Granular materials, fine powders, and nanostructured powders are extensively used in numerous industrial applications.1 Excipients, particularly, are essential in dry powder pharmaceutical formulations, such as dry powder inhalers (DPIs), capsules, and tablets. Thus, insights concerning their behavior and the effects of using additives could have major consequences for the improvement of industrial processes, including avoiding technical issues like clogging, noncompliance, caking, and non-conformity.
To increase the processability of a powder, the excipient is typically mixed with an antistatic material to lower the triboelectric effect. This article will demonstrate how the incorporation of talc may influence lactose behavior in terms of flowability, compaction dynamics, granulation, and electrical charge. It will be also revealed that the incorporation of antistatic agent is not always a feasible solution.
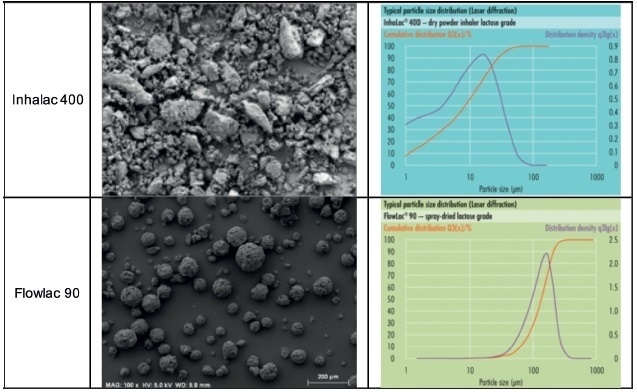
Figure 1. Photography and particle size distribution of the two lactose powders.
Material and Methods
Selected Powders
Meggle (Wasserburg, Germany) offered two lactose products (Figure 1) for use in this research:
- Inhalac 400, a superior-quality crystalline lactose powder, designed for DPIs
- FlowLac, a powder created by spray-drying a suspension of fine milled alpha-lactose monohydrate crystals in a solution of lactose
The lactose products were positioned in a chamber under ambient air environments (42% relative humidity and 24 °C) for four hours. The impact of talc addition in these products was examined with five different mass fractions 0%, 5%, 10%, 15%, and 20%. The talcum powder is a commercial powder (brand name “Care”) with different ingredients, including talc, Chamomilla recutita flower extract, magnesium stearate, perfume, zinc oxide, glycerin extract, and glycerin. Prior to the experiments, the talc was kept inside an oven at 110 °C for two hours.
Powder Compaction Dynamics
Powder compaction dynamics were investigated with the GranuPack device, an automated instrument that uses an enhanced “tapped density” measurement technique based on recent fundamental research.2 It examines the powder after it has been exposed to consecutive taps. In particular, Hausner ratio (Hr), initial density (ρ0), and final density after n taps (ρn) are measured precisely. Furthermore, a dynamic parameter matching the number of taps needed to accomplish half of the compaction (n½) and an extrapolation of the highest density (ρ∞) are extracted from compaction curves. Extra indexes can be used but they are not shown in this article.
The powder is put into a metallic tube with a rigorous automated initialization process. Later, a light, hollow cylinder is positioned on top of the powder bed to maintain the powder/air interface flat during the compaction process. The tube holding the powder sample is raised to a fixed height of ΔZ (generally fixed to 1 mm) and permitted to freefall.3
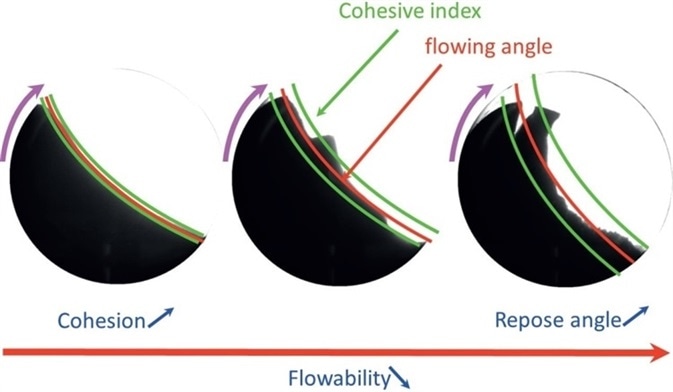
Figure 2. GranuDrum measurement principle.
Powder Flowability
Powder flowability was tested using a GranuDrum device,4 an automated instrument with a measurement technique based on a rotating drum as seen in Figure 2. Specifically, a horizontal drum having transparent sidewalls is half filled with a sample of powder, the drum rotates at rotational speeds ranging from 2 to 60 rpm, and a charge-coupled device (CCD) camera captures photographs (30–100 images per second) for each rotational speed. Automatically, the air/powder interface is defined on each photograph via an edge detection algorithm. Subsequently, the average interface position and the fluctuations around this average position are calculated.
