Powders are widely used in pharmaceuticals as active ingredients or excipients in formulations. As a result, several production processes are used for handling powders: wet and dry granulation, tableting, caps filling, blending, and more.
Therefore, any development in the understanding of the flow behaviors of powders can have large effects for pharmaceutical industries. In fact, a powder with unsuitable flowing properties can lead to severe complications in production lines (agglomeration, clogging, segregation, and so on).[1]
Applications
Tableting Process Optimization
It is widely known that in pharmaceutical industries, the material properties and process conditions determine the change in composition and the quality of tablets.
The manufacturing process of tablets involves compressing granules or dry powders in a die. This process includes three main steps: die filling, compaction, and ejection. Powders flowability and compressibility at the time of the die filling process govern the tablet properties, the tablet composition, and also the homogeneity. Thus, the analysis of the die filling process parameters has a major role in controlling the tablet manufacturing industry.[2]
In order to optimize tableting process, Granutools provides a workflow of two instruments: GranuFlow for die filling, and GranuPack for powders compressibility.
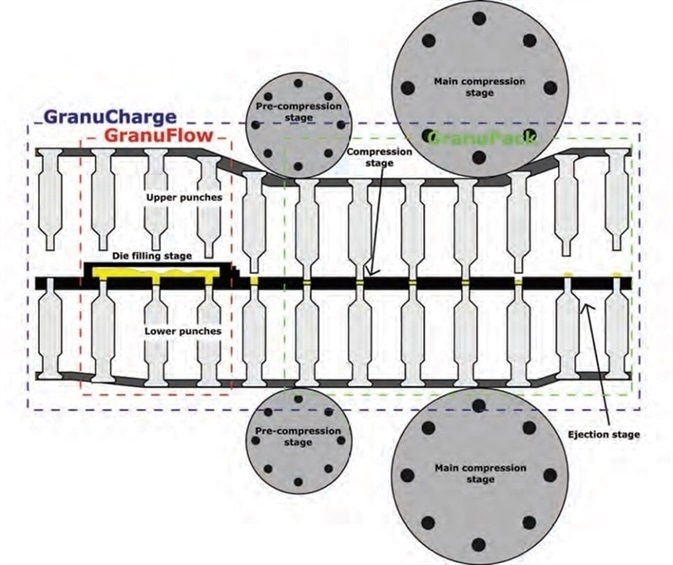
Pneumatic Vacuum Conveying Optimization
For a broad range of pharmaceutical and food materials, powder transfer is commonly done by means of pneumatic conveying. The application of either dense- or dilute-phase pneumatic transport can be used for a broad range of pharmaceutical operations such as the loading of blenders, mills, sifters, tablet presses, capsule fillers, and handling even finished tablets and capsules without causing any damage to the finished product.
The potential of the powder to produce electrical charges is a vital parameter in this process due to the friction between the grains and the system wall since these charges induce clogging. Furthermore, powder flowability is a key parameter.
With GranuDrum and GranuCharge instruments, Granutools proposes innovative physical characterization tools to overcome issues faced during pneumatic processes.
Dry Powder Inhaler Optimization
Inhalers have been developed due to the problem faced while using the traditional metered dose inhaler (MDI). Generally, dry powder inhalers (DPI) are easier to use when compared to the MDI and cause fewer irritant effects. Contrary to the MDI, only some patients develop a poor inhalation technique with constant use of DPI.
The inspiratory flow essential to attain a therapeutic effect is important with DPI. Furthermore, this technology confronts several issues: agglomeration induced by electrostatic charges, powder aging, blend homogeneity during capsule filling, and more.
To understand and enhance DPI technology, Granutools suggests using the GranuPack for the flowability, and the GranuCharge for the build-up of electrical charges at the time of API admission.
Galenic Formulation Optimization
Active Pharmaceutics Ingredient (API) must be integrated into an appropriate form in order to properly transport it to the necessary body parts. Therefore, it is essential to accurately characterize the composition of the blend (excipient + API) and its flowability.
