This document outlines the evaluation of Molecular Devices’ microplate readers for use in regulated environments, referencing 21 CFR Parts 58, 211, and 820 and EudraLex Annex 15.
21 CFR Part 58 overview
Title 21 CFR Part 58 provides guidance on Good Laboratory Practice (GLP) for executing non-clinical laboratory studies that support applications for research permits for Food and Drug Administration (FDA)-regulated products—such as medical devices, biologics, and drugs for human use.
21 CFR Part 211 overview
Good Manufacturing Practice (GMP) guidance for finished pharmaceuticals is prescribed in Title 21 CFR Part 211.
21 CFR Part 820 overview
Quality systems for medical devices are covered in 21 CFR Part 820, which outlines GMP regulations governing the methods employed in the design, manufacture, packaging, labeling, storage, installation, and servicing of all devices intended for human use.
These guidelines aim to ensure that medical devices are effective, safe, and comply with the Federal Food, Drug, and Cosmetic Act. Manufacturers of medical devices sold in the US (including those who import their products to the US) are subject to the provisions of Part 820.
Molecular Devices’ products are labeled “For Research Use Only”, as they are not designed as medical devices for diagnosing diseases or other conditions.
The principles of qualification and validation applicable to processes, equipment, utilities, and facilities utilized in medicinal product manufacture are described in Annex 15.
Adherence to GMP mandates that manufacturers manage crucial elements of their operations through qualification and validation during the lifecycle of their business products and processes.
Whose responsibility is it to validate the system?
Compliance with regulations is mandatory for regulated customers or those producing drugs or food.
Molecular Devices is exempt from FDA regulatory requirements because it does not produce food or drugs. Nonetheless, Molecular Devices can ensure that its customers adhere to 21 CFR Parts 58, 211, and 820 and EudraLex Annex 15.
Annex 11 references a system owner, process owner, qualified person, and information technologist. On the customer side, the ‘business process owner’ (typically laboratory supervisors) or ‘system owner’ (typically information technology management), in collaboration with information technology, is responsible for validation.
A validation team must include representatives from numerous stakeholders.
- Quality Assurance (QA) conducts a comprehensive assessment to confirm that local corporate standards are met.
- Department heads are essential because they provide the business case and resources for validation.
Impact of compliance vs. non-compliance
The validation of several computerized systems can incur significant costs. Plans to identify resources and project and procurement costs must be made.
Some organizations enlist third parties to design and conduct computerized system validation. However, the responsibility for the validation effort and upkeep of a compliant-validated system cannot. As outlined in 21 CFR Parts 58.63 and 820.70 and Annex 15, this is the regulated customers’ responsibility.
The cost of non-compliance (up to millions of dollars) is highlighted in public records of judgments against pharmaceutical or independent/contract laboratories. This encompasses lost productivity and revenue, rework expenses, and the potential damage to reputation with investors and customers.
The Code of Federal Regulations (CFR) is a codification of the general and permanent laws published in the Federal Register by the agencies and departments of the Federal Government.
The CFR is separated into 50 titles that represent comprehensive areas subject to regulation by the Federal Government. Title 21 is reserved for rules regulated by the Office of National Drug Control Policy, the Drug Enforcement Administration (Department of Justice), and the FDA (Department of Health and Human Services).
- Part 58 – Good Laboratory Practices for Non-Clinical Laboratory Studies
- Part 211 – Current Good Manufacturing Practice for Finished Pharmaceuticals
- Part 820 – Quality System Regulation
Volume four of “The Rules Governing Medicinal Products in the European Union,” offers guidance for interpreting the principles and guidelines of GMP for medicinal products intended for both human and veterinary use.
The GMP Guide is structured into three parts and supplemented with annexes that address comprehensive areas subject to Federal regulation.