Then, for each rotational speed, the flowing angle (αf), also referred to as “dynamic angle of repose,” is calculated from the average interface position, and the dynamic cohesive index (σf) is measured from the interface fluctuations. Generally, a low αf value matches with good flowability. The σf is only associated with the cohesive forces between the grains. A cohesive powder results in an intermittent flow, while a non-cohesive powder results in a regular flow. Thus, a σf close to zero matches to a non-cohesive powder. When the cohesiveness of powder increases, the cohesive index increases as a result.5
Besides measuring both σf and αf, GranuDrum can compute powder granulation properties with a thixotropy cohesive index (the greater this constant is for a powder, the higher its tendency to agglomerate).
Electrical Charge Affinity
Electrostatic charges are formed within a powder as it flows,6 because of the triboelectric effect, which is a charge exchange at the contact between two solids. During the flow of a powder inside a device or vessel (for example, a silo, mixer, or conveyor) the triboelectric effect happens between powder particles and between the powder and the surface of the device/vessel it is contained in. Thus, the features of the powder and the nature of the material used to construct the device are vital parameters.7
GranuCharge (Figure 3) automatically and precisely calculates the electrostatic charges formed inside a powder during flow in contact with a certain material. The powder sample flows into a vibrating V-tube and drops into a Faraday cup linked to an electrometer. The electrometer measures the charge obtained by the powder as it passes through the V-tube.
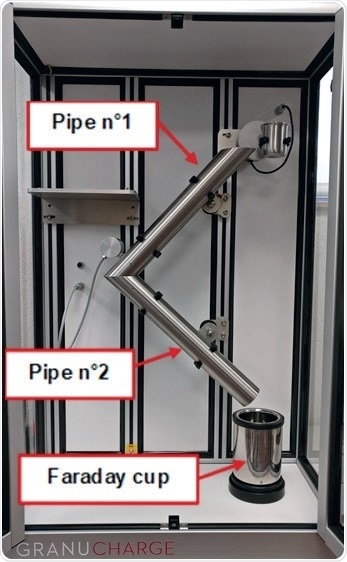
Figure 3. The GranuCharge machine.
Experimental Results
Powder Compaction Dynamics
For each experiment carried out using the GranuPack, 500 taps (tap frequency, 1 Hz) were applied to the sample and the freefall height was 1 mm (∝ tap energy). Powder mass was recorded prior to each experiment and the sample was poured inside the measurement cell in keeping with the software instructions (i.e., without user reliance).
Each measurement was done two times and the average value and standard deviation are shown here. Figure 4 illustrates bulk density as a function of the number of applied taps for each lactose mix. It can be observed that the Flowlac 90 grade is heavier in comparison with the Inhalac 400 product. Furthermore, the greater the talc mass fraction, for the same lactose grade, the higher the bulk density. This trend may be because of the size distribution of talc particle, which may be lower compared with the lactose products so that the talc particles can plug gaps between the larger lactose particles, causing an increase in bulk density.
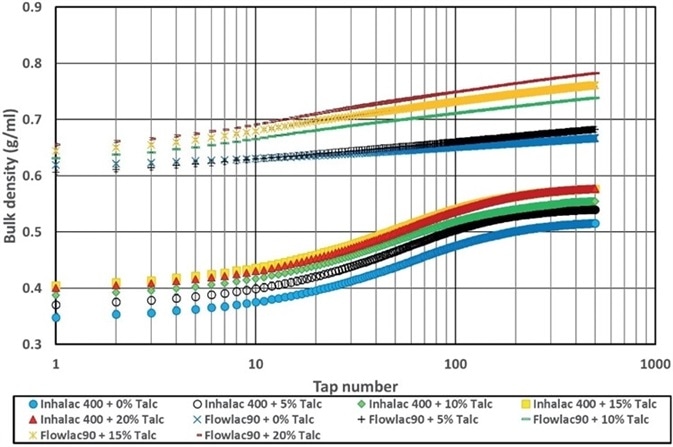
Figure 4. Bulk density as a function of number of taps for the two lactose products at different talc mass fractions.
Also, the compaction dynamic results from Inhalac 400 offer a sigmoid curve, while Flowlac 90 validates linear results, meaning Flowlac 90 compacts quicker than Inhalac 400. This observation is established by the n½ parameter (Figure 5), which is lesser for Flowlac 90.