In fact, understanding the flowing behavior in dynamic and quasi-static conditions enables it to be representative of every process part. Already, several industries are employing Granutool’s combination of two instruments — GranuDrum (rheometer for powder) and GranuHeap (improved heap shape analyzer) — for complete process characterization.
Granutools Workflow for Powder Characterization
GranuFlow—New Improved Laboratory Silo
GranuFlow is a superior laboratory silo when compared to the “Flow Through an Orifice” technique explained in the Pharmacopeia (USP1174). GranuFlow is a simple powder flowability measurement device made up of a silo with various apertures associated with a devoted electronic balance that measures the powder flow rate. This parameter is calculated automatically from the slope of the mass temporal evolution measured using the balance. The aperture size is altered easily and quickly with an original rotating system. Therefore, it is possible to easily achieve the flowability in a die filling configuration with higher accuracy (1%).

The figure below demonstrates that flowability classification between various grades of lactose can be easily achieved.
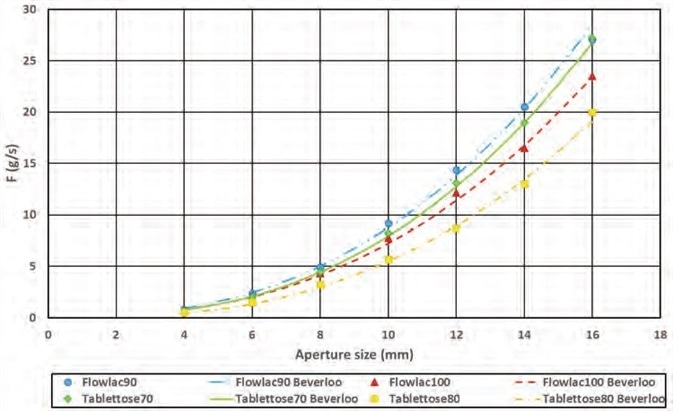
Mass flow rate versus aperture size
GranuPack — High-Resolution Tapped Density Analyzer
Besides the flowability, the other key parameter for the tableting process is the powder packing fraction. Actually, a high packing fraction decreases the porosity of the produced part and provides information about compressibility of the powders. Therefore, an accurate measurement of various packing fractions that can be accessed by the powder is also essential. Unlike the traditional manual tapped density measurement, GranuPack instrument measures a compaction curve (density plotted as a function of the tap number) with great accuracy (0.4%).[3]
The precision is due to the measurement automation (any influence of the operator) as well as the use of an initialization protocol. The optimal density, the bulk density, the compaction speed, and the compaction range are obtained from this compaction curve. Additionally, the compaction curves of various samples can be compared to evidence differences concerning compressibility, density, and flowability.[4]
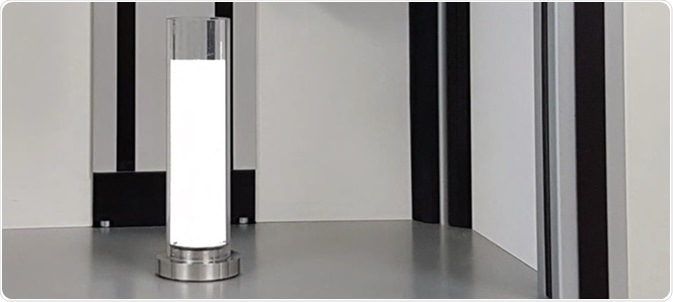
