Sponsored Content by PolytecJan 14 2020
The fundamental way to develop the next generation of resonant-based sensor technology is via the characterization of the motion of high-frequency microdevices with sub-nanometer resolution. Microfabrication processes invite a new era of healthcare technology where point-of-care sensors guarantee increased sensitivity at low cost, as well as readout times within minutes.
Newcastle University has developed a new approach that uses degenerate vibration modes, therefore given sensor geometries utilize such resonant modes. Maximum sensitivity is gained from high-quality resonating devices whereby a shift in the resonant frequency leads to the addition of mass onto the sensor causes of the device. In a perfectly fabricated device, symmetry in the system modes’ identical frequencies is fundamental, as shown in Figure 1.
Ensuring a potentially robust technology, Figure 2 displays an introduced split and its ability to be proportional to the mass added to the sensor, however it is insensitive to non-specific binding events and temperature fluctuations. The split is introduced in frequencies between the modes when the symmetry is broken whereby biomolecules can be immobilized to particular regions of the surface of the sensor, especially the antinodal position of one of the modes with the functionalization of the sensor.
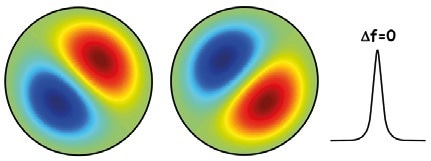
Figure 1: The mode shapes for the (1,0) vibration of a circular diaphragm. For a symmetric device, the modes form a degenerate pair.
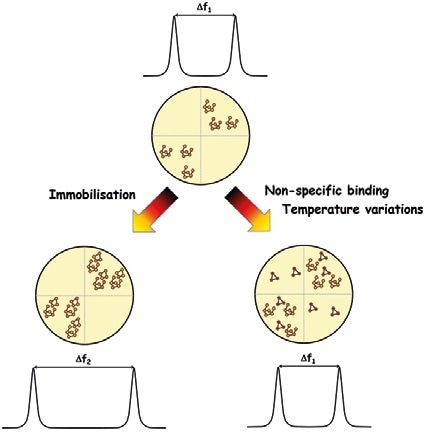
Figure 2: Upon functionalization of the sensor, degeneracy is broken and the modal frequencies show a split of Δf1. Addition of mass to the antinodal position of the functionalized mode increase this split to Δf2. For non specific variations, the split remains unaltered.
Device Design and Fabrication
Capacitively actuated and sensed through electrodes contained within a sealed cavity beneath the device, the designs of previous sensor manifestations employed a 4.5 μm thick crystalline silicon diaphragm. Ultimately raising the price of a disposable sensor, a shortcoming of this approach involved complex signal recovery electronics.
On the other hand, the most recent design iteration, funded through EPSRC (EP/G061394/1), integrates a 750 nm thick piezoelectric (PZT) film deposited onto the silicon diaphragm. A 200 nm silicon oxide layer provides a way of defining electrode regions and then the resulting induced bending moment drives the device into motion via the application of a voltage across an electrode.
The design must account for and ensure cleanroom fabrication tolerances of ±2 μm during the manufacturing process. Of the two silicon wafers, one of them is patterned. However, both are bonded together into a circular diaphragm resonator. With patterned oxide and gold layers forming the top electrodes and immobilization regions (Figure 3), a platinum base electrode forms the foundation layer for the PZT thin film that is subsequently spun on. The wafers are then diced and individual devices packaged, as displayed in Figure 4.
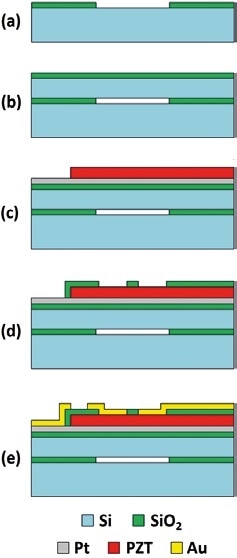
Figure 3: The process flow for fabrication of the sensor.