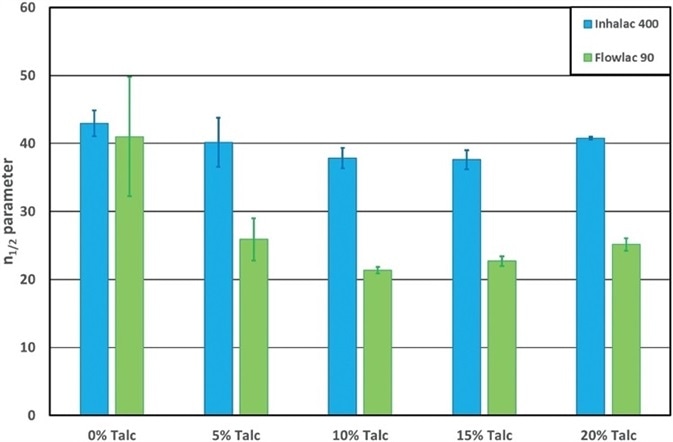
Figure 5. Measured n½ for each lactose grade with different talc mass fractions.
Another remarkable observation from Figure 5 is that up to a specific limit with Flowlac 90, the greater the talc mass fraction, the faster the compaction kinetic. Therefore, for this particular product, the tableting process can become simpler with a talc mass fraction close to 10%. But, above this limit, it appears that the compaction decelerates (n½ increasing from 23 to 25 as talc mass fraction grows from 15% to 20%). This effect is also noticed with Inhalac 400 but is a lot less obvious.
Powder Flowability
For experiments regarding powder flowability, about 50 mL of each powder was examined under typical conditions (43% RH and 25 °C). Two GranuDrum velocities were examined (1 rpm and 10 rpm), and for each rotational speed, 50 pictures were captured to boost the repeatability/accuracy of measurement.
Figure 6 illustrates the cohesive index measured at these speeds, as well as the thixotropy index. With a lower cohesive index at both speeds, it can be inferred that Flowlac 90 has a better flowability compared to Inhalac 400. However, the incorporation of talc boosted powder cohesion (i.e., a lower flowability) at both speeds.
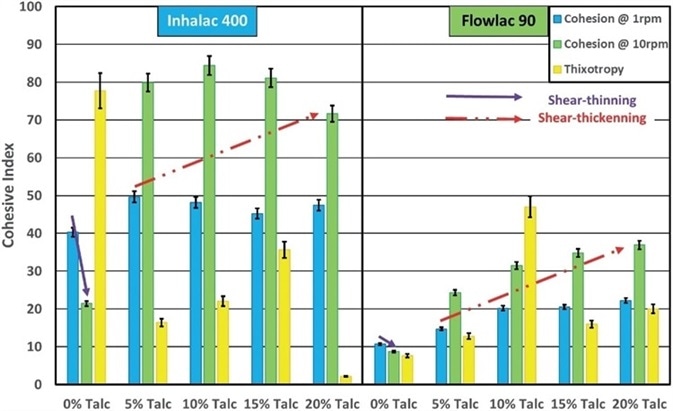
Figure 6. Cohesive index at 1 rpm and 10 rpm, and thixotropy index.
Lastly, based on the thixotropy index, for Inhalac 400, the bigger the talc mass fraction, the lower the propensity to agglomerate. However, the effect is the reverse for Flowlac 90, with an increase in the talc fraction resulting in an increase in the thixotropy index.
Electrical Charge
For each experiment to examine the electrostatic properties of the powders using the GranuCharge instrument, a vibrating feeder and stainless-steel 316 L pipes were used as seen in Figure 7. The quantity of powder used for each measurement was 40 mL and the powder was not used again. At the start of the test, the initial powder charge density (q0) was measured by adding powder straight into the Faraday cup. Once this step was finished, the powder was poured inside the rotating feeder, and then the experiment began. The final charge density was calculated at the end of experiment (qf).
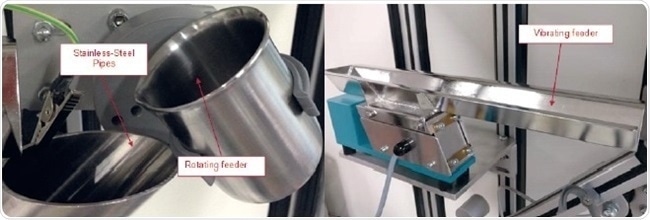
Figure 7. Vibrating/rotating feeder and stainless-steel pipes.