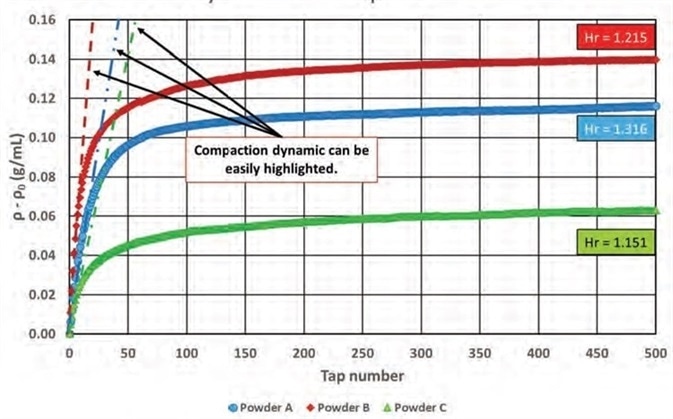
Bulk density variations versus taps number - GranuPack
GranuDrum — New Rheometer for Powder
The GranuDrum instrument is an automated powder flowability measurement technique based on the principle of a rotating drum. The sample is filled in a horizontal cylinder with transparent sidewalls. The drum spins in its axis at a predetermined angular velocity. A CCD camera takes pictures for each velocity. In each picture, the air/powder interface is detected using an edge detection algorithm. Later, the average interface position and the fluctuations around this average position are calculated. After that, for each rotating speed, the flowing angle αf is calculated from the average interface position and the dynamic cohesive index, σf, is computed from the interface fluctuations. On the whole, a low value of the flowing angle αf represents a good flowability. Therefore, the powder flowing behavior can be calculated at different velocities, and then the optimal process speed can be predicted.
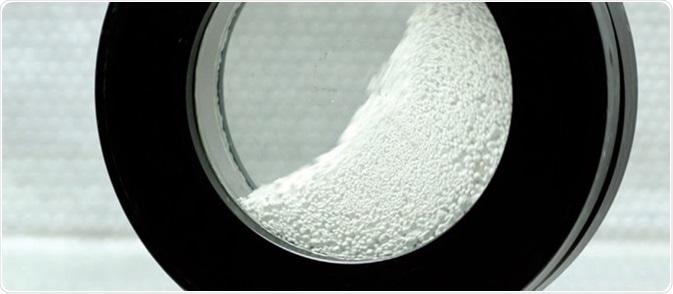
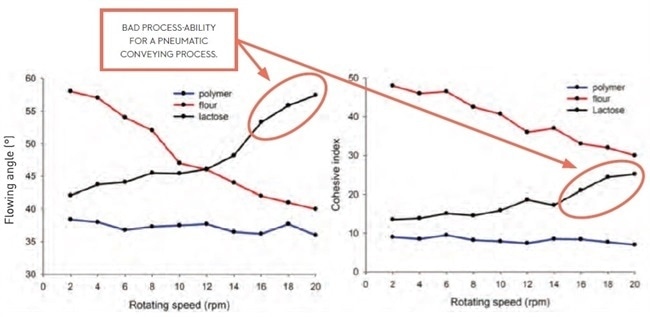
GranuCharge — Triboelectric Effect Analyzer
The presence of electrostatic charges inside a powder is known to influence drastically the material flowing properties. The triboelectric charges produced at the contacts between the grains and at the contacts between the grains and the container produces electrostatic forces. Although the triboelectric effect is useful for several applications, at the same time, the triboelectrification results in problems such as agglomeration and powder sticking on pipes surface. Therefore, GranuTools developed the GranuCharge instrument to assist industries in measuring this phenomenon. It automatically and accurately quantifies the amount of electrostatic charges generated within a powder during a flow in contact with a chosen material.
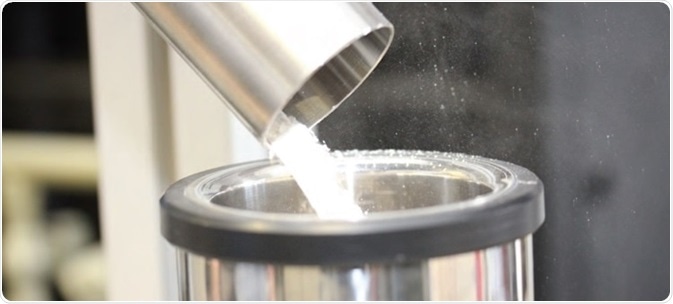
This instrument enables highly accurate charge density measurements (0.5 nC). Furthermore, the results enable the classification of the powders and the detection of problematic samples prior to introducing them inside the pneumatic conveying device. Finally, the pipes material effect can be examined, and the optimal one is chosen to reduce electrical charge accumulation during the process.