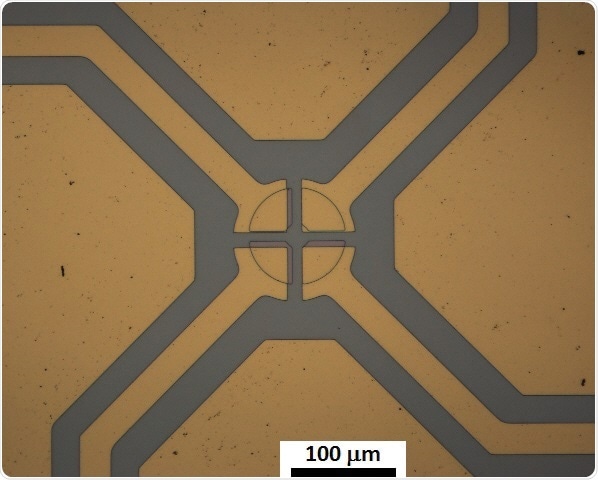
Figure 4: Microscope image of a fabricated sensor.
Sensor Characterization
Before development of the electronic solution device motion being sensed using on-board electronics, sensor performance was characterized using laser Doppler vibrometry. The devices are characterized under vacuum, at atmospheric pressure and within a liquid, where fundamental measurements are resonant frequencies and quality factors of the modes.
Due to the high electromechanical coupling factor of the PZT, the subsequent results signify that performance between the vacuum and atmospheric conditions are comparable. Unfortunately, the reduction in performance renders an electronic solution for this scenario to be problematic due to the mass loading of a liquid environment.
A key issue to sensitivity is mode shape alignment. Therefore it is pivotal that the position of the designed geometry, which dictates where molecules will be immobilized on the surface of the sensor, corresponds to the antinodal position of the required mode. Errors in fabrication can cause modal misalignment, so the accurate charting of each mode shape is mandatory at this stage. Mass sensitivity is evaluated by electroplating additional gold onto the surface of the sensor for any given modal alignment.
Results and Future Work
The development of frequency tracking electronics for the measurement of biomolecule immobilization onto the sensor surface is currently taking place. Preliminary results imply a device mass sensitivity of 12.0 Hz pg-1 [J. Micromech. Microeng. 23 (2013) 125019]. Current equipment funding from EPSRC has led to a UHF-120 system now encompassing Polytec’s characterization facilities up to 1.2 GHz. Thus preliminary sensor investigation was performed with their fiber-optic vibrometer giving characterization up to 20 MHz.
Upgrading the vibrometer permits the analysis of higher-order modes of the current sensor design and the development of ultra-high frequency surface acoustic wave sensors (SAWs) with device sensitivity scaling along with operational frequency. This UHF vibrometer also functions as an external user facility and we consequently look to support other research groups and institutes in the characterization of their high-frequency devices.
About Polytec
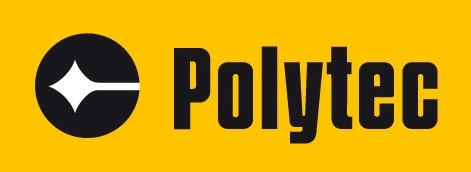
For over 50 years Polytec has provided high-technology, laser-based measurement solutions to researchers and engineers. Our commitment is to provide the most precise and reliable optical instruments and sensors available for non-contact measurement, setting Polytec apart from the competition as the gold standard in the design and manufacture of vibrometer and velocimeter systems. Our innovations answer many pressing manufacturing and engineering challenges.
Polytec was founded in 1967 to distribute commercial laser technology to industrial and research markets. Building on the company’s early success, Polytec began to develop and manufacture innovative laser-based test and measurement instruments in the 1970’s. These products have become known around the world as the gold standard in non-contact, laser-based measurement of vibration, speed and length.
Advanced product development remains a core strategic activity at Polytec with new electro-optical systems being designed for applications such as analytical process measurement, noise analysis, and factory automation.
In 2005, Polytec PT GmbH Polymere Technologien was founded as a spin-off, with over 30 years of know how in the supply and application of high tech adhesives and silicones in demanding electronic, optical and medical industries.
In 2008, LATAB was acquired and became a member of the Polytec organization. LATAB's early entry into the LED illumination market has produced the broadest and most flexible product mix for technical applications.
Sponsored Content Policy: News-Medical.net publishes articles and related content that may be derived from sources where we have existing commercial relationships, provided such content adds value to the core editorial ethos of News-Medical.Net which is to educate and inform site visitors interested in medical research, science, medical devices and treatments.