Both the USA cGMP1 and EU GMP2 dictate that cleanroom classification must be carried out according to ISO 14644-1.
The version of this ISO standard released in 19994 was rewritten by a group of international experts in the field, resulting in ISO 14644-1:20156 being published on December 15th, 2015. ISO 14644-1:2015 includes major revisions that impact the way in which cleanrooms are classified, as well as performance requirements for the air particle counting equipment employed to undertake the classification.
Cleanroom users working towards compliance with cGMP and/or GMP must consider these new rules when their cleanrooms are next requalified. This may involve the purchase of new air particle counters where current counters do not comply with the new performance rules.
Users are left with issues, in that this new requalification may imply that their cleanroom is not operating at the grade achieved via the previous classification process. This article outlines the new rules.
Introduction
While both the EU GMP and USA cGMP outline airborne particle counts/m3 for each different cleanliness class/grade, these do not include guidance on the cleanroom classification procedure itself. Instead, they direct readers to ISO 14644-1 for this cleanroom classification methodology.
An element of the routine periodic review process involved the ISO committee responsible for ISO 14644-1 is the process of making a decision as to which areas of the classification process need revising, in order to enhance statistical accuracy.
The ISO committee also made the decision to add a reference in the normative Annex on airborne particle counters to ISO 21501-45, providing both a calibration procedure and verification method for particle counters. This was included to help minimize the inaccuracy in a counter’s measurement result, as well as aiming to reduce the variance in measured results from different particle counters.
The strict performance rules in ISO 21501-4 have resulted in many older air particle counters being no longer suitable for cleanroom classification or requalification according to ISO 14644-1.
Cleanliness classes / grades
Fundamental differences exist between the USA cGMP and the EU GMP documents for cleanroom classes/grades. A central difference is that the EU GMP requires the cleanroom user to first classify and then monitor their cleanrooms for airborne particles both ≥0.5 microns and ≥5 microns in size, while the USA cGMP only requires the classification and monitoring of cleanrooms for airborne particles ≥0.5 microns.
cGMP does not dictate airborne cleanliness levels for each class of cleanroom while the cleanroom is at rest. This is in contrast with GMP which differentiates between these two states (Figures 1 and 2).
Clean Area Classification (0.5 µm particles/ft3) |
ISO Designation |
≥0.5
µm particles/m3 |
Microbiological Active Air Action Levels (cfu/m3) |
Microbiological Settling Plates Action Levels (diam. 90 mm; cfu/4 hours) |
100 |
5 |
3,520 |
1 |
1 |
1000 |
6 |
35,200 |
7 |
3 |
10,000 |
7 |
352,000 |
10 |
5 |
100,000 |
8 |
3,520,000 |
100 |
50 |
Figure 1. Cleanroom classes as defined in USA cGMP. Image Credit: Beckman Coulter Life Sciences
|
Maximum permitted number of particles per m3 equal to or greater than the tabulated size |
|
At rest |
In operation |
Grade |
0.5 µm |
5.0 µm |
0.5 µm |
5.0 µm |
A |
3,520 |
20 |
3,520 |
20 |
B |
3,520 |
29 |
352,000 |
2,900 |
C |
352,000 |
2,900 |
3,520,000 |
29,000 |
D |
3,520,000 |
29,000 |
Not defined |
Not defined |
Figure 2. Cleanroom grades as defined in EU GMP. Image Credit: Beckman Coulter Life Sciences
The third key difference between the documents is that cGMP includes an extra class between Class 100 (equivalent to GMP Grade A) and Class 10,000 (equivalent to GMP Grade B) - GMP includes the additional Grade D, defined as ≤3,520,000 particles ≥0.5 microns at rest.
The changes to ISO 14644-1
The main amendments in the ISO 14644-1:2015 document which impact on the GMP community are:
- A revised method for calculating the number of sample locations for classification/requalification
- Removal of the 95% Upper Confidence Limit (UCL) calculation
- Reference to ISO 21501-4 in the normative* Annex A where requirements for air particle counters are defined (*normative means this section must be complied with)
- Removal of the maximum allowable concentration of airborne particles/m3 - ≥5 microns for ISO Class 5 from the Cleanliness Classes table (ISO Class 5 at ≥5 microns is equivalent to GMP Grade B at rest)
This new method for calculating the number of sample locations involves the use of a look-up table, within which the number of locations per cleanroom size is defined. This differs from the current method which calculates the number of locations based on the square root of the area of the cleanroom floor.