- Part 1 – Basic Requirements for Medicinal Products
- Chapter 3 – Premise and Equipment
- Chapter 4 – Documentation
- Annex 15 – Qualification and validation
Table 1. Assessment of 21 CFR Part 58 Compliance for Plate Reader Validation & Maintenance. Source: Molecular Devices UK Ltd
Reference to 21 CFR Part 58
Subpart D – Equipment |
Molecular Devices
Products/Services |
End User Operations |
§58.61 – Equipment design
Equipment used in the generation, measurement, or assessment of data and equipment used for facility environmental control shall be of appropriate design and adequate capacity to function according to the protocol and shall be suitably located for operation, inspection, cleaning, and maintenance. |
IQ/OQ services ensure computerized systems (plate reader and software entity) are performing within specification.
PM/OQ services performed at regular intervals promote ongoing reliability and confirm performance against specification.
|
It is the end user responsibility to validate and qualify computerized systems (plate reader and software entity) into their regulated environment. |
§58.63 – Maintenance and calibration of equipment
(a) Equipment shall be adequately inspected, cleaned, and maintained. Equipment used for the generation, measurement, or assessment of data shall be adequately tested, calibrated and/or standardized. |
It is the end user responsibility to develop business process and procedures to support computerized system applications in their regulated environment. |
(b) The written standard operating procedures shall set forth in sufficient detail the methods, materials, and schedules to be used in the routine inspection, cleaning, maintenance, testing, calibration, and/or standardization of equipment, and shall specify, when appropriate, remedial action to be taken in the event of failure or malfunction of equipment. The written standard operating procedures shall designate the person responsible for the performance of each operation. |
IQ/OQ services ensure computerized systems (plate reader and software entity) are performing within specification.
SOPs for plate reader maintenance and use of SpectraTest® Validation Plates are available. |
It is the end user responsibility to govern these activities in an SOP for plate reader maintenance and calibration. |
(a) Written records shall be maintained of all inspection, maintenance, testing, calibrating and/or standardizing operations. These records, containing the date of the operation, shall describe whether the maintenance operations were routine and followed the written standard operating procedures. Written records shall be kept of nonroutine repairs performed on equipment as a result of failure and malfunction. Such records shall document the nature of the defect, how and when the defect was discovered, and any remedial action taken in response to the defect. |
PM/OQ services performed at regular intervals promote ongoing reliability and confirm performance against specification.
A completed report is provided to the customer at the completion of the PM/OQ service. |
It is the end user responsibility to maintain written records of maintenance, testing, and calibration activities. |
Table 2. Assessment of 21 CFR Part 211 Compliance for Plate Reader Validation & Maintenance. Source: Molecular Devices UK Ltd
Reference to 21 CFR Part 211 |
Molecular Devices
Products/Services |
End User Operations |
§211.160 – General requirements
(b) Laboratory controls shall include the establishment of scientifically sound and appropriate specifications, standards, sampling plans, and test procedures designed to assure that components, drug product containers, closures, in-process materials, labeling, and drug products conform to appropriate standards of identity, strength, quality, and purity. Laboratory controls shall include:
(4) The calibration of instruments, apparatus, gauges, and recording devices at suitable intervals in accordance with an established written program containing specific directions, schedules, limits for accuracy and precision, and provisions for remedial action in the event accuracy and/or precision limits are not met. Instruments, apparatus, gauges, and recording devices not meeting established specifications shall not be used.
|
Certified Field Service Engineers (FSEs) provide IQ/OQ or PM/OQ services for plate readers.
|
It is the end user responsibility to develop business process and procedures to support computerized system applications in their regulated environment.
