Quick Generation of Raman Spectroscopy Based In-Process Glucose Control to Influence Biopharmaceutical Protein Product Quality during Mammalian Cell Culture. Biotechnology Progress 2016, 32 (1), 224–234.
About Kaiser Optical Systems, Inc.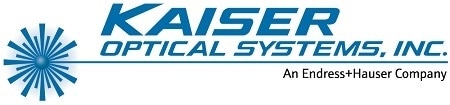
Kaiser Optical Systems, Inc. (Kaiser), an Endress+Hauser company, is the global leader in Raman spectroscopic instrumentation for laboratory, process, and manufacturing environments. Our solutions harness the powerful analytical information of Raman Spectroscopy to help our customers understand, measure, and control their chemistries.
As a trusted partner in Raman for over 30 years, Kaiser has a long history in production, including GMP manufacturing, with many proven successes. Our unmatched expertise, high quality solutions, and exceptional customer service sets Kaiser far above any other Raman option in the marketplace. Kaiser Raman technology is currently used throughout the chemical, food and beverage, oil and gas, pharmaceutical, and biopharmaceutical industries to optimize process efficiency and deliver quality products. Kaiser’s manufacturing and headquarters facility is in Ann Arbor, Michigan.
Sponsored Content Policy: News-Medical.net publishes articles and related content that may be derived from sources where we have existing commercial relationships, provided such content adds value to the core editorial ethos of News-Medical.Net which is to educate and inform site visitors interested in medical research, science, medical devices and treatments.