To ensure a pragmatic level of statistical accuracy, the number of sample locations necessary for classification/requalification has been increased. This means that in many cases, cleanroom users will need to increase the number of sample locations for cleanroom classification/requalification.
In line with the ISO 14644-1:1999 document, ISO 14644-1:2015 also asserts that the sample locations should be evenly distributed across the cleanroom in an equally-spaced grid.
This requirement for new sample locations has the potential to cause confusion in particle counter users who have previously followed the same classification/requalification routine, and this will be particularly prevalent in those users with several cleanrooms and numerous air particle counters.
Cleanroom owners can mitigate the chances of data errors or miss-sampling by opting to use air particle counters, programmed with the revised cleanroom sampling program to prompt users to take the appropriate number of samples via the most suitable particle counter configuration in each cleanroom grade.
This opportunity for confusion and potential errors may also occur in any type of manual data transfer, where data from the particle counter’s paper print outs is transferred to Microsoft Excel or another laboratory information management system (LIMS).
Cleanroom owners may opt to mitigate the risk of data transfer errors by selecting particle counters which are able to transfer the particle count data via wireless Ethernet, transferring this in an Excel readable format directly to a LIMS system or secure data server.
By improving statistical accuracy via a greater number of sampling locations, the ISO 14644-1:2015 document removes the need for the UCL calculation. This was formerly required for cleanrooms that possessed between 2 and 9 sample locations. Now, there is no need to perform the UCL calculation, as long as all sample locations are within the class/grade requirements.
ISO 21501-4 defines calibration procedures which make certain that there is a reduction in air particle counter sampling measurement inaccuracies. It also includes the Counting Efficiency test - a final confirmation of air particle counter performance. This test contrasts the performance of the particle counter under test with that of an instrument possessing a higher resolution (approximately 0.3 microns).
The counter under test, and also the higher resolution instrument, are presented with an air sample containing certified particles at the smallest calibration size for the counter being tested. This is generally 0.5 microns for GMP applications.
Because the certified particles possess an expected normal (or ‘Gaussian’) size distribution profile, 50% of these certified particles will be ≥0.5 microns and 50% will be ≤0.5 microns. Here, the counter being tested must successfully count and report that 50% of the airborne particles are ≥0.5 microns. In contrast, the higher resolution instrument should report 100% of the airborne particles as being ≥0.3 microns.
As such, the higher resolution counter will count the whole particle population, enabling the counter’s ability under test to accurately report 50% of the certified particles as being ≥0.5 microns (Figure 3).
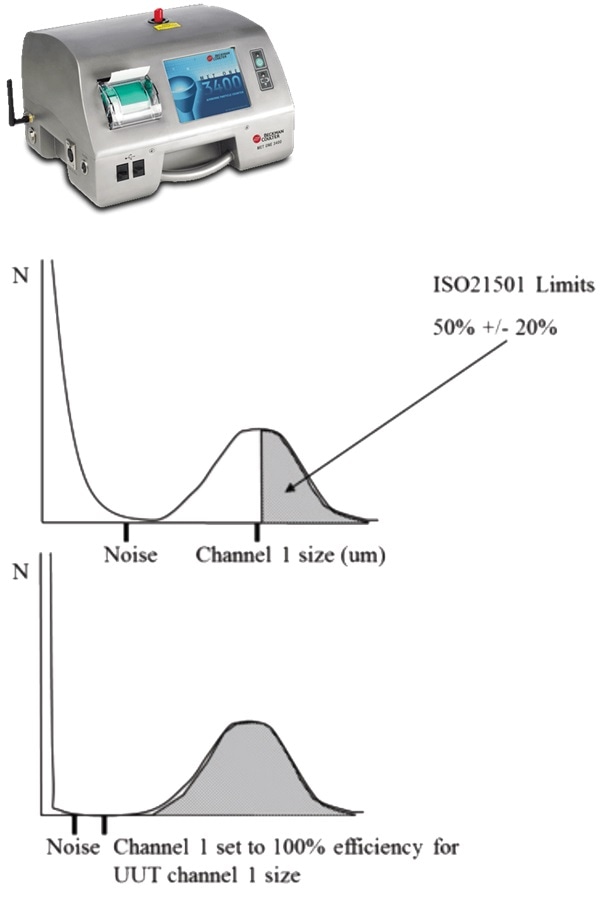
Image Credit: Beckman Coulter Life Sciences
In other efforts to improve the statistical accuracy of the classification/requalification, the experts responsible for rewriting the standard opted to remove from the Cleanliness Classes table numbers of particles that were too small to be deemed statistically sound.