|
§211.194 – Laboratory Records
(d) Complete records shall be maintained of the periodic calibration of laboratory instruments, apparatus, gauges, and recording devices required by §211.160(b)(4). |
Certified Field Service Engineers (FSEs) provide reports after IQ/OQ or PM/OQ services performed on plate readers. |
It is the end user responsibility to develop business process and procedures to support maintenance records as required. |
Table 3. Assessment of 21 CFR Part 820 Compliance for Plate Reader Validation & Maintenance. Source: Molecular Devices UK Ltd
Reference to 21 CFR Part 820
Subpart G – Production and Process Controls |
Molecular Devices
Products/Services |
End User Operations |
§820.70 – Production and Process Controls
(g) Equipment. Each manufacturer shall ensure that all equipment used in the manufacturing process meets specified requirements and is appropriately designed, constructed, placed, and installed to facilitate maintenance, adjustment, cleaning, and use. |
PM/OQ services ensure instruments are performing within specification at regular intervals, at a minimum, once annually. |
It is the end user responsibility to validate and qualify computerized systems (plate reader and software entity) into their regulated environment. |
(1) Maintenance schedule. Each manufacturer shall establish and maintain schedules for the adjustment, cleaning, and other maintenance of equipment to ensure that manufacturing specifications are met. Maintenance activities, including the date and individual(s) performing the maintenance activities, shall be documented. |
|
It is the end user responsibility to establish internal programs that manage instrument maintenance and instrument verification. |
(2) Inspection. Each manufacturer shall conduct periodic inspections in accordance with established procedures to ensure adherence to applicable equipment maintenance schedules. The inspections, including the date and individual(s) conducting the inspections, shall be documented. |
|
It is the end user responsibility to inspect their internal equipment maintenance schedules. |
(3) Adjustment. Each manufacturer shall ensure that any inherentlimitations or allowable tolerances are visibly posted on or near equipment requiring periodic adjustments or are readily available to personnel performing these adjustments. |
Software validation services are provided that could include automated processes. |
It is the end user responsibility to validate and qualify automated processes in their regulated environment. |
(i) Automated processes. When computers or automated data processing systems are used as part of production or the quality system, the manufacturer shall validate computer software for its intended use according to an established protocol. All software changes shall be validated before approval and issuance. These validation activities and results shall be documented. |
|
|
Reference to 21 CFR Part 820
Subpart G – Production and Process Controls |
Molecular Devices
Products/Services |
End User Operations |
§820.72 – Inspection, measuring, and test equipment
(a) Control of inspection, measuring, and test equipment—Each manufacturer shall ensure that all inspection, measuring, and test equipment, including mechanical, automated, or electronic inspection and test equipment, is suitable for its intended purposes and is capable of producing valid results. Each manufacturer shall establish and maintain procedures to ensure that equipment is routinely calibrated, inspected, checked, and maintained. |
IQ/OQ and/or PM/OQ services and SpectraTest Validation Plates ensure instruments are performing within specification traceable to NIST and NMI standards. A completed report is provided to the customer at the completion of the IQ/OQ or PM/OQ service.
|
It is the end user responsibility to validate and qualify computerized systems (plate reader and software entity) into their regulated environment.
|
(b) Calibration—Calibration procedures shall include specific directions and limits for accuracy and precision. When accuracy and precision limits are not met, there shall be provisions for remedial action to reestablish the limits and to evaluate whether there was any adverse effect on the device’s quality. These activities shall be documented. |
|
It is the end user responsibility to calibrate equipment and maintain records in their regulated environment. |
(1) Calibration standards—Calibration standards used for inspection, measuring, and test equipment shall be traceable to national or international standards. If national or international standards are not practical or available, the manufacturer shall use an independent reproducible standard. If no applicable standard exists, the manufacturer shall establish and maintain an in-house standard. |
|
|
(2) Calibration records—The equipment identification, calibration dates, the individual performing each calibration, and the next calibration date shall be documented. These records shall be displayed on or near each piece of equipment or shall be readily available to the personnel using such equipment and to the individuals responsible for calibrating the equipment. |
|
|
Table 4. Assessment of EudraLex Volume 4 (Part 1) Compliance for Plate Reader Validation & Maintenance. Source: Molecular Devices UK Ltd
Reference to EudraLex Volume 4 Part 1 – Basic Requirements for Medicinal Products |
Molecular Devices
Products/Services |
End User Operations |
Chapter 3 – Premises and Equipment
3.41 Measuring, weighing, recording, and control equipment should be calibrated and checked at defined intervals by appropriate methods. Adequate records of such tests should be maintained. |
IQ/OQ and/or PM/OQ services and SpectraTest Validation Plates ensure instruments are performing within specification traceable to NIST and NMI standards.