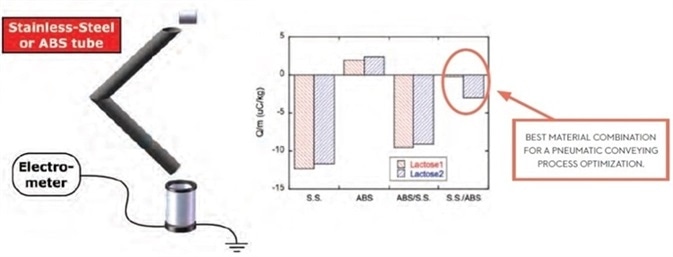
GranuHeap — Improved Heap Shape Analyzer
GranuHeap instrument is an automated heap shape measurement technique based on image processing and analysis. The powder heap is produced by following a stringent process. This step guarantees the heap reproducibility and eliminates user dependency. After completing this procedure, controlled rotation of the support coupled to snapshot analysis enables achieving various heap projections. A traditional algorithm treatment is used to determine the heap angle precisely (5%) as well as the heap shape fluctuation associated with powder cohesive interparticle forces.
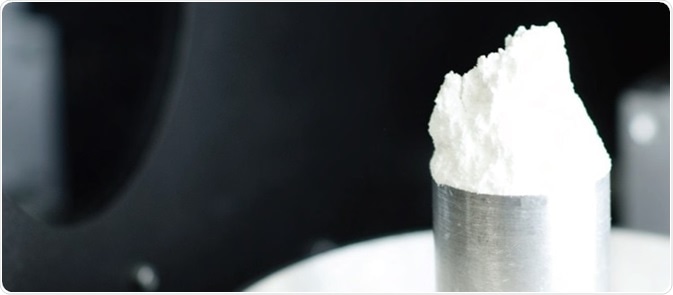
Thus, the powders flowability classification can be easily realized.
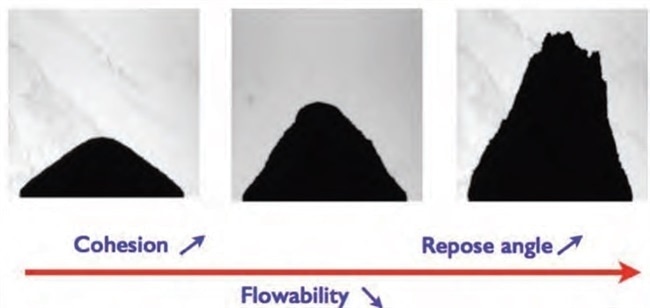
References
- F. Boschini et al., 2015. International Journal of Pharmaceutics 494 312–320.
- Varun Kumar Ojha et al., 2017. Neural Computing and Application.
- Powder Technology 224, 19–27 (2012).
- Lumay et al., 2006. Applied Physics Letters 89.
About Granutools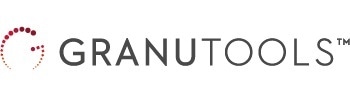
GranuTools, is a company that improves powder understanding by delivering leading edge physical characterization tools.
“All we do is powder flow characterization”
A Set of Complementary Tools
Combining decades of experience in scientific instrumentation with fundamental research on powders characterization, we offer a unique set of complementary instruments for granular materials characterization.
Named after their purpose, our instruments are tools to understand macroscopic behavior of powders.
GranuFlow for flow, GranuHeap for static cohesion, GranuDrum for dynamic cohesion, GranuPack for tapped density and GranuCharge for triboelectric charge measurements are designed with the following in mind:
- Precise & Repeatable
- Automatic
- No Operator Dependency
- Robust & Easy to Use
- Clear Interpretation