This was extended to include the 29 particles/m3 for ISO Class 5, where particles were ≥5 microns, causing some controversy by potentially weakening the EU GMP requirement to measure these particles within Grade A and Grade B environments.
Implications for the GMP cleanroom community
The undated reference to ISO 14644-1 in the GMP and cGMP documents, to the new ISO 14644-1:2015, will have a marked effect on all cleanroom users in the GMP community.
Every GMP cleanroom user will need to adjust their cleanroom classification/requalification SOPs to account for the larger number of sampling points necessary in the new version of the ISO standard.
In some instances, a risk assessment could have to retrospectively explore any potential impact on product quality, should the new classification/requalification alter the cleanroom class or grade. Where this is the case, a cleanroom owner could consider alterations in their cleanroom and air handling systems, bringing the cleanroom back into the required class/grade.
Every GMP cleanroom user must check and confirm the particle counters used to classify and monitor their cleanrooms, ensuring compliance with the requirements of ISO 21501-4. This includes those counters which are used as elements of a continuous monitoring system.
Conclusion
Amendments in the ISO 14644-1 standards might signify the most comprehensive change to GMP cleanrooms since the GMP Annex 1 in 2003 introduced the requirement to sample 1m3 at every sample location when classifying/requalifying Grade A environments.
It is advisable for the GMP cleanroom community to begin planning for these changes now, instead of waiting until they are inspected in line with the ISO 14644-1:2015 document.
References
- Food and Drug Administration. Guidance for industry. Sterile drug products produced by aseptic processing – current good manufacturing practice, 2004. U.S. Department of Health and Human Services Food and Drug Administration Center for Drug Evaluation and Research (CDER) Center for Biologics Evaluation and Research (CBER) Office of Regulatory affairs (ORA) Division of Drug Information, HFD-240 Center for Drug Evaluation and Research Food and Drug Administration 5600 Fishers Lane Rockville, MD 20857 USA
- European Commission. EudraLex. The Rules Governing Medicinal Products in the European Union. Volume 4. EU Guidelines to Good Manufacturing Practice. Medicinal products for human and veterinary use, Annex 1: Manufacture of Sterile Medicinal Products, 14th February 2008. European Commission Enterprise and Industry Directorate-General, B-1049 Bruxelles / Europese Commissie, B-1049 Brussel – Belgium.
- European Commission. Ad Hoc GMP Inspections Services Group. EC Guide to Good Manufacturing Practice. Revision to Annex 1. Manufacture of Sterile Medicinal Products, 30th May 2003
- ISO 14644-1:1999(E) Cleanrooms and associated controlled environments — Part 1: Classification of air cleanliness 1st May 1999. International Organization for Standardization Case Postale 56 • CH-1211 Genève 20 • Switzerland
- ISO 21501-4 Determination of particle size distribution — Single particle light interaction methods — Part 4: Light scattering airborne particle counter for clean spaces 2007. International Organization for Standardization Case Postale 56 • CH-1211 Genève 20 • Switzerland
- ISO 14644-1:2015 Cleanrooms and associated controlled environments — Part 1: Classification of air cleanliness by particle concentration. International Organization for Standardization Case Postale 56 • CH-1211 Genève 20 • Switzerland
*Excel is a registered trademark of Microsoft Corporation in the United States and/or other countries.
About Beckman Coulter Life Sciences
Beckman Coulter Life Sciences is dedicated to empowering discovery and scientific breakthroughs. The company’s global leadership and world-class service and support delivers sophisticated instrument systems, reagents and services to life science researchers in academic and commercial laboratories, enabling new discoveries in biology-based research and development.
A leader in centrifugation and flow cytometry, Beckman Coulter has long been an innovator in particle characterization and laboratory automation, and its products are used at the forefront of important areas of investigation, including genomics and proteomics.
Primary activity / Product lines
- Flow Cytometry
- Centrifugation
- Particle Counting and Characterization
- Liquid Handling and Robotics
- Nucleic Acid Sample Preparation
Sponsored Content Policy: News-Medical.net publishes articles and related content that may be derived from sources where we have existing commercial relationships, provided such content adds value to the core editorial ethos of News-Medical.Net which is to educate and inform site visitors interested in medical research, science, medical devices and treatments.