A completed report is provided to the customer at the completion of the IQ/OQ or PM/OQ service. |
It is the end user responsibility to develop business process and procedures to support computerized system applications in their regulated environment.
|
3.44 Defective equipment should, if possible, be removed from production and quality control areas, or at least be clearly labeled as defective. |
Not applicable. |
|
Chapter 4 – Documentation
4.29 There should be written policies, procedures, protocols, reports and the associated records of actions taken or conclusions reached, where appropriate, for the following examples:
• Validation and qualification of processes, equipment and systems
• Equipment assembly and calibration |
IQ/OQ of SoftMax® Pro GxP Data Acquisition and Analysis Software.
IQ/OQ and/or PM/OQ services ensure instruments are performing within specification traceable to NIST and NMI standards. |
|
Table 5. Assessment of EudraLex Volume 4 (Annex 15) Compliance for Plate Reader Validation & Maintenance. Source: Molecular Devices UK Ltd
Reference to EudraLex Volume 4 Annex 15: Qualification and Validation |
Molecular Devices
Products/Services |
End User Operations |
Section 2 – Documentation
2.5 Qualification documents may be combined together, where appropriate, e.g. installation qualification (IQ) and operational qualification (OQ). |
IQ/OQ services ensure instruments are performing within specification onsite when requested. |
It is the end user responsibility to develop business process and procedures to support computerized system applications in their regulated environment. |
2.6 Where validation protocols and other documentation are supplied by a third party providing validation services, appropriate personnel at the manufacturing site should confirm suitability and compliance with internal procedures before approval. Vendor protocols may be supplemented by additional documentation/test protocols before use. |
IQ/OQ and/or PM/OQ services and SpectraTest Validation Plates ensure instruments are performing within specification traceable to NIST and NMI standards. |
|
Section 3 – Qualification Stages for Equipment,
Facilities, utilities and Systems
3.1 Qualification activities should consider all stages from initial development of the user requirements specification through to the end of use of the equipment, facility, utility or system. The main stages and some suggested criteria (although this depends on individual project circumstances and may be different) which could be included in each stage are indicated below: |
Not applicable. |
It is the end user responsibility to develop business process and procedures to support equipment and computerized system applications in their regulated environment. |
Factory acceptance testing (FAT) /Site acceptance testing (SAT)
3.4. Equipment, especially if incorporating novel or complex technology, may be evaluated, if applicable, at the vendor prior to delivery. |
SpectraTest Validation Plates are in scope of accreditation to ISO/IEC 17025 and ISO 9001:2015. |
|
3.5 Prior to installation, equipment should be confirmed to comply with the URS/ functional specification at the vendor site, if applicable. |
IQ/OQ and/or PM/OQ services and SpectraTest Validation Plates ensure instruments are performing within specification traceable to NIST and NMI standards. |
|
3.6. Where appropriate and justified, documentation review and some tests could be performed at the FAT or other stages without the need to repeat on site at IQ/OQ if it can be shown that the functionality is not affected by the transport and installation. |
IQ/OQ services ensure instruments are performing within specification onsite when requested. |
It is the end user option to request an IQ/OQ when the plate reader is set up in the lab for a baseline of tests prior to performing PQ. |
3.7 FAT may be supplemented by the execution of a SAT following the receipt of equipment at the manufacturing site. |
Not applicable. |
It is the end user option to use Factory Acceptance Test criteria based on their risk-based approach to validation. |
Installation qualification (IQ)
3.8. IQ should be performed on equipment, facilities, utilities, or systems. |
|
It is the end user option to perform IQ on equipment, facilities, utilities, or systems. |
3.9. IQ should include, but is not limited to the following:
i. Verification of the correct installation of components, instrumentation, equipment