Figure 8 recapitulates the results. Each charge density value matches the average value calculated between the four tests (Δq = mean qf − mean q0).
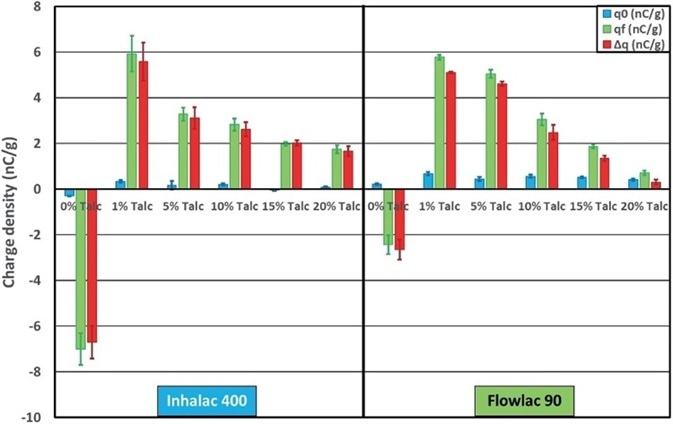
Figure 8. Comparison of initial and final charge densities for the two powders with different talc mass fractions.
The effect of talc on the electrostatic properties appears to be similar for the two products. Without talc, both products display a negative charge density following flow in contact with stainless-steel pipes, but with 1% talc mass fraction, a positive charge density can be observed. Then, the bigger the talc mass fraction, the lower the electrical charge with the effect apparently more noticeable with Flowlac 90. However, the maximum charge densities (compared with pure powder) are witnessed at mass fractions below 15%. Therefore, if a user wants to prevent electrical charge (and consequently powder sticking on the surfaces of pipes and forming agglomerates), the incorporation of talc is possibly not a feasible solution for Flowlac 90.
Conclusion
In this article, the influence of the addition of talc on powder behavior and properties has been demonstrated. It was shown that talc totally alters the electrostatic properties of the powder. Furthermore, it was observed that for certain powders, the addition of talc was not always a means to boost powder processability. It was also emphasized that talc influences powder granulation properties and dynamic flow behavior. Rheological behavior may also totally change with the incorporation of talc, from shear-thinning to a shear-thickening behavior. Lastly, lactose compaction dynamics also varied for the blends and an enhancement of compaction kinetics with the incorporation of talc was noticed for Flowlac 90.
References
- Lumay G et al, “Influence of Cohesives Forces on the Macroscopic Properties of Granular Assemblies”, AIP Conference Proceedings, 2013, Vol 1542(1), pp 995–998.
- Lumay G, Vandewalle N, “Experimental Study of Granular Compaction Dynamics at Different Scales: Grain Mobility, Hexagonal Domains, and Packing Fraction”. Physical Rev Letters, 2005, 95(2), 028002.
- Traina K, “Flow abilities of powders and granular materials evidenced from dynamical tap density measurement”. Powder Tech, 2 013, Vol 235, pp 842–852.
- Lumay G, Vandewalle N, “Flow of Magnetized Grains in a Rotating Drum”. Physical Rev, 2010, E82, 040301.
- Pirard SL et al, “Motion of Carbon Nanotubes in a Rotating Drum: The Dynamic Angle of Repose and a Bed Behavior Diagram”. Chem Eng J, 2009, Vol 146, pp 143–147.
- Rescaglio A et al, “Combined Effect of Moisture and Electrostatic Charges on Powder Flow”, EPJ Web of Conferences, 2017, Vol 140, 13009.
- Rescaglio A et al, “How Tribo- electric Charges Modify Powder Flowability”. Annual Transactions of the Nordic Rheology Society, 2017, Vol 25, pp 17–21.
About Granutools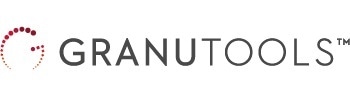
GranuTools, is a company that improves powder understanding by delivering leading edge physical characterization tools.
“All we do is powder flow characterization”
A Set of Complementary Tools
Combining decades of experience in scientific instrumentation with fundamental research on powders characterization, we offer a unique set of complementary instruments for granular materials characterization.
Named after their purpose, our instruments are tools to understand macroscopic behavior of powders.
GranuFlow for flow, GranuHeap for static cohesion, GranuDrum for dynamic cohesion, GranuPack for tapped density and GranuCharge for triboelectric charge measurements are designed with the following in mind:
- Precise & Repeatable
- Automatic
- No Operator Dependency
- Robust & Easy to Use
- Clear Interpretation