ii. Verification of the correct installation against pre-defined criteria
iii. Collection and collation of supplier operating and working instructions and maintenance requirements
iv. Calibration of instrumentation |
IQ/OQ services for software validation and IQ/OQ and PM/OQ services ensure instruments are performing within specification. |
It is the end user responsibility to request an IQ/OQ when the plate reader is set up in the lab for a baseline of tests prior to performing their own qualification tests prior to GMP/GLP use. |
Operational qualification (OQ)
3.10. OQ normally follows IQ but depending on the complexity of the equipment, it may be performed as a combined Installation/Operation Qualification (IOQ). |
|
|
Reference to EudraLex Volume 4 Annex 15: Qualification and Validation |
Molecular Devices
Products/Services |
End User Operations |
3.11. OQ should include but is not limited to the following:
i. Tests that have been developed from the knowledge of processes, systems and equipment to ensure the system is operating as designed
ii. Tests to confirm upper and lower operating limits, and/or “worst case” conditions |
IQ/OQ services for software validation and IQ/OQ and PM/OQ services ensure instruments are performing within specification. |
It is the end user responsibility to request an IQ/OQ when the plate reader is set up in the lab for a baseline of tests prior to performing their own qualification tests prior to GMP/GLP use. |
3.12. The completion of a successful OQ should allow the finalization of standard operating and cleaning procedures, operator training and preventative maintenance requirements. |
|
|
Performance qualification (PQ)
3.13. PQ should normally follow the successful completion of IQ and OQ. However, it may in some cases be appropriate to perform it in conjunction with OQ or Process Validation. |
Not applicable. |
It is the end user responsibility to demonstrate equipment is suitable for use. |
3.14. PQ should include, but is not limited to the following:
i. Tests, using production materials, qualified substitutes or simulated product proven to have equivalent behavior under normal operating conditions with worst case batch sizes. The frequency of sampling used to confirm process control should be justified.
ii. Tests should cover the operating range of the intended process, unless documented evidence from the development phases confirming the operational ranges is available. |
|
|
Section 4 – Re-Qualification
4.1 Equipment, facilities, utilities and systems should be evaluated at an appropriate frequency to confirm that they remain in a state of control. |
IQ/OQ and/or PM/OQ services and SpectraTest Validation Plates ensure instruments are performing within specification traceable to NIST and NMI standards. |
|
4.2. Where re-qualification is necessary and performed at a specific time period, the period should be justified and the criteria for evaluation defined. Furthermore, the possibility of small changes over time should be assessed. |
|
|
About Molecular Devices UK Ltd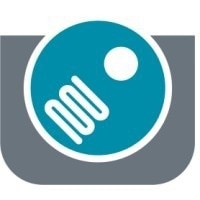
Molecular Devices is one of the world’s leading providers of high-performance life science technology. We make advanced scientific discovery possible for academia, pharma, and biotech customers with platforms for high-throughput screening, genomic and cellular analysis, colony selection and microplate detection. From cancer to COVID-19, we've contributed to scientific breakthroughs described in over 230,000 peer-reviewed publications.
Over 160,000 of our innovative solutions are incorporated into laboratories worldwide, enabling scientists to improve productivity and effectiveness – ultimately accelerating research and the development of new therapeutics. Molecular Devices is headquartered in Silicon Valley, Calif., with best-in-class teams around the globe. Over 1,000 associates are guided by our diverse leadership team and female president that prioritize a culture of collaboration, engagement, diversity, and inclusion.
To learn more about how Molecular Devices helps fast-track scientific discovery, visit www.moleculardevices.com.
Sponsored Content Policy: News-Medical.net publishes articles and related content that may be derived from sources where we have existing commercial relationships, provided such content adds value to the core editorial ethos of News-Medical.Net which is to educate and inform site visitors interested in medical research, science, medical devices and treatments.